Different Types of Casting Methods and Their Applications
By:Admin
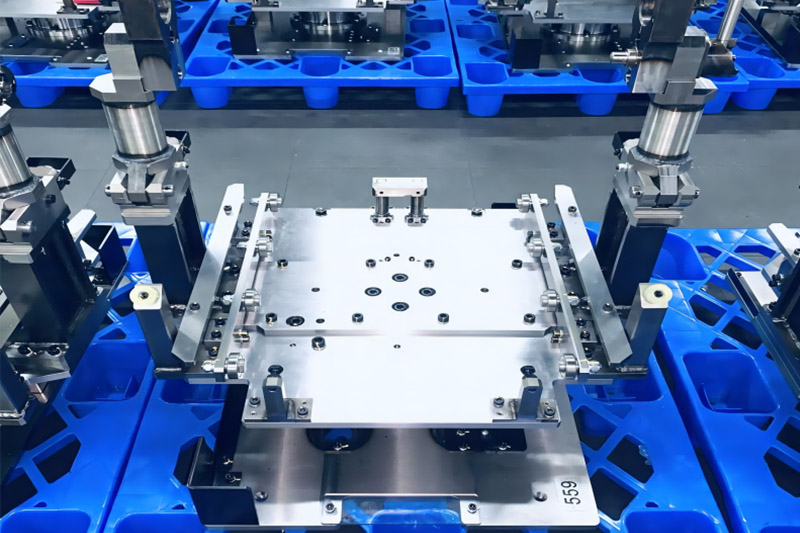
One company that has made significant strides in the field of casting methods is {}. Their dedication to pushing the boundaries of what is possible in casting technology has set them apart as a leader in the industry. With a focus on precision and innovation, {} has consistently delivered exceptional results for their clients, earning a reputation as a trusted partner in the manufacturing sector.
One of the key casting methods utilized by {} is investment casting. This intricate process involves creating a wax pattern of the part to be cast, coating it with a ceramic material, and then heating it to melt away the wax and leave a hollow ceramic mold. Molten metal is then poured into the mold, creating a precise and intricate metal part. This method is particularly well-suited for creating complex parts with fine details and tight tolerances.
In addition to investment casting, {} also specializes in sand casting, a more traditional method that involves creating a mold by compacting sand around a pattern of the part to be cast. This method is ideal for producing large, heavy parts in a cost-effective manner. By utilizing the latest technology and techniques, {} has been able to optimize the sand casting process to achieve exceptional results with minimal waste.
Another casting method that {} has perfected is die casting. This process involves injecting molten metal into a steel mold, known as a die, to create a specific shape. Die casting is ideal for producing high volumes of parts with excellent dimensional accuracy and surface finish. With their expertise in die casting, {} has been able to deliver a wide range of parts for various applications, from automotive components to electronic devices.
The introduction of 3D printing technology has also revolutionized the casting process, and {} has been at the forefront of this innovation. By utilizing 3D printing to create patterns and molds, {} has been able to streamline the casting process, reduce lead times, and minimize material waste. This cutting-edge approach has allowed {} to offer their clients a cost-effective solution for producing low-volume, highly complex parts.
In addition to their expertise in casting methods, {} also offers a full range of services to support their clients throughout the entire manufacturing process. From design and engineering support to finishing and assembly, {} is committed to providing comprehensive solutions that meet the unique needs of each project. Their dedication to quality and customer satisfaction has earned them a loyal client base and a reputation for excellence in the industry.
As the demand for high-quality, precision metal parts continues to grow, the importance of casting methods cannot be understated. Companies like {} are leading the way in innovation and setting new standards for excellence in the casting industry. With their expertise, advanced technology, and commitment to delivering exceptional results, {} is poised to remain a key player in the manufacturing sector for years to come.
