The Future of Injection Molding Industry: Trends and Forecasts
By:Admin
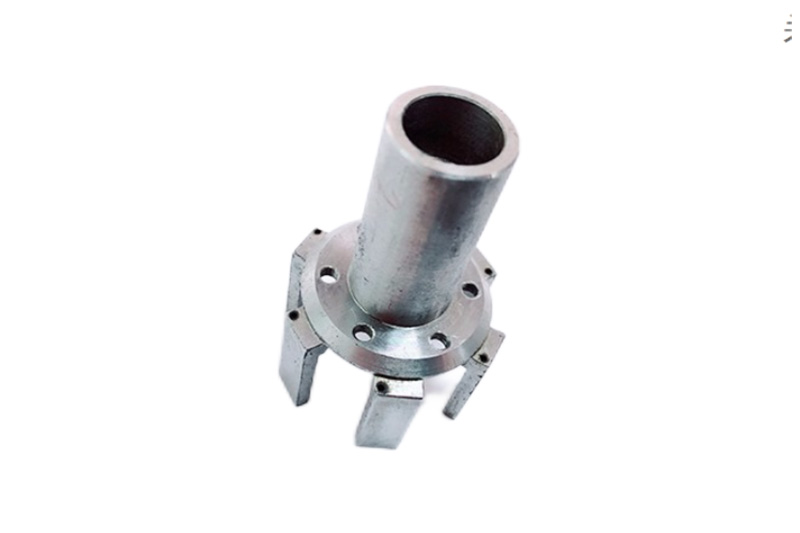
The injection molding industry has seen significant growth in recent years, with a steady increase in demand for molded plastic products across various industries. This growth can be attributed to the increasing use of plastic components in consumer goods, automotive, medical devices, and packaging. The injection molding process allows for high-volume production of complex plastic parts at a low cost, making it a preferred manufacturing method for many companies.
One company that has been at the forefront of this growth is {}. Established in 1990, {}, has emerged as a leading manufacturer in the injection molding industry. With state-of-the-art facilities and a highly skilled team, the company has been able to meet the growing demand for high-quality plastic components.
{} specializes in custom injection molding, offering a wide range of services including product design, mold making, and production. The company works closely with its clients to develop tailored solutions that meet their specific requirements. This customer-centric approach has enabled {} to build strong and long-lasting relationships with a diverse portfolio of clients, ranging from small businesses to global corporations.
One of the key factors contributing to {}'s success in the injection molding industry is its commitment to innovation. The company continuously invests in new technologies and processes to enhance its manufacturing capabilities and stay ahead of the competition. By keeping up with the latest advancements in the industry, {} is able to offer cutting-edge solutions that meet the evolving needs of its clients.
In addition to its focus on innovation, {} places a strong emphasis on quality and sustainability. The company is ISO 9001 certified and adheres to strict quality control measures throughout the manufacturing process. Furthermore, {} is committed to minimizing its environmental footprint by implementing eco-friendly practices and using recyclable materials wherever possible.
With a solid track record of delivering superior products and services, {} has positioned itself as a trusted partner in the injection molding industry. The company's unwavering dedication to excellence has earned it a reputation for reliability and integrity, making it a preferred choice for clients seeking top-notch injection molding solutions.
Looking ahead, the future of the injection molding industry appears to be promising, with continued growth expected in the coming years. As the demand for plastic components continues to rise, companies like {} are well-positioned to capitalize on this trend and further solidify their presence in the market. By staying true to their core values of innovation, quality, and sustainability, {} is poised to maintain its leadership in the injection molding industry and continue serving as a driving force behind its development.
