Exploring the Limitations of Sand Casting: Factors Hindering the Process
By:Admin
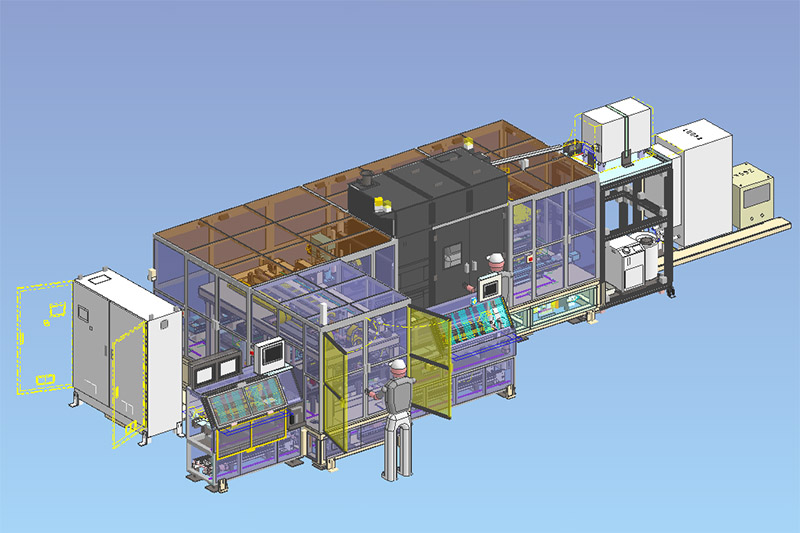
Introduction:
In the realm of manufacturing, sand casting has long been a traditional and widely-used technique for creating intricate and durable metal components. Many companies, including {}, have successfully employed sand casting in their production processes. However, it is important to be aware of the disadvantages associated with this method in order to make informed decisions in the manufacturing industry.
Sand Casting and its Application:
Before delving into the drawbacks, it is crucial to understand the fundamentals of sand casting. The process involves pouring molten metal into a sand mold to create a desired shape. This method offers flexibility, affordability, and the ability to produce intricate components with various alloys. Sand casting is widely used in industries like automotive, aerospace, and construction, where complex parts are required.
Disadvantage 1: Limited Surface Finish and Precision:
One of the major shortcomings of sand casting is the limitation it presents in achieving high surface finish and precision. The texture of the sand mold often transfers inconsistencies onto the final product, resulting in a rougher surface finish. Moreover, the molding process may introduce slight variations in dimensions, making it challenging to achieve precise measurements and tight tolerances. These factors can be critical in industries where the aesthetics and precision of components are paramount, such as consumer electronics and medical devices.
Disadvantage 2: Time and Labor Intensive:
Sand casting is a time and labor-intensive process, which can significantly impact the overall production timeline and costs. Preparing the molds, including pattern creation, gating system design, and mold assembly, requires skilled labor and careful execution. Additionally, molten metal must be cooled and solidified in the mold, followed by the removal of excess sand and finishing operations. Addressing these steps can be time-consuming, leading to longer lead times and reduced efficiency, especially for industries characterized by high-volume production demands.
Disadvantage 3: Limited Complexity and Assembly Integration:
While sand casting is suitable for various complex shapes, it has limitations in terms of intricate designs and integration with assembly components. The mold's internal cavities can be challenging to achieve with precision, prohibiting the creation of intricate features. Furthermore, sand casting may not be ideal for components requiring internal passageways, such as cooling channels, as the removal of the sand mold can be difficult and may compromise the final product's integrity. For industries that heavily rely on intricate designs and integration, such as semiconductor manufacturing or advanced machinery, alternative production methods like precision machining may be preferred.
Disadvantage 4: Material Waste and Environmental Concerns:
Sand casting generates a significant amount of waste material. After each casting, sand molds become unusable and are discarded, contributing to environmental concerns. Additionally, the process can consume large quantities of sand, leading to mining activities and the depletion of natural resources. Companies like {} have been actively working towards sustainable solutions by implementing recycling processes and exploring environmentally-friendly alternatives to sand molds, such as 3D-printed molds or investment casting.
Conclusion:
Sand casting undeniably plays a crucial role in the manufacturing industry, with its affordability and flexibility making it an attractive choice for many companies, including {}. However, it is essential to be aware of its disadvantages, which include limited surface finish and precision, time and labor intensiveness, limited complexity and integration, and environmental concerns. By understanding these drawbacks, manufacturers can make more informed decisions when choosing their production methods, potentially optimizing their processes and meeting the demands of their respective industries while considering sustainability needs.
