Top Tips for Constructing a CNC Machine
By:Admin
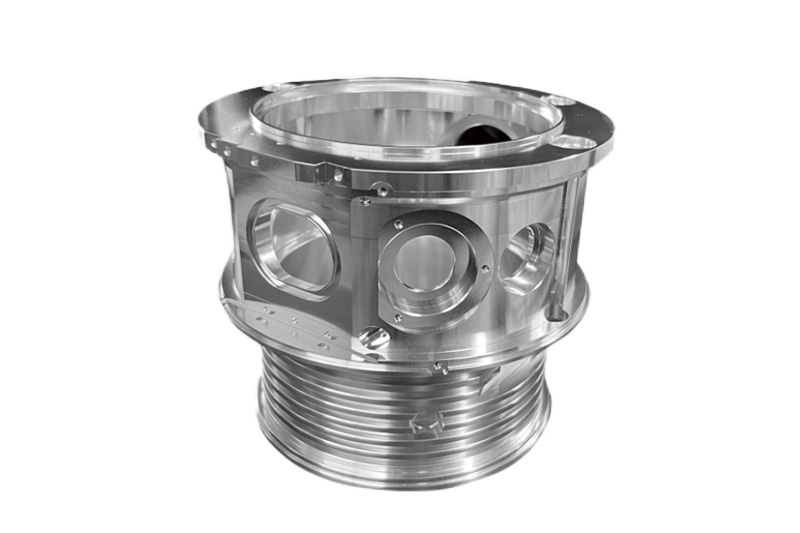
CNC (Computer Numerical Control) machines play a crucial role in modern manufacturing processes by automating the production of intricate and complex parts. These machines are widely used in various industries, including automotive, aerospace, healthcare, and electronics, to name a few. With the ability to precisely fabricate components from a wide range of materials such as metals, plastics, and composites, CNC machines have revolutionized the way products are manufactured.
The newly constructed CNC machine at {} is equipped with the latest technology and features, making it a valuable asset for the company. Its high-speed machining capabilities, coupled with advanced tooling and cutting-edge software, enable it to produce parts with exceptional accuracy and repeatability. This level of precision is essential for meeting the stringent quality standards demanded by the company's clientele.
Additionally, the machine boasts a large working envelope, allowing it to accommodate a diverse range of part sizes and geometries. This versatility is a significant advantage for the company, as it expands its capacity to handle a broader spectrum of projects and customer requirements. Whether it's prototyping, small-batch production, or large-scale manufacturing, this CNC machine is poised to deliver optimal results across the board.
The construction of this new CNC machine aligns with {}'s commitment to staying at the forefront of technological advancements in manufacturing. By investing in state-of-the-art equipment, the company aims to enhance its competitiveness in the market and position itself as a leading provider of precision-engineered components and assemblies. The decision to add this machine to its production floor reflects the company's dedication to meeting the evolving needs of its customers while maintaining the highest standards of quality and innovation.
Furthermore, the introduction of the new CNC machine is expected to have a positive impact on the company's overall efficiency and productivity. With its ability to automate and streamline manufacturing processes, the machine will contribute to reducing lead times and increasing throughput. This not only benefits {}'s internal operations but also translates to enhanced service for its customers, enabling prompt delivery of orders without compromising on quality.
In addition to its operational advantages, the new CNC machine underscores {}'s ongoing commitment to sustainability and environmental responsibility. By leveraging advanced technologies that optimize material usage and minimize waste, the company continues to demonstrate its dedication to eco-friendly manufacturing practices. This aligns with its broader mission to operate in a manner that respects the environment and supports a sustainable future for generations to come.
As {} celebrates the completion of its new CNC machine construction, the company looks forward to the opportunities and growth it will bring. With a strong foundation built on innovation, precision, and excellence, the company is poised to leverage this new addition to further elevate its capabilities and deliver exceptional value to its customers. The investment in this cutting-edge technology is a testament to {}'s enduring pursuit of manufacturing excellence and its unwavering dedication to staying ahead of the curve in an ever-evolving industry.