Company News & Blog
5 Reasons Why Rail Machining is Essential for Maintenance and Safety
Rail Machining, a leading provider of rail maintenance and machining services, has been making great strides in the industry with its innovative solutions and exceptional customer service. With a focus on quality and efficiency, Rail Machining has become a trusted partner for railroads and transit systems across the country.The company, which was founded in XXXX, has a long history of excellence in the rail machining and maintenance industry. With a team of highly skilled technicians and engineers, Rail Machining has developed a reputation for delivering precision work and cost-effective solutions for its clients. From rail grinding and welding to track maintenance and inspection, Rail Machining offers a comprehensive range of services to keep railway systems running smoothly.One of the key factors that sets Rail Machining apart from its competitors is its commitment to innovation. The company has invested heavily in the latest technology and equipment, allowing it to offer cutting-edge solutions for even the most challenging projects. Whether it's repairing damaged tracks or optimizing rail profiles, Rail Machining has the expertise and resources to deliver top-quality results.In addition to its technical expertise, Rail Machining prides itself on its customer service. The company takes a proactive approach to understanding its clients' needs and requirements, working closely with them to develop tailored solutions that meet their specific challenges. This dedication to customer satisfaction has earned Rail Machining a loyal and expanding base of clients, who rely on the company for all their rail maintenance and machining needs.Rail Machining's reputation for excellence has not gone unnoticed in the industry. The company has been recognized with numerous awards and accolades for its outstanding performance and contributions to the rail sector. With a track record of success and a commitment to continuous improvement, Rail Machining continues to be a driving force in the rail maintenance and machining industry.Looking ahead, Rail Machining is poised for further growth and success. The company is constantly researching and investing in new technologies and techniques to enhance its service offerings and maintain its competitive edge. With a focus on sustainability and efficiency, Rail Machining is well positioned to meet the evolving needs of the rail industry and exceed the expectations of its clients.As Rail Machining continues to expand its reach and capabilities, it remains firmly committed to its core values of quality, innovation, and customer satisfaction. With a strong foundation and a clear vision for the future, Rail Machining is well positioned to lead the way in rail maintenance and machining for years to come.In conclusion, Rail Machining is a powerhouse in the rail maintenance and machining industry, with a proven track record of excellence and a commitment to innovation. With its unparalleled technical expertise and dedication to customer service, Rail Machining is the go-to partner for railroads and transit systems looking for top-quality solutions. As the company continues to grow and evolve, it is set to make an even greater impact on the rail industry, driving progress and delivering exceptional results for its clients.
What You Need to Know About Large CNC Machine Sizes
The demand for precision engineering and manufacturing continues to grow as industries seek to innovate and streamline production processes. In response to this demand, ** Company ** has announced the launch of their new CNC machine size, designed to meet the evolving needs of the industry.The new CNC machine size represents a significant step forward in the company's commitment to providing cutting-edge solutions for precision engineering and manufacturing. With a focus on versatility, efficiency, and accuracy, the CNC machine size offers a wide range of capabilities to meet the diverse needs of modern manufacturing operations.One of the key features of the new CNC machine size is its impressive accuracy and precision. Equipped with advanced technology and state-of-the-art controls, the machine is capable of producing intricate and complex parts with exceptional accuracy. This level of precision is essential for industries such as aerospace, automotive, and medical devices, where even the slightest deviation can have significant implications for performance and safety.In addition to its precision, the CNC machine size also offers a high level of versatility. Equipped with a range of tooling options and advanced programming capabilities, the machine is able to accommodate a wide variety of production needs. This flexibility is particularly valuable for manufacturers who need to adapt to changing demands and produce a diverse range of parts and components.Efficiency is another key focus of the new CNC machine size. With rapid tool change and high-speed machining capabilities, the machine is able to optimize production processes and minimize downtime. This not only improves productivity and throughput but also reduces operational costs, making it an attractive investment for manufacturers looking to enhance their competitive edge.The launch of the new CNC machine size reflects ** Company's ** commitment to innovation and continuous improvement. With a strong reputation for delivering high-quality precision engineering solutions, the company has a long history of meeting and exceeding the needs of its clients. The introduction of the new CNC machine size further strengthens ** Company's ** position as a leading provider of advanced manufacturing technology.In addition to its technical capabilities, ** Company ** is also known for its exceptional customer service and support. With a team of experienced engineers and technicians, the company is able to provide comprehensive training, installation, and ongoing maintenance to ensure that clients get the most out of their investment in the new CNC machine size. This level of support is crucial for manufacturers who rely on their equipment to deliver consistent and reliable performance.The launch of the new CNC machine size comes at a time when the demand for precision engineering and manufacturing solutions is higher than ever. With industries seeking to improve efficiency, reduce costs, and enhance quality, the new CNC machine size represents a valuable asset for manufacturers looking to stay ahead of the curve. As the industry continues to evolve, ** Company ** remains at the forefront of innovation, providing cutting-edge solutions to meet the changing needs of modern manufacturing.
