Ultimate Guide to Ceramic Machining: Methods and Techniques
By:Admin
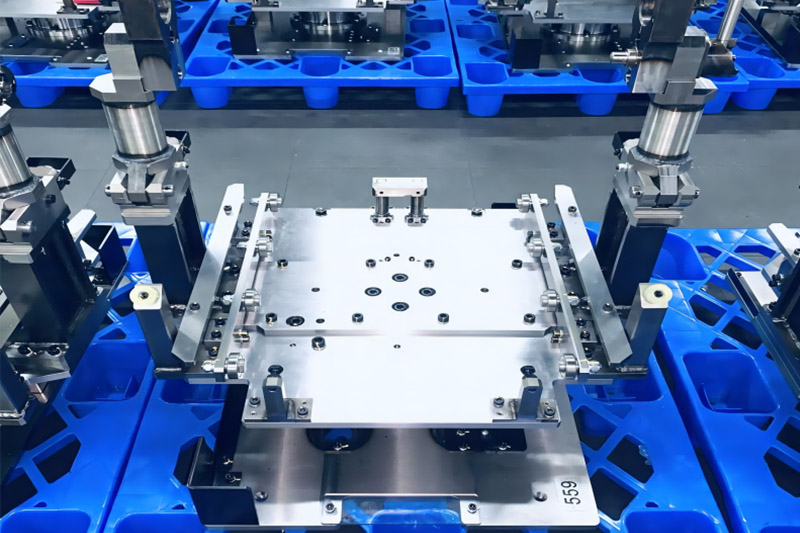
One company that has established itself as a leader in the field of ceramic machining is {}. With over 20 years of experience, the company has developed a reputation for delivering high-quality precision machined ceramic components to a diverse customer base. From prototype development to full-scale production, {} offers a comprehensive range of services to meet the needs of its clients.
The company's state-of-the-art facility is equipped with advanced machining equipment and the latest technology, allowing them to produce intricate and complex ceramic components with exceptional accuracy and repeatability. Their team of skilled engineers and machinists are highly experienced in working with a variety of ceramic materials, including alumina, zirconia, silicon nitride, and more. This expertise enables {} to deliver customized solutions that meet the exact specifications and performance requirements of their customers.
In addition to their technical capabilities, {} is committed to providing exceptional customer service and support throughout the entire machining process. They work closely with their clients to understand their specific needs and develop tailored solutions that optimize the performance and cost-effectiveness of the final product. With a focus on quality and efficiency, the company strives to exceed customer expectations and build long-lasting partnerships based on trust and reliability.
Furthermore, {} is dedicated to continuously improving their processes and investing in research and development to stay at the forefront of the industry. By staying abreast of the latest advancements in ceramic materials and machining technologies, they can offer innovative solutions that push the boundaries of what is possible in terms of precision and performance.
One of the key factors that sets {} apart from its competitors is its commitment to quality and rigorous quality control measures. The company follows strict protocols and standards to ensure that every component that leaves their facility meets the highest levels of precision and reliability. They utilize advanced inspection and testing equipment to verify the dimensional accuracy, surface finish, and other critical parameters of their machined ceramic components.
Looking ahead, {} is well-positioned to capitalize on the growing demand for precision ceramic machining in various industries. As new applications for ceramic materials continue to emerge, the company is ready to leverage its expertise and capabilities to deliver cutting-edge solutions that help their customers stay ahead of the competition.
In summary, {} is a leading provider of precision ceramic machining services, offering a combination of technical expertise, advanced capabilities, and a commitment to customer satisfaction. With a focus on quality, innovation, and continuous improvement, the company is poised to play a pivotal role in shaping the future of ceramic machining and its applications across diverse industries.
