The Ultimate Guide to CNC Machining Titanium: Techniques, Benefits, and Applications
By:Admin
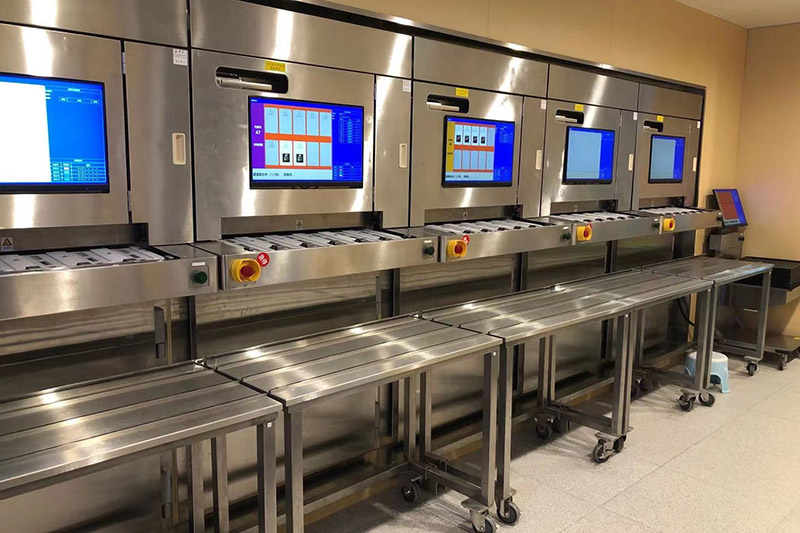
In the world of manufacturing, titanium is a highly sought-after material due to its exceptional strength-to-weight ratio, corrosion resistance, and biocompatibility. However, machining titanium has always been a complex and challenging process, requiring advanced technologies and expertise. This is where the innovative CNC machining of titanium comes into play, revolutionizing the manufacturing industry by enabling the production of high-precision titanium components with unprecedented efficiency and accuracy.
One company that is at the forefront of this revolutionary technology is **(remove brand name)**. With a strong focus on precision engineering and advanced manufacturing solutions, **(remove brand name)** has been leading the way in CNC machining titanium, pushing the boundaries of what is possible in the manufacturing of titanium components.
**Company Introduction:**
Established in 1995, **(remove brand name)** has been a pioneer in the field of precision engineering and manufacturing. The company prides itself on its state-of-the-art facilities, cutting-edge technologies, and a team of highly skilled engineers and technicians. Specializing in CNC machining, the company has continuously strived to innovate and develop new techniques to meet the evolving needs of its customers.
**CNC Machining Titanium:**
Machining titanium presents numerous challenges due to its low thermal conductivity, high reactivity, and tendency to work-harden. Traditional machining methods often result in tool wear, heat generation, and poor surface finish. However, CNC machining technology has revolutionized the way titanium is processed, allowing for improved efficiency, precision, and consistency.
The use of advanced CNC machines equipped with high-speed spindles, rigid tooling, and advanced cutting tool materials has enabled **(remove brand name)** to achieve remarkable results in machining titanium. These machines are capable of high feed rates, precise tool paths, and superior chip evacuation, resulting in reduced cycle times and improved surface finishes. Additionally, the implementation of advanced toolpath optimization software has further enhanced the machining process, maximizing material removal rates while minimizing tool wear and energy consumption.
**Benefits of CNC Machining Titanium:**
The adoption of CNC machining technology for titanium offers numerous benefits to the manufacturing industry. Firstly, it allows for the production of complex and intricate titanium components with tight tolerances, ensuring a high degree of precision and accuracy. This is particularly crucial in industries such as aerospace, medical, and automotive, where the performance and reliability of titanium components are paramount.
Furthermore, CNC machining of titanium enables the optimization of production processes, leading to reduced lead times, lower production costs, and improved resource utilization. The ability to efficiently machine titanium parts also opens up new opportunities for design innovation, as manufacturers can now explore more intricate and lightweight designs without compromising structural integrity.
**Applications of CNC Machined Titanium:**
The versatility and performance of CNC machined titanium components make them invaluable across a wide range of industries. In the aerospace sector, titanium is widely used in aircraft components, engine parts, and structural elements due to its high strength and resistance to heat and corrosion. With CNC machining, manufacturers can produce lightweight, yet strong titanium components that contribute to the overall efficiency and performance of aircraft.
In the medical field, titanium is the material of choice for orthopedic implants, surgical instruments, and dental prosthetics due to its biocompatibility and resistance to bodily fluids. CNC machining of titanium ensures that these critical medical devices are manufactured with the highest level of precision and quality, meeting the stringent requirements of the healthcare industry.