Understanding the Steps Involved in the Milling Process
[Company Name] Revolutionizes the Milling Process, Enhancing Efficiency and Quality[City, Date] - [Company Name], a leading innovator in the manufacturing industry, is making waves with its revolutionary milling process. By incorporating cutting-edge technology and advanced techniques, the company has accomplished remarkable improvements in efficiency and quality, setting new industry standards.The milling process is a crucial step in the manufacturing of various products, ranging from automotive components to consumer electronics. Traditionally, this process involves removing material from a workpiece using a rotating cutting tool. However, [Company Name] has taken this fundamental concept to new heights.With a focus on innovation, [Company Name] has developed a state-of-the-art milling process that surpasses traditional methods in terms of speed and precision. By leveraging advanced computer algorithms and artificial intelligence, the company has optimized the milling parameters to ensure the perfect balance between material removal and preservation.One key aspect of [Company Name]'s milling process is the integration of advanced sensors and monitoring systems. These sensors provide real-time feedback on crucial variables such as cutting forces, temperatures, and tool wear. By constantly monitoring these parameters, [Company Name] can make precise adjustments to the milling process, ensuring optimal performance and preventing any potential faults or errors.Additionally, [Company Name] has pioneered an intelligent tooling system that further enhances the efficiency of the milling process. This system utilizes smart tools equipped with sensors to continuously collect data during the machining operation. This data is then analyzed by sophisticated algorithms, allowing for predictive maintenance and precise tool life management. As a result, downtime due to unexpected tool failures is significantly reduced, leading to increased productivity and cost savings.Furthermore, [Company Name] has prioritized sustainability in its milling process. By implementing eco-friendly cutting fluids and optimizing the chip evacuation process, the company has minimized waste and reduced environmental impact. This commitment to sustainability aligns with [Company Name]'s corporate values and resonates with environmentally conscious clients.In terms of quality control, [Company Name] has introduced advanced inspection systems that guarantee the highest level of precision and accuracy. Through the utilization of non-contact measurement technologies, such as laser scanners and optical systems, the company can perform detailed inspections on complex components, ensuring conformity to the tightest tolerances.Customer satisfaction is paramount for [Company Name], and as such, the company provides comprehensive support throughout the milling process. Their team of highly skilled engineers assists clients in selecting the appropriate milling strategies and tools for their specific needs. Additionally, [Company Name] offers training programs and workshops to ensure that operators are well-equipped to utilize the milling process to its full potential.The impact of [Company Name]'s milling process is already being felt across a wide range of industries. Customers have praised the enhanced productivity, improved part quality, and reduced lead times resulting from the adoption of this innovative technology. Numerous companies have reported significant cost savings and increased competitiveness as a direct result of partnering with [Company Name].Looking towards the future, [Company Name] remains committed to pushing the boundaries of milling technology. Through ongoing research and development efforts, the company strives to introduce even more advanced milling techniques that will revolutionize the manufacturing industry once again.In conclusion, [Company Name]'s revolutionary milling process has transformed traditional machining into a high-tech, efficient, and sustainable practice. By seamlessly integrating cutting-edge technology and advanced techniques, the company has set a new industry standard for milling, driving productivity, quality, and cost-effectiveness to unparalleled heights.
