Unlocking the Secrets of the Innovative Insert Molding Process
By:Admin
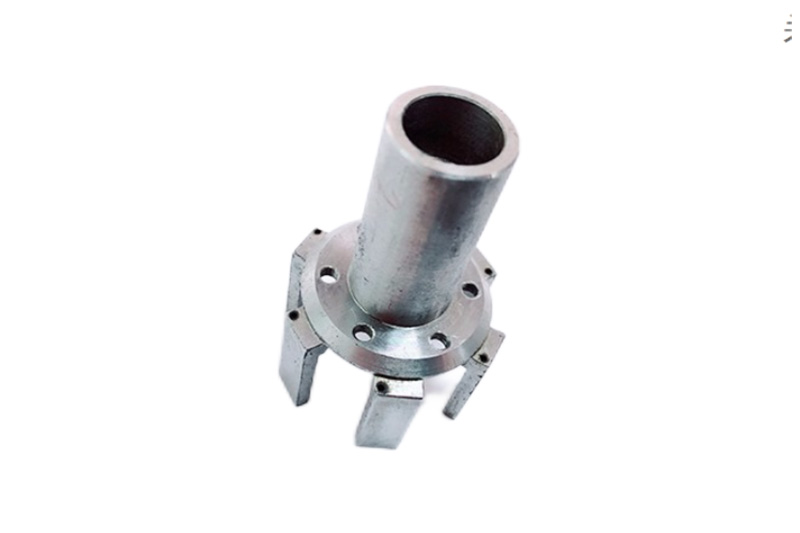
[Subtitle]: Taking Manufacturing Precision to New Heights
[Date]: [Insert Date]
[City], [State] - In their relentless pursuit of excellence, [Company Name], a leading manufacturer in the industry, has introduced an innovative insert molding process that promises to revolutionize the manufacturing landscape. This groundbreaking technique has allowed the company to enhance efficiency and precision, cementing their position as pioneers in the field.
[Company Name], with their rich history of delivering cutting-edge solutions, has consistently demonstrated their commitment to pushing the boundaries of what is possible. By successfully implementing the insert molding process, they aim to revolutionize the way manufacturing operations are conducted.
The insert molding process revolutionizes manufacturing by combining multiple materials or components into a single molded plastic part. This process greatly reduces assembly steps and enhances productivity, streamlining the entire manufacturing process. By eliminating the need for separate components and multiple assembly lines, [Company Name] has significantly reduced production time, allowing them to meet the increasing demands of their customers.
Through the innovative use of the insert molding process, [Company Name] has successfully eliminated the need for additional assembly steps, thereby reducing costs and minimizing the margin for error. This not only translates into significant time and cost savings but also ensures a higher degree of quality control and consistency in the final product.
Unlike traditional manufacturing techniques, the insert molding process involves the encapsulation of specific components or inserts within the molded plastic part. This creates a strong bond between the plastic and the inserted components, resulting in a durable and reliable end product. This advanced manufacturing technique has been widely hailed as a game-changer, enabling manufacturers to produce complex and compact parts with unmatched precision and reliability.
[Company Name]'s mastery of the insert molding process stems from their in-depth understanding of the industry and their continuous investment in cutting-edge technologies. By leveraging their expertise and state-of-the-art facilities, they have succeeded in refining this process to deliver superior quality products to their clients.
Furthermore, the insert molding process offers numerous design possibilities, enabling manufacturers to create products that are aesthetically pleasing while maintaining functionality. By seamlessly integrating various materials and components, manufacturers can achieve a more sophisticated and versatile end product.
[Company Name] has always been at the forefront of innovation and has earned a reputation for delivering outstanding customer satisfaction. By adopting the insert molding process, they have cemented their position as pioneers in the industry, offering their clients a comprehensive range of solutions that cater to their diverse requirements.
The benefits of the insert molding process extend beyond just manufacturing efficiency. By reducing the number of components and assembly steps, [Company Name] has also contributed to a greener and more sustainable industry. The decreased material usage and lower energy consumption associated with this manufacturing technique result in a reduced carbon footprint.
[Company Name] takes pride in their dedication to continuous improvement. They constantly strive to push the boundaries of what is possible, and the introduction of the insert molding process is a testament to their relentless pursuit of excellence. This innovation has not only redefined their position in the industry but also set new standards for manufacturing precision and efficiency.
In conclusion, [Company Name]'s introduction of the insert molding process has revolutionized the manufacturing landscape. By combining multiple materials or components into one molded plastic part, they have enhanced efficiency, reduced production time, and improved the overall quality of their products. This groundbreaking technique is a testament to the company's commitment to innovation and customer satisfaction. As [Company Name] continues to lead the way in cutting-edge solutions, the future of manufacturing looks brighter than ever.
