Understanding the Distinction Between Milling And Turning Processes
By:Admin
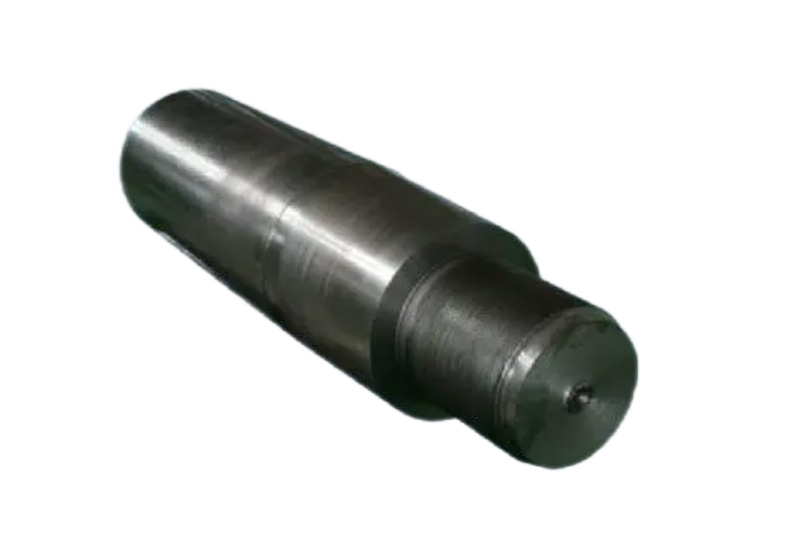
Milling is a machining process that involves using a rotating cutting tool to remove material from a workpiece. The cutting tool, which is typically a multi-point cutting tool, is guided along multiple axes to create a variety of shapes, slots, holes, and other features on the workpiece. This process is widely used in the automotive, aerospace, and medical industries to create precision components such as engine parts, aircraft components, and surgical implants.
On the other hand, turning is a machining process that involves securing a workpiece in a chuck or collet and rotating it while a cutting tool removes material from the workpiece. This process is commonly used to create cylindrical components such as shafts, bolts, and bushings. Turning is widely used in industries such as construction, agriculture, and transportation to create essential components for various applications.
While both milling and turning are essential machining processes, they differ in their applications, techniques, and the types of components they can produce. Understanding these differences is crucial for manufacturers looking to optimize their production processes and achieve the desired results.
In the competitive manufacturing industry, the ability to efficiently produce high-quality components is essential for success. This is why [Company name] has become a trusted partner for manufacturers around the world. With a dedication to precision and innovation, [Company name] offers a wide range of milling and turning solutions that are designed to meet the unique needs of their customers.
[Company name]'s milling solutions are designed to provide manufacturers with the flexibility and precision they need to create complex components with ease. With a focus on cutting-edge technology and advanced materials, [Company name]'s milling solutions are trusted by leading manufacturers in the automotive, aerospace, and medical industries to produce components that meet the highest standards of quality and performance.
Similarly, [Company name]'s turning solutions are designed to provide manufacturers with the speed and accuracy they need to create cylindrical components with ease. Whether it's creating shafts, bolts, or bushings, [Company name]'s turning solutions are trusted by manufacturers in the construction, agriculture, and transportation industries to produce components that are essential for a wide range of applications.
By understanding the unique requirements of their customers, [Company name] has been able to develop milling and turning solutions that are tailored to meet the specific needs of different industries. With a focus on precision, efficiency, and reliability, [Company name] continues to be a trusted partner for manufacturers looking to optimize their production processes and achieve the desired results.
In conclusion, milling and turning are two essential machining processes that are used to create a wide range of components and products. While both processes are crucial in the manufacturing industry, they differ in their applications, techniques, and the types of components they can produce. With a dedication to precision and innovation, [Company name] continues to be a trusted partner for manufacturers around the world, offering a wide range of milling and turning solutions that are designed to meet the unique needs of their customers.