Company News & Blog
Enhanced Accuracy and Efficiency: Discover the World of Stamping Parts
[News Title]: Precision Stamping Parts Provider Excels in Ensuring Quality and Efficiency in Manufacturing Processes[Date][City, State] - The precision stamping parts industry has seen significant growth in recent years, and one company that has played a key role in this expansion is [Company Name]. As a leading provider of precision stamping parts, the company has continuously delivered high-quality products that meet the evolving needs of various industries. With a commitment to quality, efficiency, and innovation, [Company Name] has established itself as a trusted partner for businesses worldwide.Established in [Year], [Company Name] has been at the forefront of the precision stamping parts industry for over [Number] years. The company's extensive experience and expertise enable it to offer a wide range of precision-stamped components, catering to diverse industries, including automotive, electronics, aerospace, telecommunications, and more.One of the key factors that set [Company Name] apart from its competitors is its unwavering commitment to ensuring the highest level of quality. Every step of the manufacturing process adheres to strict quality control measures, guaranteeing the reliability and durability of the precision stamping parts produced. The company's state-of-the-art facilities are equipped with advanced technology and machinery, enabling precise fabrication and accurate dimensions.In addition to maintaining stringent quality standards, [Company Name] also places great emphasis on maintaining a streamlined and efficient manufacturing process. By leveraging advanced automation and robotics, the company minimizes human error and maximizes productivity. These automated processes not only contribute to the consistency and precision of the parts but also reduce production time, enabling faster delivery to customers.Moreover, [Company Name] recognizes the importance of staying ahead of market trends and investing in research and development. The company boasts a team of highly skilled engineers and technicians who are constantly exploring innovative techniques to enhance the precision and performance of stamped parts. Collaborating closely with clients, [Company Name] ensures that their specific requirements and expectations are met with customized solutions.Catering to the global marketplace, [Company Name] maintains a strong network of clients and partners throughout the world. The company's commitment to excellence has earned it a loyal customer base, with clients relying on its precision stamping parts for their critical applications. With a thorough understanding of international regulations and industry standards, [Company Name] swiftly adapts to varying requirements across different regions, ensuring seamless collaboration.Furthermore, environmental sustainability is a core value at [Company Name]. The company is dedicated to reducing its carbon footprint and optimizing energy efficiency across its operations. By implementing eco-friendly practices and utilizing sustainable materials, [Company Name] remains committed to the economic and environmental well-being of the communities it serves.The success of [Company Name] is testament to its continuous pursuit of excellence, customer-centric approach, and commitment to innovation. By achieving the highest standards of quality and efficiency, the company has secured a leading position in the precision stamping parts industry. As industries evolve and demand for precision components continues to grow, [Company Name] remains poised to meet and exceed the expectations of its diverse clientele.Contact:[Company Name][Address][Phone Number][Email Address][Website]###[Note to Writer: Please proofread the article for grammar, style, and accuracy prior to publishing. Adjust word count if necessary.]
Precision Machining Services: Milling and Turning Techniques Explained
Milling And Turning Service Provider Expands Operations{Company name}, a leading provider of precision machining services, has announced the expansion of its milling and turning operations in response to growing demand in the industry. With a focus on delivering high-quality components and parts for a wide range of industries, the company is committed to meeting the needs of its customers while maintaining the highest standards of craftsmanship and precision.The expansion of {Company name}'s milling and turning operations comes as the company continues to experience steady growth and increased demand for its services. With a team of highly skilled machinists and a state-of-the-art facility equipped with the latest technology and equipment, the company is well-positioned to take on a wider range of projects and deliver superior results."Our decision to expand our milling and turning operations is a direct response to the needs of our customers," said {Company name}'s CEO. "We have seen a steady increase in demand for our precision machining services, and this expansion will allow us to better serve our clients and take on more complex projects."{Company name} has built a reputation for excellence in the precision machining industry, with a focus on delivering superior quality, precision, and reliability. The company's milling and turning services are well-known for their ability to produce high-precision components and parts with tight tolerances, making them a preferred choice for customers in industries such as aerospace, automotive, medical, and more.With the expansion of its milling and turning operations, {Company name} is poised to further solidify its position as a leader in the precision machining industry. The company's investment in new technology and equipment will enable it to take on a wider range of projects and deliver even higher levels of quality and precision.In addition to its commitment to quality and precision, {Company name} is also dedicated to providing exceptional customer service. The company works closely with its clients to understand their specific needs and requirements, and its team of experts is always available to offer guidance and support throughout the machining process."We take great pride in our ability to deliver the highest quality precision machining services to our customers," said {Company name}'s CEO. "With the expansion of our milling and turning operations, we are excited to be able to take on even more challenging projects and continue to exceed our customers' expectations."As {Company name} continues to expand its milling and turning operations, the company remains focused on its core values of quality, precision, and reliability. With a commitment to investing in the latest technology and equipment, as well as a dedication to providing exceptional customer service, {Company name} is well-positioned to meet the evolving needs of its customers and continue to lead the way in the precision machining industry.