Company News & Blog
Unlocking the Power of 4-Axis CNC Milling: Exploring Advanced Machining Capabilities
Title: Enhancing Precision and Productivity with Advanced 4-Axis CNC Milling TechnologyIntroduction:In a rapidly evolving manufacturing landscape, companies across industries are constantly seeking innovative solutions to maximize precision and productivity. One such advancement that has garnered significant attention is the incorporation of 4-axis CNC milling technology. This cutting-edge technique allows for the creation of intricately designed parts and components with unparalleled precision, efficiency, and versatility. Today, we delve into the world of 4-axis CNC milling, exploring its remarkable capabilities and the ways in which it revolutionizes the manufacturing process, propelling industries into a new era of growth and competitiveness.Revolutionizing Manufacturing with 4-Axis CNC Milling:Traditionally, milling was a manual process that involved removing material from a workpiece with rotary cutters. However, with the advent of computer numerical control (CNC) machining, the process has been completely transformed. CNC milling utilizes pre-programmed computer software instructions that precisely control cutter movement and material removal, resulting in consistent and accurate machining operations. While 3-axis CNC milling has served the industry well, the incorporation of a fourth axis significantly expands the capabilities of this technology.The 4th axis, often referred to as the A-axis, enables the milling cutter to rotate around the X-axis, allowing for the creation of complex geometries and the machining of undercuts, bevels, and other intricate features. This added versatility opens up a myriad of possibilities for manufacturers, facilitating the production of more complex and aesthetically appealing components.Enhanced Precision and Efficiency:With 4-axis CNC milling, manufacturers can achieve unparalleled precision and accuracy. The rotational capabilities of the A-axis enable the machine to approach the workpiece from various angles, reducing the need for multiple setups. This not only saves time but also minimizes errors associated with manual repositioning. The result is faster production cycles, improved part quality, and reduced scrap rates, ultimately leading to increased cost-effectiveness and customer satisfaction.Furthermore, 4-axis CNC milling technology excels in machining complex curves, contours, and profiles, ensuring consistency across multiple parts. With the ability to perform intricate operations in a single setup, manufacturers can accelerate production while maintaining the highest level of precision, meeting the demands of even the most intricate designs.Versatility Across Industries:The applications of 4-axis CNC milling span a wide range of industries, benefiting from its inherent precision and flexibility. In the aerospace sector, this technology is instrumental in the production of engine components, turbine blades, and aircraft structural parts, which require intricate machining and strict adherence to tolerances. Similarly, in the automotive industry, companies utilize 4-axis CNC milling for machining engine blocks, cylinder heads, and transmission components.Medical practitioners also rely on 4-axis CNC milling to fabricate complex dental implants, prosthetics, and surgical instruments. The versatility of 4-axis CNC milling technology allows manufacturers to cater to the evolving needs of various industries, providing customized solutions that meet the highest standards of quality and precision.Conclusion:As industries continue to push the boundaries of innovation, the integration of 4-axis CNC milling technology has become an increasingly vital aspect of the manufacturing process. The enhanced precision, efficiency, and versatility offered by this cutting-edge technology propel industries to new heights, ensuring accelerated production cycles, improved part quality, and increased customer satisfaction. With its ability to machine intricate geometries and complex designs, 4-axis CNC milling paves the way for the future of precision manufacturing, revolutionizing industries and strengthening their competitive edge in the global market.