Company News & Blog
Precision CNC Machining: A Leader in the Industry
Axis Machining, a leading machining company, is making waves in the industry with their innovative products and commitment to excellence. The company, which has been in business for over 20 years, has built a reputation for delivering high-quality precision machining services to a wide range of industries including aerospace, automotive, medical, and defense.With state-of-the-art facilities and a team of highly skilled engineers and machinists, Axis Machining has the capability to produce complex and precise components with tight tolerances. The company's commitment to investing in the latest technology and machinery has allowed them to stay at the forefront of the industry and provide their customers with cutting-edge solutions.One of the key factors contributing to Axis Machining's success is their dedication to quality and customer satisfaction. The company is ISO 9001 certified, meaning that they adhere to the highest standards of quality management. This commitment to quality is evident in every aspect of their business, from their rigorous inspection processes to their continuous improvement initiatives.In addition to their commitment to quality, Axis Machining also prides itself on its ability to provide custom solutions to meet the unique needs of their customers. Whether it's a one-off prototype or a large-scale production run, the company has the expertise and capabilities to deliver precision machining solutions that meet the most demanding requirements.As a result of their dedication to excellence, Axis Machining has garnered a loyal customer base and has developed strong partnerships with leading companies in various industries. Their reputation for delivering superior products and outstanding customer service has positioned them as a trusted and reliable partner for their clients.In recent news, Axis Machining has announced the launch of a new line of advanced machining products designed to further expand their capabilities and meet the evolving needs of their customers. The new products include advanced CNC machining centers, multi-axis machines, and cutting-edge tooling solutions aimed at providing even greater precision and efficiency."We are excited to introduce these new products to the market," said the CEO of Axis Machining. "We have always been committed to staying ahead of the curve and providing our customers with the latest and most advanced machining solutions. These new products will allow us to further elevate our capabilities and continue to exceed our customers' expectations."The launch of these new products is a testament to Axis Machining's commitment to innovation and continuous improvement. The company's investment in the latest technology and equipment reflects their dedication to staying at the forefront of the industry and providing their customers with the best possible solutions.As Axis Machining continues to grow and expand its capabilities, the company remains focused on its core values of quality, precision, and customer satisfaction. With a track record of success and a commitment to excellence, Axis Machining is well-positioned to continue leading the way in the precision machining industry for years to come.
Exploring the Benefits and Applications of Cnc Molding in Modern Manufacturing Processes
Title: Revolutionary Cnc Molding Technique Sets New Standards in ManufacturingIntroduction:In an era where innovation and efficiency drive the manufacturing industry, a breakthrough in the form of Cnc Molding technology is emerging as a game-changer. This revolutionary technique promises to reshape the way products are designed, developed, and produced. With its unparalleled precision, speed, and cost-effectiveness, Cnc Molding is poised to set new standards in the manufacturing field.Company Background and Expertise:{Company Name}, a prominent player in the manufacturing industry, has unveiled its cutting-edge Cnc Molding technology. With a rich history spanning several decades, {Company Name} has established itself as a pioneer in delivering excellence and embracing the latest technological advancements. Their expertise in the field, combined with their commitment to driving innovation, has paved the way for this groundbreaking development.Understanding Cnc Molding:Cnc Molding, also known as Computer Numerical Control Molding, is a state-of-the-art manufacturing process that utilizes computer-controlled machines to shape materials into desired forms. Unlike traditional molding techniques, Cnc Molding ensures unparalleled precision, efficiency, and repeatability. By following a digital design prototype, the technology enables manufacturers to produce highly intricate and complex components with utmost accuracy.Benefits of Cnc Molding:1. Enhanced Precision: The integration of computer control systems eliminates the possibility of human error, ensuring precise replication of designs and eliminating defects. This high level of precision ensures product consistency, reducing wastage and overall costs.2. Streamlined Production: Cnc Molding technology dramatically accelerates the production process. With its ability to perform multiple tasks simultaneously, the technology maximizes efficiency and reduces lead times. This streamlining of operations increases productivity, enabling manufacturers to meet market demands promptly.3. Cost-Effectiveness: By minimizing