Top Quality Injection Molding Parts for Your Business
Injection Molding Parts Sees Significant Growth in {}'s BusinessWith the increasing demand for high-quality injection molding parts, {} has experienced significant growth in its business in recent years. As a leading provider of injection molding parts, {} has been able to create a niche for itself in the industry by offering top-notch products and exceptional customer service.{} has been in the injection molding industry for over a decade and has established itself as a reliable and trusted supplier of high-quality parts for various industries. The company's commitment to excellence and innovation has enabled it to stay ahead of the competition and meet the diverse needs of its customers.The injection molding process involves the use of molten materials, typically plastic, to create various components and parts for a wide range of applications. {} has invested heavily in advanced machinery and technology to ensure that it can produce parts that meet the highest standards of quality and precision. The company's manufacturing facilities are equipped with state-of-the-art injection molding machines and automated production lines, allowing it to deliver consistent and reliable results.One of the key factors that have contributed to {}'s success in the injection molding industry is its team of skilled engineers and technicians. The company's staff is highly knowledgeable and experienced in the injection molding process, enabling them to develop innovative solutions and produce complex parts with tight tolerances. {}'s team is dedicated to providing customized solutions to its customers, ensuring that their specific requirements are met with precision and efficiency.In addition to its technical expertise, {} also places a strong emphasis on customer service and satisfaction. The company prides itself on building long-term relationships with its clients, understanding their unique needs, and delivering tailored solutions that exceed their expectations. {}'s commitment to customer service has helped it build a loyal and satisfied customer base, driving its continued growth and success in the industry.{}'s injection molding parts are used in a wide range of applications, including automotive, electronics, consumer products, and medical devices. The company's ability to produce parts with complex geometries and tight tolerances has enabled it to serve diverse industries and cater to various production requirements. With a focus on continuous improvement and innovation, {} is constantly exploring new materials and techniques to expand its capabilities and offer cutting-edge solutions to its customers.As the demand for high-quality injection molding parts continues to grow, {} remains committed to investing in its people, technology, and processes to stay at the forefront of the industry. The company is dedicated to upholding the highest standards of quality and precision in its products, and it strives to be a reliable partner for its customers, offering them the solutions they need to succeed in their respective industries.In conclusion, {} has seen significant growth in its business as a leading provider of injection molding parts. With its focus on innovation, quality, and customer service, the company has been able to build a strong reputation and establish itself as a key player in the injection molding industry. As the demand for high-quality parts continues to rise, {} is well-positioned to meet the needs of its customers and drive continued success in the years to come.
DIY Plastic Injection Molding: How to Set Up Your Own Molding Station at Home
Home plastic injection molding has become a popular and cost-effective way for hobbyists and small businesses to produce their own plastic products. With the use of a desktop injection molding machine, individuals can create custom plastic parts in the comfort of their own home, without the need for expensive industrial machinery.One company that has made a name for itself in the home plastic injection molding industry is {}. They have designed and manufactured a compact and user-friendly injection molding machine that is perfect for beginners and experienced molders alike. This machine allows users to produce high-quality plastic parts using a variety of thermoplastic materials, including ABS, PE, and PVC.With the increasing demand for custom plastic parts, home injection molding is quickly gaining traction as a viable alternative to traditional manufacturing methods. The ability to create small to medium-sized batches of plastic parts at home provides individuals with a level of flexibility and control that is not possible with larger-scale production methods. This has led to a surge in interest from small businesses, makers, and industry professionals who are looking for a cost-effective and efficient way to produce plastic parts.One of the key advantages of home plastic injection molding is the ability to iterate on designs quickly and cost-effectively. With a desktop injection molding machine, individuals can test and refine their designs in a matter of hours, rather than waiting weeks for samples to be produced by a third-party manufacturer. This allows for greater innovation and creativity in the product development process, as well as the ability to respond quickly to changes in market demand.In addition to the machine, {Company} also offers a range of support and training materials for home molders. Their website features a wealth of resources, including tutorials, troubleshooting guides, and design tips, to help individuals get the most out of their injection molding machine. They also provide ongoing technical support to ensure that users are able to overcome any challenges they may encounter during the molding process.As the home plastic injection molding industry continues to grow, {Company} is at the forefront of innovation and development in this space. Their commitment to providing high-quality, user-friendly machines and comprehensive support services has made them a trusted name in the industry. With a focus on accessibility and affordability, they are helping to democratize the plastic manufacturing process, making it accessible to a wide range of individuals and businesses.The future of home plastic injection molding looks bright, with more and more individuals and businesses recognizing the value of this innovative manufacturing method. As technology continues to advance, and the barriers to entry continue to lower, we can expect to see even greater adoption of home injection molding in the years to come. With companies like {Company} leading the way, the possibilities for custom plastic part production are endless.