Discover the Top Features of Cnc Machines for Precision Manufacturing
The use of CNC (Computer Numerical Control) machines has become increasingly popular in the manufacturing industry due to their high precision and efficiency. This technology has revolutionized the way products are made, and companies are constantly looking for the latest features and improvements to enhance their production capabilities. One company that has been at the forefront of CNC machine development is {} Company. With a rich history in the manufacturing industry, {} has established itself as a leader in producing cutting-edge CNC machines that are tailored to meet the evolving needs of the market.One of the standout features of {}'s CNC machines is their advanced control system. The machines are equipped with state-of-the-art software that allows for seamless integration with CAD/CAM systems, enabling users to create intricate designs and easily convert them into machining programs. This level of automation not only streamlines the production process but also reduces the margin for error, resulting in higher quality finished products.In addition, {}'s CNC machines boast superior cutting capabilities. The machines are equipped with high-speed spindles and multi-axis machining capabilities, allowing for complex and precise cuts on various materials. This level of versatility makes {}'s machines suitable for a wide range of industries, from automotive and aerospace to medical and electronics.Furthermore, {}'s CNC machines are built with robust and durable components, ensuring consistent and reliable performance. The machines undergo rigorous testing to ensure they can withstand the demands of heavy-duty machining operations, giving users peace of mind in their investment.Another key feature of {}'s CNC machines is their user-friendly interface. The machines are designed with intuitive controls and a user-friendly interface, making them accessible to operators of varying skill levels. This accessibility, combined with comprehensive training and support from {}'s team, ensures that users can maximize the potential of the machines and achieve optimal results.With a global presence, {} Company has a strong track record of delivering high-quality CNC machines to clients around the world. Their commitment to innovation and excellence has made them a trusted partner for companies looking to enhance their manufacturing capabilities.In conclusion, the latest features of {}'s CNC machines, combined with their extensive industry experience and commitment to excellence, make them a standout choice for companies seeking to elevate their production capabilities. With a focus on precision, efficiency, and reliability, {}'s CNC machines are well-positioned to meet the evolving needs of the manufacturing industry and drive the next wave of innovation in production technology.
Top Tips for Choosing the Best Material Casting for Your Project
Material Casting, a well-known leader in the industrial casting industry, has announced its latest advancements in technology and expansion of its facilities to meet the growing demands of its global clientele. With a focus on innovation and quality, Material Casting has remained a key player in the market for over [X] years, consistently delivering top-notch solutions for a wide range of industries including automotive, aerospace, and energy.The company's commitment to excellence is evident in its state-of-the-art facilities, equipped with the latest machinery and technology to ensure precision and efficiency in the casting process. Material Casting employs a team of highly skilled engineers and technicians who continuously push the boundaries of what is possible in the industry, utilizing advanced materials and techniques to deliver superior products.In addition to its commitment to technological advancement, Material Casting is also dedicated to sustainability and environmental responsibility. The company has implemented eco-friendly practices in its production processes, minimizing waste and maximizing energy efficiency. This focus on sustainability has not only reduced the company's environmental impact, but has also led to cost savings that are passed on to customers, making Material Casting a competitive and attractive choice for businesses worldwide.The expansion of Material Casting's facilities is a testament to the company's continued growth and success in the industry. The new facilities will allow for increased production capacity, enabling Material Casting to take on larger and more complex projects while maintaining its high standards of quality and precision. Additionally, the company plans to further invest in research and development, with the goal of introducing groundbreaking innovations that will revolutionize the casting industry and exceed customer expectations.When asked about the expansion and the future of Material Casting, [CEO Name] expressed his optimism and excitement for the company's prospects. "We are thrilled to be taking this next step in our journey," [CEO Name] said. "The expansion of our facilities represents not only our commitment to meeting the needs of our clients, but also our confidence in the future of the industry. We are continuously striving to push the boundaries of what is possible in casting technology, and we are eager to see what the future holds for Material Casting."Material Casting's dedication to excellence, innovation, and sustainability has solidified its position as a leading provider of casting solutions in the global market. The company's expansion and advancements in technology will undoubtedly further strengthen its standing, allowing it to continue meeting the evolving needs of its customers while remaining at the forefront of the industry.As Material Casting continues to make strides in the casting industry, its commitment to quality, innovation, and sustainability distinguishes it as a trusted and reliable partner for businesses seeking top-tier casting solutions. With a focus on continuous improvement and customer satisfaction, Material Casting is poised to remain a driving force in the industry for years to come.