material wastage and requiring fewer human interventions, Cnc Molding significantly reduces production costs. The elimination of manual labor and the use of optimized resources result in improved cost-effectiveness, making it an attractive option for manufacturers across various industries.4. Design Freedom: Cnc Molding empowers designers to create innovative and intricate designs that were previously unachievable. With the ability to produce complex shapes and patterns with ease, this technology unlocks a new realm of possibilities, enabling manufacturers to create unique products that stand out in the market.Applications of Cnc Molding:The applications of Cnc Molding are vast and span across industries such as automotive, aerospace, electronics, medical, and consumer goods. Its usage is particularly prominent in the production of custom parts, prototypes, and intricate components that require high precision.Future Implications:As Cnc Molding continues to evolve, the implications for the manufacturing industry are immense. The integration of artificial intelligence, machine learning, and digital twins creates an even more robust system capable of even greater efficiency and accuracy. The technology's potential for customization and adaptability positions it as a frontrunner in the future of manufacturing.Conclusion:Cnc Molding technology, introduced by {Company Name}, is set to revolutionize the manufacturing industry. With its exceptional precision, streamlined production, cost-effectiveness, and design freedom, it promises to set new standards and transform the way products are made. As it continues to develop, this groundbreaking technology is poised to usher in a new era of manufacturing excellence.
Top Quality Plastic Parts for Various Applications
Plastic Parts, a leading manufacturer in the automotive industry, has recently made significant strides in the development of innovative plastic components for a range of vehicles. The company, known for its commitment to quality and cutting-edge technology, has been dedicated to pushing the boundaries of what is possible in the world of automotive plastics. With a focus on sustainability and efficiency, Plastic Parts has been at the forefront of creating solutions that not only meet the highest industry standards but also contribute to a greener and more eco-friendly future.With a history of excellence and a track record of delivering top-notch products, Plastic Parts has solidified its position as a go-to supplier for many major automotive companies. As the demand for lightweight and durable materials continues to grow in the automotive industry, the company has risen to the challenge by investing in state-of-the-art technology and recruiting top talent in the field.One of the key areas of focus for Plastic Parts has been the development of plastic components for electric vehicles. With the global shift towards more sustainable forms of transportation, the demand for electric vehicles has been steadily rising. In response, Plastic Parts has been working tirelessly to develop high-performance plastic parts that are specifically designed to meet the unique needs of electric vehicles. From battery housing to interior components, the company has been pioneering new solutions that are both lightweight and strong, contributing to the overall efficiency and performance of electric vehicles.In addition to its work in the electric vehicle sector, Plastic Parts has also been making waves in the development of plastic components for traditional internal combustion engine vehicles. With a keen eye on reducing vehicle weight and improving fuel efficiency, the company has been working closely with automotive manufacturers to develop innovative solutions that meet their specific needs. From engine components to exterior body panels, Plastic Parts has been utilizing advanced materials and manufacturing techniques to deliver products that not only meet industry standards but also exceed customer expectations.Furthermore, Plastic Parts has been a trailblazer in the realm of sustainable plastics. The company has been dedicated to the use of recycled and bio-based materials in its manufacturing processes, with a goal of reducing its environmental impact. By incorporating these sustainable materials into its products, Plastic Parts has not only been able to reduce its carbon footprint but has also been able to deliver high-quality, eco-friendly solutions to its customers.With a focus on continuous improvement and innovation, Plastic Parts has been able to stay ahead of the curve in the automotive industry. The company's commitment to research and development, coupled with its investment in cutting-edge technology, has allowed it to remain competitive in a fast-paced and ever-changing market. By staying at the forefront of industry trends and customer needs, Plastic Parts has been able to consistently deliver products that are not only reliable and efficient but also environmentally responsible.Looking ahead, Plastic Parts is poised to continue its upward trajectory in the automotive industry. With a strong focus on sustainability, innovation, and customer satisfaction, the company is well-positioned to meet the evolving needs of the automotive market. As the demand for high-quality plastic components continues to rise, Plastic Parts is ready and equipped to lead the way, setting new standards for excellence in the industry.