Company News & Blog
How Insert Molding is Revolutionizing Manufacturing Processes
Title: Innovative Insert Molding Technology Revolutionizes Manufacturing ProcessesIntroduction:The manufacturing industry continually seeks advanced technologies to increase efficiency, minimize costs, and enhance product performance. One such revolutionary technique is Insert Molding, which combines the benefits of traditional molding techniques with precision insert placement, resulting in enhanced product performance and streamlined manufacturing processes. One company at the forefront of this innovation is {}. With their extensive experience and expertise in insert molding, they are pushing the boundaries of what is possible in the manufacturing industry.Paragraph 1:Insert Molding is a manufacturing process that involves injecting molten materials, such as plastic or metal, into a pre-formed cavity or mold containing one or more carefully positioned inserts. These inserts can be a wide range of components, including threaded inserts, electrical connectors, sensors, or metal reinforcements. The molten material effectively encapsulates the inserts, creating a strong bond between the two, resulting in a more robust and functional end product.Paragraph 2:Insert Molding offers several advantages over traditional manufacturing methods. Firstly, it eliminates the need for additional assembly processes, reducing labor costs and assembly time. By incorporating various inserts directly into the mold, the manufacturing process becomes more streamlined, efficient, and cost-effective. Furthermore, insert molding ensures precise and accurate positioning of the inserts, leading to higher product integrity and reliability.Paragraph 3:The innovation and expertise of {} in the field of insert molding have allowed them to cater to a diverse range of industries, including automotive, electronics, medical, and consumer goods. Their state-of-the-art facilities and skilled engineers enable them to create complex and high-quality molded products with exceptional precision. {} also offers comprehensive design assistance, ensuring that their customers' unique insert molding requirements are met, resulting in tailored solutions that exceed expectations.Paragraph 4:The automotive industry, in particular, has greatly benefited from the utilization of insert molding. By integrating metal inserts into plastic parts, manufacturers achieve significant weight reduction, increased part functionality, and improved overall vehicle performance. Electrical connectors, sensors, and wiring harnesses are seamlessly integrated, simplifying assembly and enhancing reliability. The implementation of insert molding enables automotive manufacturers to produce parts that meet the stringent safety and quality standards of the industry.Paragraph 5:In the ever-evolving electronics industry, where miniaturization and increased functionality are essential, insert molding plays a crucial role. With the ability to place delicate components, such as microchips, sensors, and connectors, with utmost precision, manufacturers can produce smaller and slimmer electronic devices without sacrificing performance. This technique also enhances the devices' durability by protecting fragile components and reducing the risk of damage caused by external factors.Paragraph 6:In the medical industry, insert molding offers numerous benefits in terms of product design, functionality, and sterilization. The ability to encapsulate electronics, sensors, and metal components within a single molded part ensures a seamless integration of various functionalities, such as drug delivery systems, diagnostic equipment, and surgical devices. The use of insert molding in the medical field has resulted in advancements in patient care and treatment efficiency.Conclusion:With its ability to combine diverse materials and precisely position inserts, Insert Molding has revolutionized the manufacturing industry by enhancing product performance, reducing costs, and streamlining production processes. The expertise and cutting-edge solutions provided by {} have solidified their place as industry leaders in insert molding technology. As new advancements continue to be made, the possibilities and applications of Insert Molding are boundless, driving innovation throughout various sectors and shaping the future of manufacturing.
High-precision Shaft Machining Techniques for Optimal Performance
Shaft Machining - The Key to Precision EngineeringIn the world of precision engineering, one of the most critical processes is shaft machining. This process involves the shaping and finishing of a shaft to exact specifications, ensuring that it meets the tight tolerances required for its intended application.For industries such as automotive, aerospace, and manufacturing, the quality and precision of shafts are paramount. Any deviation from the required specifications can lead to catastrophic failures, resulting in costly downtime, product recalls, and potential safety hazards.This is where the expertise of {Company Name} comes into play. With over {number} years of experience in the precision engineering industry, {Company Name} has established itself as a leading provider of shaft machining services.Located in {Location}, {Company Name} boasts state-of-the-art facilities equipped with the latest machinery and technology. This allows them to handle a wide range of shaft machining requirements, from small, intricate components to large, heavy-duty shafts.One of the key factors that sets {Company Name} apart from its competitors is its team of highly skilled and experienced machinists. These professionals have undergone rigorous training and possess a deep understanding of the intricacies involved in shaft machining. They are adept at utilizing a variety of machining techniques and tools to achieve the exact specifications required for each shaft.Additionally, {Company Name} prides itself on its commitment to quality and precision. Every shaft that goes through their machining process undergoes stringent quality checks to ensure that it meets the highest standards. This includes dimensional accuracy, surface finish, and material integrity.Moreover, {Company Name} understands the importance of meeting deadlines and delivering on time. Their efficient