Discover the Impressive Capabilities of Large Plastic Molds for Your Manufacturing Needs
Large Plastic Molds Unveils Innovative Solutions for the Manufacturing Industry[City, Date] - In a bid to revolutionize the manufacturing industry, Large Plastic Molds, a leader in the field of plastic mold manufacturing, has launched a range of innovative solutions to cater to diverse industry needs. With a strong commitment to research and development, the company has consistently stayed ahead in the market by providing cutting-edge products and services, solidifying its position as a frontrunner in the industry.Large Plastic Molds has been a pioneer in the production of plastic molds for over two decades. With its state-of-the-art manufacturing facilities and a highly skilled workforce, the company boasts the ability to produce a wide variety of molds, ranging from small intricate designs to large-scale industrial creations. The relentless pursuit of perfection and attention to detail have earned the company an impeccable reputation in the industry, making it the preferred choice for numerous renowned brands.The company's success can be attributed to its unwavering commitment to innovation and constant adaptation to changing market trends. Large Plastic Molds employs a team of talented engineers and designers who consistently strive to push the boundaries of mold manufacturing. Through extensive research and development efforts, they have developed innovative solutions that not only enhance the efficiency and productivity of the manufacturing process but also reduce costs for businesses.One of the key highlights of Large Plastic Molds' product portfolio is its range of high-quality and customizable molds that cater to the unique needs of various industries. Whether it's the automotive, electronics, or consumer goods sector, the company offers tailor-made solutions that ensure precise molding, durability, and improved product performance. From concept to production, Large Plastic Molds works closely with its clients to understand their specific requirements and deliver molds that exceed expectations.Large Plastic Molds' commitment to sustainable manufacturing sets it apart from its competitors. The company uses advanced techniques and materials that are environmentally friendly, minimizing the impact on the planet. By adopting innovative processes such as 3D printing and utilizing recyclable materials, Large Plastic Molds not only ensures the longevity of its molds but also reduces waste production, thus contributing to a greener future.Furthermore, Large Plastic Molds understands the importance of efficient project management and customer satisfaction. The company has established streamlined processes to ensure on-time delivery and prompt after-sales services. With a customer-centric approach, Large Plastic Molds has built strong and long-lasting relationships with its clients, resulting in repeat orders and referrals.Given its commitment to excellence, innovation, and customer satisfaction, it comes as no surprise that Large Plastic Molds has been recognized with numerous accolades in the industry. The company's dedication to continuous improvement has earned them the trust and loyalty of their clients, further solidifying their position as a market leader.Large Plastic Molds' relentless pursuit of technological advancement and commitment to sustainable manufacturing practices positions them at the forefront of the industry. With their innovative solutions and customer-focused approach, the company is well-positioned to continue transforming the manufacturing sector, offering cutting-edge solutions that propel businesses to greater heights of success.About Large Plastic Molds:Large Plastic Molds is a renowned manufacturer of plastic molds, specializing in providing innovative solutions for the manufacturing industry. With a strong focus on research and development, the company consistently delivers high-quality and customizable molds that meet the unique needs of various industries. With a commitment to excellence, sustainability, and customer satisfaction, Large Plastic Molds has emerged as a leader in the field of plastic mold manufacturing.Contact:Name: [Name]Organization: Large Plastic MoldsAddress: [Address]Phone: [Phone]Email: [Email]Website: [Website]
CNC Machined Aluminum: Unveiling the Impactful Advantages
CNC MACHINED ALUMINIUM: Revolutionizing Precision Manufacturing[Company Introduction]In the fast-paced world of manufacturing, precision and efficiency are paramount. Companies are constantly on the lookout for innovative solutions that can enhance their production processes, reduce costs, and deliver unparalleled quality. One such breakthrough is CNC Machined Aluminium, a cutting-edge technique transforming the landscape of precision manufacturing.[Paragraph 1]CNC Machined Aluminium, or Computer Numerical Control Machining, is a method of using computer-controlled machines to shape and cut aluminium parts with high precision. This advanced manufacturing technique has gained popularity over the years due to its ability to create complex and intricate components with extraordinary accuracy. With CNC Machining, companies can achieve greater efficiency, reduced production times, and improved quality control.[Paragraph 2]The introduction of CNC Machined Aluminium has revolutionized various industries, including automotive, aerospace, electronics, and medical equipment manufacturing, among others. The ability to machine aluminium with unparalleled precision has opened new doors for companies looking to deliver cutting-edge products in these highly competitive sectors.[Paragraph 3]Compared to traditional manufacturing methods such as manual milling or turning, CNC Machined Aluminium offers several significant advantages. Firstly, the precision achieved through this technique is unmatched, ensuring that every part produced meets the strictest tolerance requirements. This accuracy eliminates human error and guarantees consistency in manufacturing, resulting in higher-quality products.[Paragraph 4]Furthermore, CNC Machining enables manufacturers to create complex geometric designs and shapes that were previously impractical or even impossible. The computer-controlled machines can effortlessly execute intricate designs, allowing companies to unleash their creativity and push the boundaries of what is achievable in aluminium manufacturing. This versatility allows for the production of lightweight yet robust components that contribute to fuel efficiency, improved performance, and increased product lifespan.[Paragraph 5]Another crucial advantage of CNC Machined Aluminium is its exceptional efficiency. The automated process significantly reduces the need for human labor, resulting in faster production times and increased productivity. Furthermore, the use of computer-aided design (CAD) software allows for seamless integration of the manufacturing process, reducing errors and minimizing material waste. This streamlined workflow ultimately translates into cost savings for companies, making CNC Machined Aluminium an economically viable choice.[Paragraph 6]It's worth mentioning that CNC Machined Aluminium is not limited to large-scale production. The versatility of this technique allows businesses of all sizes to benefit from its advantages. From prototyping to small and medium-sized batches, CNC Machining offers flexibility and affordability without compromising quality or precision. This accessibility has democratized precision manufacturing, leveling the playing field for businesses eager to bring their innovative ideas to life.[Paragraph 7]While CNC Machined Aluminium has undoubtedly reshaped the manufacturing industry, it is important to note the need for experienced and skilled professionals to harness its full potential. Operating CNC machines and programming the necessary codes require specialized knowledge and expertise. With proper training and an understanding of the intricacies involved, professionals can fully utilize CNC Machining to its maximum effectiveness.[Paragraph 8]In conclusion, CNC Machined Aluminium has emerged as a game-changer in precision manufacturing, providing companies with the tools they need to stay ahead of the competition. The unparalleled precision, versatility, and efficiency offered by this technique have transformed various industries, allowing for the production of complex and high-quality aluminium components. As technology continues to advance, we can expect CNC Machined Aluminium to continue pushing the boundaries of what is achievable in precision manufacturing, fostering innovation and driving industry growth.