Enhancing Efficiency and Precision: The Ultimate Guide to Machining Fixture Design
Machining Fixture Design: Enhancing Precision and Efficiency in ManufacturingIn today's fast-paced manufacturing industry, precision and efficiency are paramount. Companies are constantly searching for ways to improve their production processes, reduce costs, and enhance product quality. One such solution that has gained significant attention is machining fixture design. By removing brand names, we can focus on the concept itself and explore how this innovative technology is revolutionizing manufacturing.Machining fixtures are specialized tools used to hold and position workpieces during machining operations. They ensure that the workpiece remains stable and secure, minimizing errors and maximizing productivity. By providing a rigid support structure, machining fixtures enable precision machining, resulting in accurate and consistent parts.With advancements in design and engineering, machining fixtures have evolved to cater to the unique requirements of various industries. Whether it is the automotive, aerospace, or electronics sectors, machining fixture design plays a vital role in optimizing the manufacturing process. By customizing the fixtures according to the specific needs of the product, companies can achieve greater flexibility and efficiency.One key factor contributing to the success of machining fixture design is computer-aided design (CAD) software. CAD allows engineers to create highly complex and detailed fixture designs, taking into account factors such as material properties, clamping forces, and geometric constraints. By simulating the machining process in a virtual environment, engineers can identify potential issues and make necessary adjustments before manufacturing the actual fixture. This not only saves time but also reduces the risk of errors, ensuring a seamless production process.Furthermore, the integration of CAD with computer-aided manufacturing (CAM) software allows for a streamlined transition from design to production. The CAM software generates machine instructions directly from the CAD model, enabling the efficient programming of machining operations. This integration promotes collaboration between design and production teams, resulting in better communication, reduced lead times, and improved overall efficiency.In addition to CAD and CAM, the use of advanced materials and technologies has revolutionized machining fixture design. Lightweight and high-strength materials, such as aluminum alloys and carbon fiber reinforced polymers, have replaced traditional materials like steel. These modern materials offer greater rigidity, reducing vibrations during the machining process and improving surface finish quality. Moreover, they contribute to the overall weight reduction of fixtures, making them more ergonomic and easier to handle.In line with the principles of Industry 4.0, machining fixture design has also embraced automation and robotics. Robotic machining fixtures are capable of performing complex tasks with high precision, reducing human errors and dependence. These fixtures can be programmed to adapt to different workpieces, further enhancing flexibility in production processes. By automating repetitive tasks, manufacturers can increase productivity, reduce costs, and improve worker safety.The company, known for its expertise in machining fixture design, has been at the forefront of these advancements. With a dedicated team of engineers and designers, they have consistently pushed the boundaries of innovation in manufacturing. By continually investing in research and development, the company has been able to develop cutting-edge solutions tailored to meet specific customer needs.From the automotive industry to aerospace and beyond, this company's machining fixtures have become synonymous with precision and efficiency. Their commitment to quality and customer satisfaction has made them a trusted partner for numerous manufacturers worldwide. Through their collaborations and partnerships, they aim to further optimize machining processes, driving the industry towards greater productivity and competitiveness.In conclusion, machining fixture design holds tremendous potential for the manufacturing industry. By leveraging the power of CAD, CAM, advanced materials, and automation, companies can enhance precision, improve efficiency, and reduce costs. As this technology continues to evolve, it is expected to play an increasingly integral role in the manufacturing landscape, enabling businesses to stay ahead in the competitive global market.