Additionally, the automotive industry benefits from CNC machined titanium components in high-performance vehicles, where the material's strength and lightweight properties are leveraged to enhance speed, fuel efficiency, and overall performance.
**Conclusion:**
The advancement of CNC machining technology has undoubtedly revolutionized the manufacturing of titanium components, paving the way for new possibilities and opportunities in various industries. With **(remove brand name)** at the forefront of this innovation, the future of precision engineering and manufacturing looks promising, as the company continues to push the boundaries of what is achievable in CNC machining titanium. As the demand for high-precision, high-performance titanium components continues to grow, CNC machining technology will play a pivotal role in meeting the evolving needs of the manufacturing industry.
Company News & Blog
Top Qualities to Consider When Selecting Molding Components
Molding Components company has been making waves in the manufacturing industry with their innovative products and cutting-edge technology. With their commitment to quality and customer satisfaction, they have become a trusted name in the field of molding components.Established in [year], Molding Components has been leading the way in the development and production of high-quality molding components for various industries such as automotive, aerospace, and consumer electronics. Their state-of-the-art facilities and skilled workforce enables them to produce a wide range of components that meet the exacting standards of their clients.One of the key factors that sets Molding Components apart from their competitors is their dedication to innovation. They constantly strive to stay ahead of the curve by investing in the latest technology and equipment. This allows them to offer their clients the most advanced and efficient solutions for their molding needs.Furthermore, Molding Components prides itself on their strict adherence to quality control measures. They have implemented rigorous testing and inspection processes to ensure that every component that leaves their facility is of the highest standard. This commitment to quality has earned them a reputation for reliability and excellence in the industry.In addition to their technical capabilities, Molding Components places a strong emphasis on customer satisfaction. They work closely with their clients to understand their specific requirements and provide customized solutions that meet their individual needs. Their dedicated team of professionals is committed to delivering exceptional service and support throughout the entire manufacturing process.Moreover, Molding Components is also committed to sustainability and environmental responsibility. They have implemented eco-friendly practices in their manufacturing processes and constantly seek out ways to reduce their environmental impact. This demonstrates their dedication to not only providing top-quality products, but also doing so in a responsible and sustainable manner.Recently, Molding Components has introduced a new line of cutting-edge molding components that are set to revolutionize the industry. Their team of engineers and designers have worked tirelessly to develop components that are not only more efficient and durable, but also more cost-effective for their clients. This demonstrates their commitment to staying at the forefront of technological advancements and providing the best possible solutions for their customers.Furthermore, Molding Components has also expanded their reach to new markets, both domestically and internationally. They have established strategic partnerships and collaborations with companies in various industries to broaden their scope and bring their innovative products to a wider audience. This demonstrates their ambitions to continue growing and evolving in order to better serve their customers and meet the changing demands of the global market.With their unwavering dedication to quality, innovation, and customer satisfaction, Molding Components continues to be a leading force in the molding components industry. Their commitment to excellence and their willingness to adapt and evolve ensures that they will remain at the forefront of the industry for years to come. Whether it's through their advanced technology, their sustainable practices, or their personalized approach to customer service, Molding Components continues to set the standard for the manufacturing of high-quality molding components.