Company News & Blog
How Insert Molding is Revolutionizing Manufacturing Processes
Title: Innovative Insert Molding Technology Revolutionizes Manufacturing ProcessesIntroduction:The manufacturing industry continually seeks advanced technologies to increase efficiency, minimize costs, and enhance product performance. One such revolutionary technique is Insert Molding, which combines the benefits of traditional molding techniques with precision insert placement, resulting in enhanced product performance and streamlined manufacturing processes. One company at the forefront of this innovation is {}. With their extensive experience and expertise in insert molding, they are pushing the boundaries of what is possible in the manufacturing industry.Paragraph 1:Insert Molding is a manufacturing process that involves injecting molten materials, such as plastic or metal, into a pre-formed cavity or mold containing one or more carefully positioned inserts. These inserts can be a wide range of components, including threaded inserts, electrical connectors, sensors, or metal reinforcements. The molten material effectively encapsulates the inserts, creating a strong bond between the two, resulting in a more robust and functional end product.Paragraph 2:Insert Molding offers several advantages over traditional manufacturing methods. Firstly, it eliminates the need for additional assembly processes, reducing labor costs and assembly time. By incorporating various inserts directly into the mold, the manufacturing process becomes more streamlined, efficient, and cost-effective. Furthermore, insert molding ensures precise and accurate positioning of the inserts, leading to higher product integrity and reliability.Paragraph 3:The innovation and expertise of {} in the field of insert molding have allowed them to cater to a diverse range of industries, including automotive, electronics, medical, and consumer goods. Their state-of-the-art facilities and skilled engineers enable them to create complex and high-quality molded products with exceptional precision. {} also offers comprehensive design assistance, ensuring that their customers' unique insert molding requirements are met, resulting in tailored solutions that exceed expectations.Paragraph 4:The automotive industry, in particular, has greatly benefited from the utilization of insert molding. By integrating metal inserts into plastic parts, manufacturers achieve significant weight reduction, increased part functionality, and improved overall vehicle performance. Electrical connectors, sensors, and wiring harnesses are seamlessly integrated, simplifying assembly and enhancing reliability. The implementation of insert molding enables automotive manufacturers to produce parts that meet the stringent safety and quality standards of the industry.Paragraph 5:In the ever-evolving electronics industry, where miniaturization and increased functionality are essential, insert molding plays a crucial role. With the ability to place delicate components, such as microchips, sensors, and connectors, with utmost precision, manufacturers can produce smaller and slimmer electronic devices without sacrificing performance. This technique also enhances the devices' durability by protecting fragile components and reducing the risk of damage caused by external factors.Paragraph 6:In the medical industry, insert molding offers numerous benefits in terms of product design, functionality, and sterilization. The ability to encapsulate electronics, sensors, and metal components within a single molded part ensures a seamless integration of various functionalities, such as drug delivery systems, diagnostic equipment, and surgical devices. The use of insert molding in the medical field has resulted in advancements in patient care and treatment efficiency.Conclusion:With its ability to combine diverse materials and precisely position inserts, Insert Molding has revolutionized the manufacturing industry by enhancing product performance, reducing costs, and streamlining production processes. The expertise and cutting-edge solutions provided by {} have solidified their place as industry leaders in insert molding technology. As new advancements continue to be made, the possibilities and applications of Insert Molding are boundless, driving innovation throughout various sectors and shaping the future of manufacturing.
Professional Tips for Constructing a High-Quality CNC Machine
The construction of a new CNC machine has been completed by a leading company in the manufacturing industry. This state-of-the-art machine is set to revolutionize the production process and provide a competitive edge in the market.The CNC machine, which stands for Computer Numerical Control, is a cutting-edge piece of equipment that is used to automate the manufacturing process. It is capable of cutting and shaping materials with a high level of precision, making it an essential tool for industries such as automotive, aerospace, and electronics.The construction of this new CNC machine is a result of extensive research and development by the company. With a team of experienced engineers and technicians, they have been able to design and build a machine that meets the highest standards of quality and performance.The company, which has been in the industry for over 20 years, has a strong track record of delivering innovative solutions to their clients. Their commitment to excellence and continuous improvement has led them to invest in cutting-edge technology such as the new CNC machine.Incorporating the latest advancements in software and hardware, the CNC machine boasts a range of features that set it apart from traditional machining tools. Its ability to operate with a high degree of accuracy and efficiency makes it a valuable asset for any manufacturing operation.One of the key highlights of the new CNC machine is its versatility. It is capable of handling a wide range of materials, including metals, plastics, and composites. This flexibility allows for a diverse range of applications, from intricate components to large-scale production runs.Furthermore, the CNC machine is equipped with advanced automation features, which streamline the production process and reduce the need for manual intervention. This not only improves efficiency but also ensures consistent quality across all output.In addition to its technical capabilities, the company has also focused on the ergonomic design of the CNC machine. This consideration ensures that operators can work comfortably and safely, thereby enhancing productivity and reducing the risk of workplace injuries.The construction of the new CNC machine represents a significant investment for the company, both in terms of resources and expertise. However, they are confident that the benefits it will bring to their clients and the industry as a whole will far outweigh the initial costs.As the manufacturing landscape continues to evolve, the demand for advanced machining solutions is only set to increase. By staying ahead of the curve and investing in cutting-edge technology, the company has positioned themselves as a leader in the industry, capable of meeting the needs of their clients both now and in the future.In conclusion, the completion of the new CNC machine construction marks a significant milestone for the company and the manufacturing industry as a whole. With its advanced capabilities and commitment to innovation, the company is set to make a lasting impact on the market and solidify its position as a trusted partner for manufacturers around the world.
