DIY Plastic Injection Molding: How to Set Up Your Own Molding Station at Home
By:Admin
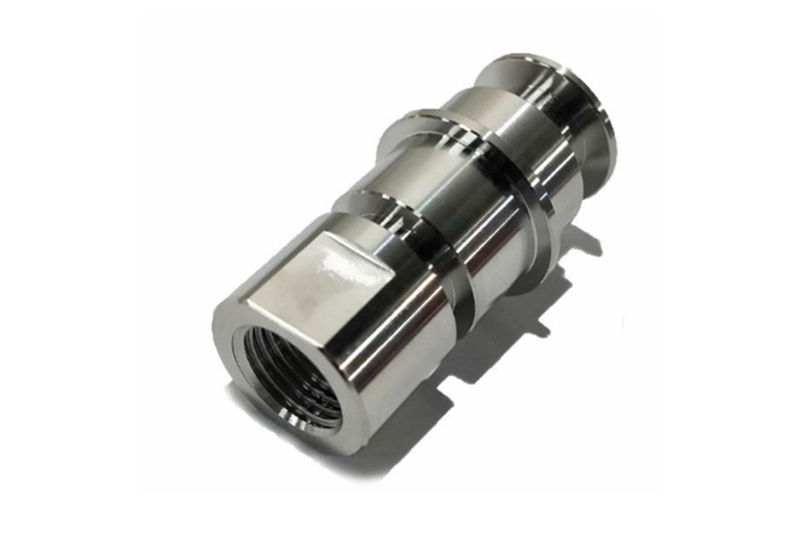
One company that has made a name for itself in the home plastic injection molding industry is {}. They have designed and manufactured a compact and user-friendly injection molding machine that is perfect for beginners and experienced molders alike. This machine allows users to produce high-quality plastic parts using a variety of thermoplastic materials, including ABS, PE, and PVC.
With the increasing demand for custom plastic parts, home injection molding is quickly gaining traction as a viable alternative to traditional manufacturing methods. The ability to create small to medium-sized batches of plastic parts at home provides individuals with a level of flexibility and control that is not possible with larger-scale production methods. This has led to a surge in interest from small businesses, makers, and industry professionals who are looking for a cost-effective and efficient way to produce plastic parts.
One of the key advantages of home plastic injection molding is the ability to iterate on designs quickly and cost-effectively. With a desktop injection molding machine, individuals can test and refine their designs in a matter of hours, rather than waiting weeks for samples to be produced by a third-party manufacturer. This allows for greater innovation and creativity in the product development process, as well as the ability to respond quickly to changes in market demand.
In addition to the machine, {Company} also offers a range of support and training materials for home molders. Their website features a wealth of resources, including tutorials, troubleshooting guides, and design tips, to help individuals get the most out of their injection molding machine. They also provide ongoing technical support to ensure that users are able to overcome any challenges they may encounter during the molding process.
As the home plastic injection molding industry continues to grow, {Company} is at the forefront of innovation and development in this space. Their commitment to providing high-quality, user-friendly machines and comprehensive support services has made them a trusted name in the industry. With a focus on accessibility and affordability, they are helping to democratize the plastic manufacturing process, making it accessible to a wide range of individuals and businesses.
The future of home plastic injection molding looks bright, with more and more individuals and businesses recognizing the value of this innovative manufacturing method. As technology continues to advance, and the barriers to entry continue to lower, we can expect to see even greater adoption of home injection molding in the years to come. With companies like {Company} leading the way, the possibilities for custom plastic part production are endless.