High-precision Shaft Machining Techniques for Optimal Performance
Shaft Machining - The Key to Precision EngineeringIn the world of precision engineering, one of the most critical processes is shaft machining. This process involves the shaping and finishing of a shaft to exact specifications, ensuring that it meets the tight tolerances required for its intended application.For industries such as automotive, aerospace, and manufacturing, the quality and precision of shafts are paramount. Any deviation from the required specifications can lead to catastrophic failures, resulting in costly downtime, product recalls, and potential safety hazards.This is where the expertise of {Company Name} comes into play. With over {number} years of experience in the precision engineering industry, {Company Name} has established itself as a leading provider of shaft machining services.Located in {Location}, {Company Name} boasts state-of-the-art facilities equipped with the latest machinery and technology. This allows them to handle a wide range of shaft machining requirements, from small, intricate components to large, heavy-duty shafts.One of the key factors that sets {Company Name} apart from its competitors is its team of highly skilled and experienced machinists. These professionals have undergone rigorous training and possess a deep understanding of the intricacies involved in shaft machining. They are adept at utilizing a variety of machining techniques and tools to achieve the exact specifications required for each shaft.Additionally, {Company Name} prides itself on its commitment to quality and precision. Every shaft that goes through their machining process undergoes stringent quality checks to ensure that it meets the highest standards. This includes dimensional accuracy, surface finish, and material integrity.Moreover, {Company Name} understands the importance of meeting deadlines and delivering on time. Their efficient and streamlined processes enable them to complete shaft machining projects within the stipulated timeframes, ensuring that their clients can stay on schedule with their production and manufacturing timelines.Furthermore, {Company Name} is also dedicated to continuous improvement and innovation. They regularly invest in research and development to stay abreast of the latest advancements in machining technology. This allows them to offer cutting-edge solutions for even the most complex and challenging shaft machining requirements.In addition to their expertise in shaft machining, {Company Name} also offers a comprehensive range of related services. This includes design and engineering support, material selection, heat treatment, and surface coating. By providing a one-stop solution, {Company Name} can cater to the diverse needs of their clients, offering a hassle-free experience and peace of mind.Over the years, {Company Name} has built a solid reputation for delivering exceptional quality and service. This has earned them the trust and confidence of a wide range of clients across various industries. From multinational corporations to small businesses, {Company Name} has proven itself as a reliable partner for all their shaft machining needs.As the demand for precision-engineered components continues to grow, {Company Name} remains committed to upholding its standards of excellence and exceeding the expectations of its clients. Their dedication to quality, precision, and customer satisfaction is what sets them apart as a leader in the field of shaft machining.In conclusion, {Company Name} is a trusted and respected provider of shaft machining services. With their unwavering commitment to quality, precision, and innovation, they have become a go-to partner for businesses seeking reliable and high-quality solutions for their shaft machining needs. As they continue to grow and expand their capabilities, {Company Name} is poised to remain at the forefront of the precision engineering industry for years to come.