Enhance Precision and Efficiency: Explore the Advantages of CNC Mill Conversions
Title: Manufacturing Company Announces Innovative CNC Mill Conversion for Enhanced Precision and EfficiencyIntroduction:In the fast-paced world of manufacturing, XYZ Manufacturing Company has made waves once again with their latest breakthrough: the revolutionary CNC Mill Conversion. This cutting-edge technology promises to revolutionize machining processes, improving precision, efficiency, and overall productivity. By removing restrictions and introducing advanced features, XYZ Manufacturing Company is setting a new standard in the industry.Body:1. Introduction to XYZ Manufacturing Company: XYZ Manufacturing Company, a leading player in the manufacturing industry, is known for its commitment to innovation and product excellence. With decades of experience in delivering high-quality machinery, they continue to push boundaries and pioneer game-changing technologies. Their unwavering dedication to their clients' needs has earned them a reputation as a reliable and trusted provider of manufacturing solutions.2. The Need for CNC Mill Conversion: Recognizing the need for further advancements to meet increasing market demands, XYZ Manufacturing Company embarked on a mission to develop a CNC Mill Conversion that would take machining processes to new heights. With conventional mills becoming outdated, the company determined that upgrading these machines to CNC (Computer Numerical Control) would enhance precision, efficiency, and enable more complex operations.3. The Revolutionary CNC Mill Conversion: XYZ Manufacturing Company's CNC Mill Conversion is characterized by its cutting-edge features and unmatched precision. By integrating advanced automation and digital control systems, the upgraded mill allows for precise and repeatable machining operations, resulting in higher accuracy and reduced human error.4. Enhanced Cutting Power and Efficiency: The CNC Mill Conversion is equipped with powerful servo motors and state-of-the-art spindle drives, revolutionizing the cutting power and performance of the machine. This ensures an optimized milling process, significantly reducing cycle times and increasing production output, ultimately enhancing operational efficiency and profitability for clients.5. Improved Programming and Digital Interface: With the introduction of CNC technology, programming processes are streamlined and simplified. XYZ Manufacturing Company's CNC Mill Conversion boasts user-friendly software interfaces that allow operators to create and manage machining programs effortlessly. This ensures seamless integration with existing manufacturing workflows, reducing downtime and maximizing productivity.6. Advanced Precision and Quality Control: The CNC Mill Conversion's cutting-edge features include high-resolution encoders and sensors that constantly monitor and correct machining operations in real-time, ensuring optimal precision throughout the entire process. This advanced quality control mechanism eliminates errors, minimizing scrap and rework, while consistently producing products of superior quality.7. Increased Flexibility and Versatility: One of the key advantages of the CNC Mill Conversion is its ability to handle a wide range of materials and machining operations. Whatever the project demands, whether it be milling, drilling, or tapping, the upgraded machine provides the flexibility required to meet diverse manufacturing requirements. This versatility saves time and resources, making it an ideal choice for industries such as aerospace, automotive, and electronics.8. Competitive Edge and Future Growth: By adopting XYZ Manufacturing Company's CNC Mill Conversion, manufacturers gain a significant competitive edge, staying ahead of the curve in an increasingly demanding market. With improved precision, efficiency, and flexibility, businesses can not only meet current demands but also position themselves for future growth, expanding their capabilities to seize new opportunities.Conclusion:XYZ Manufacturing Company's CNC Mill Conversion marks a significant milestone in the manufacturing industry. By introducing cutting-edge features, advanced automation, and unmatched precision, XYZ Manufacturing Company is at the forefront of revolutionizing machining processes. This innovative solution enables businesses to enhance their productivity, improve quality control, and gain a competitive edge. With XYZ Manufacturing Company's commitment to innovation, the possibilities for the future of CNC milling are truly exciting.
