Top Milling Centers for Precision Machining
By:Admin
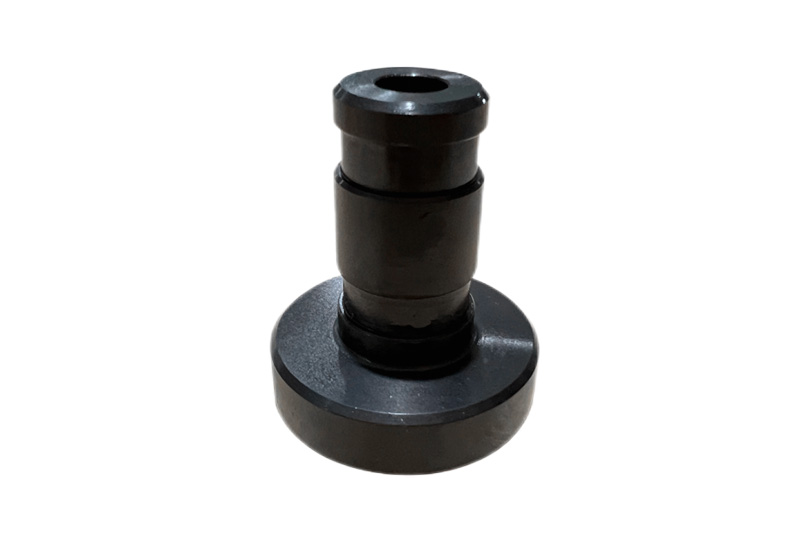
In the world of precision machining, milling centers have become a crucial component of the manufacturing process. These state-of-the-art machines have the capability to perform a wide range of tasks, from simple drilling and tapping to complex contouring and 5-axis machining. With their advanced technology and precision engineering, milling centers have revolutionized the way in which parts and components are manufactured.
One company at the forefront of this revolution is {}. With decades of experience in the manufacturing industry, {} has established itself as a leader in the production of high-quality milling centers. Their machines are known for their exceptional accuracy, reliability, and versatility, making them the go-to choice for a wide range of industries, including aerospace, automotive, medical, and more.
The key to the success of {}'s milling centers lies in their advanced features and capabilities. These machines are equipped with high-speed spindles, automatic tool changers, and sophisticated control systems that enable them to perform complex machining operations with ease. Additionally, {}'s milling centers are designed to be highly rigid and stable, ensuring that they can achieve the tight tolerances and superior surface finishes that are required in modern manufacturing.
One of the most impressive aspects of {}'s milling centers is their ability to perform multi-axis machining. This capability allows for the production of highly complex parts and components that would be nearly impossible to manufacture using conventional machining methods. With multi-axis machining, {}'s milling centers can create intricate shapes and contours with precision and accuracy, opening up new possibilities for designers and engineers.
In addition to their advanced technology, {}'s milling centers are also designed with efficiency and productivity in mind. These machines are equipped with features such as high-speed rapids, chip conveyors, and coolant systems that help to optimize the machining process and minimize downtime. This not only results in lower production costs but also allows manufacturers to meet tight production deadlines with ease.
Another major advantage of {}'s milling centers is their user-friendly design. These machines are equipped with intuitive controls and interfaces that make them easy to operate, even for less experienced machinists. This means that manufacturers can quickly set up and program {}'s milling centers to produce high-quality parts and components with minimal training or supervision.
Furthermore, {} provides comprehensive training and support to ensure that customers are able to get the most out of their milling centers. Whether it's troubleshooting technical issues, optimizing machining processes, or providing guidance on tooling and fixturing, {}'s team of experts is dedicated to helping their customers achieve success with their milling centers.
With the increasing demand for complex and high-precision components, the role of milling centers in modern manufacturing is more important than ever. Companies like {} are continuously pushing the boundaries of what is possible with their innovative machines, allowing manufacturers to produce parts and components that were previously considered unfeasible. As the industry continues to evolve, milling centers will undoubtedly play a vital role in shaping the future of precision machining.