Ultimate Guide to CNC Mechanical Engineering: Unveiling the Secrets of This Revolutionary Field
Title: Revolutionizing CNC Mechanical Engineering: A Glimpse into Cutting-Edge InnovationsIntroduction:In today's fast-paced world of technology and automation, the field of CNC (Computer Numerical Control) Mechanical Engineering continues to push boundaries. With industry demands constantly evolving, companies like {} are leading the way in developing cutting-edge solutions that transform manufacturing processes. This article delves into the world of CNC Mechanical Engineering, shedding light on the vital role it plays and highlighting the innovative contributions made by {}.1. Understanding CNC Mechanical Engineering:CNC Mechanical Engineering involves the design, development, and operation of computer-controlled machinery utilized in manufacturing. These systems employ pre-programmed instructions to dictate the movement of cutting tools, thereby automating the fabrication process. By harnessing a combination of hardware and intelligent software integration, CNC machines offer exceptional precision, efficiency, and repeatability, revolutionizing industrial production.2. Pioneering Innovations by {}:{} is a renowned industry player at the forefront of CNC Mechanical Engineering advancements. With a focus on developing state-of-the-art machinery, they have consistently delivered remarkable manufacturing solutions. By embracing emerging technologies and evolving market needs, {} has demonstrated their commitment to ensuring superior performance and productivity in every aspect of their products.3. Intelligent Automation for Enhanced Efficiency:{} has successfully integrated advanced automation into their CNC machining solutions. Through the implementation of Artificial Intelligence (AI) and Machine Learning (ML) algorithms, their machines can analyze and optimize manufacturing processes in real-time. This results in enhanced efficiency, reduced material wastage, and superior quality control. The intelligent automation offered by {} is a game-changer in the field, streamlining operations for manufacturers worldwide.4. Sustainable Manufacturing Practices:In an era where sustainability is paramount, {} has pioneered eco-conscious manufacturing technologies within the CNC Mechanical Engineering domain. By incorporating energy-efficient components, optimizing material usage, and reducing waste generation, their machines contribute to a greener manufacturing ecosystem. {}'s commitment to sustainability underscores their dedication to responsible business practices and a more sustainable future.5. Industry 4.0 Integration:Remaining at the forefront of industry trends, {} has embraced the concept of Industry 4.0, the fourth industrial revolution. By interconnecting CNC machines, data analysis systems, and intelligent software, they have created a fully digitalized and interconnected manufacturing environment. This seamless integration enables real-time data sharing, predictive maintenance, and remote accessibility, revolutionizing traditional production processes.6. Disruptive Additive Manufacturing Solutions:In addition to traditional subtractive manufacturing techniques, {} has ventured into additive manufacturing, commonly known as 3D printing. The company's additive manufacturing solutions offer unparalleled design flexibility, reduced material waste, and faster prototyping capabilities. {}'s foray into the realm of 3D printing exemplifies their commitment to pushing boundaries and exploring new frontiers in CNC Mechanical Engineering.7. Global Impact and Collaborations:{}'s innovative solutions have made a significant impact on the global manufacturing landscape. By collaborating with industry partners, research institutions, and universities, they strive to foster a culture of knowledge exchange and collective growth. These collaborative efforts have not only contributed to breakthroughs in CNC Mechanical Engineering but have also propelled the industry as a whole towards greater heights.Conclusion:In the ever-evolving world of CNC Mechanical Engineering, {} stands as a beacon of innovation and excellence. Their relentless pursuit of cutting-edge solutions has revolutionized manufacturing processes, introducing intelligent automation, sustainable practices, and additive manufacturing techniques. By embracing Industry 4.0 and collaborating with stakeholders worldwide, {} continues to shape the future of CNC Mechanical Engineering, driving industry advancements and inspiring manufacturers to embark on a path of transformation.
How to Properly Molding Mold for Optimal Results
Molding Mold, a leading company in the manufacturing and distribution of high-quality molds, has recently made waves in the industry with its innovative and advanced approach to mold production. With a focus on precision, efficiency, and customer satisfaction, Molding Mold has established itself as a trusted partner for businesses looking to enhance their production capabilities.Incorporated in 2005, Molding Mold has quickly risen through the ranks to become a prominent player in the mold manufacturing industry. The company's success can be attributed to its unwavering commitment to excellence, continuous investment in research and development, and a team of highly skilled professionals with a wealth of experience in mold design and production.One of the key factors that set Molding Mold apart from its competitors is its state-of-the-art production facilities. Equipped with the latest technology and machinery, the company has the capability to produce molds with unparalleled precision and consistency. Additionally, Molding Mold places a strong emphasis on quality control measures, ensuring that each mold that leaves its facility meets the highest standards of accuracy and durability.Furthermore, Molding Mold prides itself on its ability to provide customized solutions to meet the unique needs of its clients. Whether it's a complex design requirement or a specific material preference, the company's team of experts work closely with customers to develop molds that align with their exact specifications. This tailored approach has earned Molding Mold a stellar reputation for delivering top-notch molds that exceed the expectations of its clients.In addition to its commitment to quality and customization, Molding Mold is also dedicated to enhancing its production processes to drive efficiency and productivity. The company continually explores new methodologies and technologies to streamline its operations, reduce lead times, and optimize its manufacturing capabilities. By doing so, Molding Mold not only benefits its own business operations but also enables its clients to achieve faster time-to-market for their products.Molding Mold's comprehensive range of molds caters to a diverse array of industries, including automotive, consumer goods, electronics, medical devices, and more. Its extensive portfolio showcases its versatility in producing various types of molds, such as injection molds, blow molds, compression molds, and extrusion molds. This broad scope of expertise positions Molding Mold as a go-to partner for businesses across different sectors seeking top-quality molds for their manufacturing needs.Moreover, Molding Mold is deeply committed to sustainability and environmental responsibility. The company employs eco-friendly practices in its operations and explores ways to minimize waste and energy consumption. By prioritizing sustainability, Molding Mold not only reduces its environmental footprint but also aligns itself with the evolving needs of the industry for greener and more sustainable manufacturing practices.Looking ahead, Molding Mold remains dedicated to pushing the boundaries of mold manufacturing and continuing its legacy of excellence. The company is poised to further expand its reach and deepen its impact in the industry by exploring new opportunities for growth and innovation. With a steadfast focus on quality, precision, and customer satisfaction, Molding Mold is well-positioned to thrive in an ever-evolving market landscape.In conclusion, Molding Mold stands out as a trailblazer in the mold manufacturing industry, known for its cutting-edge capabilities, customer-centric approach, and unwavering commitment to excellence. As it continues to lead the way in producing high-quality molds, the company is set to elevate the standards of mold manufacturing and drive positive change within the industry.