How to Achieve Successful Overmolding of Plastic onto Metal
Title: A Revolutionary Advancement in Manufacturing: Overmolding Plastic On MetalIntroduction:In a groundbreaking development in the manufacturing industry, a leading company has recently unveiled its latest innovation in overmolding technology, allowing the seamless integration of plastic onto metal components. This cutting-edge process promises to revolutionize various industries, offering unparalleled opportunities for enhanced product durability, design flexibility, and cost-effectiveness. By merging the benefits of metal strength with the versatility of plastic, this groundbreaking technique opens up endless possibilities for manufacturers across the globe. Background:Recognizing the growing demand for more durable and aesthetically appealing products, manufacturers have long been seeking innovative ways to combine the strengths of different materials. These endeavors have led to the evolution of overmolding, a process that involves molding one material, usually plastic, over an existing component made of another material, commonly metal. Overmolding has been widely utilized in various industries, including automotive, electronics, and consumer goods, to improve product performance, ergonomics, and aesthetics.Product Introduction:Leading the charge in this realm of technology-advanced manufacturing is an industry trailblazer known for its commitment to innovation and relentless pursuit of excellence. Through tireless research and development, this company has perfected the art of overmolding plastic on metal, achieving unparalleled precision and quality in their products. The company's breakthrough overmolding process involves the injection of molten plastic onto metal components, resulting in a durable, seamless bond that surpasses traditional plastic or metal components in terms of both strength and aesthetic appeal.Advantages of Overmolding Plastic On Metal:1. Enhanced Durability: Overmolding plastic on metal creates a robust bond that significantly improves the structural integrity of the product. By minimizing the risk of component failure due to impacts, temperature variations, or chemical exposure, manufacturers can ensure longer product lifespans and ultimately enhance customer satisfaction.2. Improved Design Flexibility: Overmolding offers unparalleled design freedom, enabling manufacturers to create complex shapes and innovative designs that were previously not achievable with traditional manufacturing techniques. The ability to combine various materials with different properties allows for the creation of aesthetically pleasing and ergonomically superior products.3. Cost-effectiveness: Overmolding eliminates the need for additional assembly processes, reducing overall production costs. By combining multiple components into a single overmolded part, manufacturers can streamline their manufacturing processes, minimize assembly time, and decrease labor expenses.4. Reduced Noise and Vibration: Overmolding plastic dampens noise and absorbs vibrations, making it an ideal choice for applications requiring noise reduction, such as automotive interiors and consumer goods. This not only enhances user comfort but also improves the overall quality and perceived value of the product.Applications in Various Industries:The introduction of overmolding plastic on metal opens up new possibilities across a wide range of industries:1. Automotive: Overmolded components find extensive use in automotive interiors, offering improved aesthetics, comfort, and functional integration. From steering wheels to gear knobs, the overmolding process allows manufacturers to create visually appealing, ergonomic, and durable components.2. Electronics: Overmolded connectors, switches, and protective casings in the electronics industry provide enhanced resistance to moisture, dust, and impact. This not only improves the product's performance and durability but also enhances user safety.3. Consumer Goods: Overmolding plastic on metal can significantly enhance the quality and functionality of consumer goods. From kitchen appliances to power tools, the incorporation of overmolded components improves ergonomics, reduces noise, and extends product lifespan.Conclusion:The advent of overmolding plastic on metal marks a significant leap forward in manufacturing technology, offering unprecedented opportunities for industries seeking to enhance the durability, design flexibility, and cost-effectiveness of their products. The seamless integration of plastic onto metal components enables manufacturers to create innovative, aesthetically pleasing, and high-performance products that surpass the limits of traditional manufacturing techniques. As this groundbreaking technology continues to evolve, it is poised to revolutionize numerous industries and drive the development of the manufacturing sector to new heights.