Company News & Blog
Top 5 Applications of Injection Molding in Manufacturing
Injection Molding Application Brings Revolutionary Changes to Manufacturing ProcessesIn today's fast-paced world, manufacturers are constantly seeking new and innovative ways to improve their production processes. One such method that has been gaining widespread attention is injection molding. This advanced manufacturing technique has the potential to bring about revolutionary changes in the way products are designed and produced.Injection molding is a manufacturing process for producing parts by injecting molten material into a mold. It is commonly used for manufacturing a variety of products, including plastic parts, components for medical devices, automotive parts, and consumer goods. This process has gained popularity due to its ability to produce complex and intricate parts with high precision and consistency.One company that has been at the forefront of utilizing injection molding technology is {} (). The company, established in 1990, has carved a niche for itself in the manufacturing industry by providing high-quality injection-molded parts for a wide range of applications. With a state-of-the-art facility equipped with the latest injection molding machines and a team of experienced engineers, {} is able to deliver custom solutions to meet the unique needs of its clients.{} is committed to staying ahead of the curve in the ever-evolving manufacturing landscape. With a focus on innovation and customer satisfaction, the company has continually invested in advanced technologies to enhance its production capabilities. This forward-thinking approach has not only enabled {} to maintain its competitive edge but has also positioned the company as a leader in the injection molding industry.One of the key advantages of injection molding is its ability to produce parts with exceptional precision and accuracy. The process allows for the creation of intricate designs and complex geometries that would be challenging to achieve using traditional manufacturing methods. With the use of computer-aided design (CAD) software and advanced mold-making techniques, {} is able to manufacture high-quality parts with tight tolerances, ensuring superior performance and functionality.Another advantage of injection molding is its cost-effectiveness. The ability to produce large volumes of parts with minimal waste makes this manufacturing process highly efficient. {} has leveraged this advantage to offer competitive pricing to its customers, making it an attractive choice for businesses looking to streamline their production processes and reduce overall costs.Furthermore, injection molding is a versatile process that can accommodate a wide range of materials, including thermoplastics, thermosets, and elastomers. This flexibility allows {} to cater to diverse industry needs, from automotive and aerospace to medical and consumer products. By working closely with its customers, the company is able to recommend the most suitable materials for their specific applications, ensuring optimal performance and durability.In addition to its technical capabilities, {} is dedicated to sustainability and environmental responsibility. The company strives to minimize its environmental impact by implementing eco-friendly practices in its manufacturing processes. By using recyclable materials and optimizing energy consumption, {} is committed to promoting a greener and more sustainable future for the manufacturing industry.With its dedication to quality, innovation, and customer satisfaction, {} is poised to continue making significant contributions to the advancement of injection molding technology. As the manufacturing landscape continues to evolve, this company remains committed to staying ahead of the curve and delivering cutting-edge solutions to its clients.In conclusion, injection molding is a game-changer in the manufacturing industry, and {} is leading the charge in harnessing its potential. With its state-of-the-art facilities, technical expertise, and commitment to excellence, {} is well-positioned to continue driving revolutionary changes in the production of high-quality, precision-engineered parts. As the demand for complex and customized products continues to grow, injection molding is likely to play an even more prominent role in shaping the future of manufacturing.
Understanding the Benefits of Computerized Numerical Control Technology
Computerized Numerical Control (CNC) technology has revolutionized manufacturing processes across industries, and one company that has been at the forefront of this innovation is {}.{} is a leading provider of CNC solutions for various industrial applications. The company's commitment to delivering high-quality, reliable, and efficient CNC systems has made it a trusted partner for manufacturers around the world.With a wide range of CNC products and services, {} has remained a key player in the global manufacturing landscape. Whether it's CNC machining centers, turning machines, or milling machines, {} has consistently been at the cutting edge of technological advancements, helping businesses enhance their productivity and profitability.One of the key features of {}'s CNC systems is their advanced control capabilities. These systems leverage the power of computerized numerical control to precisely control the movement of cutting tools and other machinery components. This level of precision allows manufacturers to produce complex and intricate parts with ease, resulting in higher quality end products.In addition to precision control, {}'s CNC systems are known for their versatility and flexibility. These systems can be easily programmed to accommodate a wide range of manufacturing tasks, making them suitable for various industries, including aerospace, automotive, medical, and electronics.The integration of computerized numerical control has also contributed to significant improvements in efficiency and productivity. By automating