Enhancing Efficiency and Precision: The Ultimate Guide to Machining Fixture Design
Machining Fixture Design: Enhancing Precision and Efficiency in ManufacturingIn today's fast-paced manufacturing industry, precision and efficiency are paramount. Companies are constantly searching for ways to improve their production processes, reduce costs, and enhance product quality. One such solution that has gained significant attention is machining fixture design. By removing brand names, we can focus on the concept itself and explore how this innovative technology is revolutionizing manufacturing.Machining fixtures are specialized tools used to hold and position workpieces during machining operations. They ensure that the workpiece remains stable and secure, minimizing errors and maximizing productivity. By providing a rigid support structure, machining fixtures enable precision machining, resulting in accurate and consistent parts.With advancements in design and engineering, machining fixtures have evolved to cater to the unique requirements of various industries. Whether it is the automotive, aerospace, or electronics sectors, machining fixture design plays a vital role in optimizing the manufacturing process. By customizing the fixtures according to the specific needs of the product, companies can achieve greater flexibility and efficiency.One key factor contributing to the success of machining fixture design is computer-aided design (CAD) software. CAD allows engineers to create highly complex and detailed fixture designs, taking into account factors such as material properties, clamping forces, and geometric constraints. By simulating the machining process in a virtual environment, engineers can identify potential issues and make necessary adjustments before manufacturing the actual fixture. This not only saves time but also reduces the risk of errors, ensuring a seamless production process.Furthermore, the integration of CAD with computer-aided manufacturing (CAM) software allows for a streamlined transition from design to production. The CAM software generates machine instructions directly from the CAD model, enabling the efficient programming of machining operations. This integration promotes collaboration between design and production teams, resulting in better communication, reduced lead times, and improved overall efficiency.In addition to CAD and CAM, the use of advanced materials and technologies has revolutionized machining fixture design. Lightweight and high-strength materials, such as aluminum alloys and carbon fiber reinforced polymers, have replaced traditional materials like steel. These modern materials offer greater rigidity, reducing vibrations during the machining process and improving surface finish quality. Moreover, they contribute to the overall weight reduction of fixtures, making them more ergonomic and easier to handle.In line with the principles of Industry 4.0, machining fixture design has also embraced automation and robotics. Robotic machining fixtures are capable of performing complex tasks with high precision, reducing human errors and dependence. These fixtures can be programmed to adapt to different workpieces, further enhancing flexibility in production processes. By automating repetitive tasks, manufacturers can increase productivity, reduce costs, and improve worker safety.The company, known for its expertise in machining fixture design, has been at the forefront of these advancements. With a dedicated team of engineers and designers, they have consistently pushed the boundaries of innovation in manufacturing. By continually investing in research and development, the company has been able to develop cutting-edge solutions tailored to meet specific customer needs.From the automotive industry to aerospace and beyond, this company's machining fixtures have become synonymous with precision and efficiency. Their commitment to quality and customer satisfaction has made them a trusted partner for numerous manufacturers worldwide. Through their collaborations and partnerships, they aim to further optimize machining processes, driving the industry towards greater productivity and competitiveness.In conclusion, machining fixture design holds tremendous potential for the manufacturing industry. By leveraging the power of CAD, CAM, advanced materials, and automation, companies can enhance precision, improve efficiency, and reduce costs. As this technology continues to evolve, it is expected to play an increasingly integral role in the manufacturing landscape, enabling businesses to stay ahead in the competitive global market.