and streamlined processes enable them to complete shaft machining projects within the stipulated timeframes, ensuring that their clients can stay on schedule with their production and manufacturing timelines.Furthermore, {Company Name} is also dedicated to continuous improvement and innovation. They regularly invest in research and development to stay abreast of the latest advancements in machining technology. This allows them to offer cutting-edge solutions for even the most complex and challenging shaft machining requirements.In addition to their expertise in shaft machining, {Company Name} also offers a comprehensive range of related services. This includes design and engineering support, material selection, heat treatment, and surface coating. By providing a one-stop solution, {Company Name} can cater to the diverse needs of their clients, offering a hassle-free experience and peace of mind.Over the years, {Company Name} has built a solid reputation for delivering exceptional quality and service. This has earned them the trust and confidence of a wide range of clients across various industries. From multinational corporations to small businesses, {Company Name} has proven itself as a reliable partner for all their shaft machining needs.As the demand for precision-engineered components continues to grow, {Company Name} remains committed to upholding its standards of excellence and exceeding the expectations of its clients. Their dedication to quality, precision, and customer satisfaction is what sets them apart as a leader in the field of shaft machining.In conclusion, {Company Name} is a trusted and respected provider of shaft machining services. With their unwavering commitment to quality, precision, and innovation, they have become a go-to partner for businesses seeking reliable and high-quality solutions for their shaft machining needs. As they continue to grow and expand their capabilities, {Company Name} is poised to remain at the forefront of the precision engineering industry for years to come.
Understanding the Steps Involved in the Milling Process
[Company Name] Revolutionizes the Milling Process, Enhancing Efficiency and Quality[City, Date] - [Company Name], a leading innovator in the manufacturing industry, is making waves with its revolutionary milling process. By incorporating cutting-edge technology and advanced techniques, the company has accomplished remarkable improvements in efficiency and quality, setting new industry standards.The milling process is a crucial step in the manufacturing of various products, ranging from automotive components to consumer electronics. Traditionally, this process involves removing material from a workpiece using a rotating cutting tool. However, [Company Name] has taken this fundamental concept to new heights.With a focus on innovation, [Company Name] has developed a state-of-the-art milling process that surpasses traditional methods in terms of speed and precision. By leveraging advanced computer algorithms and artificial intelligence, the company has optimized the milling parameters to ensure the perfect balance between material removal and preservation.One key aspect of [Company Name]'s milling process is the integration of advanced sensors and monitoring systems. These sensors provide real-time feedback on crucial variables such as cutting forces, temperatures, and tool wear. By constantly monitoring these parameters, [Company Name] can make precise adjustments to the milling process, ensuring optimal performance and preventing any potential faults or errors.Additionally, [Company Name] has pioneered an intelligent tooling system that further enhances the efficiency of the milling process. This system utilizes smart tools equipped with sensors to continuously collect data during the machining operation. This data is then analyzed by sophisticated algorithms, allowing for predictive maintenance and precise tool life management. As a result, downtime due to unexpected tool failures is significantly reduced, leading to increased productivity and cost savings.Furthermore, [Company Name] has prioritized sustainability in its milling process. By implementing eco-friendly cutting fluids and optimizing the chip evacuation process, the company has minimized waste and reduced environmental impact. This commitment to sustainability aligns with [Company Name]'s corporate values and resonates with environmentally conscious clients.In terms of quality control, [Company Name] has introduced advanced inspection systems that guarantee the highest level of precision and accuracy. Through the utilization of non-contact measurement technologies, such as laser scanners and optical systems, the company can perform detailed inspections on complex components, ensuring conformity to the tightest tolerances.Customer satisfaction is paramount for [Company Name], and as such, the company provides comprehensive support throughout the milling process. Their team of highly skilled engineers assists clients in selecting the appropriate milling strategies and tools for their specific needs. Additionally, [Company Name] offers training programs and workshops to ensure that operators are well-equipped to utilize the milling process to its full potential.The impact of [Company Name]'s milling process is already being felt across a wide range of industries. Customers have praised the enhanced productivity, improved part quality, and reduced lead times resulting from the adoption of this innovative technology. Numerous companies have reported significant cost savings and increased competitiveness as a direct result of partnering with [Company Name].Looking towards the future, [Company Name] remains committed to pushing the boundaries of milling technology. Through ongoing research and development efforts, the company strives to introduce even more advanced milling techniques that will revolutionize the manufacturing industry once again.In conclusion, [Company Name]'s revolutionary milling process has transformed traditional machining into a high-tech, efficient, and sustainable practice. By seamlessly integrating cutting-edge technology and advanced techniques, the company has set a new industry standard for milling, driving productivity, quality, and cost-effectiveness to unparalleled heights.