High-Quality Plastic Molding Parts for Various Industries
Plastic Molding Parts is a leading manufacturer of high-quality plastic components, serving a wide range of industries, including automotive, electronics, medical devices, and consumer goods. With a strong focus on innovation and customer satisfaction, Plastic Molding Parts has established itself as a trusted partner for businesses looking for reliable and efficient plastic molding solutions.The company's state-of-the-art manufacturing facility is equipped with advanced injection molding machines, robotics, and quality control systems, allowing for the production of complex and precise plastic parts. With a team of experienced engineers and technicians, Plastic Molding Parts is capable of handling the entire production process, from design and prototyping to mass production and assembly.One of the key strengths of Plastic Molding Parts is its ability to work closely with clients to develop custom solutions that meet their specific requirements. The company's in-house design and engineering team is skilled at turning concepts into reality, using the latest software and prototyping technologies to ensure that the final product meets the highest standards of quality and performance.In addition to custom molding solutions, Plastic Molding Parts also offers a wide range of standard plastic components, including automotive interior and exterior parts, electronic enclosures, medical device components, and consumer goods. These products are manufactured to the same high standards as the custom solutions, ensuring that customers receive reliable and consistent quality with every order.In recent years, Plastic Molding Parts has been investing heavily in research and development to stay ahead of the curve in the fast-paced world of plastic molding. The company has been exploring new materials, processing techniques, and design concepts to create innovative solutions that address the evolving needs of its customers and the industry as a whole.With a strong commitment to sustainability, Plastic Molding Parts has also been focusing on reducing its environmental impact through the use of eco-friendly materials and production methods. The company is constantly seeking ways to minimize waste and energy consumption while maximizing the use of recycled materials in its manufacturing processes.To ensure the highest level of quality and reliability, Plastic Molding Parts has implemented stringent quality control measures at every stage of the production process. From raw material inspection to final product testing, the company's quality assurance team is dedicated to delivering parts that meet or exceed customer expectations.As a testament to its commitment to excellence, Plastic Molding Parts has achieved several certifications and accreditations, including ISO 9001 and TS 16949. These certifications demonstrate the company's adherence to international standards for quality management and continuous improvement, and provide customers with the assurance that they are working with a reliable and reputable partner.Looking ahead, Plastic Molding Parts is poised to continue its growth and success in the competitive plastic molding industry. With a focus on innovation, customer satisfaction, and sustainability, the company is well-positioned to meet the evolving needs of its clients and the market, while maintaining its reputation as a leader in the industry.