DIY Plastic Injection Molding: How to Set Up Your Own Molding Station at Home
Home plastic injection molding has become a popular and cost-effective way for hobbyists and small businesses to produce their own plastic products. With the use of a desktop injection molding machine, individuals can create custom plastic parts in the comfort of their own home, without the need for expensive industrial machinery.One company that has made a name for itself in the home plastic injection molding industry is {}. They have designed and manufactured a compact and user-friendly injection molding machine that is perfect for beginners and experienced molders alike. This machine allows users to produce high-quality plastic parts using a variety of thermoplastic materials, including ABS, PE, and PVC.With the increasing demand for custom plastic parts, home injection molding is quickly gaining traction as a viable alternative to traditional manufacturing methods. The ability to create small to medium-sized batches of plastic parts at home provides individuals with a level of flexibility and control that is not possible with larger-scale production methods. This has led to a surge in interest from small businesses, makers, and industry professionals who are looking for a cost-effective and efficient way to produce plastic parts.One of the key advantages of home plastic injection molding is the ability to iterate on designs quickly and cost-effectively. With a desktop injection molding machine, individuals can test and refine their designs in a matter of hours, rather than waiting weeks for samples to be produced by a third-party manufacturer. This allows for greater innovation and creativity in the product development process, as well as the ability to respond quickly to changes in market demand.In addition to the machine, {Company} also offers a range of support and training materials for home molders. Their website features a wealth of resources, including tutorials, troubleshooting guides, and design tips, to help individuals get the most out of their injection molding machine. They also provide ongoing technical support to ensure that users are able to overcome any challenges they may encounter during the molding process.As the home plastic injection molding industry continues to grow, {Company} is at the forefront of innovation and development in this space. Their commitment to providing high-quality, user-friendly machines and comprehensive support services has made them a trusted name in the industry. With a focus on accessibility and affordability, they are helping to democratize the plastic manufacturing process, making it accessible to a wide range of individuals and businesses.The future of home plastic injection molding looks bright, with more and more individuals and businesses recognizing the value of this innovative manufacturing method. As technology continues to advance, and the barriers to entry continue to lower, we can expect to see even greater adoption of home injection molding in the years to come. With companies like {Company} leading the way, the possibilities for custom plastic part production are endless.
The Importance of Precision Machining in Manufacturing Industry
[Company Name] is a leading manufacturer of precision machining parts for a wide range of industries. With a focus on innovation and quality, [Company Name] strives to provide top-notch products to their customers. Their state-of-the-art facilities and advanced technology allow them to produce high precision components that meet the stringent requirements of various industries.Recently, [Company Name] introduced their latest innovation in precision machining, which promises to revolutionize the industry. This new technology aims to improve the accuracy and efficiency of machining processes, ultimately resulting in higher quality products for their customers.The precision machining process is crucial for manufacturing industries as it involves the shaping of metal and other materials to very specific dimensions and tolerances. Any minor error in the machining process can result in faulty products and production delays, making precision machining a critical aspect of manufacturing.[Company Name]'s new technology is designed to address the challenges and demands of precision machining. By leveraging advanced software and cutting-edge machinery, they have developed a system that is capable of achieving unparalleled accuracy and consistency in machining operations. This new technology not only enhances the precision of the machining process but also improves the overall efficiency and productivity of the manufacturing process.One of the key features of this new technology is its ability to minimize human error in the machining process. By automating certain aspects of the machining operation and integrating advanced quality control measures, [Company Name] ensures that the final products meet the highest standards of precision and quality. This not only reduces the risk of defects and rework but also streamlines the production process, leading to cost savings and faster lead times for their customers.Furthermore, [Company Name]'s new technology offers a higher degree of flexibility and versatility in machining operations. With the capability to handle a wide variety of materials and complex geometries, this technology allows [Company Name] to cater to the diverse needs of their customers across different industries. Whether it's aerospace components, medical devices, or automotive parts, [Company Name] can now deliver precision-machined products with unmatched accuracy and reliability.The introduction of this new technology exemplifies [Company Name]'s