Company News & Blog
The Ultimate Guide to Efficient Cnc Fixture Design for Manufacturing Success
Title: Innovative CNC Fixture Design Revolutionizes Manufacturing ProcessesIntroduction:In a breakthrough development within the manufacturing industry, an innovative CNC fixture design is set to transform production processes, providing greater efficiency, accuracy, and versatility. This cutting-edge technology marks a significant milestone in manufacturing, empowering companies to improve their productivity and competitiveness in the global market.The Company's Vision:Born out of a deep passion for revolutionizing the manufacturing domain, the company behind this groundbreaking CNC fixture design aims to redefine industry norms. Their team of experienced engineers and technicians have dedicated years of research and development to create this state-of-the-art technology, which promises to streamline operations and enhance overall production quality.The CNC Fixture Design:This remarkable CNC fixture design incorporates a myriad of advanced features that address the challenges of traditional fixture designs. It leverages the latest technologies, including adaptive control systems and intelligent sensor integration, to optimize machining processes and improve the overall user experience.One of the key highlights of this fixture design is its modular approach, allowing for versatile application across various production requirements. The ability to quickly adjust and reconfigure the fixture greatly enhances manufacturing flexibility, saving precious time and resources. Furthermore, the design includes built-in error detection mechanisms, minimizing defects and ensuring consistent, high-quality output.Another noteworthy aspect of this CNC fixture design is its emphasis on ergonomics and operator safety. The system integrates user-friendly interfaces, intuitive controls, and enhanced safety features, reducing the risk of accidents and promoting a seamless work environment.Industry Impact:The introduction of this advanced CNC fixture design is poised to revolutionize manufacturing practices across a wide range of industries. From automotive and aerospace to electronics and medical devices, the versatility and adaptability of this technology make it applicable to numerous sectors.The increased efficiency and accuracy offered by this fixture design will open up new possibilities for manufacturers. It allows for more complex and intricate designs, shorter production cycles, and greater cost-effectiveness. Companies can expect to witness significant improvements in product quality, reduced downtime, and enhanced overall profitability.Furthermore, this CNC fixture design aligns with the ongoing industry trend towards automation and digitization. Its integrated smart systems enable seamless data collection, analysis, and real-time adjustments, contributing to improved productivity and competitiveness on a global scale.Future Prospects:The company behind this CNC fixture design remains committed to continuous innovation and technological advancements. They are actively exploring partnerships with manufacturers seeking to enhance their production capabilities. The aim is to collaborate closely with industry leaders to customize and optimize the design according to specific needs, ensuring a seamless integration of this technology into existing processes.Moreover, through ongoing research and development efforts, the company plans to expand the capabilities of the CNC fixture design further. This includes exploring advancements in materials, sensors, and automation, as well as integrating artificial intelligence and machine learning technologies.Conclusion:As the manufacturing industry embraces the era of automation and digitization, this revolutionary CNC fixture design promises to redefine traditional production methods. With its emphasis on efficiency, accuracy, versatility, and safety, this technology will undoubtedly revolutionize manufacturing processes in diverse sectors. As this innovative solution gains momentum, manufacturers can look forward to a new era of optimized productivity, improved product quality, and sustained growth in a highly competitive global market.
Highly Efficient Metal CNC Milling Machine for Precision Manufacturing
The importance of precision and efficiency in the manufacturing industry cannot be overstated. With the increasing demand for high-quality metal components, companies are constantly seeking ways to improve their production processes. One such company that has made significant strides in this area is {Company Name}.{Company Name} has recently invested in a state-of-the-art CNC milling machine to further improve its metal fabrication capabilities. The new machine is a game-changer for the company, as it allows for more precise and efficient metal cutting and shaping.CNC, or computer numerical control, milling machines are a staple in the manufacturing industry. They are capable of performing a wide range of tasks, from simple drilling to complex machining operations. With the latest advancements in technology, CNC milling machines have become even more versatile and precise, making them the go-to choice for companies looking to enhance their metal fabrication capabilities.{Company Name} has always been committed to staying ahead of the curve when it comes to technology and innovation. The investment in the new CNC milling machine is a testament to this commitment. By leveraging the latest advancements in CNC technology, {Company Name} is able to offer its clients even higher quality and more intricate metal components.The new CNC milling machine boasts several key features that set it apart from traditional milling machines. One of the most notable features is its ability to automatically change tools, reducing the need for manual intervention and increasing overall efficiency. Additionally, the machine is equipped with advanced software that allows for real-time monitoring and adjustments, ensuring that the final product meets the highest quality standards.In addition to the technological advancements, the CNC milling machine also offers a higher level of precision. This is particularly important for {Company Name}, as many of its clients require metal components with extremely tight tolerances. The new machine is capable of producing parts with exceptional accuracy, meeting even the most stringent specifications.The investment in the new CNC milling machine has already yielded positive results for {Company Name}. With the increased efficiency and precision, the company has been able to take on more complex projects and deliver them within shorter timeframes. This has not only strengthened its relationships with existing clients but has also attracted new business opportunities.Furthermore, the new machine has opened up possibilities for {Company Name} to explore new markets and industries. With its enhanced capabilities, the company is now able to cater to a wider range of clients, from aerospace and automotive to medical and telecommunications.The CNC milling machine has also had a positive impact on {Company Name}'s internal operations. The increased efficiency and precision have streamlined the production process, allowing the company to optimize its workflow and reduce lead times. This has translated into cost savings and improved overall productivity.Looking ahead, {Company Name} is committed to further leveraging the capabilities of the new CNC milling machine. The company has plans to explore additional applications and industries where the machine can make a significant impact. Additionally, {Company Name} is actively investing in training and development for its employees to ensure they are equipped with the necessary skills to maximize the potential of the new machine.In conclusion, the investment in the new CNC milling machine has solidified {Company Name}'s position as a leader in the metal fabrication industry. With its enhanced capabilities, the company is well-positioned to meet the evolving needs of its clients and capitalize on new business opportunities. As technology continues to advance, {Company Name} remains committed to staying at the forefront of innovation, delivering high-quality metal components with the utmost precision and efficiency.