The Ultimate Guide to Efficient Cnc Fixture Design for Manufacturing Success
Title: Innovative CNC Fixture Design Revolutionizes Manufacturing ProcessesIntroduction:In a breakthrough development within the manufacturing industry, an innovative CNC fixture design is set to transform production processes, providing greater efficiency, accuracy, and versatility. This cutting-edge technology marks a significant milestone in manufacturing, empowering companies to improve their productivity and competitiveness in the global market.The Company's Vision:Born out of a deep passion for revolutionizing the manufacturing domain, the company behind this groundbreaking CNC fixture design aims to redefine industry norms. Their team of experienced engineers and technicians have dedicated years of research and development to create this state-of-the-art technology, which promises to streamline operations and enhance overall production quality.The CNC Fixture Design:This remarkable CNC fixture design incorporates a myriad of advanced features that address the challenges of traditional fixture designs. It leverages the latest technologies, including adaptive control systems and intelligent sensor integration, to optimize machining processes and improve the overall user experience.One of the key highlights of this fixture design is its modular approach, allowing for versatile application across various production requirements. The ability to quickly adjust and reconfigure the fixture greatly enhances manufacturing flexibility, saving precious time and resources. Furthermore, the design includes built-in error detection mechanisms, minimizing defects and ensuring consistent, high-quality output.Another noteworthy aspect of this CNC fixture design is its emphasis on ergonomics and operator safety. The system integrates user-friendly interfaces, intuitive controls, and enhanced safety features, reducing the risk of accidents and promoting a seamless work environment.Industry Impact:The introduction of this advanced CNC fixture design is poised to revolutionize manufacturing practices across a wide range of industries. From automotive and aerospace to electronics and medical devices, the versatility and adaptability of this technology make it applicable to numerous sectors.The increased efficiency and accuracy offered by this fixture design will open up new possibilities for manufacturers. It allows for more complex and intricate designs, shorter production cycles, and greater cost-effectiveness. Companies can expect to witness significant improvements in product quality, reduced downtime, and enhanced overall profitability.Furthermore, this CNC fixture design aligns with the ongoing industry trend towards automation and digitization. Its integrated smart systems enable seamless data collection, analysis, and real-time adjustments, contributing to improved productivity and competitiveness on a global scale.Future Prospects:The company behind this CNC fixture design remains committed to continuous innovation and technological advancements. They are actively exploring partnerships with manufacturers seeking to enhance their production capabilities. The aim is to collaborate closely with industry leaders to customize and optimize the design according to specific needs, ensuring a seamless integration of this technology into existing processes.Moreover, through ongoing research and development efforts, the company plans to expand the capabilities of the CNC fixture design further. This includes exploring advancements in materials, sensors, and automation, as well as integrating artificial intelligence and machine learning technologies.Conclusion:As the manufacturing industry embraces the era of automation and digitization, this revolutionary CNC fixture design promises to redefine traditional production methods. With its emphasis on efficiency, accuracy, versatility, and safety, this technology will undoubtedly revolutionize manufacturing processes in diverse sectors. As this innovative solution gains momentum, manufacturers can look forward to a new era of optimized productivity, improved product quality, and sustained growth in a highly competitive global market.