Company News & Blog
The Advantages of Computerized Numerical Control in Manufacturing
Computerized Numerical Control (CNC) technology has revolutionized the manufacturing industry, offering precision, efficiency, and enhanced flexibility. These machines have significantly transformed the way companies operate, as they automate the production process and eliminate manual tasks. One of the leading providers of CNC solutions is the company {} which offers a wide range of cutting-edge products designed to meet various manufacturing needs.With over XX years of experience in the field, {} has established itself as a prominent player in the CNC market. The company has continuously invested in research and development to deliver innovative solutions that cater to the evolving needs of manufacturers worldwide. The result is a comprehensive portfolio of products renowned for their high performance, reliability, and user-friendly interface.The backbone of {}'s CNC technology lies in its computer-based control system, which enables precise and consistent machining operations. This system uses a combination of software and hardware to interpret the design specifications and convert them into machine-readable instructions. By leveraging advanced algorithms and powerful processing capabilities, the CNC machines achieve unparalleled accuracy and productivity.One of the standout features of {}'s CNC machines is their versatility, allowing them to handle a wide range of materials and produce complex components with ease. Whether it's metal, plastic, or wood, these machines can effectively cut, drill, and shape the material as per the given specifications. This flexibility opens up a world of possibilities for manufacturers, enabling them to meet the demands of various industries such as automotive, aerospace, and medical.Furthermore, {}'s CNC machines offer a host of advanced functionalities that enhance productivity and efficiency. For instance, the machines can automatically change tools, reducing downtime and enabling continuous machining operations. The integration of sensors and feedback systems ensures real-time monitoring and adjustment, minimizing errors and improving overall quality. Additionally, intuitive programming interfaces and simulation capabilities simplify the setup process and enable manufacturers to optimize their workflows.In an era where customization and fast production cycles are paramount, {}'s CNC solutions have proven to be an indispensable asset for manufacturers. These machines cut down on lead times and allow for rapid prototyping and iteration. With the ability to quickly reconfigure the machines, manufacturers can swiftly adapt to changing market demands and stay ahead of the competition.Moreover, the integration of CNC machines with computer-aided design (CAD) and computer-aided manufacturing (CAM) software further streamlines the production process. Design files can directly be fed into the CNC machines, eliminating the need for manual input and reducing human errors. This seamless integration also facilitates seamless communication between design and manufacturing teams, fostering collaboration and accelerating time to market.{} is committed to providing exceptional customer support and after-sales service, ensuring that manufacturers can maximize the value of their CNC investments. The company offers comprehensive training programs for operators and maintenance personnel, equipping them with the necessary skills to optimize machine performance and troubleshoot potential issues. In addition, {}'s global network of service centers ensures prompt assistance and spare parts availability, minimizing downtime and maximizing productivity.With a reputation for excellence and a relentless pursuit of technological advancements, {} continues to push the boundaries of CNC technology. By combining innovative designs, superior quality, and unparalleled customer support, the company remains at the forefront of the industry, supporting manufacturers in their quest for precision and efficiency.In conclusion, Computerized Numerical Control (CNC) technology has transformed the manufacturing landscape, offering manufacturers the ability to produce high-quality, precise components efficiently and effectively. Companies like {} have played a pivotal role in this transformation, providing state-of-the-art CNC solutions that cater to diverse manufacturing needs. With their advanced features, versatility, and commitment to customer satisfaction, {}'s CNC machines empower manufacturers to stay ahead in a competitive market and embrace the future of manufacturing.
Efficient Methods for Machining Large Parts Unveiled
Machining Large Parts: Revolutionizing Manufacturing with Precision and EfficiencyIn today's ever-evolving world of manufacturing, precision and efficiency remain the utmost priority for businesses. As industries continue to push the boundaries of innovation, the demand for machining large parts has soared remarkably. One company, known for its commitment to excellence and cutting-edge technology, has emerged as a leader in this field, providing innovative solutions that are revolutionizing the manufacturing industry. With a strong focus on pushing the limits of what is possible, this company has consistently delivered exceptional results. Through state-of-the-art facilities and a team of skilled professionals, they have perfected the art of machining large parts. Equipped with advanced CNC machines and a diverse range of cutting tools, they have the capability to manufacture components of extraordinary size and complexity, meeting the most stringent specifications and requirements of their clients.Harnessing the immense potential of computer-aided design (CAD) and computer-aided manufacturing (CAM), this company has paved the way for precision machining on an unprecedented scale. By utilizing powerful software solutions, they are able to seamlessly translate digital designs into tangible products, utilizing a streamlined and highly efficient process. This allows for increased accuracy and repeatability, ensuring that every machined part is an exact replica of the original design.One of the key advantages this company offers is their ability to handle large parts without compromising on quality. Their state-of-the-art machining centers can accommodate components that weigh up to several tons, demonstrating their commitment to tackling even the most