Understanding the Different Axis of CNC Milling: A Comprehensive Guide
CNC Milling Axis Revolutionizes Manufacturing ProcessesIn today's rapidly evolving world, technology continues to reshape industries, and the manufacturing sector is no exception. With the advent of Computer Numerical Control (CNC) machines, precision and efficiency in manufacturing have reached new heights. Among the various CNC machines available, CNC Milling Axis has emerged as a game-changer in this highly competitive field. Its cutting-edge capabilities and superior performance have revolutionized the manufacturing processes, empowering companies to achieve greater productivity and accuracy.CNC Milling Axis, developed by a leading innovator in the industry, has garnered widespread recognition for its exceptional quality and reliability. Riding on the cutting edge of technology, it has become the go-to choice for manufacturers across diverse sectors. The integrated software and hardware systems have been carefully designed to streamline operations and deliver outstanding results consistently. This has made CNC Milling Axis an indispensable tool for companies focused on maximizing production efficiency.One of the key advantages of CNC Milling Axis is the flexibility it offers in terms of both complex designs and materials. Whether it's prototyping or mass production, this machine possesses the capability to handle intricate shapes and structures with ease. With advanced software and precision engineering, manufacturers can now create customized components and parts efficiently, meeting the unique requirements of their clients.Another significant benefit of CNC Milling Axis is its exceptional accuracy. Traditional manufacturing processes often involve human errors, resulting in inconsistent product quality. However, with the precision and repeatability offered by CNC Milling Axis, manufacturers can ensure consistent and precise results every time. This not only reduces waste and rework but also enhances the overall quality of the end product.Furthermore, CNC Milling Axis enables manufacturers to optimize their production schedules and meet tight deadlines. Its cutting-edge technology allows for fast machining speeds while maintaining uncompromised quality. Companies can now achieve higher output and faster turnaround times, leading to improved customer satisfaction and increased profitability.In addition to efficiency and accuracy, CNC Milling Axis also prioritizes operator safety. The machine is equipped with advanced safety features that protect operators from potential hazards. As workplace safety becomes a crucial aspect of any manufacturing operation, the integration of these safety measures underscores the commitment of the company to providing a secure working environment.The company behind CNC Milling Axis has a rich legacy of innovation and technological advancement. With decades of experience, they have remained at the forefront of the industry, consistently exceeding customer expectations. Their commitment to research and development ensures that their products always incorporate the latest advancements, enabling manufacturers to stay ahead in a fiercely competitive market.To further enhance the customer experience, the company provides comprehensive support and after-sales service. This includes technical training, maintenance assistance, and software updates. The company's dedicated team of experts is always available to address any concerns or queries, ensuring that manufacturers get the most out of their CNC Milling Axis machine.Looking ahead, the future of manufacturing will undoubtedly be shaped by CNC Milling Axis and similar cutting-edge technologies. As industries continue to evolve and demands for sophisticated products increase, companies that embrace CNC Milling Axis will have a significant advantage. By aligning themselves with the latest advancements in manufacturing technology, they can streamline processes, enhance efficiency, and stay ahead in an ever-changing landscape.In conclusion, CNC Milling Axis is driving a new wave of innovation in the manufacturing sector. Its combination of precision, efficiency, and safety empowers manufacturers to achieve exceptional results while reducing costs. As the industry moves towards increased automation and digitization, CNC Milling Axis proves to be an invaluable asset, enabling companies to thrive in a competitive marketplace.