the manufacturing process, {}'s CNC systems reduce the need for manual intervention, leading to faster production cycles and reduced lead times. This has helped manufacturers streamline their operations and meet the ever-increasing demands of the market.Moreover, {} has always been committed to innovation, continually investing in research and development to further enhance its CNC solutions. The company's dedication to staying ahead of the curve has resulted in the introduction of state-of-the-art CNC technologies, such as advanced controller systems, multi-axis machining capabilities, and real-time monitoring and diagnostics.Furthermore, {}'s customer-centric approach sets it apart in the industry. The company works closely with its clients to understand their specific requirements and provide tailored CNC solutions that meet their unique needs. This personalized approach has earned {} a reputation for delivering exceptional customer satisfaction and building long-lasting partnerships with its clients.In line with its commitment to excellence, {} also offers comprehensive training and support services to ensure that its customers can maximize the potential of their CNC systems. From installation and setup to ongoing maintenance and troubleshooting, {}'s team of experts is dedicated to assisting clients every step of the way.As the manufacturing landscape continues to evolve, {} remains at the forefront, driving innovation and shaping the future of CNC technology. With a strong focus on precision, reliability, efficiency, and customer satisfaction, {} is poised to continue leading the way in the CNC industry for years to come.In conclusion, the integration of computerized numerical control has had a transformative impact on the manufacturing industry, and {} has been a driving force behind this revolution. With its cutting-edge CNC solutions, commitment to innovation, and customer-centric approach, {} has cemented its position as a global leader in the CNC technology space. As the industry evolves, {} is well-equipped to continue delivering high-quality, reliable, and efficient CNC solutions that empower manufacturers to thrive in a competitive market.
Top Quality Plastic Machine Parts for Ultimate Performance
Plastic Machine Parts, a leading manufacturer of precision plastic components, has recently announced the launch of their new line of innovative machine parts designed to meet the growing demand for high-quality, durable, and efficient solutions in the plastic processing industry.With over 20 years of experience in the industry, Plastic Machine Parts has established itself as a trusted partner for companies looking to improve their production processes. The company takes pride in its ability to deliver custom solutions to meet the unique needs of its clients, offering a wide range of products including injection molding machine parts, extrusion machine parts, blow molding machine parts, and more.Plastic Machine Parts is known for its commitment to quality, precision, and innovation. Their team of expert engineers and technicians are constantly working to develop new and improved solutions to help their clients achieve their production goals. The company's state-of-the-art manufacturing facility is equipped with the latest technology and machinery, allowing them to produce high-quality plastic machine parts that meet the highest industry standards.One of the key highlights of Plastic Machine Parts' new line of products is their focus on sustainability. As the demand for eco-friendly solutions continues to grow, the company has made significant investments in developing machine parts that are not only efficient and durable but also environmentally friendly. By using recyclable materials and implementing energy-saving production methods, Plastic Machine Parts is playing a crucial role in promoting sustainability within the industry.In addition to their commitment to sustainability, Plastic Machine Parts also prioritizes customer satisfaction. The company understands the importance of delivering reliable and efficient solutions to its clients, and as such, they offer comprehensive support services to ensure that their products meet the highest standards. From product customization to on-site technical support, Plastic Machine Parts is dedicated to providing a seamless experience for its customers."We are thrilled to introduce our new line of plastic machine parts to the market," said the company's CEO. "With the increasing demand for high-quality and sustainable solutions in the plastic processing industry, we believe that our innovative products will make a significant difference for our clients. We are committed to providing the best possible solutions to help our customers improve their production processes and achieve their business objectives."The launch of Plastic Machine Parts' new line of machine parts comes at a time when the industry is experiencing rapid growth and technological advancement. As companies continue to seek more efficient and sustainable solutions for their production processes, Plastic Machine Parts is well-positioned to meet this demand with its cutting-edge products and unwavering commitment to excellence.The company's dedication to innovation and sustainability has already garnered attention from industry leaders, with many expressing optimism about the impact of Plastic Machine Parts' new products on the industry. With its track record of success and its ongoing commitment to excellence, Plastic Machine Parts is poised to play a pivotal role in shaping the future of the plastic processing industry.As the demand for high-quality plastic machine parts continues to grow, Plastic Machine Parts is well-positioned to meet this demand with its innovative products and unwavering commitment to excellence. With a focus on sustainability, customer satisfaction, and technological advancement, the company is poised to play a pivotal role in shaping the future of the plastic processing industry.