commitment to continuous improvement and innovation. As a forward-thinking company, they are constantly investing in research and development to stay ahead of the curve and provide their customers with the best solutions for their machining needs.In addition to their technological advancements, [Company Name] takes pride in their team of highly skilled engineers and machinists who are dedicated to delivering precision machining solutions. With their expertise and attention to detail, they ensure that every product meets the exact specifications and quality standards set by their customers.As a result of their relentless pursuit of excellence, [Company Name] has earned a stellar reputation in the industry for their precision machining capabilities. Their track record of delivering high-quality products and exceptional customer service has positioned them as a trusted partner for many leading companies across various sectors.At [Company Name], they understand the critical role that precision machining plays in the success of their customers' businesses. By investing in cutting-edge technology and fostering a culture of innovation, they are not only raising the bar for precision machining but also contributing to the growth and competitiveness of the industries they serve.In conclusion, the introduction of [Company Name]'s new precision machining technology marks a significant milestone in the industry. With its potential to elevate the standards of precision and efficiency in machining operations, this innovation demonstrates [Company Name]'s unwavering commitment to pushing the boundaries of what's possible in precision machining. As they continue to explore new frontiers in technology and engineering, [Company Name] is poised to lead the way in delivering unparalleled precision machining solutions for years to come.
High-Quality Moulding Machine Parts for Your Industrial Needs
Moulding Machine Parts is celebrating a decade of supplying high-quality equipment and parts to the manufacturing industry. The company has been a key player in the industry, providing innovative solutions and top-of-the-line products to its customers. As part of its commitment to excellence, Moulding Machine Parts has continuously worked to improve its products and services, setting a benchmark for the industry.With a focus on quality, precision, and reliability, Moulding Machine Parts has positioned itself as a leading supplier of moulding machine parts in the market. The company's parts are used in a wide range of industries, including automotive, aerospace, and consumer goods manufacturing. Moulding Machine Parts has earned a reputation for delivering superior products that meet and exceed industry standards.The company's success can be attributed to its skilled team of engineers and technicians, as well as its state-of-the-art manufacturing facilities. Moulding Machine Parts invests heavily in research and development to ensure that its products are at the forefront of technological advancements. This dedication to innovation has enabled the company to stay ahead of the competition and maintain its position as a trusted partner to its customers.One of the company's flagship products is its range of injection moulding machine parts. These parts are essential for the efficient operation of the machines, and Moulding Machine Parts has developed a comprehensive line of components that are known for their durability and performance. The company's injection moulding machine parts are designed to withstand the rigors of high-volume production, delivering consistent results and minimizing downtime.In addition to injection moulding machine parts, Moulding Machine Parts also offers a wide selection of other components and accessories for moulding machines. From screws and barrels to heating elements and controls, the company's product range is designed to meet the diverse needs of its customers. Moulding Machine Parts understands that each manufacturing operation is unique, and its team works closely with clients to provide customized solutions that address their specific requirements.Moulding Machine Parts is committed to providing exceptional customer service, and the company's support team is always on hand to assist customers with technical inquiries, troubleshooting, and product recommendations. By prioritizing customer satisfaction, Moulding Machine Parts has built long-lasting relationships with clients and has established a loyal customer base.Looking ahead, Moulding Machine Parts remains dedicated to driving innovation and setting new standards in the industry. The company is continuously exploring new technologies and refining its manufacturing processes to deliver the next generation of moulding machine parts. With a focus on sustainability and efficiency, Moulding Machine Parts is poised to lead the way in providing environmentally friendly solutions that reduce waste and energy consumption.As Moulding Machine Parts celebrates its 10-year anniversary, the company is proud to reflect on its achievements and the milestones it has reached. With a solid foundation built on expertise, quality, and customer satisfaction, Moulding Machine Parts looks forward to the next decade of serving the manufacturing industry and exceeding expectations.In conclusion, Moulding Machine Parts has set the standard for excellence in the supply of moulding machine parts. With a commitment to innovation, quality, and customer service, the company has established itself as a trusted partner to its clients. As it celebrates a decade of success, Moulding Machine Parts is well-positioned to continue its legacy of delivering cutting-edge solutions to the manufacturing industry.