ambitious projects. By integrating cutting-edge technology with extensive knowledge and experience, they have eliminated the traditional limitations associated with machining large parts, opening up new possibilities for manufacturers across various industries.The company's dedication to excellence and innovation is further exemplified by their team of highly skilled engineers and technicians. With a deep understanding of the intricacies of machining large parts, they meticulously plan and execute each project, ensuring that every component meets the highest standards of quality. Their expertise extends beyond conventional methodologies, allowing them to develop customized solutions that address the unique challenges presented by each project.Furthermore, this company's commitment to sustainable practices sets them apart from their competitors. By leveraging advanced manufacturing techniques, such as near-net-shape machining and optimal material utilization, they reduce waste and minimize environmental impact. Additionally, they prioritize the use of recyclable materials, further contributing to a greener and more sustainable future.The applications of these machined large parts span across various industries, including aerospace, automotive, energy, and heavy machinery. From manufacturing precision-engineered components for aircraft engines to producing critical automotive components, this company's expertise and capabilities are highly sought-after by manufacturers worldwide.In conclusion, the demand for machining large parts continues to rise in today's competitive manufacturing landscape. This company, with its dedication to excellence, innovation, and sustainability, is at the forefront of this revolution. Through the utilization of advanced technology, a skilled workforce, and a commitment to exceptional quality, they have redefined what is possible in precision machining of large parts. As industries continue to evolve, they will undoubtedly remain a driving force in shaping the future of manufacturing, enabling businesses to achieve greater precision and efficiency in their operations.
Expert Tips for Machining Metal: The Ultimate Guide for Precision Metalwork
Title: Revolutionizing Metal Machining: Company X Introduces Cutting-Edge InnovationIntroduction:In the dynamic world of metal machining, Company X has emerged as a leading pioneer, focusing on elevating precision and efficiency to new heights. With their unwavering commitment to research and development, they have introduced groundbreaking technologies that are poised to revolutionize the industry. In this article, we delve into Company X's latest innovation in machining metal, its features, and the potential implications on industries worldwide.Enhancing Precision and Efficiency:Building on their expertise in metal machining, Company X has unveiled a cutting-edge technology that promises enhanced precision and efficiency in the manufacturing process. By combining advanced robotics, artificial intelligence, and state-of-the-art algorithms, their innovation ensures unrivaled accuracy and repeatability.The integration of robotics enables Company X to carry out intricate machining tasks with unprecedented precision. These robots are equipped with advanced sensors that constantly monitor the machining process, making real-time adjustments to ensure optimal results. Moreover, with the use of artificial intelligence, the machines are capable of learning and adapting, further improving their precision over time.Additionally, Company X's innovation incorporates proprietary algorithms, specifically designed to optimize machining parameters. By analyzing vast amounts of data generated during the machining process, these algorithms can identify the ideal conditions for different applications. This results in reduced waste, improved surface finishes, and increased overall efficiency.Addressing Cost and Time Constraints:Recognizing the time and cost implications involved in traditional metal machining processes, Company X's new technology aims to alleviate these concerns. With their advanced automation systems, machining processes are streamlined, eliminating manual errors and reducing human intervention. This automation not only saves time but also minimizes labor costs, ultimately enhancing cost-effectiveness for businesses.Moreover, Company X's technology enables a significant reduction in lead times. By implementing predictive maintenance through continuous monitoring, downtime due to machinery failures is minimized. Consequently, businesses can maintain optimal productivity, meeting tight delivery deadlines without compromising on quality.Application across Industries:Company X's innovation transcends the constraints of a single industry. This breakthrough technology is applicable across diverse sectors such as automotive, aerospace, medical, and electronics, just to name a few.In the automotive sector, for instance, precision machining is crucial for the production of engine components, ensuring optimal performance and longevity. With Company X's technology, manufacturers can achieve unparalleled precision, resulting in improved efficiency, reduced friction, and lower emissions.Likewise, in the aerospace industry, where precision and safety are paramount, Company X's innovation brings unparalleled advantages. From manufacturing turbine blades to intricate structural components, their technology guarantees precise tolerances, which are critical for aircraft performance and passenger safety.Looking Ahead:With their latest innovation in metal machining, Company X has showcased their dedication to pushing the boundaries of what is possible. This advanced technology not only enhances precision and efficiency but also addresses cost and time constraints, positioning Company X as a trailblazer in the industry.As businesses across industries seek to stay competitive in a rapidly changing market, Company X's technology presents a compelling solution. By embracing this revolutionary approach to metal machining, businesses can unlock new levels of productivity, quality, and profitability.In conclusion, Company X has boldly redefined the metal machining landscape with its cutting-edge innovation. As this technology becomes more widespread, it has the potential to transform industries worldwide by revolutionizing the production process, streamlining operations, and elevating the standards of precision and efficiency.