Advanced Rapid Molding Techniques and Innovations in Manufacturing
Rapid Molding, a leading provider of high-quality rapid prototyping and low-volume manufacturing services, has recently made waves in the industry with their cutting-edge technology and innovative solutions. With a strong focus on customer satisfaction and quality control, the company has become a trusted partner for businesses looking to bring their ideas to life.The company, which was founded in 2005, has quickly grown to become a prominent player in the rapid prototyping and manufacturing space. Their state-of-the-art facilities and advanced equipment allow them to deliver precision parts and components with short lead times, helping their clients to stay ahead of the competition and meet tight deadlines.Rapid Molding specializes in a wide range of manufacturing processes, including 3D printing, CNC machining, injection molding, and sheet metal fabrication. This diverse set of capabilities allows them to cater to a variety of industries, from automotive and aerospace to consumer electronics and medical devices. Their team of experienced engineers and technicians work closely with each client to understand their specific needs and provide customized solutions that meet or exceed their expectations.In addition to their superior manufacturing capabilities, Rapid Molding also prides itself on its commitment to quality. They have rigorous quality control procedures in place to ensure that every part they produce meets the highest standards. From material selection to final inspection, every step of the manufacturing process is carefully monitored to guarantee the integrity and performance of the finished product.Furthermore, the company is dedicated to continuous improvement and invests heavily in research and development to stay at the forefront of technological advancements. This forward-thinking approach has allowed Rapid Molding to consistently deliver breakthrough solutions and drive innovation in the industry.One of the key factors that sets Rapid Molding apart from its competitors is its emphasis on speed. The company understands the importance of fast turnaround times in today's fast-paced business environment, and they have optimized their processes to minimize lead times without compromising on quality. This agility and responsiveness have earned them a stellar reputation for reliability and efficiency among their clients.Moreover, Rapid Molding prioritizes customer satisfaction above all else. They place a strong emphasis on communication and transparency, and they work closely with their clients at every stage of the manufacturing process to ensure that their needs are met. This client-centric approach has resulted in long-term partnerships and a high rate of customer retention for the company.Looking ahead, Rapid Molding is poised for continued success and growth in the rapidly evolving manufacturing industry. They have ambitious plans to expand their capabilities and offerings, including the integration of new technologies and processes to further streamline their operations and meet the evolving needs of their clients. With their unwavering commitment to quality, speed, and customer satisfaction, Rapid Molding is well-positioned to remain a leader in the industry for years to come.In conclusion, Rapid Molding has established itself as a trusted partner for businesses seeking top-tier rapid prototyping and low-volume manufacturing services. Through its dedication to quality, innovation, and customer satisfaction, the company has set itself apart as a leader in the industry. As they continue to push the boundaries of manufacturing technology and expand their capabilities, Rapid Molding is primed to maintain its position at the forefront of the industry.
Highly Efficient Metal CNC Milling Machine for Precision Manufacturing
The importance of precision and efficiency in the manufacturing industry cannot be overstated. With the increasing demand for high-quality metal components, companies are constantly seeking ways to improve their production processes. One such company that has made significant strides in this area is {Company Name}.{Company Name} has recently invested in a state-of-the-art CNC milling machine to further improve its metal fabrication capabilities. The new machine is a game-changer for the company, as it allows for more precise and efficient metal cutting and shaping.CNC, or computer numerical control, milling machines are a staple in the manufacturing industry. They are capable of performing a wide range of tasks, from simple drilling to complex machining operations. With the latest advancements in technology, CNC milling machines have become even more versatile and precise, making them the go-to choice for companies looking to enhance their metal fabrication capabilities.{Company Name} has always been committed to staying ahead of the curve when it comes to technology and innovation. The investment in the new CNC milling machine is a testament to this commitment. By leveraging the latest advancements in CNC technology, {Company Name} is able to offer its clients even higher quality and more intricate metal components.The new CNC milling machine boasts several key features that set it apart from traditional milling machines. One of the most notable features is its ability to automatically change tools, reducing the need for manual intervention and increasing overall efficiency. Additionally, the machine is equipped with advanced software that allows for real-time monitoring and adjustments, ensuring that the final product meets the highest quality standards.In addition to the technological advancements, the CNC milling machine also offers a higher level of precision. This is particularly important for {Company Name}, as many of its clients require metal components with extremely tight tolerances. The new machine is capable of producing parts with exceptional accuracy, meeting even the most stringent specifications.The investment in the new CNC milling machine has already yielded positive results for {Company Name}. With the increased efficiency and precision, the company has been able to take on more complex projects and deliver them within shorter timeframes. This has not only strengthened its relationships with existing clients but has also attracted new business opportunities.Furthermore, the new machine has opened up possibilities for {Company Name} to explore new markets and industries. With its enhanced capabilities, the company is now able to cater to a wider range of clients, from aerospace and automotive to medical and telecommunications.The CNC milling machine has also had a positive impact on {Company Name}'s internal operations. The increased efficiency and precision have streamlined the production process, allowing the company to optimize its workflow and reduce lead times. This has translated into cost savings and improved overall productivity.Looking ahead, {Company Name} is committed to further leveraging the capabilities of the new CNC milling machine. The company has plans to explore additional applications and industries where the machine can make a significant impact. Additionally, {Company Name} is actively investing in training and development for its employees to ensure they are equipped with the necessary skills to maximize the potential of the new machine.In conclusion, the investment in the new CNC milling machine has solidified {Company Name}'s position as a leader in the metal fabrication industry. With its enhanced capabilities, the company is well-positioned to meet the evolving needs of its clients and capitalize on new business opportunities. As technology continues to advance, {Company Name} remains committed to staying at the forefront of innovation, delivering high-quality metal components with the utmost precision and efficiency.