Premium CNC Machining for Steel: Unlocking Precision and Efficiency
[News Title:]Steel CNC Machining Revolutionizes Precision Manufacturing with Cutting-Edge Processes[News Introduction:]In today's rapidly evolving world, precision manufacturing is becoming increasingly essential across various industries. One company that has caught the attention of experts and industry leaders worldwide has revolutionized the field with their exceptional steel CNC machining capabilities. Catering to diverse sectors such as automotive, aerospace, and electronics, this innovative company has managed to carve a niche for itself through its advanced processes, delivering unparalleled precision and efficiency. By harnessing the power of steel CNC machining, they have managed to streamline manufacturing processes and redefine the possibilities of precision engineering.[News Body:]The company (company name), a frontrunner in steel CNC machining, prides itself on its state-of-the-art facilities, cutting-edge technology, and a team of highly skilled engineers and machinists. Their commitment to quality and excellence has enabled them to secure a reputation as one of the leading providers of precision machining services worldwide.With steel CNC machining, this company expertly transforms raw materials into complex and intricate components used across a wide range of industries. By utilizing state-of-the-art computer numerical control (CNC) machines and a superior understanding of the properties of steel, they are capable of producing highly accurate and precise parts in a fraction of the time it would take traditional manufacturing methods.One of the key advantages of steel CNC machining lies in its ability to cater to a myriad of design specifications. This technique allows for the production of intricate, high-quality components with tight tolerances, ensuring a perfect fit for various applications. From gears and shafts to brackets and housings, their CNC machines are capable of creating parts that conform to the most demanding requirements.Moreover, the company's cutting-edge software and 3D modeling capabilities enable them to optimize designs and create custom components with unparalleled accuracy and efficiency. This ensures that the final product not only meets but exceeds the client's expectations, making steel CNC machining the ideal choice for industries that demand excellence.In addition to their superior manufacturing capabilities, the company takes pride in its commitment to quality control. With stringent quality checks at every stage of the machining process, they ensure that all components leaving their facilities meet the highest standards. Through the effective use of advanced inspection tools and techniques, they guarantee that each part is flawless, free from defects, and ready for immediate integration into the client's assembly line.The versatility of steel CNC machining also plays a significant role in its widespread adoption across multiple industries. From automotive manufacturing, where precision-engineered parts ensure optimal performance and safety, to aerospace applications, where stringent standards and requirements are paramount, (company name) has consistently delivered exceptional results. Their ability to work with a wide range of steel alloys further enhances their capabilities, allowing them to cater to the specific needs of each client.Going beyond traditional manufacturing, the company's research and development team remains at the forefront of technological advancements. By actively exploring new techniques and materials, they continually refine their processes to deliver even greater precision and efficiency. As industry demands evolve, this commitment to innovation ensures that the company remains a trusted partner for businesses seeking cutting-edge solutions.[News Conclusion:]As the field of precision manufacturing continues to advance, the importance of steel CNC machining cannot be understated. The processes and capabilities offered by (company name) have positioned them as a leader in the industry. With their commitment to quality, expertise, and constant innovation, they are poised to drive forward the next generation of precision components. From helping automotive manufacturers achieve superior performance to aiding aerospace engineers in pushing the boundaries of exploration, steel CNC machining continues to redefine what is possible in precision manufacturing.