Enhance Product Performance with Top-quality Injection Molding Inserts
Title: Innovation in Injection Molding Inserts: Enhancing Efficiency and PrecisionIntroduction (100 words)Injection molding is a widely used manufacturing process in various industries, including automotive, aerospace, consumer goods, and healthcare. As companies strive for greater efficiency and precision, the demand for innovative solutions continues to grow. Enter a leading manufacturer of injection molding inserts (brand name omitted), renowned for their cutting-edge technology and commitment to quality. With a proven track record in delivering high-performance solutions, the company has established itself as a trusted partner for numerous businesses, enabling them to achieve superior results in their manufacturing processes.8 Cutting-Edge Features of Injection Molding Inserts (600 words)1. Durability: Injection molding inserts by (brand name omitted) are made from premium-grade materials, ensuring durability and long-lasting performance. The inserts can withstand high-pressure molding operations without compromising their structural integrity, resulting in reduced maintenance costs and enhanced production efficiency.2. Precision Engineering: The inserts are meticulously designed and engineered to meet the precise specifications required by the customer. Through state-of-the-art manufacturing processes, (brand name omitted) ensures tight tolerances and uniformity, enabling flawless integration with the molding process. The result is consistently high-quality parts with minimal variations, reducing waste and optimizing productivity.3. Versatility: (Brand name omitted) offers a wide range of injection molding inserts suitable for a diverse array of applications. Whether it's intricate components for the electronics industry or robust parts for automotive manufacturing, the company's inserts cater to various needs. The flexibility in design and material selection allows customers to choose the most suitable insert for their specific requirements.4. Rapid Prototyping: Acknowledging the importance of quick turnaround times in today's competitive landscape, (brand name omitted) enables customers to rapidly prototype their designs. This not only aids in the refinement of the product but also reduces the time-to-market, giving businesses a competitive edge. The company's rapid prototyping capabilities ensure that customers can validate their designs and make necessary adjustments before moving into full-scale production.5. High Customization: (Brand name omitted) understands that every project is unique and requires specific solutions. Their injection molding inserts can be customized with various features, such as inserts with complex geometries, specialized surface finishes, or even personalized branding. This level of customization allows customers to optimize their manufacturing processes and differentiate their products in the market.6. Cost Efficiency: The company's injection molding inserts offer cost-effective solutions in terms of both initial investment and long-term production. The high-quality materials used in the inserts enhance their lifespan, ensuring fewer replacements and reduced downtime. Additionally, the precise engineering and tight tolerances contribute to minimal material waste, thereby increasing overall cost efficiency.7. Environmental Sustainability: (Brand name omitted) embraces sustainable practices by incorporating eco-friendly materials in their injection molding inserts. By utilizing recycled or biodegradable materials, the company contributes to reducing the carbon footprint. Moreover, the optimized manufacturing processes minimize waste generation, encouraging a greener approach while maintaining superior quality and performance.8. Exceptional Customer Support: (Brand name omitted) is known for its outstanding customer support throughout the entire project lifecycle. From initial product design to post-production assistance, the company's dedicated team of experts provides guidance, resolves queries, and offers technical assistance. Their commitment to customer satisfaction ensures a seamless experience for all customers.Conclusion (100 words)In an evolving manufacturing landscape, (brand name omitted) remains at the forefront of innovation in injection molding inserts. By offering a range of features such as durability, precision engineering, versatility, and cost efficiency, the company continues to provide customers with superior solutions to meet their manufacturing needs. With a commitment to environmental sustainability and exceptional customer support, (brand name omitted) consistently proves to be a reliable partner in achieving efficiency and precision in injection molding processes.