Effective Ways to Utilize Material Molding for Your Project
Material Molding, also known as injection molding, is a process that involves injecting a material into a mold to produce various products. The process is widely used in the manufacturing industry to create a wide range of items, from small components to large parts. The flexibility and efficiency of material molding make it a popular choice for producing high-quality products in large quantities.One company that specializes in material molding is {}. With over 20 years of experience in the industry, {} has established itself as a leading provider of material molding solutions. The company's state-of-the-art facilities and advanced technology allow them to meet the diverse needs of their clients, delivering products that meet the highest standards of quality and performance.{} offers a comprehensive range of material molding services, including design and engineering, prototyping, tooling, and production. Their team of experienced engineers and technicians work closely with clients to develop customized solutions that meet their specific requirements. With a focus on innovation and continuous improvement, {} is able to stay ahead of the competition and deliver cutting-edge material molding solutions.The company's commitment to quality is evident in their rigorous quality control processes, ensuring that every product meets the highest standards of performance and durability. With a strong emphasis on customer satisfaction, {} strives to exceed the expectations of their clients, delivering reliable and cost-effective material molding solutions.{} is also dedicated to sustainability and environmental responsibility. They have implemented various initiatives to minimize their environmental impact, including the use of eco-friendly materials and energy-efficient processes. By adopting sustainable practices, {} is able to contribute to a greener and more sustainable future while meeting the needs of their clients.In addition to their material molding services, {} also offers comprehensive support throughout the entire product development process. From initial concept and design to production and beyond, their team provides expert guidance and assistance, ensuring a seamless and efficient development process.As a trusted partner for numerous industries, {} has built a strong reputation for reliability, innovation, and excellence. Their commitment to delivering high-quality material molding solutions has earned them the trust and loyalty of clients from around the world.The future looks bright for {}, as they continue to invest in new technologies and expand their capabilities to meet the evolving needs of the market. With a focus on delivering superior products and exceptional customer service, {} is poised to remain at the forefront of the material molding industry for years to come.In conclusion, material molding is a critical process in the manufacturing industry, and companies like {} play a vital role in delivering high-quality solutions to meet the diverse needs of their clients. With a focus on innovation, quality, and sustainability, {} is a trusted partner for numerous industries, providing reliable and cost-effective material molding services. With their commitment to excellence and continuous improvement, {} is well-positioned to maintain its leadership in the material molding industry for years to come.