DIY Plastic Injection Molding: How to Set Up Your Own Molding Station at Home
Home plastic injection molding has become a popular and cost-effective way for hobbyists and small businesses to produce their own plastic products. With the use of a desktop injection molding machine, individuals can create custom plastic parts in the comfort of their own home, without the need for expensive industrial machinery.One company that has made a name for itself in the home plastic injection molding industry is {}. They have designed and manufactured a compact and user-friendly injection molding machine that is perfect for beginners and experienced molders alike. This machine allows users to produce high-quality plastic parts using a variety of thermoplastic materials, including ABS, PE, and PVC.With the increasing demand for custom plastic parts, home injection molding is quickly gaining traction as a viable alternative to traditional manufacturing methods. The ability to create small to medium-sized batches of plastic parts at home provides individuals with a level of flexibility and control that is not possible with larger-scale production methods. This has led to a surge in interest from small businesses, makers, and industry professionals who are looking for a cost-effective and efficient way to produce plastic parts.One of the key advantages of home plastic injection molding is the ability to iterate on designs quickly and cost-effectively. With a desktop injection molding machine, individuals can test and refine their designs in a matter of hours, rather than waiting weeks for samples to be produced by a third-party manufacturer. This allows for greater innovation and creativity in the product development process, as well as the ability to respond quickly to changes in market demand.In addition to the machine, {Company} also offers a range of support and training materials for home molders. Their website features a wealth of resources, including tutorials, troubleshooting guides, and design tips, to help individuals get the most out of their injection molding machine. They also provide ongoing technical support to ensure that users are able to overcome any challenges they may encounter during the molding process.As the home plastic injection molding industry continues to grow, {Company} is at the forefront of innovation and development in this space. Their commitment to providing high-quality, user-friendly machines and comprehensive support services has made them a trusted name in the industry. With a focus on accessibility and affordability, they are helping to democratize the plastic manufacturing process, making it accessible to a wide range of individuals and businesses.The future of home plastic injection molding looks bright, with more and more individuals and businesses recognizing the value of this innovative manufacturing method. As technology continues to advance, and the barriers to entry continue to lower, we can expect to see even greater adoption of home injection molding in the years to come. With companies like {Company} leading the way, the possibilities for custom plastic part production are endless.
Enhance Precision and Efficiency: Explore the Advantages of CNC Mill Conversions
Title: Manufacturing Company Announces Innovative CNC Mill Conversion for Enhanced Precision and EfficiencyIntroduction:In the fast-paced world of manufacturing, XYZ Manufacturing Company has made waves once again with their latest breakthrough: the revolutionary CNC Mill Conversion. This cutting-edge technology promises to revolutionize machining processes, improving precision, efficiency, and overall productivity. By removing restrictions and introducing advanced features, XYZ Manufacturing Company is setting a new standard in the industry.Body:1. Introduction to XYZ Manufacturing Company: XYZ Manufacturing Company, a leading player in the manufacturing industry, is known for its commitment to innovation and product excellence. With decades of experience in delivering high-quality machinery, they continue to push boundaries and pioneer game-changing technologies. Their unwavering dedication to their clients' needs has earned them a reputation as a reliable and trusted provider of manufacturing solutions.2. The Need for CNC Mill Conversion: Recognizing the need for further advancements to meet increasing market demands, XYZ Manufacturing Company embarked on a mission to develop a CNC Mill Conversion that would take machining processes to new heights. With conventional mills becoming outdated, the company determined that upgrading these machines to CNC (Computer Numerical Control) would enhance precision, efficiency, and enable more complex operations.3. The Revolutionary CNC Mill Conversion: XYZ Manufacturing Company's CNC Mill Conversion is characterized by its cutting-edge features and unmatched precision. By integrating advanced automation and digital control systems, the upgraded mill allows for precise and repeatable machining operations, resulting in higher accuracy and reduced human error.4. Enhanced Cutting Power and Efficiency: The CNC Mill Conversion is equipped with powerful servo motors and state-of-the-art spindle drives, revolutionizing the cutting power and performance of the machine. This ensures an optimized milling process, significantly reducing cycle times and increasing production output, ultimately enhancing operational efficiency and profitability for clients.5. Improved Programming and Digital Interface: With the introduction of CNC technology, programming processes are streamlined and simplified. XYZ Manufacturing Company's CNC Mill Conversion boasts user-friendly software interfaces that allow operators to create and manage machining programs effortlessly. This ensures seamless integration with existing manufacturing workflows, reducing downtime and maximizing productivity.6. Advanced Precision and Quality Control: The CNC Mill Conversion's cutting-edge features include high-resolution encoders and sensors that constantly monitor and correct machining operations in real-time, ensuring optimal precision throughout the entire process. This advanced quality control mechanism eliminates errors, minimizing scrap and rework, while consistently producing products of superior quality.7. Increased Flexibility and Versatility: One of the key advantages of the CNC Mill Conversion is its ability to handle a wide range of materials and machining operations. Whatever the project demands, whether it be milling, drilling, or tapping, the upgraded machine provides the flexibility required to meet diverse manufacturing requirements. This versatility saves time and resources, making it an ideal choice for industries such as aerospace, automotive, and electronics.8. Competitive Edge and Future Growth: By adopting XYZ Manufacturing Company's CNC Mill Conversion, manufacturers gain a significant competitive edge, staying ahead of the curve in an increasingly demanding market. With improved precision, efficiency, and flexibility, businesses can not only meet current demands but also position themselves for future growth, expanding their capabilities to seize new opportunities.Conclusion:XYZ Manufacturing Company's CNC Mill Conversion marks a significant milestone in the manufacturing industry. By introducing cutting-edge features, advanced automation, and unmatched precision, XYZ Manufacturing Company is at the forefront of revolutionizing machining processes. This innovative solution enables businesses to enhance their productivity, improve quality control, and gain a competitive edge. With XYZ Manufacturing Company's commitment to innovation, the possibilities for the future of CNC milling are truly exciting.