Enhanced Accuracy and Efficiency: Discover the World of Stamping Parts
[News Title]: Precision Stamping Parts Provider Excels in Ensuring Quality and Efficiency in Manufacturing Processes[Date][City, State] - The precision stamping parts industry has seen significant growth in recent years, and one company that has played a key role in this expansion is [Company Name]. As a leading provider of precision stamping parts, the company has continuously delivered high-quality products that meet the evolving needs of various industries. With a commitment to quality, efficiency, and innovation, [Company Name] has established itself as a trusted partner for businesses worldwide.Established in [Year], [Company Name] has been at the forefront of the precision stamping parts industry for over [Number] years. The company's extensive experience and expertise enable it to offer a wide range of precision-stamped components, catering to diverse industries, including automotive, electronics, aerospace, telecommunications, and more.One of the key factors that set [Company Name] apart from its competitors is its unwavering commitment to ensuring the highest level of quality. Every step of the manufacturing process adheres to strict quality control measures, guaranteeing the reliability and durability of the precision stamping parts produced. The company's state-of-the-art facilities are equipped with advanced technology and machinery, enabling precise fabrication and accurate dimensions.In addition to maintaining stringent quality standards, [Company Name] also places great emphasis on maintaining a streamlined and efficient manufacturing process. By leveraging advanced automation and robotics, the company minimizes human error and maximizes productivity. These automated processes not only contribute to the consistency and precision of the parts but also reduce production time, enabling faster delivery to customers.Moreover, [Company Name] recognizes the importance of staying ahead of market trends and investing in research and development. The company boasts a team of highly skilled engineers and technicians who are constantly exploring innovative techniques to enhance the precision and performance of stamped parts. Collaborating closely with clients, [Company Name] ensures that their specific requirements and expectations are met with customized solutions.Catering to the global marketplace, [Company Name] maintains a strong network of clients and partners throughout the world. The company's commitment to excellence has earned it a loyal customer base, with clients relying on its precision stamping parts for their critical applications. With a thorough understanding of international regulations and industry standards, [Company Name] swiftly adapts to varying requirements across different regions, ensuring seamless collaboration.Furthermore, environmental sustainability is a core value at [Company Name]. The company is dedicated to reducing its carbon footprint and optimizing energy efficiency across its operations. By implementing eco-friendly practices and utilizing sustainable materials, [Company Name] remains committed to the economic and environmental well-being of the communities it serves.The success of [Company Name] is testament to its continuous pursuit of excellence, customer-centric approach, and commitment to innovation. By achieving the highest standards of quality and efficiency, the company has secured a leading position in the precision stamping parts industry. As industries evolve and demand for precision components continues to grow, [Company Name] remains poised to meet and exceed the expectations of its diverse clientele.Contact:[Company Name][Address][Phone Number][Email Address][Website]###[Note to Writer: Please proofread the article for grammar, style, and accuracy prior to publishing. Adjust word count if necessary.]
The Advantages of Computerized Numerical Control in Manufacturing
Computerized Numerical Control (CNC) technology has revolutionized the manufacturing industry, offering precision, efficiency, and enhanced flexibility. These machines have significantly transformed the way companies operate, as they automate the production process and eliminate manual tasks. One of the leading providers of CNC solutions is the company {} which offers a wide range of cutting-edge products designed to meet various manufacturing needs.With over XX years of experience in the field, {} has established itself as a prominent player in the CNC market. The company has continuously invested in research and development to deliver innovative solutions that cater to the evolving needs of manufacturers worldwide. The result is a comprehensive portfolio of products renowned for their high performance, reliability, and user-friendly interface.The backbone of {}'s CNC technology lies in its computer-based control system, which enables precise and consistent machining operations. This system uses a combination of software and hardware to interpret the design specifications and convert them into machine-readable instructions. By leveraging advanced algorithms and powerful processing capabilities, the CNC machines achieve unparalleled accuracy and productivity.One of the standout features of {}'s CNC machines is their versatility, allowing them to handle a wide range of materials and produce complex components with ease. Whether it's metal, plastic, or wood, these machines can effectively cut, drill, and shape the material as per the given specifications. This flexibility opens up a world of possibilities for manufacturers, enabling them to meet the demands of various industries such as automotive, aerospace, and medical.Furthermore, {}'s CNC machines offer a host of advanced functionalities that enhance productivity and efficiency. For instance, the machines can automatically change tools, reducing downtime and enabling continuous machining operations. The integration of sensors and feedback systems ensures real-time monitoring and adjustment, minimizing errors and improving overall quality. Additionally, intuitive programming interfaces and simulation capabilities simplify the setup process and enable manufacturers to optimize their workflows.In an era where customization and fast production cycles are paramount, {}'s CNC solutions have proven to be an indispensable asset for manufacturers. These machines cut down on lead times and allow for rapid prototyping and iteration. With the ability to quickly reconfigure the machines, manufacturers can swiftly adapt to changing market demands and stay ahead of the competition.Moreover, the integration of CNC machines with computer-aided design (CAD) and computer-aided manufacturing (CAM) software further streamlines the production process. Design files can directly be fed into the CNC machines, eliminating the need for manual input and reducing human errors. This seamless integration also facilitates seamless communication between design and manufacturing teams, fostering collaboration and accelerating time to market.