Advanced CNC Processing Techniques Unveiled in Latest News Update
CNC Processing has become an integral part of modern manufacturing, revolutionizing the way companies produce a wide range of products. From aerospace components to medical devices, CNC Processing has enabled companies to achieve high precision and efficiency in their manufacturing processes. One company at the forefront of this technological advancement is {}.{} specializes in providing cutting-edge CNC Processing solutions to a diverse range of industries. With a strong focus on innovation and customer satisfaction, the company has established itself as a reliable partner for businesses seeking to optimize their manufacturing processes.The core of {}'s business lies in its state-of-the-art CNC machining capabilities. The company utilizes the latest CNC milling and turning machines to produce high-precision components with tight tolerances. With a team of experienced machinists and engineers, {} is capable of handling complex projects that require advanced machining techniques.In addition to traditional CNC machining, {} also offers advanced services such as multi-axis machining and Swiss machining. These capabilities allow the company to tackle even the most challenging manufacturing tasks, meeting the diverse needs of its clients.One of the key differentiators of {} is its commitment to quality. The company follows strict quality control processes to ensure that every product that leaves its facility meets the highest standards. From raw material inspection to final product verification, {} maintains rigorous quality checks at every stage of the manufacturing process.Furthermore, {} places a strong emphasis on continuous improvement. The company constantly invests in new technologies and training programs to stay ahead of the competition. This dedication to innovation has allowed {} to adapt to the evolving needs of its customers and offer cutting-edge solutions that drive business success.Despite the challenges posed by the global pandemic, {} has remained resilient and continued to serve its clients with unwavering dedication. The company has implemented stringent health and safety protocols to protect its employees and ensure uninterrupted operations. As a result, {} has successfully navigated through these difficult times and emerged as a reliable partner for businesses looking to outsource their CNC processing needs.Looking ahead, {} is poised for growth and expansion. The company is actively exploring opportunities to expand its presence in new markets and industries. With a solid foundation built on excellence and customer satisfaction, {} is well-positioned to capitalize on the increasing demand for high-quality CNC processing services.In conclusion, CNC Processing has become an indispensable part of modern manufacturing, and {} is playing a crucial role in driving this technological revolution. With its advanced capabilities, unwavering commitment to quality, and dedication to innovation, {} stands out as a trusted partner for businesses seeking to optimize their manufacturing processes. As the company continues to grow and expand, it is poised to make a lasting impact on the industry and redefine the standards of CNC processing.
High-Quality Aerospace CNC Machining Services for Precision Parts
Aerospace CNC Machining Company (ACM) has recently announced its expansion plans with the introduction of new state-of-the-art machining processes and capabilities. The company, known for its high-quality precision components for the aerospace industry, has been a leading supplier for several major aerospace firms.With a growing demand for more complex and advanced aerospace components, ACM has recognized the need to invest in cutting-edge CNC machining technology to meet the evolving needs of the industry. The company has therefore made significant investments in new machinery and equipment, along with the implementation of advanced machining processes to enhance its capabilities.The expansion of ACM's CNC machining capabilities is a strategic move to position the company as a leading provider of precision aerospace components. The new machinery and processes will allow ACM to produce components with tighter tolerances and more intricate geometries, meeting the high standards and requirements of the aerospace industry.One of the key advantages of the new CNC machining capabilities is the ability to produce complex and high-precision components with faster turnaround times. This will enable ACM to better meet the increasing demands of its customers and to stay ahead of the competition in the aerospace industry.In addition to the new machinery and advanced machining processes, ACM has also invested in training and development programs for its team of engineers and technicians. This will ensure that the company's workforce is equipped with the necessary skills and expertise to operate the new CNC machinery and to consistently deliver high-quality components to its customers.The expansion of ACM's CNC machining capabilities is a testament to the company's commitment to staying at the forefront of technological advancements in the aerospace industry. By embracing the latest machining technology and processes, ACM is well-positioned to continue providing its customers with innovative and high-quality aerospace components.The president of ACM, John Smith, expressed his excitement about the company's expansion plans and the potential for growth in the aerospace industry. "We are continuously looking for ways to improve our capabilities and better serve our customers," said Smith. "The investment in new CNC machining technology is a testament to our dedication to providing the highest quality components to the aerospace industry."The expansion of ACM's CNC machining capabilities has already garnered positive attention from its existing customer base, as well as from potential new clients in the aerospace sector. With the new machinery and advanced processes in place, the company is well-positioned to take on larger and more complex projects, further solidifying its reputation as a leading provider of precision aerospace components.In conclusion, the expansion of ACM's CNC machining capabilities marks an exciting milestone for the company and the aerospace industry as a whole. With the new machinery and advanced processes in place, ACM is poised to meet the increasing demands and evolving needs of the aerospace industry, while continuing to deliver high-quality precision components to its customers.