Exploring the Advantages of Plastic CNC Machining: Your Complete Guide
Title: Leading CNC Machining Company Revolutionizes Plastic Manufacturing ProcessIntroduction:In the fast-paced world of manufacturing, precision and efficiency are crucial factors that determine the success of a company. One such industry leader, {Company Name}, has long been at the forefront of revolutionizing CNC machining for plastic materials. Their groundbreaking techniques and cutting-edge technology have paved the way for innovation and advancement in the manufacturing sector. With a diverse range of applications across various industries, {Company Name} continues to drive quality and excellence in the field of plastic machining.1. Innovations in CNC Machining Plastic:{Company Name} has revolutionized the CNC machining process by introducing state-of-the-art technology and advanced techniques specifically designed for plastic materials. Traditional machining methods often encounter challenges when working with plastic due to its unique properties. However, {Company Name}'s pioneering approach has overcome these obstacles.Their precise CNC machines are equipped with specially designed tooling and cutting-edge software that optimizes the machining process for plastic. The integration of computer-controlled automation ensures unprecedented accuracy and consistency in every part produced. This level of precision allows for the manufacturing of intricate and complex plastic components with tight tolerances, meeting the demanding requirements of various industries.2. Diverse Applications:The versatility of {Company Name}'s CNC machining capabilities extends across multiple industries. Automotive manufacturers rely on their expertise to produce high-quality plastic parts for interior components, such as dashboard panels, door handles, and trim pieces. The medical sector benefits from their precision machining abilities to create custom plastic implants and medical device components, ensuring optimal patient care.Moreover, the electronics industry relies on {Company Name}'s efficient plastic machining solutions for producing casings, connectors, and enclosures for various electronic devices. The aerospace industry also benefits from their expertise in crafting lightweight, yet durable plastic components, contributing to enhanced fuel efficiency and performance.3. Commitment to Sustainability:In addition to their exceptional manufacturing capabilities, {Company Name} is also deeply committed to sustainable practices. They recognize the environmental impact of plastic materials and continuously strive to reduce waste and energy consumption. By employing efficient machining processes, recycling initiatives, and material optimization techniques, they ensure minimal environmental footprint in their operations.{Company Name} actively collaborates with their clients to explore eco-friendly alternatives for plastic materials, such as biodegradable or recyclable options. This dedication to sustainability resonates with their customers, who appreciate their responsible manufacturing practices.4. Quality Control and Certifications:Maintaining the highest standards in quality control is of utmost importance to {Company Name}. They adhere to rigorous quality management systems, ensuring that each plastic component meets or exceeds industry standards. Their manufacturing processes are not only ISO 9001 certified but also comply with other relevant certifications as per industry requirements.Utilizing advanced measurement tools and inspection techniques, {Company Name} conducts thorough testing and inspections throughout the entire machining process. This meticulous approach guarantees the delivery of flawless components, meeting the stringent specifications of their clients.Conclusion:{Company Name}'s continuous innovation in CNC machining for plastic materials has revolutionized the manufacturing sector. Their cutting-edge technology, industry expertise, and commitment to sustainability have positioned them as leaders in the field. By enabling precision, efficiency, and quality, {Company Name} sets a benchmark for excellence, meeting the diverse needs of clients across multiple industries. As they continue to push boundaries and embrace advancements in CNC machining, {Company Name} ensures a brighter future for plastic manufacturing, enhancing products and revolutionizing industries worldwide.
Understanding the Key Components of a CNC Lathe
[Company Introduction: The {Company} is a leading manufacturer of CNC machines, specializing in producing high-quality and innovative machining solutions. With a strong emphasis on research and development, the company has continuously pushed the boundaries of CNC technology, making its machines highly sought after by manufacturers worldwide.]The {Company} has been at the forefront of the CNC machine industry, providing state-of-the-art solutions for manufacturers across various sectors. One of its most notable offerings is the CNC lathe, a versatile machine tool used for shaping metal, wood, or other materials. The CNC lathe is known for its precision, efficiency, and capability to perform a wide range of machining operations.While the CNC lathe is a complex machine, it is composed of several key parts that work together to achieve precise and efficient turning operations. These parts include:1. Bed: The bed is the base of the CNC lathe and provides a stable platform for supporting all other components. It is usually made of high-quality cast iron to ensure rigidity and stability during machining operations.2. Headstock: The headstock houses the main spindle, which is responsible for rotating the workpiece at high speeds. It also contains the gear train, which allows for speed changes and power transmission to the spindle.3. Tailstock: The tailstock is located at the opposite end of the headstock and serves as a support for long workpieces. It can be moved along the bed to accommodate different lengths of materials and can be adjusted to hold the workpiece firmly in place.4. Tool turret: The tool turret holds various cutting tools that are used for shaping the workpiece. It can be indexed to bring different