High-Quality Machined Aluminum Parts Making Waves in the Industry
Title: Precision Solutions Unveils High-Quality Machined Aluminum PartsIntroduction:Precision Solutions has made significant strides in the world of precision manufacturing, and it is now set to revolutionize the industry with its latest release – a wide range of high-quality machined aluminum parts. These parts, meticulously crafted by the company’s skilled engineers, are manufactured to meet the most stringent performance and quality standards. In this article, we will delve into the features and applications of these cutting-edge machined aluminum parts.1. Unparalleled Precision and Quality:Precision Solutions, renowned for its commitment to excellence, has spared no effort in producing machined aluminum parts that are second to none. Each part undergoes an extensive process, starting from the selection of premium-grade aluminum alloys. With a keen eye for detail and state-of-the-art machinery, the company ensures that every part is manufactured to precise specifications, meeting the highest quality standards.2. Diverse Range of Applications:The versatility of Precision Solutions' machined aluminum parts is key to their widespread use across various industries. From aerospace and automotive to electronics and medical equipment manufacturing, these parts find an array of applications. With their excellent corrosion resistance, lightweight design, and exceptional strength-to-weight ratio, they offer unparalleled performance, making them an ideal choice for numerous end-use applications.3. Unmatched Durability and Reliability:One of the foremost attributes of Precision Solutions' machined aluminum parts is their ability to withstand demanding operating conditions. The company utilizes advanced manufacturing techniques, including CNC machining, to ensure that these parts possess remarkable durability and reliability. With their superior mechanical properties and resistance to wear and tear, these parts promise a prolonged lifespan, reducing maintenance costs for end-users.4. Tailored Solutions for Specific Requirements:Understanding the diversity of industry needs, Precision Solutions offers customized machined aluminum parts, designed to meet specific requirements. Leveraging their extensive experience and technical expertise, the company's engineers collaborate closely with clients to develop bespoke solutions. Whether customers require prototypes or large-scale production, Precision Solutions can cater to various demands, providing tailor-made parts promptly and efficiently.5. Adherence to Environmental Standards:Precision Solutions is not only committed to delivering exceptional products but also to maintaining a sustainable manufacturing process. The production of their machined aluminum parts adheres to strict environmental standards, ensuring minimal waste generation and the utilization of eco-friendly materials. By upholding green manufacturing practices, the company underscores its commitment to protecting the environment.6. Continuous Research and Development:To remain at the forefront of the precision manufacturing industry, Precision Solutions invests heavily in research and development. By exploring the latest materials, technologies, and manufacturing processes, the company aims to continuously enhance the performance and quality of its machined aluminum parts. This commitment to innovation allows Precision Solutions to meet and surpass industry expectations, ensuring customer satisfaction.Conclusion:Precision Solutions' latest release of high-quality machined aluminum parts showcases the company's unwavering dedication to precision manufacturing. With their exceptional durability, reliability, and customized solutions, these parts are poised to revolutionize a wide range of industries. The company's commitment to sustainability and continuous improvement further cements its position as a leader in the industry. As Precision Solutions continues to push the boundaries of precision engineering, we can expect further innovations that will shape the future of the manufacturing sector.