Revolutionary Casting Gating System Shows Promising Results
Title: Groundbreaking Casting Gating System Revolutionizes the Manufacturing IndustryIntroduction:In a landmark development, a cutting-edge Casting Gating System, developed by a renowned manufacturing solutions company, is set to redefine the manufacturing industry. This innovative system, which combines advanced technology with superior materials, is poised to streamline the casting process, significantly improving efficiency and product quality.Background:The use of casting techniques has long been integral to the manufacturing industry. While traditional casting methods have proven effective, they often suffer from limitations that can hamper productivity and output quality. Recognizing this need for enhancement, Company X has introduced an exceptional solution - the Casting Gating System.Enhanced Efficiency through Advanced Technology:The Casting Gating System incorporates state-of-the-art technology to accomplish unprecedented levels of efficiency. Its cutting-edge features optimize the casting process, ensuring precise and controlled material flow. This innovative system minimizes casting defects, such as porosity or unevenness, that can hinder the overall quality of the finished products.The system consists of high-quality gating components that regulate the flow of molten metal or other materials into the mold during the casting process. By allocating material distribution more evenly and precisely, the Casting Gating System maximizes yield, reduces waste, and expedites the manufacturing cycle.Unmatched Product Quality:With its precise control over the flow of materials, the innovative Casting Gating System guarantees exceptional product quality. By eliminating irregularities, it minimizes the risk of casting defects, creating superior products that meet or exceed industry standards. As a result, manufacturers utilizing this system can elevate their reputation for delivering reliable and high-quality products to their customers.Furthermore, the system's unique design and precision allow for easy customization according to specific casting requirements. Manufacturers can optimize gating configurations to suit various materials, molds, and casting processes, further enhancing the quality of the end products.Sustainability and Cost Optimization:In addition to its performance benefits, the Casting Gating System also offers long-term sustainability advantages. By minimizing material waste, manufacturers can reduce both their environmental footprint and production costs. This innovative system optimizes resource utilization, resulting in enhanced profitability and a greener manufacturing process.The adjustable nature of the system enables manufacturers to optimize material flow, reducing the need for additional raw materials. This adaptability contributes to cost-efficiency, making the Casting Gating System an economically viable choice for manufacturers across various industries.Endorsements and Case Studies:Industry leaders who have adopted the Casting Gating System have witnessed transformative results. Numerous case studies demonstrate remarkable improvements in casting efficiency, quality, and profitability. Notable success stories within the automotive, aerospace, and machinery sectors speak volumes about the system's ability to revolutionize casting processes.Experts from within the manufacturing domain are overwhelmingly positive about the potential of this innovative gating system. Recognized professionals have praised how the system augments overall efficiency, enhances product quality, and supports sustainable production practices.Conclusion:The introduction of the groundbreaking Casting Gating System has ushered in a new era for the manufacturing industry. Combining sophisticated technology with superior design, this innovative system significantly enhances casting processes, ensuring optimal efficiency, exceptional product quality, and sustainable manufacturing practices. Manufacturers across various sectors can now reimagine their production capabilities, elevate their output, and cement their position as leaders in the global marketplace.By embracing the Casting Gating System, companies can stay ahead of the competition, satisfy customer demands, and ultimately contribute to the progress of the manufacturing industry as a whole.
High-Quality Machining Parts for Optimal Performance
Title: Industry-Leading Company Paving the Way in Precision Brass Machining PartsIntroduction:In today's rapidly evolving industrial landscape, the demand for high-quality and precision machined parts continues to rise. With this in mind, one company stands tall as a leader in the industry, offering unparalleled expertise and innovation in brass machining parts. With a commitment to delivering exceptional products and dedicating themselves to customer satisfaction, this industry giant has become a go-to source for clients looking to meet their brass machining needs.[Company Name], a globally renowned manufacturer and supplier of brass machining parts, has carved a niche for itself through its dedication to excellence. With cutting-edge facilities, state-of-the-art technology, and a team of highly skilled professionals, the company has the capabilities to produce intricate and sophisticated brass components that meet the highest standards of quality.Offering a wide range of brass machining parts, [Company Name] has become a trusted partner for industries ranging from automotive and aerospace to medical and electronics. The expertise of their engineering team allows them to cater to the unique specifications and requirements of each client, ensuring precise solutions that enhance the efficiency and effectiveness of their operations.Industry-Leading Capabilities:With an unwavering commitment to technological advancements, [Company Name] has continuously invested in state-of-the-art machinery and equipment. This extensive assortment of high-precision CNC machines empowers the company to undertake complex machining projects with ease, delivering exceptional results time and again.To further enhance their capabilities, [Company Name] has established a stringent quality control system. Every brass machining