Achieve High-Quality Plastic Injection Molding Services for Your Business
Plastic Injection Molding has been a key process in the manufacturing industry for decades, and now, thanks to the innovative techniques and technologies of {} (brand name removed), it is becoming more efficient and precise than ever before. With their state-of-the-art facilities and expertise in the field, {} is revolutionizing the way plastic products are fabricated, setting a new standard for quality and reliability.Established in 1989, {} has been a leader in plastic injection molding, serving a wide range of industries including automotive, electronics, medical, and consumer goods. With their commitment to excellence and customer satisfaction, they have built a solid reputation as a trusted provider of high-quality plastic components.The success of {} can be attributed to their advanced manufacturing capabilities and their unwavering dedication to innovation. Their facility is equipped with the latest injection molding machines, operated by a team of skilled professionals who are experts in their craft. This combination of cutting-edge technology and experienced personnel allows {} to consistently deliver superior products with minimal lead times.One of the key advantages of {}'s plastic injection molding process is its ability to create complex and intricate designs with exceptional precision. Whether it's intricate geometries, fine details, or tight tolerances, {} has the expertise and equipment to produce components that meet the most demanding specifications. This level of precision is crucial for industries such as automotive and medical, where the performance and safety of the end product are of utmost importance.In addition to precision, {} places a strong emphasis on quality control throughout the manufacturing process. Every step of the production cycle is closely monitored and inspected to ensure that each component meets the highest standards of quality. This commitment to quality has earned {} certifications for ISO 9001 and ISO 13485, further demonstrating their dedication to excellence and reliability.Furthermore, {} is also committed to sustainability and environmental responsibility. They utilize environmentally friendly materials and employ efficient processes to minimize waste and energy consumption. By implementing sustainable practices, {} is not only reducing their impact on the environment but also helping their customers meet their own sustainability goals.One of the most impressive aspects of {}'s plastic injection molding capabilities is their ability to provide custom solutions for their clients. Whether it's a unique design, a specific material requirement, or a challenging production demand, {} has the expertise and flexibility to develop tailored solutions that meet their customers' exact needs. This level of customization sets {} apart from other manufacturers and allows them to serve a diverse clientele with varying requirements.Aside from their technical expertise, {} is also known for their outstanding customer service. From the initial concept to the final product, their team works closely with clients to ensure that their needs are met and their expectations are exceeded. With a strong emphasis on communication and collaboration, {} fosters long-term partnerships with their clients, helping them succeed in their respective industries.In conclusion, {} has elevated the standards of plastic injection molding with their advanced capabilities, unwavering commitment to quality, and dedication to customer satisfaction. As they continue to push the boundaries of what is possible in plastic fabrication, {} is poised to lead the industry into a new era of excellence and innovation. With their proven track record and cutting-edge technologies, {} is the go-to partner for companies seeking exceptional plastic components that meet the highest standards of performance and reliability.