Highly Efficient Metal CNC Milling Machine for Precision Manufacturing
The importance of precision and efficiency in the manufacturing industry cannot be overstated. With the increasing demand for high-quality metal components, companies are constantly seeking ways to improve their production processes. One such company that has made significant strides in this area is {Company Name}.{Company Name} has recently invested in a state-of-the-art CNC milling machine to further improve its metal fabrication capabilities. The new machine is a game-changer for the company, as it allows for more precise and efficient metal cutting and shaping.CNC, or computer numerical control, milling machines are a staple in the manufacturing industry. They are capable of performing a wide range of tasks, from simple drilling to complex machining operations. With the latest advancements in technology, CNC milling machines have become even more versatile and precise, making them the go-to choice for companies looking to enhance their metal fabrication capabilities.{Company Name} has always been committed to staying ahead of the curve when it comes to technology and innovation. The investment in the new CNC milling machine is a testament to this commitment. By leveraging the latest advancements in CNC technology, {Company Name} is able to offer its clients even higher quality and more intricate metal components.The new CNC milling machine boasts several key features that set it apart from traditional milling machines. One of the most notable features is its ability to automatically change tools, reducing the need for manual intervention and increasing overall efficiency. Additionally, the machine is equipped with advanced software that allows for real-time monitoring and adjustments, ensuring that the final product meets the highest quality standards.In addition to the technological advancements, the CNC milling machine also offers a higher level of precision. This is particularly important for {Company Name}, as many of its clients require metal components with extremely tight tolerances. The new machine is capable of producing parts with exceptional accuracy, meeting even the most stringent specifications.The investment in the new CNC milling machine has already yielded positive results for {Company Name}. With the increased efficiency and precision, the company has been able to take on more complex projects and deliver them within shorter timeframes. This has not only strengthened its relationships with existing clients but has also attracted new business opportunities.Furthermore, the new machine has opened up possibilities for {Company Name} to explore new markets and industries. With its enhanced capabilities, the company is now able to cater to a wider range of clients, from aerospace and automotive to medical and telecommunications.The CNC milling machine has also had a positive impact on {Company Name}'s internal operations. The increased efficiency and precision have streamlined the production process, allowing the company to optimize its workflow and reduce lead times. This has translated into cost savings and improved overall productivity.Looking ahead, {Company Name} is committed to further leveraging the capabilities of the new CNC milling machine. The company has plans to explore additional applications and industries where the machine can make a significant impact. Additionally, {Company Name} is actively investing in training and development for its employees to ensure they are equipped with the necessary skills to maximize the potential of the new machine.In conclusion, the investment in the new CNC milling machine has solidified {Company Name}'s position as a leader in the metal fabrication industry. With its enhanced capabilities, the company is well-positioned to meet the evolving needs of its clients and capitalize on new business opportunities. As technology continues to advance, {Company Name} remains committed to staying at the forefront of innovation, delivering high-quality metal components with the utmost precision and efficiency.