part undergoes rigorous inspection and testing at various stages of the production process, guaranteeing products that exceed industry standards. By adhering to these strict quality control protocols, the company ensures the durability, precision, and reliability of every single part that they deliver.Innovation and Customization:Understanding that industries thrive on innovation, [Company Name] constantly seeks opportunities to push the boundaries of brass machining. The company's research and development team is at the forefront of exploring new materials, techniques, and processes that can enhance the functionality and performance of their brass parts.Moreover, [Company Name] places great emphasis on customization, recognizing that each client may have unique requirements. By working closely with their customers, the company tailors their brass machining parts to exact specifications, providing bespoke solutions that perfectly align with individual needs. This personalized approach enables them to create components that seamlessly integrate into clients' assembly lines, resulting in optimized productivity and seamless operations.Global Reach and Sustainable Practices:With a global footprint, [Company Name] has successfully established a strong presence in various markets around the world. By catering to the needs of diverse industries, they have built trust and credibility as a reliable partner in the field of brass machining parts manufacturing.Furthermore, [Company Name] places great importance on sustainability and environmental responsibility. In their manufacturing processes, they prioritize the use of eco-friendly materials and adhere to stringent waste management practices. By ensuring that their operations have minimal impact on the environment, they set an example for the industry and contribute towards a greener future.Conclusion:As the demand for precision brass machining parts intensifies, [Company Name] continues to lead the industry with its unwavering dedication to quality, innovation, and customer satisfaction. With a globally recognized presence, cutting-edge technology, and a commitment to sustainability, they remain steadfast in delivering the highest-quality brass machining parts that meet the evolving needs of industries around the world.
Efficient Methods for Machining Large Parts Unveiled
Machining Large Parts: Revolutionizing Manufacturing with Precision and EfficiencyIn today's ever-evolving world of manufacturing, precision and efficiency remain the utmost priority for businesses. As industries continue to push the boundaries of innovation, the demand for machining large parts has soared remarkably. One company, known for its commitment to excellence and cutting-edge technology, has emerged as a leader in this field, providing innovative solutions that are revolutionizing the manufacturing industry. With a strong focus on pushing the limits of what is possible, this company has consistently delivered exceptional results. Through state-of-the-art facilities and a team of skilled professionals, they have perfected the art of machining large parts. Equipped with advanced CNC machines and a diverse range of cutting tools, they have the capability to manufacture components of extraordinary size and complexity, meeting the most stringent specifications and requirements of their clients.Harnessing the immense potential of computer-aided design (CAD) and computer-aided manufacturing (CAM), this company has paved the way for precision machining on an unprecedented scale. By utilizing powerful software solutions, they are able to seamlessly translate digital designs into tangible products, utilizing a streamlined and highly efficient process. This allows for increased accuracy and repeatability, ensuring that every machined part is an exact replica of the original design.One of the key advantages this company offers is their ability to handle large parts without compromising on quality. Their state-of-the-art machining centers can accommodate components that weigh up to several tons, demonstrating their commitment to tackling even the most ambitious projects. By integrating cutting-edge technology with extensive knowledge and experience, they have eliminated the traditional limitations associated with machining large parts, opening up new possibilities for manufacturers across various industries.The company's dedication to excellence and innovation is further exemplified by their team of highly skilled engineers and technicians. With a deep understanding of the intricacies of machining large parts, they meticulously plan and execute each project, ensuring that every component meets the highest standards of quality. Their expertise extends beyond conventional methodologies, allowing them to develop customized solutions that address the unique challenges presented by each project.Furthermore, this company's commitment to sustainable practices sets them apart from their competitors. By leveraging advanced manufacturing techniques, such as near-net-shape machining and optimal material utilization, they reduce waste and minimize environmental impact. Additionally, they prioritize the use of recyclable materials, further contributing to a greener and more sustainable future.The applications of these machined large parts span across various industries, including aerospace, automotive, energy, and heavy machinery. From manufacturing precision-engineered components for aircraft engines to producing critical automotive components, this company's expertise and capabilities are highly sought-after by manufacturers worldwide.In conclusion, the demand for machining large parts continues to rise in today's competitive manufacturing landscape. This company, with its dedication to excellence, innovation, and sustainability, is at the forefront of this revolution. Through the utilization of advanced technology, a skilled workforce, and a commitment to exceptional quality, they have redefined what is possible in precision machining of large parts. As industries continue to evolve, they will undoubtedly remain a driving force in shaping the future of manufacturing, enabling businesses to achieve greater precision and efficiency in their operations.