High-Quality Cnc Milled Aluminum Products for Various Industries
CNC Milled Aluminum Revolutionizing the Manufacturing IndustryIn the world of manufacturing, precision and quality are of utmost importance. This is where CNC (Computer Numerical Control) Milled Aluminum comes into play, offering unparalleled precision, efficiency, and high-quality output. With the advanced capabilities of CNC milling, combined with the expertise of a leading manufacturing company, the manufacturing industry is seeing a revolution in the production of aluminum components.As a prominent player in the manufacturing industry, {Company Name} has been at the forefront of utilizing CNC milled aluminum in their production processes. With state-of-the-art facilities and a team of skilled engineers and technicians, {Company Name} has been able to harness the full potential of CNC milling technology to meet the demands of the modern market.CNC milling is a cutting-edge manufacturing process that utilizes computerized controls and rotating multi-point cutting tools to remove material from a workpiece, producing highly precise and intricate parts and components. Aluminum, with its lightweight yet durable properties, has become a popular choice of material in various industries, ranging from aerospace and automotive to consumer electronics and more. The demand for high-quality, precision-machined aluminum components has been steadily increasing, and CNC milled aluminum has proven to be the answer to this growing demand.One of the key advantages of CNC milled aluminum is its ability to deliver consistency and accuracy in the production of complex parts. The computer-controlled nature of CNC milling ensures that each component is machined with pinpoint precision, resulting in minimal margin for error and a high degree of dimensional accuracy. This level of precision is crucial in industries where the performance and reliability of components are of critical importance.Additionally, CNC milled aluminum offers superior surface finishes, making it an ideal choice for components that require aesthetically pleasing and smooth surfaces. The elimination of manual labor in the machining process reduces the likelihood of human error and ensures that the finished aluminum parts meet the highest standards of quality.{Company Name} has recognized the potential of CNC milled aluminum in meeting the evolving needs of its clientele. By investing in the latest CNC milling technology and continuously upgrading its capabilities, the company has set itself apart as a leader in the production of precision-machined aluminum components. {Company Name}’s commitment to innovation and excellence has positioned it at the forefront of the manufacturing industry, offering a comprehensive range of CNC milled aluminum solutions to cater to a diverse array of industries.Furthermore, {Company Name}’s team of engineers and technicians possess extensive knowledge and expertise in CNC milling, allowing them to optimize the manufacturing processes and deliver exceptional results for their clients. With a focus on continuous improvement and innovation, {Company Name} remains dedicated to pushing the boundaries of what is achievable with CNC milled aluminum, setting new standards for quality and performance in the industry.As the demand for high-quality, precision-machined aluminum components continues to rise, the combination of CNC milled aluminum and the advanced capabilities of {Company Name} is poised to play a pivotal role in shaping the future of the manufacturing industry. By harnessing the power of CNC milling technology, {Company Name} is driving innovation, enhancing productivity, and elevating the standards of precision engineering in the production of aluminum components.In conclusion, CNC milled aluminum represents a game-changing advancement in the manufacturing industry, offering unparalleled precision, efficiency, and quality. With {Company Name} leading the way in harnessing the full potential of CNC milling technology, the future of precision-machined aluminum components looks promising. As advancements in CNC milling continue to unfold, it is evident that CNC milled aluminum will play a pivotal role in shaping the future of manufacturing, driving innovation and excellence in the production of high-quality aluminum components.