Enhance Product Performance with Top-quality Injection Molding Inserts
Title: Innovation in Injection Molding Inserts: Enhancing Efficiency and PrecisionIntroduction (100 words)Injection molding is a widely used manufacturing process in various industries, including automotive, aerospace, consumer goods, and healthcare. As companies strive for greater efficiency and precision, the demand for innovative solutions continues to grow. Enter a leading manufacturer of injection molding inserts (brand name omitted), renowned for their cutting-edge technology and commitment to quality. With a proven track record in delivering high-performance solutions, the company has established itself as a trusted partner for numerous businesses, enabling them to achieve superior results in their manufacturing processes.8 Cutting-Edge Features of Injection Molding Inserts (600 words)1. Durability: Injection molding inserts by (brand name omitted) are made from premium-grade materials, ensuring durability and long-lasting performance. The inserts can withstand high-pressure molding operations without compromising their structural integrity, resulting in reduced maintenance costs and enhanced production efficiency.2. Precision Engineering: The inserts are meticulously designed and engineered to meet the precise specifications required by the customer. Through state-of-the-art manufacturing processes, (brand name omitted) ensures tight tolerances and uniformity, enabling flawless integration with the molding process. The result is consistently high-quality parts with minimal variations, reducing waste and optimizing productivity.3. Versatility: (Brand name omitted) offers a wide range of injection molding inserts suitable for a diverse array of applications. Whether it's intricate components for the electronics industry or robust parts for automotive manufacturing, the company's inserts cater to various needs. The flexibility in design and material selection allows customers to choose the most suitable insert for their specific requirements.4. Rapid Prototyping: Acknowledging the importance of quick turnaround times in today's competitive landscape, (brand name omitted) enables customers to rapidly prototype their designs. This not only aids in the refinement of the product but also reduces the time-to-market, giving businesses a competitive edge. The company's rapid prototyping capabilities ensure that customers can validate their designs and make necessary adjustments before moving into full-scale production.5. High Customization: (Brand name omitted) understands that every project is unique and requires specific solutions. Their injection molding inserts can be customized with various features, such as inserts with complex geometries, specialized surface finishes, or even personalized branding. This level of customization allows customers to optimize their manufacturing processes and differentiate their products in the market.6. Cost Efficiency: The company's injection molding inserts offer cost-effective solutions in terms of both initial investment and long-term production. The high-quality materials used in the inserts enhance their lifespan, ensuring fewer replacements and reduced downtime. Additionally, the precise engineering and tight tolerances contribute to minimal material waste, thereby increasing overall cost efficiency.7. Environmental Sustainability: (Brand name omitted) embraces sustainable practices by incorporating eco-friendly materials in their injection molding inserts. By utilizing recycled or biodegradable materials, the company contributes to reducing the carbon footprint. Moreover, the optimized manufacturing processes minimize waste generation, encouraging a greener approach while maintaining superior quality and performance.8. Exceptional Customer Support: (Brand name omitted) is known for its outstanding customer support throughout the entire project lifecycle. From initial product design to post-production assistance, the company's dedicated team of experts provides guidance, resolves queries, and offers technical assistance. Their commitment to customer satisfaction ensures a seamless experience for all customers.Conclusion (100 words)In an evolving manufacturing landscape, (brand name omitted) remains at the forefront of innovation in injection molding inserts. By offering a range of features such as durability, precision engineering, versatility, and cost efficiency, the company continues to provide customers with superior solutions to meet their manufacturing needs. With a commitment to environmental sustainability and exceptional customer support, (brand name omitted) consistently proves to be a reliable partner in achieving efficiency and precision in injection molding processes.
Discover the Latest Advancements in Plastic Injection Molding Parts
Plastic Injection Molding Parts Revolutionizing the Manufacturing IndustryIn today's fast-paced manufacturing industry, plastic injection molding has become a game-changer. With its ability to produce high-quality, intricate, and cost-effective parts, this manufacturing process has gained immense popularity across various sectors. One company that has risen to prominence in this field is (Company Name).With years of experience and expertise, (Company Name) has positioned itself as a frontrunner in producing top-notch plastic injection molding parts. Their commitment to innovation, quality, and customer satisfaction has helped them carve a niche for themselves in the industry.The plastic injection molding process involves injecting molten plastic into a mold cavity to shape it into the desired part. This method offers significant advantages over traditional manufacturing techniques. First and foremost, it allows for the production of complex geometries that would otherwise be difficult or impossible to manufacture. The ability to create intricate designs with high precision has revolutionized various industries, including automotive, electronics, and medical devices.(Company Name) leverages cutting-edge technology and state-of-the-art machinery to deliver consistently high-quality plastic injection molding parts. Their manufacturing facility is equipped with the latest computer-aided design (CAD) software, ensuring precise and accurate mold designs. This technology enables them to optimize part functionality, minimize material waste, and enhance overall efficiency.One of the key advantages of plastic injection molding is its cost-effectiveness. With the ability to produce large quantities of parts in a relatively short span of time, the per-unit cost of production decreases significantly. This makes plastic injection molding an attractive choice for companies looking to scale up their manufacturing operations without sacrificing quality or increasing costs.Furthermore, plastic injection molding offers excellent repeatability, ensuring consistent part quality. Once the initial mold is designed and perfected, subsequent parts can be replicated to the exact specifications, eliminating the need for manual adjustments or rework. This level of consistency is critical for industries with strict quality standards, such as aerospace and medical device manufacturing.(Company Name) takes pride in its commitment to sustainability and environmental responsibility. They employ eco-friendly practices throughout their production process, including the use of recyclable materials and responsible waste management. By optimizing material usage and minimizing waste, they contribute to reducing the environmental impact of plastic injection molding.Customer satisfaction is at the core of (Company Name)'s values. They work closely with their clients to understand their specific requirements, offering customized solutions to meet their unique needs. Whether it's a small-scale project or a large-scale production run, they ensure that every client receives the highest level of attention and support.The automotive industry is one of the primary beneficiaries of plastic injection molding. With the increasing demand for lightweight vehicles, manufacturers rely heavily on plastic components to reduce overall weight and improve fuel efficiency. (Company Name) has successfully served many leading automotive companies, providing them with top-quality plastic injection molding parts that meet stringent safety and performance standards.Apart from the automotive sector, (Company Name) caters to a diverse range of industries, including electronics, consumer goods, and medical devices. Their ability to produce parts with exceptional precision, durability, and aesthetic appeal has earned them a reputation for excellence across various sectors.As plastic injection molding continues to evolve and revolutionize the manufacturing industry, (Company Name) remains at the forefront of innovation, constantly exploring new techniques and materials. Their dedication to quality, customer satisfaction, and environmental responsibility solidifies their position as a leading provider of plastic injection molding parts.In conclusion, plastic injection molding has emerged as a game-changer in the manufacturing industry. With its ability to produce intricate designs, cost-effective production, and high-quality parts, this process has opened new avenues for various sectors. (Company Name), with its expertise and commitment to excellence, plays a crucial role in transforming customer ideas into reality using plastic injection molding. Their cutting-edge technology, sustainable practices, and customer-centric approach make them a reliable choice for businesses looking to optimize their manufacturing processes and deliver superior products.