Discover the Ingenious Uses and Benefits of Teflon Coating in CNC Applications
Title: Pioneering Innovation in Teflon Manufacturing Process Revolutionizes IndustriesIntroduction:CNC Teflon, in collaboration with leading chemical engineering experts, has developed an advanced manufacturing process that promises to revolutionize industries worldwide. This breakthrough method delivers superior quality Teflon products that exhibit enhanced durability, high resistance to heat and chemicals, and remarkable versatility. (Note: Name removal - replacing with "the company" for anonymity). CNC Teflon - A Trailblazer in Teflon Manufacturing:Founded with a vision to transform the Teflon manufacturing landscape, the company has consistently been at the forefront of innovation. With a highly skilled team of engineers and chemists, CNC Teflon has been able to amalgamate their expertise and cutting-edge technologies to create exceptional Teflon products for a wide range of applications.Revolutionary Manufacturing Process Delivers Superior Quality:The recently developed manufacturing process, which remains confidential, ensures that CNC Teflon sets a new standard in terms of product performance and durability. By meticulously controlling the chemical composition and leveraging advanced manufacturing techniques, CNC Teflon is able to produce Teflon products of unmatched quality.Unparalleled Durability for Industrious Applications:CNC Teflon's Teflon products are specially engineered to withstand the rigors of demanding industrial applications. The company's innovative manufacturing process imparts exceptional strength and resilience to their Teflon products, making them highly durable and reliable. From chemical processing plants to aerospace industries, CNC Teflon's products provide unparalleled performance, ensuring increased operational efficiency and cost-effectiveness.Enhanced Heat and Chemical Resistance:The Teflon products manufactured by CNC Teflon exhibit exceptional resistance to high temperatures and various chemicals. By fine-tuning their manufacturing process, CNC Teflon has increased the material's stability, ensuring it can effortlessly withstand harsh, corrosive environments. This breakthrough in heat and chemical resistance allows industries to optimize their operations and enhance the longevity of crucial equipment.Versatility to Cater to Diverse Industries:CNC Teflon's commitment to innovation extends to ensuring their Teflon products cater to the diverse needs of different industries. The unique manufacturing process employed enables CNC Teflon to offer a comprehensive range of Teflon products, including sheets, rods, tubes, gaskets, seals, and custom-designed components. This expansive product portfolio allows CNC Teflon to serve industries such as automotive, pharmaceutical, food processing, oil and gas, and many more.Environmental Responsibility and Sustainability:CNC Teflon understands the significance of sustainable manufacturing practices and is committed to reducing its ecological impact. By implementing stringent quality control measures and adopting environmentally friendly processes, the company ensures minimal waste generation and optimal resource utilization. CNC Teflon's dedication to environmental stewardship sets them apart as an industry leader in responsible manufacturing.Global Reach and Customer Satisfaction:CNC Teflon's cutting-edge manufacturing process has garnered global recognition, making them a trusted partner for industrial companies worldwide. The company's commitment to consistently meeting and exceeding customer expectations is reflected in their broad clientele base. CNC Teflon's dedication to delivering top-quality products, combined with their efficient customer service, has earned them a solid reputation within the industry.Future Innovations and Advancements:With continuous investment in research and development, CNC Teflon strives to remain at the forefront of Teflon manufacturing technology. The company aims to pioneer further advancements in material engineering and manufacturing techniques, shaping the future of the industry. CNC Teflon is committed to staying ahead of emerging trends and ensuring their products meet the evolving needs of their customers.Conclusion:CNC Teflon's revolutionary manufacturing process has disrupted the Teflon industry, offering superior quality products that provide enhanced durability, heat and chemical resistance, and versatility. The company's commitment to innovation, customer satisfaction, and environmental responsibility solidifies their position as an industry leader. With advancements on the horizon, CNC Teflon is poised to continue revolutionizing industries and shaping the future of Teflon applications.