Discover the Latest Advancements in Plastic Injection Molding Parts
Plastic Injection Molding Parts Revolutionizing the Manufacturing IndustryIn today's fast-paced manufacturing industry, plastic injection molding has become a game-changer. With its ability to produce high-quality, intricate, and cost-effective parts, this manufacturing process has gained immense popularity across various sectors. One company that has risen to prominence in this field is (Company Name).With years of experience and expertise, (Company Name) has positioned itself as a frontrunner in producing top-notch plastic injection molding parts. Their commitment to innovation, quality, and customer satisfaction has helped them carve a niche for themselves in the industry.The plastic injection molding process involves injecting molten plastic into a mold cavity to shape it into the desired part. This method offers significant advantages over traditional manufacturing techniques. First and foremost, it allows for the production of complex geometries that would otherwise be difficult or impossible to manufacture. The ability to create intricate designs with high precision has revolutionized various industries, including automotive, electronics, and medical devices.(Company Name) leverages cutting-edge technology and state-of-the-art machinery to deliver consistently high-quality plastic injection molding parts. Their manufacturing facility is equipped with the latest computer-aided design (CAD) software, ensuring precise and accurate mold designs. This technology enables them to optimize part functionality, minimize material waste, and enhance overall efficiency.One of the key advantages of plastic injection molding is its cost-effectiveness. With the ability to produce large quantities of parts in a relatively short span of time, the per-unit cost of production decreases significantly. This makes plastic injection molding an attractive choice for companies looking to scale up their manufacturing operations without sacrificing quality or increasing costs.Furthermore, plastic injection molding offers excellent repeatability, ensuring consistent part quality. Once the initial mold is designed and perfected, subsequent parts can be replicated to the exact specifications, eliminating the need for manual adjustments or rework. This level of consistency is critical for industries with strict quality standards, such as aerospace and medical device manufacturing.(Company Name) takes pride in its commitment to sustainability and environmental responsibility. They employ eco-friendly practices throughout their production process, including the use of recyclable materials and responsible waste management. By optimizing material usage and minimizing waste, they contribute to reducing the environmental impact of plastic injection molding.Customer satisfaction is at the core of (Company Name)'s values. They work closely with their clients to understand their specific requirements, offering customized solutions to meet their unique needs. Whether it's a small-scale project or a large-scale production run, they ensure that every client receives the highest level of attention and support.The automotive industry is one of the primary beneficiaries of plastic injection molding. With the increasing demand for lightweight vehicles, manufacturers rely heavily on plastic components to reduce overall weight and improve fuel efficiency. (Company Name) has successfully served many leading automotive companies, providing them with top-quality plastic injection molding parts that meet stringent safety and performance standards.Apart from the automotive sector, (Company Name) caters to a diverse range of industries, including electronics, consumer goods, and medical devices. Their ability to produce parts with exceptional precision, durability, and aesthetic appeal has earned them a reputation for excellence across various sectors.As plastic injection molding continues to evolve and revolutionize the manufacturing industry, (Company Name) remains at the forefront of innovation, constantly exploring new techniques and materials. Their dedication to quality, customer satisfaction, and environmental responsibility solidifies their position as a leading provider of plastic injection molding parts.In conclusion, plastic injection molding has emerged as a game-changer in the manufacturing industry. With its ability to produce intricate designs, cost-effective production, and high-quality parts, this process has opened new avenues for various sectors. (Company Name), with its expertise and commitment to excellence, plays a crucial role in transforming customer ideas into reality using plastic injection molding. Their cutting-edge technology, sustainable practices, and customer-centric approach make them a reliable choice for businesses looking to optimize their manufacturing processes and deliver superior products.