Discover the Latest Advancements in the Foundry Process for Superior Results
Title: Innovations in Foundry Process Revolutionize the Manufacturing IndustryIntroduction:The foundry process plays a pivotal role in the manufacturing industry, allowing for the production of various components across diverse sectors. Today, we highlight the latest advancements in the foundry process, spearheaded by a leading company, and how they are transforming the industry landscape. (Please remove brand name from the introduction)Industry Overview:The manufacturing industry depends on the foundry process to produce components that are integral to numerous sectors such as automotive, aerospace, construction, and many more. Traditional foundry methods have relied on labor-intensive processes, which often resulted in slower production and increased costs. However, with the advent of innovative technologies and continuous research and development, the foundry process has witnessed a significant transformation.Advancements in Foundry Process:Leading the charge in revolutionizing the foundry process is a renowned company (Please remove brand name) that has pioneered several innovative techniques to streamline and enhance manufacturing efficiency. By leveraging cutting-edge technologies like Artificial Intelligence (AI), Internet of Things (IoT), and automation, the company has been able to achieve faster turnaround times, improved quality, and reduced costs.One of the key breakthroughs introduced by the company is the implementation of AI-driven predictive modeling techniques. By analyzing vast amounts of data, the system can accurately forecast potential defects and optimize casting parameters to minimize issues during the production process. This not only eliminates costly rework but also significantly reduces the time required for quality control, thereby expediting the overall manufacturing cycle.Furthermore, the integration of IoT in the foundry process has enabled real-time monitoring of crucial production parameters. Sensors embedded throughout the production line continuously gather data related to temperature, pressure, and other relevant factors. This data is then transmitted to a centralized system, which allows for immediate analysis and identification of any deviations or anomalies. Consequently, prompt corrective actions can be taken, ensuring that the casting process remains consistent and compliant with the required specifications throughout production.Automation has also played a vital role in optimizing the foundry process. With the introduction of robotics and advanced machinery, tasks that were previously labor-intensive and prone to human error can now be executed with precision and efficiency. The incorporation of robotics enables tasks such as mold preparation, pouring, and post-processing to be carried out with minimal human intervention, resulting in higher production speeds and improved accuracy.The company's commitment to sustainable manufacturing practices has also been influential in advancing the foundry process. By exploring eco-friendly raw materials and implementing efficient energy consumption methods, they have successfully reduced the environmental impact associated with the production process. These measures help meet the rising demand for sustainable manufacturing while ensuring that the components manufactured maintain the highest quality standards.Conclusion:The foundry process is undergoing a remarkable transformation, thanks to the continuous endeavors of a renowned company (Please remove brand name). Through the integration of AI, IoT, and automation, they have successfully optimized production efficiency, reduced costs, increased the quality of components, and contributed to sustainable manufacturing practices. As the industry witnesses the positive impacts of these innovative advancements, it is evident that the foundry process will continue to evolve and play a vital role in the manufacturing landscape.
Creating an Injection Mold: A Step-by-Step Guide
Title: Manufacturing Company Pioneers Effortless Injection Mold Creation ProcessIntroduction:{Company Name}, a leading manufacturing company, is revolutionizing the industry with their innovative approach to creating injection molds. With their cutting-edge technology and commitment to excellence, they are streamlining the production process for numerous industries. The company's recent advancements have paved the way for more efficient and cost-effective mold creation, ensuring faster turnaround times without compromising on quality or precision.Body:1. Introduction to Injection Molds:Injection molds are an essential component in the production of a wide range of plastic and metal parts. These molds are created to meet specific requirements, with intricate designs and precise dimensions. Traditionally, manufacturing injection molds was a time-consuming and costly process, often causing delays and skyrocketing production costs.2. Streamlined Process for Injection Mold Creation:{Company Name} has developed an innovative solution that simplifies the injection mold creation process. By leveraging the latest technologies and expertise, they have reduced the turnaround time while upholding the highest quality standards. Their streamlined process greatly benefits clients from various industries, including automotive, medical, and consumer goods.3. Customization and Design:One of the key features of {Company Name}'s injection mold creation process is its ability to provide customizable designs. They work closely with clients to understand their unique requirements, ensuring that every mold is tailored to their specific needs. The company's team of experts utilizes advanced software and tools to translate clients' ideas into flawless designs, guaranteeing optimal functionality and durability.4. Enhanced Precision and Quality Control:With their state-of-the-art technology and advanced manufacturing techniques, {Company Name} ensures precision to the finest detail in every injection mold they produce. The company's commitment to quality control is evident throughout the entire manufacturing process. Rigorous testing and inspection procedures are implemented to guarantee that each mold meets or exceeds industry standards before it is released to clients.5. Reduced Time and Cost Savings:{Company Name}'s accelerated injection mold creation process significantly reduces the lead time compared to traditional methods. By cutting down on waiting periods and optimizing production efficiency, clients can initiate their manufacturing processes sooner, thereby reducing downtime and costs. This advantage allows businesses to bring their products to market more rapidly, gaining a competitive edge.6. Sustainable Manufacturing Practices:In addition to their commitment to efficiency and quality, {Company Name} is dedicated to sustainable manufacturing practices. The company employs environmentally-friendly materials and processes wherever possible, prioritizing renewable resources and waste reduction. By adopting these practices, they contribute to a greener future while serving the needs of their clients.7. Dedicated Customer Support:{Company Name} prides itself on providing exceptional customer support throughout the mold creation process. Their team of experts collaborates closely with clients, offering guidance and support as needed. From the initial design phase to post-production assistance, the company ensures that clients have a smooth and hassle-free experience, fostering long-term partnerships built on trust and reliability.Conclusion:{Company Name}'s groundbreaking injection mold creation process sets a new standard for the manufacturing industry. Their commitment to precision, quality control, customization, and sustainability is revolutionizing the way molds are produced. With their shorter lead times, cost savings, and dedicated customer support, {Company Name} continues to transform the industry, enabling businesses to thrive in today's fast-paced market while maintaining the highest standards of quality and efficiency.