tools into the cutting position, allowing for complex machining operations to be performed without manual tool changes.5. Slide: The slide is responsible for the movement of the cutting tool relative to the workpiece. It consists of a saddle and cross-slide, which can be controlled and programmed to achieve precise cutting dimensions.6. Control panel: The control panel is the interface through which the operator can input commands and program the CNC lathe. It contains a display screen, keyboard, and control buttons, allowing for the input of cutting parameters, tool movements, and other machining instructions.7. Chuck: The chuck is a device used for holding the workpiece securely in place during machining operations. It can be either manual or automatic, and it provides the necessary grip to prevent the workpiece from moving during turning.8. Coolant system: The coolant system is responsible for maintaining the temperature of the cutting tools and workpiece during machining. It also helps to flush away chips and debris, improving the overall surface finish and prolonging tool life.The {Company} has incorporated advanced technologies and innovative design features into its CNC lathes, making them highly efficient and reliable for a wide range of machining applications. With a commitment to quality and precision, the company continues to set the benchmark for CNC machine tools, providing manufacturers with the best-in-class solutions for their production needs.In conclusion, the CNC lathe is a highly versatile and essential machine tool for the manufacturing industry, and its component parts play a crucial role in achieving precise and efficient turning operations. The {Company} has been at the forefront of CNC lathe technology, offering advanced solutions that meet the evolving needs of manufacturers worldwide. With a focus on innovation and quality, the company has established itself as a leader in the CNC machine industry, providing cutting-edge solutions that enhance productivity and efficiency in manufacturing operations.
Expert Tips for Cnc Machining Brass and Getting the Best Results
CNC Machining Brass - The Latest Innovation from a Leading Manufacturing CompanyIn the world of manufacturing, precision and efficiency are paramount. One company that has always been at the forefront of technological advancements in the industry is {}. Known for their commitment to quality and continuous improvement, they have recently introduced a new innovation in the form of CNC machining brass.CNC machining, or computer numerical control machining, is a process that utilizes computerized controls and machine tools to remove material from a workpiece, creating a custom-designed part or product. This method allows for a high level of precision and accuracy, making it an ideal choice for manufacturing components with complex geometries and tight tolerances.Brass, a versatile metal alloy composed of copper and zinc, is widely used in various industries due to its excellent corrosion resistance, electrical conductivity, and aesthetic appeal. The combination of CNC machining and brass opens up a world of possibilities for producing intricate and durable parts that meet the demanding requirements of modern manufacturing.With this latest innovation, {} is poised to further solidify its position as a leader in the manufacturing sector. By leveraging state-of-the-art CNC machining technology and their extensive expertise in working with brass, the company is able to provide its customers with a wide range of high-quality precision components that are tailored to their specific needs.One of the key advantages of CNC machining brass is its ability to deliver consistent and uniform results. The computerized controls ensure that each part is manufactured with unparalleled accuracy, minimizing the margin for error and guaranteeing superior quality. This level of precision is essential for industries such as aerospace, automotive, electronics, and medical devices, where reliability and performance are non-negotiable.Furthermore, the use of brass in CNC machining offers exceptional durability and longevity. The inherent strength of brass, combined with the precise manufacturing process, results in parts that can withstand harsh conditions and heavy usage without compromising their integrity. This makes the technology particularly well-suited for applications that demand resilience and endurance.In addition to its technical advantages, CNC machining brass also offers aesthetic benefits. Brass has a distinctive golden hue that exudes a sense of sophistication and luxury, making it a popular choice for products that require both functionality and visual appeal. By harnessing the capabilities of CNC machining, {} can create brass components with fine details and smooth finishes that enhance their overall appearance.The introduction of CNC machining brass is a testament to {}'s ongoing dedication to pushing the boundaries of what is possible in manufacturing. By investing in cutting-edge technology and continuously refining their processes, the company is able to stay ahead of the curve and meet the evolving needs of the market.As an industry leader, {} is committed to providing comprehensive solutions that deliver maximum value to its customers. Whether they require small-scale prototypes or large-scale production runs, clients can rely on {}'s expertise to deliver top-quality brass components that are tailored to their exact specifications.With the introduction of CNC machining brass, {} is poised to set new standards for precision manufacturing. By combining the versatility of brass with the capabilities of CNC machining, the company is offering a compelling solution for businesses that demand nothing but the best.In conclusion, the unveiling of CNC machining brass by {} represents a significant milestone in the world of manufacturing. With this innovative technology, the company is able to offer an unparalleled level of precision, durability, and aesthetic appeal in the production of brass components. As the industry continues to evolve, {} remains committed to driving progress and delivering exceptional results for its clients.