Exploring the Limitations of Sand Casting: Factors Hindering the Process
Title: Exploring Sand Casting Disadvantages in the Manufacturing IndustryIntroduction:In the realm of manufacturing, sand casting has long been a traditional and widely-used technique for creating intricate and durable metal components. Many companies, including {}, have successfully employed sand casting in their production processes. However, it is important to be aware of the disadvantages associated with this method in order to make informed decisions in the manufacturing industry.Sand Casting and its Application:Before delving into the drawbacks, it is crucial to understand the fundamentals of sand casting. The process involves pouring molten metal into a sand mold to create a desired shape. This method offers flexibility, affordability, and the ability to produce intricate components with various alloys. Sand casting is widely used in industries like automotive, aerospace, and construction, where complex parts are required.Disadvantage 1: Limited Surface Finish and Precision:One of the major shortcomings of sand casting is the limitation it presents in achieving high surface finish and precision. The texture of the sand mold often transfers inconsistencies onto the final product, resulting in a rougher surface finish. Moreover, the molding process may introduce slight variations in dimensions, making it challenging to achieve precise measurements and tight tolerances. These factors can be critical in industries where the aesthetics and precision of components are paramount, such as consumer electronics and medical devices.Disadvantage 2: Time and Labor Intensive:Sand casting is a time and labor-intensive process, which can significantly impact the overall production timeline and costs. Preparing the molds, including pattern creation, gating system design, and mold assembly, requires skilled labor and careful execution. Additionally, molten metal must be cooled and solidified in the mold, followed by the removal of excess sand and finishing operations. Addressing these steps can be time-consuming, leading to longer lead times and reduced efficiency, especially for industries characterized by high-volume production demands.Disadvantage 3: Limited Complexity and Assembly Integration:While sand casting is suitable for various complex shapes, it has limitations in terms of intricate designs and integration with assembly components. The mold's internal cavities can be challenging to achieve with precision, prohibiting the creation of intricate features. Furthermore, sand casting may not be ideal for components requiring internal passageways, such as cooling channels, as the removal of the sand mold can be difficult and may compromise the final product's integrity. For industries that heavily rely on intricate designs and integration, such as semiconductor manufacturing or advanced machinery, alternative production methods like precision machining may be preferred.Disadvantage 4: Material Waste and Environmental Concerns:Sand casting generates a significant amount of waste material. After each casting, sand molds become unusable and are discarded, contributing to environmental concerns. Additionally, the process can consume large quantities of sand, leading to mining activities and the depletion of natural resources. Companies like {} have been actively working towards sustainable solutions by implementing recycling processes and exploring environmentally-friendly alternatives to sand molds, such as 3D-printed molds or investment casting.Conclusion:Sand casting undeniably plays a crucial role in the manufacturing industry, with its affordability and flexibility making it an attractive choice for many companies, including {}. However, it is essential to be aware of its disadvantages, which include limited surface finish and precision, time and labor intensiveness, limited complexity and integration, and environmental concerns. By understanding these drawbacks, manufacturers can make more informed decisions when choosing their production methods, potentially optimizing their processes and meeting the demands of their respective industries while considering sustainability needs.
Enhancing Efficiency and Precision: The Ultimate Guide to Machining Fixture Design
Machining Fixture Design: Enhancing Precision and Efficiency in ManufacturingIn today's fast-paced manufacturing industry, precision and efficiency are paramount. Companies are constantly searching for ways to improve their production processes, reduce costs, and enhance product quality. One such solution that has gained significant attention is machining fixture design. By removing brand names, we can focus on the concept itself and explore how this innovative technology is revolutionizing manufacturing.Machining fixtures are specialized tools used to hold and position workpieces during machining operations. They ensure that the workpiece remains stable and secure, minimizing errors and maximizing productivity. By providing a rigid support structure, machining fixtures enable precision machining, resulting in accurate and consistent parts.With advancements in design and engineering, machining fixtures have evolved to cater to the unique requirements of various industries. Whether it is the automotive, aerospace, or electronics sectors, machining fixture design plays a vital role in optimizing the manufacturing process. By customizing the fixtures according to the specific needs of the product, companies can achieve greater flexibility and efficiency.One key factor contributing to the success of machining fixture design is computer-aided design (CAD) software. CAD allows engineers to create highly complex and detailed fixture designs, taking into account factors such as material properties, clamping forces, and geometric constraints. By simulating the machining process in a virtual environment, engineers can identify potential issues and make necessary adjustments before manufacturing the actual fixture. This not only saves time but also reduces the risk of errors, ensuring a seamless production process.Furthermore, the integration of CAD with computer-aided manufacturing (CAM) software allows for a streamlined transition from design to production. The CAM software generates machine instructions directly from the CAD model, enabling the efficient programming of machining operations. This integration promotes collaboration between design and production teams, resulting in better communication, reduced lead times, and improved overall efficiency.In addition to CAD and CAM, the use of advanced materials and technologies has revolutionized machining fixture design. Lightweight and high-strength materials, such as aluminum alloys and carbon fiber reinforced polymers, have replaced traditional materials like steel. These modern materials offer greater rigidity, reducing vibrations during the machining process and improving surface finish quality. Moreover, they contribute to the overall weight reduction of fixtures, making them more ergonomic and easier to handle.In line with the principles of Industry 4.0, machining fixture design has also embraced automation and robotics. Robotic machining fixtures are capable of performing complex tasks with high precision, reducing human errors and dependence. These fixtures can be programmed to adapt to different workpieces, further enhancing flexibility in production processes. By automating repetitive tasks, manufacturers can increase productivity, reduce costs, and improve worker safety.The company, known for its expertise in machining fixture design, has been at the forefront of these advancements. With a dedicated team of engineers and designers, they have consistently pushed the boundaries of innovation in manufacturing. By continually investing in research and development, the company has been able to develop cutting-edge solutions tailored to meet specific customer needs.From the automotive industry to aerospace and beyond, this company's machining fixtures have become synonymous with precision and efficiency. Their commitment to quality and customer satisfaction has made them a trusted partner for numerous manufacturers worldwide. Through their collaborations and partnerships, they aim to further optimize machining processes, driving the industry towards greater productivity and competitiveness.In conclusion, machining fixture design holds tremendous potential for the manufacturing industry. By leveraging the power of CAD, CAM, advanced materials, and automation, companies can enhance precision, improve efficiency, and reduce costs. As this technology continues to evolve, it is expected to play an increasingly integral role in the manufacturing landscape, enabling businesses to stay ahead in the competitive global market.