How to Achieve Successful Overmolding of Plastic onto Metal
Title: A Revolutionary Advancement in Manufacturing: Overmolding Plastic On MetalIntroduction:In a groundbreaking development in the manufacturing industry, a leading company has recently unveiled its latest innovation in overmolding technology, allowing the seamless integration of plastic onto metal components. This cutting-edge process promises to revolutionize various industries, offering unparalleled opportunities for enhanced product durability, design flexibility, and cost-effectiveness. By merging the benefits of metal strength with the versatility of plastic, this groundbreaking technique opens up endless possibilities for manufacturers across the globe. Background:Recognizing the growing demand for more durable and aesthetically appealing products, manufacturers have long been seeking innovative ways to combine the strengths of different materials. These endeavors have led to the evolution of overmolding, a process that involves molding one material, usually plastic, over an existing component made of another material, commonly metal. Overmolding has been widely utilized in various industries, including automotive, electronics, and consumer goods, to improve product performance, ergonomics, and aesthetics.Product Introduction:Leading the charge in this realm of technology-advanced manufacturing is an industry trailblazer known for its commitment to innovation and relentless pursuit of excellence. Through tireless research and development, this company has perfected the art of overmolding plastic on metal, achieving unparalleled precision and quality in their products. The company's breakthrough overmolding process involves the injection of molten plastic onto metal components, resulting in a durable, seamless bond that surpasses traditional plastic or metal components in terms of both strength and aesthetic appeal.Advantages of Overmolding Plastic On Metal:1. Enhanced Durability: Overmolding plastic on metal creates a robust bond that significantly improves the structural integrity of the product. By minimizing the risk of component failure due to impacts, temperature variations, or chemical exposure, manufacturers can ensure longer product lifespans and ultimately enhance customer satisfaction.2. Improved Design Flexibility: Overmolding offers unparalleled design freedom, enabling manufacturers to create complex shapes and innovative designs that were previously not achievable with traditional manufacturing techniques. The ability to combine various materials with different properties allows for the creation of aesthetically pleasing and ergonomically superior products.3. Cost-effectiveness: Overmolding eliminates the need for additional assembly processes, reducing overall production costs. By combining multiple components into a single overmolded part, manufacturers can streamline their manufacturing processes, minimize assembly time, and decrease labor expenses.4. Reduced Noise and Vibration: Overmolding plastic dampens noise and absorbs vibrations, making it an ideal choice for applications requiring noise reduction, such as automotive interiors and consumer goods. This not only enhances user comfort but also improves the overall quality and perceived value of the product.Applications in Various Industries:The introduction of overmolding plastic on metal opens up new possibilities across a wide range of industries:1. Automotive: Overmolded components find extensive use in automotive interiors, offering improved aesthetics, comfort, and functional integration. From steering wheels to gear knobs, the overmolding process allows manufacturers to create visually appealing, ergonomic, and durable components.2. Electronics: Overmolded connectors, switches, and protective casings in the electronics industry provide enhanced resistance to moisture, dust, and impact. This not only improves the product's performance and durability but also enhances user safety.3. Consumer Goods: Overmolding plastic on metal can significantly enhance the quality and functionality of consumer goods. From kitchen appliances to power tools, the incorporation of overmolded components improves ergonomics, reduces noise, and extends product lifespan.Conclusion:The advent of overmolding plastic on metal marks a significant leap forward in manufacturing technology, offering unprecedented opportunities for industries seeking to enhance the durability, design flexibility, and cost-effectiveness of their products. The seamless integration of plastic onto metal components enables manufacturers to create innovative, aesthetically pleasing, and high-performance products that surpass the limits of traditional manufacturing techniques. As this groundbreaking technology continues to evolve, it is poised to revolutionize numerous industries and drive the development of the manufacturing sector to new heights.