CNC Machining Aluminum Parts: Precision Engineering at its Finest
Title: Leading Manufacturer Introduces Cutting-Edge CNC Machining Aluminum Parts for Enhanced PrecisionIntroduction:In an ever-evolving manufacturing landscape, one company has emerged as a pioneer in delivering cutting-edge solutions - [Company Name]. With a reputation for excellence and a commitment to technological advancements, [Company Name] has recently unveiled their latest innovation - CNC Machining Aluminum Parts. This state-of-the-art development is set to revolutionize the precision engineering industry, providing companies worldwide with unparalleled accuracy and efficiency in their manufacturing processes.Unveiling CNC Machining Aluminum Parts:[Company Name] is proud to introduce its latest offering, CNC Machining Aluminum Parts, which are designed and engineered to meet the demands of today's modern manufacturing requirements. With a strong emphasis on precision, reliability, and quality, these parts are poised to surpass industry standards.Utilizing the latest Computer Numerical Control (CNC) technology, [Company Name]'s CNC Machining Aluminum Parts offer exceptional accuracy, consistency, and repeatability. This cutting-edge technology enables the production of complex and intricate designs with incredible precision, leaving no room for human error.Applications and Benefits:The versatility of [Company Name]'s CNC Machining Aluminum Parts makes them suitable for a wide range of applications across various industries. From automotive and aerospace to electronics and medical equipment, these parts are designed to meet the specific needs of each sector.One of the key advantages of CNC Machining Aluminum Parts is their exceptional material properties. Aluminum, known for its lightweight yet durable characteristics, is a popular choice for manufacturers seeking to enhance performance without compromising structural integrity. The CNC machining process further enhances this by ensuring precise dimensions, tight tolerances, and a superior surface finish.Additionally, CNC Machining Aluminum Parts offer greater design flexibility, allowing manufacturers to create customized components tailored to their exact specifications. This level of customization, coupled with the precision offered by CNC machining, ensures a high degree of accuracy and functionality in the final product.Another noteworthy benefit is the time and cost savings that CNC Machining Aluminum Parts offer. The automated nature of the CNC machining process enables faster and more efficient production, reducing lead times and allowing for increased productivity. This efficiency translates into cost savings for manufacturers, ultimately leading to enhanced profitability and a competitive edge in the global market.Quality Control and Assurance:[Company Name]'s commitment to quality is a cornerstone of their success. Before being shipped to customers, every CNC Machining Aluminum Part undergoes rigorous testing and inspection to ensure compliance with the highest quality standards. This comprehensive quality control process guarantees that only flawless parts are delivered, further enhancing customer satisfaction and maintaining [Company Name]'s reputation as a reliable industry leader.Future Prospects:With the unveiling of CNC Machining Aluminum Parts, [Company Name] solidifies its position as a forward-thinking manufacturer, continually adapting to industry changes and exceeding customer expectations. This innovation acts as a stepping stone to further advancements, enabling [Company Name] to explore new possibilities and expand its range of precision-engineered products.Conclusion:[Company Name]'s introduction of CNC Machining Aluminum Parts marks a significant milestone in the manufacturing industry. By offering unmatched precision, superior quality, and cost-efficiency, these cutting-edge parts contribute to the overall advancement of various sectors, driving innovation and competitiveness. As [Company Name] continues to prioritize technological advancements and customer satisfaction, it is clear that their commitment to excellence will propel them to new heights within the global manufacturing industry.