Boost Your Manufacturing Process with Efficient 3-Axis CNC Machining
Title: Revolutionary 3-Axis CNC Machining Ushering in a New Era of Precision ManufacturingIntroduction:In the fast-paced world of manufacturing, companies are constantly seeking more efficient and accurate methods to produce high-quality products in a cost-effective manner. This quest for excellence has driven the development of advanced technologies such as the revolutionary 3-axis CNC machining system. With its exceptional precision and versatility, this cutting-edge methodology has garnered worldwide acclaim, transforming the manufacturing landscape across industries.Body:1. What is 3-Axis CNC Machining?At its core, 3-axis CNC machining is a computer-controlled process used to shape materials such as metal, plastic, or wood, providing unparalleled precision and repeatability. This technology enables the creation of complex and intricate designs with remarkable speed and accuracy, far surpassing the capabilities of traditional manual machining.2. The Advantages of 3-Axis CNC Machining:a. Precision: The precise movement of the 3-axis CNC machine ensures accurate and consistent outcomes, reducing human errors to an absolute minimum. This level of precision allows manufacturers to create highly intricate and complex designs that were once unachievable.b. Versatility: Unlike other machining methods, 3-axis CNC machining offers unparalleled versatility. It can be used to shape a wide range of materials, from plastics to metals, with ease. This adaptability enables manufacturers to cater to diverse industries, from automotive and aerospace to electronics and medical.c. Efficiency: The automation capabilities of 3-axis CNC machining dramatically enhance efficiency. This system can run continuously, maximizing productivity while minimizing downtime traditionally associated with manual operations. Additionally, the ability to program the machine precisely allows for the replication of parts with consistent quality, further speeding up the manufacturing process.d. Cost-effectiveness: Although initial investment costs may be higher, 3-axis CNC machining saves money in the long run. The reduced labor requirements and increased efficiency lead to lower operating costs, improved productivity, and minimized waste. Furthermore, this method allows for the production of intricate designs without costly manual labor, making it an economical choice for manufacturers.3. Applications of 3-Axis CNC Machining:The versatility of 3-axis CNC machining has enabled its application in numerous industries. Below are some areas where this technology is extensively used:a. Automotive: In the automotive industry, 3-axis CNC machining is employed to produce high-precision components, such as engine parts, transmission components, and intricate car body shapes.b. Aerospace: The aerospace industry relies on 3-axis CNC machining to create vital parts such as turbine blades, control surfaces, and structural components. The consistent precision and reliability of this technology are critical for ensuring flight safety.c. Electronics: The production of complex electronic devices demands precise machining, making 3-axis CNC machining a preferred option. It is used to manufacture circuit boards, connectors, and intricate casings, guaranteeing a high level of precision and minimizing electrical malfunctions.d. Medical: In the medical field, 3-axis CNC machining is essential for the manufacturing of intricate surgical instruments, implants, orthopedic devices, and prosthetics. This technology allows for precision that is crucial in these life-saving applications.Conclusion:The advent of 3-axis CNC machining has revolutionized precision manufacturing across industries. Its unparalleled precision, versatility, efficiency, and cost-effectiveness have made it an integral part of modern manufacturing processes, elevating the standard of quality and contributing to technological advances. As technology continues to evolve, 3-axis CNC machining is expected to further enhance manufacturing capabilities, driving innovation and propelling various industries toward a future of unprecedented precision and efficiency.