Revolutionary Casting Gating System Shows Promising Results
Title: Groundbreaking Casting Gating System Revolutionizes the Manufacturing IndustryIntroduction:In a landmark development, a cutting-edge Casting Gating System, developed by a renowned manufacturing solutions company, is set to redefine the manufacturing industry. This innovative system, which combines advanced technology with superior materials, is poised to streamline the casting process, significantly improving efficiency and product quality.Background:The use of casting techniques has long been integral to the manufacturing industry. While traditional casting methods have proven effective, they often suffer from limitations that can hamper productivity and output quality. Recognizing this need for enhancement, Company X has introduced an exceptional solution - the Casting Gating System.Enhanced Efficiency through Advanced Technology:The Casting Gating System incorporates state-of-the-art technology to accomplish unprecedented levels of efficiency. Its cutting-edge features optimize the casting process, ensuring precise and controlled material flow. This innovative system minimizes casting defects, such as porosity or unevenness, that can hinder the overall quality of the finished products.The system consists of high-quality gating components that regulate the flow of molten metal or other materials into the mold during the casting process. By allocating material distribution more evenly and precisely, the Casting Gating System maximizes yield, reduces waste, and expedites the manufacturing cycle.Unmatched Product Quality:With its precise control over the flow of materials, the innovative Casting Gating System guarantees exceptional product quality. By eliminating irregularities, it minimizes the risk of casting defects, creating superior products that meet or exceed industry standards. As a result, manufacturers utilizing this system can elevate their reputation for delivering reliable and high-quality products to their customers.Furthermore, the system's unique design and precision allow for easy customization according to specific casting requirements. Manufacturers can optimize gating configurations to suit various materials, molds, and casting processes, further enhancing the quality of the end products.Sustainability and Cost Optimization:In addition to its performance benefits, the Casting Gating System also offers long-term sustainability advantages. By minimizing material waste, manufacturers can reduce both their environmental footprint and production costs. This innovative system optimizes resource utilization, resulting in enhanced profitability and a greener manufacturing process.The adjustable nature of the system enables manufacturers to optimize material flow, reducing the need for additional raw materials. This adaptability contributes to cost-efficiency, making the Casting Gating System an economically viable choice for manufacturers across various industries.Endorsements and Case Studies:Industry leaders who have adopted the Casting Gating System have witnessed transformative results. Numerous case studies demonstrate remarkable improvements in casting efficiency, quality, and profitability. Notable success stories within the automotive, aerospace, and machinery sectors speak volumes about the system's ability to revolutionize casting processes.Experts from within the manufacturing domain are overwhelmingly positive about the potential of this innovative gating system. Recognized professionals have praised how the system augments overall efficiency, enhances product quality, and supports sustainable production practices.Conclusion:The introduction of the groundbreaking Casting Gating System has ushered in a new era for the manufacturing industry. Combining sophisticated technology with superior design, this innovative system significantly enhances casting processes, ensuring optimal efficiency, exceptional product quality, and sustainable manufacturing practices. Manufacturers across various sectors can now reimagine their production capabilities, elevate their output, and cement their position as leaders in the global marketplace.By embracing the Casting Gating System, companies can stay ahead of the competition, satisfy customer demands, and ultimately contribute to the progress of the manufacturing industry as a whole.
Exploring the Limitations of Sand Casting: Factors Hindering the Process
Title: Exploring Sand Casting Disadvantages in the Manufacturing IndustryIntroduction:In the realm of manufacturing, sand casting has long been a traditional and widely-used technique for creating intricate and durable metal components. Many companies, including {}, have successfully employed sand casting in their production processes. However, it is important to be aware of the disadvantages associated with this method in order to make informed decisions in the manufacturing industry.Sand Casting and its Application:Before delving into the drawbacks, it is crucial to understand the fundamentals of sand casting. The process involves pouring molten metal into a sand mold to create a desired shape. This method offers flexibility, affordability, and the ability to produce intricate components with various alloys. Sand casting is widely used in industries like automotive, aerospace, and construction, where complex parts are required.Disadvantage 1: Limited Surface Finish and Precision:One of the major shortcomings of sand casting is the limitation it presents in achieving high surface finish and precision. The texture of the sand mold often transfers inconsistencies onto the final product, resulting in a rougher surface finish. Moreover, the molding process may introduce slight variations in dimensions, making it challenging to achieve precise measurements and tight tolerances. These factors can be critical in industries where the aesthetics and precision of components are paramount, such as consumer electronics and medical devices.Disadvantage 2: Time and Labor Intensive:Sand casting is a time and labor-intensive process, which can significantly impact the overall production timeline and costs. Preparing the molds, including pattern creation, gating system design, and mold assembly, requires skilled