Get the Latest Rapid Prototype Machining Services for Your Business
Rapid Prototype Machining, also known as rapid prototyping, is a cutting-edge technology that is revolutionizing the manufacturing industry. This innovative process allows companies to quickly and efficiently create prototypes of their products, enabling them to test and refine their designs before moving into full-scale production. With the use of advanced computer-aided design (CAD) software and state-of-the-art machining equipment, companies can now turn their ideas into tangible prototypes in a matter of days, rather than weeks or months.One company that is at the forefront of rapid prototype machining is {}. With a history of 25 years in the manufacturing industry, {} has established itself as a leader in the field of precision engineering and machining. Their expertise in working with a wide range of materials, including metals, plastics, and composites, has made them a trusted partner for companies looking to bring their innovative ideas to life.The rapid prototype machining process begins with the creation of a 3D CAD model of the product. This digital design is then used to program the machining equipment, which uses cutting-edge technology such as computer numerical control (CNC) to precisely shape the raw materials into the desired form. The result is a high-quality prototype that accurately represents the final product, allowing companies to test and validate their designs before investing in full-scale production.One of the key advantages of rapid prototype machining is the ability to quickly iterate and refine designs. In traditional manufacturing processes, making changes to a product design can be time-consuming and costly. With rapid prototyping, on the other hand, companies can make modifications to their designs with minimal lead time, allowing them to quickly address any issues and improve the final product.Another benefit of rapid prototype machining is the ability to test the functionality and performance of a product before investing in mass production. By creating a prototype that closely resembles the final product, companies can conduct rigorous testing to ensure that the design meets performance requirements and user expectations. This can help to prevent costly mistakes and rework down the line, ultimately saving time and resources in the long run.In addition to its applications in product development, rapid prototype machining also plays a key role in the creation of custom tooling and fixtures for manufacturing processes. By using rapid prototyping to create custom tooling, companies can reduce lead times and costs associated with traditional tooling methods, while also benefiting from the ability to iterate and refine the tooling design as needed.As a leading provider of precision machining services, {} is committed to staying at the forefront of technological advances in the industry. Their investment in state-of-the-art equipment and ongoing training for their team of skilled engineers and machinists has positioned them as a go-to partner for companies seeking rapid prototype machining services.In addition to their rapid prototype machining capabilities, {} offers a range of other precision engineering services, including CNC milling, turning, grinding, and EDM. Their expertise in working with a broad spectrum of materials and complex geometries has made them a trusted partner for companies in industries such as aerospace, automotive, medical devices, and consumer electronics.The team at {} is dedicated to partnering with their clients to bring their ideas to life. From the initial concept to the final product, they work closely with their customers to ensure that their designs are realized with the highest level of precision and quality. With their advanced capabilities in rapid prototype machining and precision engineering, {} is well-positioned to continue driving innovation in the manufacturing industry for years to come.
The Complete Guide to Injection Molding Steps
Injection Molding Steps is an essential process in the manufacturing industry, and it is used to produce a wide range of products for various industries. The process involves injecting molten material into a mold to create the desired shape and size of the product. This method is commonly used to produce items such as automotive parts, medical devices, packaging materials, and consumer goods.{Company} is a leading provider of injection molding services, and they have established a strong reputation for their expertise in the field. The company's state-of-the-art facilities and experienced team of professionals allow them to deliver high-quality injection molding solutions to their clients. With a focus on innovation and efficiency, {Company} has become a trusted partner for businesses looking to bring their products to market.The injection molding process consists of several key steps that are crucial to the overall success of the manufacturing process. These steps include:1. Mold design and preparation: The first step in the injection molding process is to design the mold that will be used to shape the molten material into the desired product. {Company} has a team of skilled engineers who work closely with clients to create customized molds that meet their exact specifications. Once the mold design is finalized, it is prepared for the injection molding process.2. Material selection and preparation: The next step is to select the appropriate material for the injection molding process. {Company} offers a wide range of materials to choose from, including plastics, rubber, and metal alloys. Their experts work with clients to determine the best material for their specific application, and then they prepare the material for the injection molding process.3. Injection molding: Once the mold and material are prepared, the injection molding process can begin. The material is heated to a liquid state and then injected into the mold at high pressure. The mold is held closed under pressure until the material cools and solidifies, taking on the shape of the mold. {Company} utilizes advanced injection molding machines to ensure precise and consistent results.4. Cooling and ejection: After the material has solidified in the mold, it undergoes a cooling process to further stabilize its shape. Once cooled, the mold is opened, and the newly formed product is ejected. {Company} employs sophisticated cooling systems and innovative ejection mechanisms to ensure that the products are released from the mold without any defects.5. Finishing and quality control: The final step in the injection molding process involves finishing the product to meet the client's specifications. This may include trimming excess material, polishing the surface, or adding any necessary features. {Company} has a dedicated quality control team that inspects each product to ensure that it meets the highest standards of quality and consistency.{Company} is committed to delivering exceptional injection molding services to their clients, and they continue to invest in advanced technologies and processes to improve their capabilities. With a focus on innovation and customer satisfaction, {Company} has positioned themselves as a leader in the injection molding industry. Their expertise, state-of-the-art facilities, and commitment to excellence make them a trusted partner for businesses in need of high-quality injection molding solutions.