Enhance Product Performance with Top-quality Injection Molding Inserts
Title: Innovation in Injection Molding Inserts: Enhancing Efficiency and PrecisionIntroduction (100 words)Injection molding is a widely used manufacturing process in various industries, including automotive, aerospace, consumer goods, and healthcare. As companies strive for greater efficiency and precision, the demand for innovative solutions continues to grow. Enter a leading manufacturer of injection molding inserts (brand name omitted), renowned for their cutting-edge technology and commitment to quality. With a proven track record in delivering high-performance solutions, the company has established itself as a trusted partner for numerous businesses, enabling them to achieve superior results in their manufacturing processes.8 Cutting-Edge Features of Injection Molding Inserts (600 words)1. Durability: Injection molding inserts by (brand name omitted) are made from premium-grade materials, ensuring durability and long-lasting performance. The inserts can withstand high-pressure molding operations without compromising their structural integrity, resulting in reduced maintenance costs and enhanced production efficiency.2. Precision Engineering: The inserts are meticulously designed and engineered to meet the precise specifications required by the customer. Through state-of-the-art manufacturing processes, (brand name omitted) ensures tight tolerances and uniformity, enabling flawless integration with the molding process. The result is consistently high-quality parts with minimal variations, reducing waste and optimizing productivity.3. Versatility: (Brand name omitted) offers a wide range of injection molding inserts suitable for a diverse array of applications. Whether it's intricate components for the electronics industry or robust parts for automotive manufacturing, the company's inserts cater to various needs. The flexibility in design and material selection allows customers to choose the most suitable insert for their specific requirements.4. Rapid Prototyping: Acknowledging the importance of quick turnaround times in today's competitive landscape, (brand name omitted) enables customers to rapidly prototype their designs. This not only aids in the refinement of the product but also reduces the time-to-market, giving businesses a competitive edge. The company's rapid prototyping capabilities ensure that customers can validate their designs and make necessary adjustments before moving into full-scale production.5. High Customization: (Brand name omitted) understands that every project is unique and requires specific solutions. Their injection molding inserts can be customized with various features, such as inserts with complex geometries, specialized surface finishes, or even personalized branding. This level of customization allows customers to optimize their manufacturing processes and differentiate their products in the market.6. Cost Efficiency: The company's injection molding inserts offer cost-effective solutions in terms of both initial investment and long-term production. The high-quality materials used in the inserts enhance their lifespan, ensuring fewer replacements and reduced downtime. Additionally, the precise engineering and tight tolerances contribute to minimal material waste, thereby increasing overall cost efficiency.7. Environmental Sustainability: (Brand name omitted) embraces sustainable practices by incorporating eco-friendly materials in their injection molding inserts. By utilizing recycled or biodegradable materials, the company contributes to reducing the carbon footprint. Moreover, the optimized manufacturing processes minimize waste generation, encouraging a greener approach while maintaining superior quality and performance.8. Exceptional Customer Support: (Brand name omitted) is known for its outstanding customer support throughout the entire project lifecycle. From initial product design to post-production assistance, the company's dedicated team of experts provides guidance, resolves queries, and offers technical assistance. Their commitment to customer satisfaction ensures a seamless experience for all customers.Conclusion (100 words)In an evolving manufacturing landscape, (brand name omitted) remains at the forefront of innovation in injection molding inserts. By offering a range of features such as durability, precision engineering, versatility, and cost efficiency, the company continues to provide customers with superior solutions to meet their manufacturing needs. With a commitment to environmental sustainability and exceptional customer support, (brand name omitted) consistently proves to be a reliable partner in achieving efficiency and precision in injection molding processes.