{} is committed to providing exceptional customer support and after-sales service, ensuring that manufacturers can maximize the value of their CNC investments. The company offers comprehensive training programs for operators and maintenance personnel, equipping them with the necessary skills to optimize machine performance and troubleshoot potential issues. In addition, {}'s global network of service centers ensures prompt assistance and spare parts availability, minimizing downtime and maximizing productivity.With a reputation for excellence and a relentless pursuit of technological advancements, {} continues to push the boundaries of CNC technology. By combining innovative designs, superior quality, and unparalleled customer support, the company remains at the forefront of the industry, supporting manufacturers in their quest for precision and efficiency.In conclusion, Computerized Numerical Control (CNC) technology has transformed the manufacturing landscape, offering manufacturers the ability to produce high-quality, precise components efficiently and effectively. Companies like {} have played a pivotal role in this transformation, providing state-of-the-art CNC solutions that cater to diverse manufacturing needs. With their advanced features, versatility, and commitment to customer satisfaction, {}'s CNC machines empower manufacturers to stay ahead in a competitive market and embrace the future of manufacturing.
Understanding the Steps Involved in the Milling Process
[Company Name] Revolutionizes the Milling Process, Enhancing Efficiency and Quality[City, Date] - [Company Name], a leading innovator in the manufacturing industry, is making waves with its revolutionary milling process. By incorporating cutting-edge technology and advanced techniques, the company has accomplished remarkable improvements in efficiency and quality, setting new industry standards.The milling process is a crucial step in the manufacturing of various products, ranging from automotive components to consumer electronics. Traditionally, this process involves removing material from a workpiece using a rotating cutting tool. However, [Company Name] has taken this fundamental concept to new heights.With a focus on innovation, [Company Name] has developed a state-of-the-art milling process that surpasses traditional methods in terms of speed and precision. By leveraging advanced computer algorithms and artificial intelligence, the company has optimized the milling parameters to ensure the perfect balance between material removal and preservation.One key aspect of [Company Name]'s milling process is the integration of advanced sensors and monitoring systems. These sensors provide real-time feedback on crucial variables such as cutting forces, temperatures, and tool wear. By constantly monitoring these parameters, [Company Name] can make precise adjustments to the milling process, ensuring optimal performance and preventing any potential faults or errors.Additionally, [Company Name] has pioneered an intelligent tooling system that further enhances the efficiency of the milling process. This system utilizes smart tools equipped with sensors to continuously collect data during the machining operation. This data is then analyzed by sophisticated algorithms, allowing for predictive maintenance and precise tool life management. As a result, downtime due to unexpected tool failures is significantly reduced, leading to increased productivity and cost savings.Furthermore, [Company Name] has prioritized sustainability in its milling process. By implementing eco-friendly cutting fluids and optimizing the chip evacuation process, the company has minimized waste and reduced environmental impact. This commitment to sustainability aligns with [Company Name]'s corporate values and resonates with environmentally conscious clients.In terms of quality control, [Company Name] has introduced advanced inspection systems that guarantee the highest level of precision and accuracy. Through the utilization of non-contact measurement technologies, such as laser scanners and optical systems, the company can perform detailed inspections on complex components, ensuring conformity to the tightest tolerances.Customer satisfaction is paramount for [Company Name], and as such, the company provides comprehensive support throughout the milling process. Their team of highly skilled engineers assists clients in selecting the appropriate milling strategies and tools for their specific needs. Additionally, [Company Name] offers training programs and workshops to ensure that operators are well-equipped to utilize the milling process to its full potential.The impact of [Company Name]'s milling process is already being felt across a wide range of industries. Customers have praised the enhanced productivity, improved part quality, and reduced lead times resulting from the adoption of this innovative technology. Numerous companies have reported significant cost savings and increased competitiveness as a direct result of partnering with [Company Name].Looking towards the future, [Company Name] remains committed to pushing the boundaries of milling technology. Through ongoing research and development efforts, the company strives to introduce even more advanced milling techniques that will revolutionize the manufacturing industry once again.In conclusion, [Company Name]'s revolutionary milling process has transformed traditional machining into a high-tech, efficient, and sustainable practice. By seamlessly integrating cutting-edge technology and advanced techniques, the company has set a new industry standard for milling, driving productivity, quality, and cost-effectiveness to unparalleled heights.