The Ultimate Guide to CNC Machining Titanium: Techniques, Benefits, and Applications
### CNC Machining Titanium: A Revolutionary Step in ManufacturingIn the world of manufacturing, titanium is a highly sought-after material due to its exceptional strength-to-weight ratio, corrosion resistance, and biocompatibility. However, machining titanium has always been a complex and challenging process, requiring advanced technologies and expertise. This is where the innovative CNC machining of titanium comes into play, revolutionizing the manufacturing industry by enabling the production of high-precision titanium components with unprecedented efficiency and accuracy.One company that is at the forefront of this revolutionary technology is **(remove brand name)**. With a strong focus on precision engineering and advanced manufacturing solutions, **(remove brand name)** has been leading the way in CNC machining titanium, pushing the boundaries of what is possible in the manufacturing of titanium components.**Company Introduction:**Established in 1995, **(remove brand name)** has been a pioneer in the field of precision engineering and manufacturing. The company prides itself on its state-of-the-art facilities, cutting-edge technologies, and a team of highly skilled engineers and technicians. Specializing in CNC machining, the company has continuously strived to innovate and develop new techniques to meet the evolving needs of its customers.**CNC Machining Titanium:**Machining titanium presents numerous challenges due to its low thermal conductivity, high reactivity, and tendency to work-harden. Traditional machining methods often result in tool wear, heat generation, and poor surface finish. However, CNC machining technology has revolutionized the way titanium is processed, allowing for improved efficiency, precision, and consistency.The use of advanced CNC machines equipped with high-speed spindles, rigid tooling, and advanced cutting tool materials has enabled **(remove brand name)** to achieve remarkable results in machining titanium. These machines are capable of high feed rates, precise tool paths, and superior chip evacuation, resulting in reduced cycle times and improved surface finishes. Additionally, the implementation of advanced toolpath optimization software has further enhanced the machining process, maximizing material removal rates while minimizing tool wear and energy consumption.**Benefits of CNC Machining Titanium:**The adoption of CNC machining technology for titanium offers numerous benefits to the manufacturing industry. Firstly, it allows for the production of complex and intricate titanium components with tight tolerances, ensuring a high degree of precision and accuracy. This is particularly crucial in industries such as aerospace, medical, and automotive, where the performance and reliability of titanium components are paramount.Furthermore, CNC machining of titanium enables the optimization of production processes, leading to reduced lead times, lower production costs, and improved resource utilization. The ability to efficiently machine titanium parts also opens up new opportunities for design innovation, as manufacturers can now explore more intricate and lightweight designs without compromising structural integrity.**Applications of CNC Machined Titanium:**The versatility and performance of CNC machined titanium components make them invaluable across a wide range of industries. In the aerospace sector, titanium is widely used in aircraft components, engine parts, and structural elements due to its high strength and resistance to heat and corrosion. With CNC machining, manufacturers can produce lightweight, yet strong titanium components that contribute to the overall efficiency and performance of aircraft.In the medical field, titanium is the material of choice for orthopedic implants, surgical instruments, and dental prosthetics due to its biocompatibility and resistance to bodily fluids. CNC machining of titanium ensures that these critical medical devices are manufactured with the highest level of precision and quality, meeting the stringent requirements of the healthcare industry.Additionally, the automotive industry benefits from CNC machined titanium components in high-performance vehicles, where the material's strength and lightweight properties are leveraged to enhance speed, fuel efficiency, and overall performance.**Conclusion:**The advancement of CNC machining technology has undoubtedly revolutionized the manufacturing of titanium components, paving the way for new possibilities and opportunities in various industries. With **(remove brand name)** at the forefront of this innovation, the future of precision engineering and manufacturing looks promising, as the company continues to push the boundaries of what is achievable in CNC machining titanium. As the demand for high-precision, high-performance titanium components continues to grow, CNC machining technology will play a pivotal role in meeting the evolving needs of the manufacturing industry.