labor and careful execution. Additionally, molten metal must be cooled and solidified in the mold, followed by the removal of excess sand and finishing operations. Addressing these steps can be time-consuming, leading to longer lead times and reduced efficiency, especially for industries characterized by high-volume production demands.Disadvantage 3: Limited Complexity and Assembly Integration:While sand casting is suitable for various complex shapes, it has limitations in terms of intricate designs and integration with assembly components. The mold's internal cavities can be challenging to achieve with precision, prohibiting the creation of intricate features. Furthermore, sand casting may not be ideal for components requiring internal passageways, such as cooling channels, as the removal of the sand mold can be difficult and may compromise the final product's integrity. For industries that heavily rely on intricate designs and integration, such as semiconductor manufacturing or advanced machinery, alternative production methods like precision machining may be preferred.Disadvantage 4: Material Waste and Environmental Concerns:Sand casting generates a significant amount of waste material. After each casting, sand molds become unusable and are discarded, contributing to environmental concerns. Additionally, the process can consume large quantities of sand, leading to mining activities and the depletion of natural resources. Companies like {} have been actively working towards sustainable solutions by implementing recycling processes and exploring environmentally-friendly alternatives to sand molds, such as 3D-printed molds or investment casting.Conclusion:Sand casting undeniably plays a crucial role in the manufacturing industry, with its affordability and flexibility making it an attractive choice for many companies, including {}. However, it is essential to be aware of its disadvantages, which include limited surface finish and precision, time and labor intensiveness, limited complexity and integration, and environmental concerns. By understanding these drawbacks, manufacturers can make more informed decisions when choosing their production methods, potentially optimizing their processes and meeting the demands of their respective industries while considering sustainability needs.
Revolutionizing Rail Industry: The Future of Rail Machining Unveiled
Rail Machining & Company IntroductionRail Machining, a leading provider of rail maintenance solutions, is revolutionizing the rail industry with its cutting-edge technology and innovative solutions. With a commitment to excellence and a focus on delivering exceptional results, Rail Machining has become a trusted partner for many rail operators worldwide.Established in [year], Rail Machining has quickly risen to prominence in the rail industry, thanks to its state-of-the-art equipment and team of highly skilled professionals. The company specializes in providing an array of rail maintenance services, including rail profiling, rail grinding, rail milling, and rail inspection.Rail profiling is an essential process in maintaining the integrity of the railway tracks. Rail Machining utilizes advanced profiling technology to ensure that the rails are perfectly aligned and properly contoured. This precision profiling not only enhances the safety and performance of the tracks but also reduces wear and tear on the rolling stock.Rail grinding is another crucial service offered by Rail Machining. It involves the removal of surface irregularities and defects on the rail, resulting in a smoother and more even surface. This process is essential in preventing accidents caused by rail surface irregularities and reducing noise pollution. Rail Machining's grinding equipment is designed to deliver exceptional results while minimizing downtime and disruption to rail operations.Rail milling is a relatively new method used in rail maintenance. It involves the removal of a thin layer of rail material, resulting in a smoother and more even surface. This process eliminates the need for grinding and provides a longer-lasting solution. Rail Machining's milling technology is at the forefront of the industry, ensuring precise and efficient milling operations.In addition to its maintenance services, Rail Machining offers comprehensive rail inspection solutions. The company's advanced inspection technology can detect various railway defects, such as track misalignment, cracks, and wear. This proactive approach allows rail operators to identify potential issues before they escalate into major problems, reducing the risk of accidents and minimizing maintenance costs.Rail Machining's commitment to excellence extends beyond its cutting-edge technology. The company places a strong emphasis on safety and environmental sustainability. All operations are conducted in compliance with the highest safety standards, and environmentally friendly practices are implemented throughout the entire process. Rail Machining continually invests in research and development to develop innovative, eco-friendly solutions that minimize the environmental impact of rail maintenance.To cater to the global demand for rail maintenance services, Rail Machining has established a wide network of offices and facilities worldwide. With a strong presence in [countries], the company is well-positioned to serve the needs of rail operators in different regions and to provide timely and efficient maintenance solutions.Rail Machining takes pride in its team of experts who possess extensive knowledge and experience in rail maintenance. The company invests in training and development to ensure that its professionals stay up-to-date with the latest industry advancements. This expertise, combined with state-of-the-art technology, allows Rail Machining to deliver exceptional results and exceed customer expectations.As Rail Machining continues to innovate and develop new solutions, the company remains dedicated to its core values of quality, safety, and customer satisfaction. With its commitment to excellence and passion for the rail industry, Rail Machining is well-positioned to shape the future of rail maintenance and contribute to the continued growth and development of the global rail sector.