High-Quality Machined Aluminum Parts Making Waves in the Industry
Title: Precision Solutions Unveils High-Quality Machined Aluminum PartsIntroduction:Precision Solutions has made significant strides in the world of precision manufacturing, and it is now set to revolutionize the industry with its latest release – a wide range of high-quality machined aluminum parts. These parts, meticulously crafted by the company’s skilled engineers, are manufactured to meet the most stringent performance and quality standards. In this article, we will delve into the features and applications of these cutting-edge machined aluminum parts.1. Unparalleled Precision and Quality:Precision Solutions, renowned for its commitment to excellence, has spared no effort in producing machined aluminum parts that are second to none. Each part undergoes an extensive process, starting from the selection of premium-grade aluminum alloys. With a keen eye for detail and state-of-the-art machinery, the company ensures that every part is manufactured to precise specifications, meeting the highest quality standards.2. Diverse Range of Applications:The versatility of Precision Solutions' machined aluminum parts is key to their widespread use across various industries. From aerospace and automotive to electronics and medical equipment manufacturing, these parts find an array of applications. With their excellent corrosion resistance, lightweight design, and exceptional strength-to-weight ratio, they offer unparalleled performance, making them an ideal choice for numerous end-use applications.3. Unmatched Durability and Reliability:One of the foremost attributes of Precision Solutions' machined aluminum parts is their ability to withstand demanding operating conditions. The company utilizes advanced manufacturing techniques, including CNC machining, to ensure that these parts possess remarkable durability and reliability. With their superior mechanical properties and resistance to wear and tear, these parts promise a prolonged lifespan, reducing maintenance costs for end-users.4. Tailored Solutions for Specific Requirements:Understanding the diversity of industry needs, Precision Solutions offers customized machined aluminum parts, designed to meet specific requirements. Leveraging their extensive experience and technical expertise, the company's engineers collaborate closely with clients to develop bespoke solutions. Whether customers require prototypes or large-scale production, Precision Solutions can cater to various demands, providing tailor-made parts promptly and efficiently.5. Adherence to Environmental Standards:Precision Solutions is not only committed to delivering exceptional products but also to maintaining a sustainable manufacturing process. The production of their machined aluminum parts adheres to strict environmental standards, ensuring minimal waste generation and the utilization of eco-friendly materials. By upholding green manufacturing practices, the company underscores its commitment to protecting the environment.6. Continuous Research and Development:To remain at the forefront of the precision manufacturing industry, Precision Solutions invests heavily in research and development. By exploring the latest materials, technologies, and manufacturing processes, the company aims to continuously enhance the performance and quality of its machined aluminum parts. This commitment to innovation allows Precision Solutions to meet and surpass industry expectations, ensuring customer satisfaction.Conclusion:Precision Solutions' latest release of high-quality machined aluminum parts showcases the company's unwavering dedication to precision manufacturing. With their exceptional durability, reliability, and customized solutions, these parts are poised to revolutionize a wide range of industries. The company's commitment to sustainability and continuous improvement further cements its position as a leader in the industry. As Precision Solutions continues to push the boundaries of precision engineering, we can expect further innovations that will shape the future of the manufacturing sector.