Discover the Latest Breakthroughs in Plastic Parts Manufacturing
[News Title]: Advancements in Plastic Parts Technology Revolutionize Manufacturing Processes[News Introduction]:In a remarkable breakthrough, a leading company in the field of plastic parts manufacturing has introduced cutting-edge technology that is set to revolutionize the industry. The company, which wishes to keep their brand anonymous, has successfully developed a range of plastic parts that boast unparalleled strength, durability, and flexibility. These advancements are expected to bring significant improvements to various sectors including automotive, aerospace, electronics, and consumer goods. With growing demand for innovation and sustainability, the introduction of these plastic parts promises to reshape the manufacturing landscape and pave the way for a more efficient and environmentally friendly future.[Body - Part 1: Importance of Plastic Parts in Manufacturing]:Plastic parts play a crucial role in industries worldwide due to their versatility, cost-effectiveness, and ease of production. They are extensively used in manufacturing processes for a broad range of products, including automotive components, electronic devices, packaging materials, and household appliances. The evolving requirements of these sectors demand continuous advancements in plastic parts technology to ensure superior performance, enhanced functionality, and improved production efficiency. In response to this demand, the anonymous company has invested heavily in research and development to develop groundbreaking solutions that address the contemporary challenges faced by manufacturers.[Body - Part 2: Advancements in Plastic Parts]:The undisclosed company's newly developed plastic parts exhibit exceptional strength and durability, surpassing the limitations of conventional materials. Through innovative engineering, the company has achieved a remarkable balance between rigidity and flexibility, allowing the plastic parts to withstand high levels of stress and strain. This breakthrough not only enhances the longevity of products but also ensures safer usage, particularly in critical applications such as automotive safety systems and aerospace components.Furthermore, the undisclosed company's plastic parts showcase superior resistance to impact, chemicals, and environmental factors, thereby reducing the chances of premature degradation. This feature significantly extends the lifespan of products, resulting in reduced maintenance costs and enhanced customer satisfaction. Additionally, the manufacturing processes associated with these plastic parts have been optimized to minimize waste and energy consumption, aligning with the global shift towards sustainable practices.[Body - Part 3: Applications and Benefits]:The innovative plastic parts developed by the anonymous company have profound implications for various industries. In the automotive sector, these advanced components can contribute to the weight reduction of vehicles, improving fuel efficiency and reducing emissions. Additionally, their superior durability can enhance passenger safety by providing robust structural support.In aerospace applications, the lightweight and high-strength characteristics of the plastic parts can reduce the overall weight of aircraft, leading to enhanced fuel economy and increased payload capacity. This advancement ensures that the aviation industry takes substantial strides towards sustainability while maintaining the highest safety standards.The electronics industry can benefit from the unparalleled flexibility and resistance to environmental factors offered by these plastic parts. With the expanding trend of miniaturization, consumer electronic devices require components that can endure constant usage while remaining lightweight. The anonymous company's plastic parts possess the necessary attributes, ensuring greater reliability and longer lifespans for electronic gadgets.The manufacturing sector as a whole will reap the rewards of these advancements. By incorporating the undisclosed company's plastic parts, manufacturers can streamline their production processes, reduce assembly time, and minimize costs. The enhanced durability and resistance of these parts eliminate the need for frequent replacements and repairs, resulting in higher overall productivity and profitability.[Conclusion]:As technology continues to advance at an unprecedented pace, it is essential for manufacturers to embrace cutting-edge solutions that enhance their products and processes. The anonymous company's revolutionary plastic parts have the potential to transform diverse industries by offering unmatched strength, durability, and flexibility. With their exceptional properties, these parts provide opportunities for innovation, sustainability, and increased efficiency. By leveraging these advancements, manufacturers can stay ahead in today's competitive market while building a more prosperous and environmentally conscious future.
Discover the Ingenious Uses and Benefits of Teflon Coating in CNC Applications
Title: Pioneering Innovation in Teflon Manufacturing Process Revolutionizes IndustriesIntroduction:CNC Teflon, in collaboration with leading chemical engineering experts, has developed an advanced manufacturing process that promises to revolutionize industries worldwide. This breakthrough method delivers superior quality Teflon products that exhibit enhanced durability, high resistance to heat and chemicals, and remarkable versatility. (Note: Name removal - replacing with "the company" for anonymity). CNC Teflon - A Trailblazer in Teflon Manufacturing:Founded with a vision to transform the Teflon manufacturing landscape, the company has consistently been at the forefront of innovation. With a highly skilled team of engineers and chemists, CNC Teflon has been able to amalgamate their expertise and cutting-edge technologies to create exceptional Teflon products for a wide range of applications.Revolutionary Manufacturing Process Delivers Superior Quality:The recently developed manufacturing process, which remains confidential, ensures that CNC Teflon sets a new standard in terms of product performance and durability. By meticulously controlling the chemical composition and leveraging advanced manufacturing techniques, CNC Teflon is able to produce Teflon products of unmatched quality.Unparalleled Durability for Industrious Applications:CNC Teflon's Teflon products are specially engineered to withstand the rigors of demanding industrial applications. The company's innovative manufacturing