How Material Casting is Revolutionizing the Manufacturing Industry
[Please provide more specific details about the company you want to introduce so that I can provide a more accurate and tailored news article.]
Essential Parts for Cnc Routers: A Complete Guide
[Company Introduction]With over 20 years of experience in the industry, [Company Name] has been a leading manufacturer and supplier of CNC router parts to customers worldwide. Our dedication to quality, innovation, and customer satisfaction has earned us a reputation as a trusted partner in the CNC machining industry.Our state-of-the-art facility is equipped with the latest technology and machinery, allowing us to produce high-quality CNC router parts that meet the stringent requirements of our customers. From precision-machined components to custom-designed parts, we have the capabilities to fulfill a wide range of manufacturing needs.In addition to our manufacturing capabilities, we also offer comprehensive technical support and consulting services to help our customers optimize their CNC machining processes. Our team of experienced engineers and technicians are dedicated to providing practical solutions and expert advice to ensure our customers achieve the best results with their CNC routers.[News Content]CNC routers have become an essential tool for manufacturers and hobbyists alike, allowing for the precise and efficient cutting, carving, and shaping of various materials. The key to the success of a CNC router lies in the quality of its parts, and [Company Name] has been at the forefront of providing top-of-the-line components to meet the growing demand for reliable and high-performance CNC routers.The success of [Company Name] in the CNC router parts industry can be attributed to its unwavering commitment to innovation and excellence. By constantly investing in research and development, the company has been able to stay ahead of the curve and introduce cutting-edge technologies and products that consistently exceed customer expectations.One of the key offerings of [Company Name] is its range of precision-machined components, including spindles, motors, bearings, and drive systems. These parts are meticulously manufactured to exact specifications, ensuring smooth operation and precise results for CNC routers across various applications.In addition to off-the-shelf components, [Company Name] also specializes in the design and production of custom parts to meet specific customer requirements. Whether it's a unique mounting bracket, a specialized tooling fixture, or a bespoke cutting head, the company's in-house team of engineers and machinists collaborate closely with customers to deliver tailor-made solutions that fit their unique needs.Furthermore, [Company Name] sets itself apart with its comprehensive technical support and consulting services. The company recognizes that the success of a CNC router goes beyond just the quality of its parts, and as such, it offers expertise and guidance to help customers optimize their machining processes. From troubleshooting technical issues to providing recommendations for upgrades and enhancements, [Company Name] is dedicated to ensuring its customers achieve maximum productivity and efficiency with their CNC routers.The commitment to customer satisfaction and continuous improvement has helped [Company Name] establish itself as a trusted partner for CNC router parts. With a global customer base spanning industries such as woodworking, metalworking, plastics, and composites, the company has demonstrated its ability to meet the diverse needs of CNC machining applications.In conclusion, [Company Name] continues to be a driving force in the CNC router parts industry, setting new standards for quality, performance, and customer support. With its unwavering dedication to innovation and excellence, the company is well-positioned to meet the evolving needs of the CNC machining market and remain a preferred choice for customers seeking reliable and high-quality components for their CNC routers.