Revolutionary Casting Gating System Shows Promising Results
Title: Groundbreaking Casting Gating System Revolutionizes the Manufacturing IndustryIntroduction:In a landmark development, a cutting-edge Casting Gating System, developed by a renowned manufacturing solutions company, is set to redefine the manufacturing industry. This innovative system, which combines advanced technology with superior materials, is poised to streamline the casting process, significantly improving efficiency and product quality.Background:The use of casting techniques has long been integral to the manufacturing industry. While traditional casting methods have proven effective, they often suffer from limitations that can hamper productivity and output quality. Recognizing this need for enhancement, Company X has introduced an exceptional solution - the Casting Gating System.Enhanced Efficiency through Advanced Technology:The Casting Gating System incorporates state-of-the-art technology to accomplish unprecedented levels of efficiency. Its cutting-edge features optimize the casting process, ensuring precise and controlled material flow. This innovative system minimizes casting defects, such as porosity or unevenness, that can hinder the overall quality of the finished products.The system consists of high-quality gating components that regulate the flow of molten metal or other materials into the mold during the casting process. By allocating material distribution more evenly and precisely, the Casting Gating System maximizes yield, reduces waste, and expedites the manufacturing cycle.Unmatched Product Quality:With its precise control over the flow of materials, the innovative Casting Gating System guarantees exceptional product quality. By eliminating irregularities, it minimizes the risk of casting defects, creating superior products that meet or exceed industry standards. As a result, manufacturers utilizing this system can elevate their reputation for delivering reliable and high-quality products to their customers.Furthermore, the system's unique design and precision allow for easy customization according to specific casting requirements. Manufacturers can optimize gating configurations to suit various materials, molds, and casting processes, further enhancing the quality of the end products.Sustainability and Cost Optimization:In addition to its performance benefits, the Casting Gating System also offers long-term sustainability advantages. By minimizing material waste, manufacturers can reduce both their environmental footprint and production costs. This innovative system optimizes resource utilization, resulting in enhanced profitability and a greener manufacturing process.The adjustable nature of the system enables manufacturers to optimize material flow, reducing the need for additional raw materials. This adaptability contributes to cost-efficiency, making the Casting Gating System an economically viable choice for manufacturers across various industries.Endorsements and Case Studies:Industry leaders who have adopted the Casting Gating System have witnessed transformative results. Numerous case studies demonstrate remarkable improvements in casting efficiency, quality, and profitability. Notable success stories within the automotive, aerospace, and machinery sectors speak volumes about the system's ability to revolutionize casting processes.Experts from within the manufacturing domain are overwhelmingly positive about the potential of this innovative gating system. Recognized professionals have praised how the system augments overall efficiency, enhances product quality, and supports sustainable production practices.Conclusion:The introduction of the groundbreaking Casting Gating System has ushered in a new era for the manufacturing industry. Combining sophisticated technology with superior design, this innovative system significantly enhances casting processes, ensuring optimal efficiency, exceptional product quality, and sustainable manufacturing practices. Manufacturers across various sectors can now reimagine their production capabilities, elevate their output, and cement their position as leaders in the global marketplace.By embracing the Casting Gating System, companies can stay ahead of the competition, satisfy customer demands, and ultimately contribute to the progress of the manufacturing industry as a whole.
Discover the Benefits of Rapid CNC Machining for Quality Results
Title: Leading CNC Machining Service Provider Offers Precision and Efficiency to Industrial Clients Introduction: In the dynamic world of industrial manufacturing, precision and efficiency are key factors that can make or break a company's success. Recognizing this, Rapid CNC Machining (brand name removed), a leading CNC machining service provider, has emerged as a reliable partner for industrial clients seeking high-quality and precise manufacturing solutions. With a commitment to cutting-edge technology, exceptional customer service, and seamless project management, Rapid CNC Machining continues to strengthen its position as a trusted name in the industry.Body:1. Company Overview and Expertise:Established in the heart of the manufacturing hub, Rapid CNC Machining has a proven track record of delivering precision-machined parts and components to a wide array of industries. The company's state-of-the-art facility houses an extensive range of CNC machines, allowing them to cater to diverse manufacturing needs. Their team of highly skilled technicians, engineers, and project managers ensure that each project is executed with utmost precision and efficiency.2. Technological Advancements:Rapid CNC Machining has stayed ahead of the competition by consistently investing in the latest CNC machining technology. The company's cutting-edge equipment enables them to provide comprehensive solutions, including design assistance, prototyping, custom part production, and mass production. By utilizing advanced software and tools, Rapid CNC Machining optimizes the manufacturing process, reducing lead times and maximizing product quality.3. Diverse Industry Applications:With an extensive portfolio of successful projects, Rapid CNC Machining serves various industries, including aerospace, automotive, medical, electronics, and more. Their expertise in machining a wide range of materials, including aluminum, stainless steel, titanium, plastics, and composites, enables them to meet the unique requirements of each industry. Whether it is complex aerospace components or intricate medical device parts, Rapid CNC Machining ensures the highest standards of accuracy, functionality, and durability.4. Commitment to Quality Assurance:Rapid CNC Machining