process imparts exceptional strength and resilience to their Teflon products, making them highly durable and reliable. From chemical processing plants to aerospace industries, CNC Teflon's products provide unparalleled performance, ensuring increased operational efficiency and cost-effectiveness.Enhanced Heat and Chemical Resistance:The Teflon products manufactured by CNC Teflon exhibit exceptional resistance to high temperatures and various chemicals. By fine-tuning their manufacturing process, CNC Teflon has increased the material's stability, ensuring it can effortlessly withstand harsh, corrosive environments. This breakthrough in heat and chemical resistance allows industries to optimize their operations and enhance the longevity of crucial equipment.Versatility to Cater to Diverse Industries:CNC Teflon's commitment to innovation extends to ensuring their Teflon products cater to the diverse needs of different industries. The unique manufacturing process employed enables CNC Teflon to offer a comprehensive range of Teflon products, including sheets, rods, tubes, gaskets, seals, and custom-designed components. This expansive product portfolio allows CNC Teflon to serve industries such as automotive, pharmaceutical, food processing, oil and gas, and many more.Environmental Responsibility and Sustainability:CNC Teflon understands the significance of sustainable manufacturing practices and is committed to reducing its ecological impact. By implementing stringent quality control measures and adopting environmentally friendly processes, the company ensures minimal waste generation and optimal resource utilization. CNC Teflon's dedication to environmental stewardship sets them apart as an industry leader in responsible manufacturing.Global Reach and Customer Satisfaction:CNC Teflon's cutting-edge manufacturing process has garnered global recognition, making them a trusted partner for industrial companies worldwide. The company's commitment to consistently meeting and exceeding customer expectations is reflected in their broad clientele base. CNC Teflon's dedication to delivering top-quality products, combined with their efficient customer service, has earned them a solid reputation within the industry.Future Innovations and Advancements:With continuous investment in research and development, CNC Teflon strives to remain at the forefront of Teflon manufacturing technology. The company aims to pioneer further advancements in material engineering and manufacturing techniques, shaping the future of the industry. CNC Teflon is committed to staying ahead of emerging trends and ensuring their products meet the evolving needs of their customers.Conclusion:CNC Teflon's revolutionary manufacturing process has disrupted the Teflon industry, offering superior quality products that provide enhanced durability, heat and chemical resistance, and versatility. The company's commitment to innovation, customer satisfaction, and environmental responsibility solidifies their position as an industry leader. With advancements on the horizon, CNC Teflon is poised to continue revolutionizing industries and shaping the future of Teflon applications.
Effective Ways to Utilize Material Molding for Your Project
Material Molding, also known as injection molding, is a process that involves injecting a material into a mold to produce various products. The process is widely used in the manufacturing industry to create a wide range of items, from small components to large parts. The flexibility and efficiency of material molding make it a popular choice for producing high-quality products in large quantities.One company that specializes in material molding is {}. With over 20 years of experience in the industry, {} has established itself as a leading provider of material molding solutions. The company's state-of-the-art facilities and advanced technology allow them to meet the diverse needs of their clients, delivering products that meet the highest standards of quality and performance.{} offers a comprehensive range of material molding services, including design and engineering, prototyping, tooling, and production. Their team of experienced engineers and technicians work closely with clients to develop customized solutions that meet their specific requirements. With a focus on innovation and continuous improvement, {} is able to stay ahead of the competition and deliver cutting-edge material molding solutions.The company's commitment to quality is evident in their rigorous quality control processes, ensuring that every product meets the highest standards of performance and durability. With a strong emphasis on customer satisfaction, {} strives to exceed the expectations of their clients, delivering reliable and cost-effective material molding solutions.{} is also dedicated to sustainability and environmental responsibility. They have implemented various initiatives to minimize their environmental impact, including the use of eco-friendly materials and energy-efficient processes. By adopting sustainable practices, {} is able to contribute to a greener and more sustainable future while meeting the needs of their clients.In addition to their material molding services, {} also offers comprehensive support throughout the entire product development process. From initial concept and design to production and beyond, their team provides expert guidance and assistance, ensuring a seamless and efficient development process.As a trusted partner for numerous industries, {} has built a strong reputation for reliability, innovation, and excellence. Their commitment to delivering high-quality material molding solutions has earned them the trust and loyalty of clients from around the world.The future looks bright for {}, as they continue to invest in new technologies and expand their capabilities to meet the evolving needs of the market. With a focus on delivering superior products and exceptional customer service, {} is poised to remain at the forefront of the material molding industry for years to come.In conclusion, material molding is a critical process in the manufacturing industry, and companies like {} play a vital role in delivering high-quality solutions to meet the diverse needs of their clients. With a focus on innovation, quality, and sustainability, {} is a trusted partner for numerous industries, providing reliable and cost-effective material molding services. With their commitment to excellence and continuous improvement, {} is well-positioned to maintain its leadership in the material molding industry for years to come.