How Insert Molding is Revolutionizing Manufacturing Processes
Title: Innovative Insert Molding Technology Revolutionizes Manufacturing ProcessesIntroduction:The manufacturing industry continually seeks advanced technologies to increase efficiency, minimize costs, and enhance product performance. One such revolutionary technique is Insert Molding, which combines the benefits of traditional molding techniques with precision insert placement, resulting in enhanced product performance and streamlined manufacturing processes. One company at the forefront of this innovation is {}. With their extensive experience and expertise in insert molding, they are pushing the boundaries of what is possible in the manufacturing industry.Paragraph 1:Insert Molding is a manufacturing process that involves injecting molten materials, such as plastic or metal, into a pre-formed cavity or mold containing one or more carefully positioned inserts. These inserts can be a wide range of components, including threaded inserts, electrical connectors, sensors, or metal reinforcements. The molten material effectively encapsulates the inserts, creating a strong bond between the two, resulting in a more robust and functional end product.Paragraph 2:Insert Molding offers several advantages over traditional manufacturing methods. Firstly, it eliminates the need for additional assembly processes, reducing labor costs and assembly time. By incorporating various inserts directly into the mold, the manufacturing process becomes more streamlined, efficient, and cost-effective. Furthermore, insert molding ensures precise and accurate positioning of the inserts, leading to higher product integrity and reliability.Paragraph 3:The innovation and expertise of {} in the field of insert molding have allowed them to cater to a diverse range of industries, including automotive, electronics, medical, and consumer goods. Their state-of-the-art facilities and skilled engineers enable them to create complex and high-quality molded products with exceptional precision. {} also offers comprehensive design assistance, ensuring that their customers' unique insert molding requirements are met, resulting in tailored solutions that exceed expectations.Paragraph 4:The automotive industry, in particular, has greatly benefited from the utilization of insert molding. By integrating metal inserts into plastic parts, manufacturers achieve significant weight reduction, increased part functionality, and improved overall vehicle performance. Electrical connectors, sensors, and wiring harnesses are seamlessly integrated, simplifying assembly and enhancing reliability. The implementation of insert molding enables automotive manufacturers to produce parts that meet the stringent safety and quality standards of the industry.Paragraph 5:In the ever-evolving electronics industry, where miniaturization and increased functionality are essential, insert molding plays a crucial role. With the ability to place delicate components, such as microchips, sensors, and connectors, with utmost precision, manufacturers can produce smaller and slimmer electronic devices without sacrificing performance. This technique also enhances the devices' durability by protecting fragile components and reducing the risk of damage caused by external factors.Paragraph 6:In the medical industry, insert molding offers numerous benefits in terms of product design, functionality, and sterilization. The ability to encapsulate electronics, sensors, and metal components within a single molded part ensures a seamless integration of various functionalities, such as drug delivery systems, diagnostic equipment, and surgical devices. The use of insert molding in the medical field has resulted in advancements in patient care and treatment efficiency.Conclusion:With its ability to combine diverse materials and precisely position inserts, Insert Molding has revolutionized the manufacturing industry by enhancing product performance, reducing costs, and streamlining production processes. The expertise and cutting-edge solutions provided by {} have solidified their place as industry leaders in insert molding technology. As new advancements continue to be made, the possibilities and applications of Insert Molding are boundless, driving innovation throughout various sectors and shaping the future of manufacturing.
CNC Turning Machining Services: Advanced Precision Techniques for Your Needs
Title: Revolutionizing Precision Manufacturing: Cutting-Edge CNC Turning Machining UnveiledIntroduction:In the ever-evolving landscape of modern manufacturing, precision and efficiency are paramount. Companies around the world are constantly searching for innovative solutions to meet the growing demands of customers while maintaining high-quality standards. One such groundbreaking technology that has been making waves in the manufacturing industry is CNC turning machining. This advanced process, when combined with the expertise and commitment of leading companies, is revolutionizing precision manufacturing like never before, ensuring both accuracy and speed in the production process.[Company Name] Leads the Way in CNC Turning Machining Excellence:As a pioneer in precision engineering, [Company Name] has emerged as a global leader in the implementation of CNC turning machining. With its unwavering commitment to cutting-edge technology and expertise in advanced manufacturing techniques, [Company Name] has consistently pushed boundaries and set new industry standards.State-of-the-Art CNC Turning Machining:CNC turning machining, standing for computer numerical control turning, refers to a manufacturing process involving the use of computer-controlled machines to produce custom-designed parts and components. This process utilizes lathes to shape and mold raw materials into intricate and precise forms. It offers unparalleled precision and repeatability, making it the go-to choice for companies operating in diverse sectors such as aerospace, automotive, medical, and more.Benefits of CNC Turning Machining:1. Enhanced Precision: CNC turning machining ensures exceptional accuracy in creating parts with minimal human intervention. The computerized controls enable precise measurements and tight tolerances, reducing the risk of errors