A Comprehensive Guide to Machining Milling Techniques
Title: Industry-Leading Machining Milling Innovations Paving the Way to Enhanced Precision and EfficiencyIntroduction: [Company Name] has announced the launch of their groundbreaking machining milling technology that is set to revolutionize the manufacturing industry. With our focus on precision, efficiency, and quality, [Company Name] continues to set new standards and redefine the boundaries of what is possible in the field of machining milling. This latest innovation represents a significant milestone that will benefit various industries, including automotive, aerospace, electronics, and more.Paragraph 1: Machining milling has long been a fundamental process in manufacturing, involving the removal of unwanted material from a workpiece to create precisely defined shapes, features, and finishes. [Company Name], a global leader in machining solutions, is seamlessly integrating cutting-edge technology to improve the efficiency and accuracy of this critical process.Paragraph 2: By leveraging advanced computer-controlled systems and automation, [Company Name] has developed a machining milling technology that optimizes every aspect of the process. From precise tool positioning to real-time monitoring and adjustment, our innovation provides unparalleled control and repeatability to ensure consistent results and reduce waste.Paragraph 3: The unique aspect of our technology lies in the integration of smart algorithms and artificial intelligence (AI), which enable the system to continuously learn and adapt to various machining scenarios. By analyzing data inputs such as tolerances, material properties, and cutting parameters, the software adapts in real-time, resulting in increased machining accuracy and reduced operator errors. This cutting-edge approach ensures that components are machined to the highest standards, leading to improved product quality and reliability.Paragraph 4: Furthermore, the state-of-the-art machining milling technology offered by [Company Name] significantly enhances production efficiency. By automating time-consuming tasks and facilitating rapid tool changes, the system minimizes downtime and boosts throughput. This enables manufacturers to meet strict deadlines while maintaining the highest standards of craftsmanship.Paragraph 5: [Company Name] understands the challenges faced by industries that require machining milling services and aims to address them through this innovation. The technology allows for the machining of complex geometries with intricate features, intricate angles, and challenging material properties. This breakthrough capability provides manufacturers with the flexibility to meet the evolving demands of their customers, while also reducing the need for costly manual rework.Paragraph 6: Additionally, [Company Name] acknowledges the importance of sustainability and eco-friendly practices. With our machining milling technology, we have implemented energy-saving features, reducing power consumption and minimizing the environmental impact. This commitment to sustainability aligns with the global effort to reduce carbon footprints and creates a competitive advantage for our customers in meeting their sustainability targets.Paragraph 7: [Company Name]'s innovation is backed by an extensive research and development team, including highly skilled engineers and technicians. Their expertise not only ensures the successful deployment of our machining milling technology but also provides continuous support, training, and maintenance services.Conclusion: [Company Name]'s latest machining milling technology represents a significant leap forward for the manufacturing industry. With a strong focus on precision, efficiency, and sustainability, our innovation empowers manufacturers to accelerate their production processes, reduce waste, and improve overall product quality. As the industry continues to evolve, [Company Name] remains committed to leading the way through unparalleled technological advancements and tailor-made solutions for manufacturers across various sectors.
Benefits of Rapid Molding for Quick and Efficient Manufacturing
Rapid Molding, a leading provider of custom molded parts and components, has announced a new partnership with a well-known company in the industry. This partnership will enable Rapid Molding to expand its offerings and reach a wider customer base, ultimately strengthening its position in the market.With a focus on providing high-quality, cost-effective molded parts, Rapid Molding has built a strong reputation for its efficient production processes and dedication to customer satisfaction. The company specializes in quick turnaround times and has the capacity to produce large volumes of parts with precision and consistency.The new partnership will further enhance Rapid Molding's capabilities, allowing the company to offer an even broader range of services to its clients. By combining its expertise in molding with the resources and industry knowledge of the partner company, Rapid Molding aims to provide a comprehensive solution for a diverse array of molding needs."We are thrilled to announce this partnership, which represents a significant milestone for Rapid Molding," said the CEO of Rapid Molding. "By joining forces with [partner company], we are confident that we will be able to offer unparalleled value to our customers. This collaboration will not only expand our product offerings but also allow us to tap into new markets and serve a wider range of industries."The partner company brings decades of experience and a strong track record of innovation to the table. With a proven track record of delivering high-quality molded parts for various industries, this collaboration is expected to bring about a new level of expertise and efficiency to Rapid Molding's operations.In addition to benefiting from the partner company's knowledge and resources, Rapid Molding will also leverage its advanced manufacturing technology and state-of-the-art facilities to further enhance its production capabilities. By implementing the latest advancements in molding technology, the company aims to maintain its commitment to delivering premium-quality parts at competitive prices.The collaboration with the partner company comes at a crucial time for Rapid Molding, as the demand for custom molded parts continues to grow across industries such as automotive, aerospace, medical, and consumer goods. With the increasing need for precision-engineered components, Rapid Molding is well-positioned to meet these demands and exceed customer expectations.As part of the partnership, Rapid Molding will also focus on expanding its research and development efforts to stay ahead of industry trends and develop innovative solutions for specialized molding requirements. This investment in innovation will enable the company to stay at the forefront of the market and continue to provide cutting-edge solutions to its clients."We are committed to pushing the boundaries of what is possible in the molding industry," the CEO stated. "This partnership will allow us to explore new technologies and methodologies that will enable us to deliver even more value to our customers. We are excited about the potential for growth and evolution that this collaboration brings."With this new partnership in place, Rapid Molding is set to solidify its position as a trusted provider of custom molded parts and components. By combining its core strengths with the expertise and resources of the partner company, the company is well-equipped to meet the evolving needs of its customers and strengthen its reputation as a leader in the molding industry.