Boost Your Manufacturing Process with Efficient 3-Axis CNC Machining
Title: Revolutionary 3-Axis CNC Machining Ushering in a New Era of Precision ManufacturingIntroduction:In the fast-paced world of manufacturing, companies are constantly seeking more efficient and accurate methods to produce high-quality products in a cost-effective manner. This quest for excellence has driven the development of advanced technologies such as the revolutionary 3-axis CNC machining system. With its exceptional precision and versatility, this cutting-edge methodology has garnered worldwide acclaim, transforming the manufacturing landscape across industries.Body:1. What is 3-Axis CNC Machining?At its core, 3-axis CNC machining is a computer-controlled process used to shape materials such as metal, plastic, or wood, providing unparalleled precision and repeatability. This technology enables the creation of complex and intricate designs with remarkable speed and accuracy, far surpassing the capabilities of traditional manual machining.2. The Advantages of 3-Axis CNC Machining:a. Precision: The precise movement of the 3-axis CNC machine ensures accurate and consistent outcomes, reducing human errors to an absolute minimum. This level of precision allows manufacturers to create highly intricate and complex designs that were once unachievable.b. Versatility: Unlike other machining methods, 3-axis CNC machining offers unparalleled versatility. It can be used to shape a wide range of materials, from plastics to metals, with ease. This adaptability enables manufacturers to cater to diverse industries, from automotive and aerospace to electronics and medical.c. Efficiency: The automation capabilities of 3-axis CNC machining dramatically enhance efficiency. This system can run continuously, maximizing productivity while minimizing downtime traditionally associated with manual operations. Additionally, the ability to program the machine precisely allows for the replication of parts with consistent quality, further speeding up the manufacturing process.d. Cost-effectiveness: Although initial investment costs may be higher, 3-axis CNC machining saves money in the long run. The reduced labor requirements and increased efficiency lead to lower operating costs, improved productivity, and minimized waste. Furthermore, this method allows for the production of intricate designs without costly manual labor, making it an economical choice for manufacturers.3. Applications of 3-Axis CNC Machining:The versatility of 3-axis CNC machining has enabled its application in numerous industries. Below are some areas where this technology is extensively used:a. Automotive: In the automotive industry, 3-axis CNC machining is employed to produce high-precision components, such as engine parts, transmission components, and intricate car body shapes.b. Aerospace: The aerospace industry relies on 3-axis CNC machining to create vital parts such as turbine blades, control surfaces, and structural components. The consistent precision and reliability of this technology are critical for ensuring flight safety.c. Electronics: The production of complex electronic devices demands precise machining, making 3-axis CNC machining a preferred option. It is used to manufacture circuit boards, connectors, and intricate casings, guaranteeing a high level of precision and minimizing electrical malfunctions.d. Medical: In the medical field, 3-axis CNC machining is essential for the manufacturing of intricate surgical instruments, implants, orthopedic devices, and prosthetics. This technology allows for precision that is crucial in these life-saving applications.Conclusion:The advent of 3-axis CNC machining has revolutionized precision manufacturing across industries. Its unparalleled precision, versatility, efficiency, and cost-effectiveness have made it an integral part of modern manufacturing processes, elevating the standard of quality and contributing to technological advances. As technology continues to evolve, 3-axis CNC machining is expected to further enhance manufacturing capabilities, driving innovation and propelling various industries toward a future of unprecedented precision and efficiency.