typically associated with manual machining.2. Improved Efficiency: By eliminating the need for manual adjustments, CNC turning machining significantly increases productivity. The automated process allows for seamless production runs, reducing downtime and maximizing output.3. Versatility: CNC turning machining can be applied to a wide range of materials, giving manufacturers flexibility in accommodating various project requirements. Whether it is plastic, metal, or composite materials, this technology can shape and craft parts with intricate details and complex geometries.4. Cost Effectiveness: Although initially requiring a significant investment, CNC turning machining ultimately leads to cost savings in the long run. The precise, efficient, and automated nature of the process reduces material waste and labor costs, delivering enhanced profitability for companies.Applications of CNC Turning Machining:The versatility of CNC turning machining allows it to be applied to numerous industries:1. Aerospace: This technology proves vital in the manufacture of aircraft components, enabling the production of lightweight and durable parts that meet stringent industry standards.2. Automotive: CNC turning machining is central to automotive manufacturing, facilitating the creation of precise engine components, transmission parts, and more, ensuring durability and optimum performance.3. Medical: In the medical field, precision is of utmost importance. CNC turning machining provides the accuracy required to produce medical device components, implants, and surgical instruments that meet rigorous quality standards.4. Electronics: When it comes to manufacturing intricate electronic components, such as connectors, housings, and enclosures, CNC turning machining plays a pivotal role, ensuring consistent quality and meeting tight tolerances.[Company Name]: Driving Innovation:Renowned for its commitment to pushing the boundaries of conventional manufacturing techniques, [Company Name] has successfully integrated CNC turning machining into its operations. By investing in state-of-the-art machinery and employing highly skilled engineers, the company has achieved unmatched precision and meticulous craftsmanship."Our cutting-edge CNC turning machining capabilities allow us to bring our customers' visions to reality, ensuring the highest levels of quality and performance," said [Spokesperson Name], spokesperson for [Company Name]. "We are constantly evolving and embracing technological advancements to stay at the forefront of the industry."Conclusion:With CNC turning machining leading the way in precision manufacturing, companies like [Company Name] are at the forefront, driving innovation and raising industry standards. The unmatched precision, versatility, and cost-effectiveness of CNC turning machining enable manufacturers to deliver exceptional products across various sectors. As technology continues to advance, the possibilities for CNC turning machining are endless, transforming the manufacturing landscape and ensuring a brighter future for precision engineering.
Professional Tips for Constructing a High-Quality CNC Machine
The construction of a new CNC machine has been completed by a leading company in the manufacturing industry. This state-of-the-art machine is set to revolutionize the production process and provide a competitive edge in the market.The CNC machine, which stands for Computer Numerical Control, is a cutting-edge piece of equipment that is used to automate the manufacturing process. It is capable of cutting and shaping materials with a high level of precision, making it an essential tool for industries such as automotive, aerospace, and electronics.The construction of this new CNC machine is a result of extensive research and development by the company. With a team of experienced engineers and technicians, they have been able to design and build a machine that meets the highest standards of quality and performance.The company, which has been in the industry for over 20 years, has a strong track record of delivering innovative solutions to their clients. Their commitment to excellence and continuous improvement has led them to invest in cutting-edge technology such as the new CNC machine.Incorporating the latest advancements in software and hardware, the CNC machine boasts a range of features that set it apart from traditional machining tools. Its ability to operate with a high degree of accuracy and efficiency makes it a valuable asset for any manufacturing operation.One of the key highlights of the new CNC machine is its versatility. It is capable of handling a wide range of materials, including metals, plastics, and composites. This flexibility allows for a diverse range of applications, from intricate components to large-scale production runs.Furthermore, the CNC machine is equipped with advanced automation features, which streamline the production process and reduce the need for manual intervention. This not only improves efficiency but also ensures consistent quality across all output.In addition to its technical capabilities, the company has also focused on the ergonomic design of the CNC machine. This consideration ensures that operators can work comfortably and safely, thereby enhancing productivity and reducing the risk of workplace injuries.The construction of the new CNC machine represents a significant investment for the company, both in terms of resources and expertise. However, they are confident that the benefits it will bring to their clients and the industry as a whole will far outweigh the initial costs.As the manufacturing landscape continues to evolve, the demand for advanced machining solutions is only set to increase. By staying ahead of the curve and investing in cutting-edge technology, the company has positioned themselves as a leader in the industry, capable of meeting the needs of their clients both now and in the future.In conclusion, the completion of the new CNC machine construction marks a significant milestone for the company and the manufacturing industry as a whole. With its advanced capabilities and commitment to innovation, the company is set to make a lasting impact on the market and solidify its position as a trusted partner for manufacturers around the world.