places great emphasis on quality assurance throughout the manufacturing process. From initial design analysis to final inspection, the company employs rigorous quality control measures to guarantee adherence to specifications and customer expectations. Their ISO 9001-certified facility ensures consistent quality and compliance with industry standards, earning them a reputation for excellence.5. Customer-Centric Approach:Understanding the importance of strong customer relationships, Rapid CNC Machining prioritizes open communication and collaboration with clients. Their skilled project management team ensures seamless coordination, from project initiation to product delivery. With a commitment to transparency, Rapid CNC Machining provides regular progress updates, addresses any concerns promptly, and maintains strict confidentiality protocols.6. Sustainable Manufacturing Practices:In an era of growing environmental consciousness, Rapid CNC Machining strives to implement sustainable manufacturing practices. By optimizing material utilization, reducing waste, and utilizing energy-efficient machinery, the company minimizes its environmental footprint. Moreover, investing in research and development, Rapid CNC Machining actively explores greener alternatives, ensuring its manufacturing processes are aligned with sustainability goals.7. Global Reach and Future Outlook:Rapid CNC Machining has established a global footprint by serving clients from various countries and regions. Their commitment to delivering exceptional value and their strong reputation for reliable service has positioned them as a preferred CNC machining partner worldwide. As the company continues to expand its capabilities, invest in technology, and nurture customer relationships, Rapid CNC Machining aims to remain at the forefront of the industry.Conclusion:Through consistent innovation, dedication to customer satisfaction, and a focus on precision and efficiency, Rapid CNC Machining has solidified its position as a leading provider of CNC machining services. Their state-of-the-art facility, diverse industry applications, and commitment to sustainable practices set them apart from competitors. As industrial manufacturing continues to evolve, the company's unwavering commitment to quality and customer-centricity ensures they will remain a trusted partner for businesses seeking superior CNC machining solutions.
Understanding the Steps Involved in the Milling Process
[Company Name] Revolutionizes the Milling Process, Enhancing Efficiency and Quality[City, Date] - [Company Name], a leading innovator in the manufacturing industry, is making waves with its revolutionary milling process. By incorporating cutting-edge technology and advanced techniques, the company has accomplished remarkable improvements in efficiency and quality, setting new industry standards.The milling process is a crucial step in the manufacturing of various products, ranging from automotive components to consumer electronics. Traditionally, this process involves removing material from a workpiece using a rotating cutting tool. However, [Company Name] has taken this fundamental concept to new heights.With a focus on innovation, [Company Name] has developed a state-of-the-art milling process that surpasses traditional methods in terms of speed and precision. By leveraging advanced computer algorithms and artificial intelligence, the company has optimized the milling parameters to ensure the perfect balance between material removal and preservation.One key aspect of [Company Name]'s milling process is the integration of advanced sensors and monitoring systems. These sensors provide real-time feedback on crucial variables such as cutting forces, temperatures, and tool wear. By constantly monitoring these parameters, [Company Name] can make precise adjustments to the milling process, ensuring optimal performance and preventing any potential faults or errors.Additionally, [Company Name] has pioneered an intelligent tooling system that further enhances the efficiency of the milling process. This system utilizes smart tools equipped with sensors to continuously collect data during the machining operation. This data is then analyzed by sophisticated algorithms, allowing for predictive maintenance and precise tool life management. As a result, downtime due to unexpected tool failures is significantly reduced, leading to increased productivity and cost savings.Furthermore, [Company Name] has prioritized sustainability in its milling process. By implementing eco-friendly cutting fluids and optimizing the chip evacuation process, the company has minimized waste and reduced environmental impact. This commitment to sustainability aligns with [Company Name]'s corporate values and resonates with environmentally conscious clients.In terms of quality control, [Company Name] has introduced advanced inspection systems that guarantee the highest level of precision and accuracy. Through the utilization of non-contact measurement technologies, such as laser scanners and optical systems, the company can perform detailed inspections on complex components, ensuring conformity to the tightest tolerances.Customer satisfaction is paramount for [Company Name], and as such, the company provides comprehensive support throughout the milling process. Their team of highly skilled engineers assists clients in selecting the appropriate milling strategies and tools for their specific needs. Additionally, [Company Name] offers training programs and workshops to ensure that operators are well-equipped to utilize the milling process to its full potential.The impact of [Company Name]'s milling process is already being felt across a wide range of industries. Customers have praised the enhanced productivity, improved part quality, and reduced lead times resulting from the adoption of this innovative technology. Numerous companies have reported significant cost savings and increased competitiveness as a direct result of partnering with [Company Name].Looking towards the future, [Company Name] remains committed to pushing the boundaries of milling technology. Through ongoing research and development efforts, the company strives to introduce even more advanced milling techniques that will revolutionize the manufacturing industry once again.In conclusion, [Company Name]'s revolutionary milling process has transformed traditional machining into a high-tech, efficient, and sustainable practice. By seamlessly integrating cutting-edge technology and advanced techniques, the company has set a new industry standard for milling, driving productivity, quality, and cost-effectiveness to unparalleled heights.