How Insert Molding is Revolutionizing Manufacturing Processes
Title: Innovative Insert Molding Technology Revolutionizes Manufacturing ProcessesIntroduction:The manufacturing industry continually seeks advanced technologies to increase efficiency, minimize costs, and enhance product performance. One such revolutionary technique is Insert Molding, which combines the benefits of traditional molding techniques with precision insert placement, resulting in enhanced product performance and streamlined manufacturing processes. One company at the forefront of this innovation is {}. With their extensive experience and expertise in insert molding, they are pushing the boundaries of what is possible in the manufacturing industry.Paragraph 1:Insert Molding is a manufacturing process that involves injecting molten materials, such as plastic or metal, into a pre-formed cavity or mold containing one or more carefully positioned inserts. These inserts can be a wide range of components, including threaded inserts, electrical connectors, sensors, or metal reinforcements. The molten material effectively encapsulates the inserts, creating a strong bond between the two, resulting in a more robust and functional end product.Paragraph 2:Insert Molding offers several advantages over traditional manufacturing methods. Firstly, it eliminates the need for additional assembly processes, reducing labor costs and assembly time. By incorporating various inserts directly into the mold, the manufacturing process becomes more streamlined, efficient, and cost-effective. Furthermore, insert molding ensures precise and accurate positioning of the inserts, leading to higher product integrity and reliability.Paragraph 3:The innovation and expertise of {} in the field of insert molding have allowed them to cater to a diverse range of industries, including automotive, electronics, medical, and consumer goods. Their state-of-the-art facilities and skilled engineers enable them to create complex and high-quality molded products with exceptional precision. {} also offers comprehensive design assistance, ensuring that their customers' unique insert molding requirements are met, resulting in tailored solutions that exceed expectations.Paragraph 4:The automotive industry, in particular, has greatly benefited from the utilization of insert molding. By integrating metal inserts into plastic parts, manufacturers achieve significant weight reduction, increased part functionality, and improved overall vehicle performance. Electrical connectors, sensors, and wiring harnesses are seamlessly integrated, simplifying assembly and enhancing reliability. The implementation of insert molding enables automotive manufacturers to produce parts that meet the stringent safety and quality standards of the industry.Paragraph 5:In the ever-evolving electronics industry, where miniaturization and increased functionality are essential, insert molding plays a crucial role. With the ability to place delicate components, such as microchips, sensors, and connectors, with utmost precision, manufacturers can produce smaller and slimmer electronic devices without sacrificing performance. This technique also enhances the devices' durability by protecting fragile components and reducing the risk of damage caused by external factors.Paragraph 6:In the medical industry, insert molding offers numerous benefits in terms of product design, functionality, and sterilization. The ability to encapsulate electronics, sensors, and metal components within a single molded part ensures a seamless integration of various functionalities, such as drug delivery systems, diagnostic equipment, and surgical devices. The use of insert molding in the medical field has resulted in advancements in patient care and treatment efficiency.Conclusion:With its ability to combine diverse materials and precisely position inserts, Insert Molding has revolutionized the manufacturing industry by enhancing product performance, reducing costs, and streamlining production processes. The expertise and cutting-edge solutions provided by {} have solidified their place as industry leaders in insert molding technology. As new advancements continue to be made, the possibilities and applications of Insert Molding are boundless, driving innovation throughout various sectors and shaping the future of manufacturing.
Discover the Benefits of Rapid CNC Machining for Quality Results
Title: Leading CNC Machining Service Provider Offers Precision and Efficiency to Industrial Clients Introduction: In the dynamic world of industrial manufacturing, precision and efficiency are key factors that can make or break a company's success. Recognizing this, Rapid CNC Machining (brand name removed), a leading CNC machining service provider, has emerged as a reliable partner for industrial clients seeking high-quality and precise manufacturing solutions. With a commitment to cutting-edge technology, exceptional customer service, and seamless project management, Rapid CNC Machining continues to strengthen its position as a trusted name in the industry.Body:1. Company Overview and Expertise:Established in the heart of the manufacturing hub, Rapid CNC Machining has a proven track record of delivering precision-machined parts and components to a wide array of industries. The company's state-of-the-art facility houses an extensive range of CNC machines, allowing them to cater to diverse manufacturing needs. Their team of highly skilled technicians, engineers, and project managers ensure that each project is executed with utmost precision and efficiency.2. Technological Advancements:Rapid CNC Machining has stayed ahead of the competition by consistently investing in the latest CNC machining technology. The company's cutting-edge equipment enables them to provide comprehensive solutions, including design assistance, prototyping, custom part production, and mass production. By utilizing advanced software and tools, Rapid CNC Machining optimizes the manufacturing process, reducing lead times and maximizing product quality.3. Diverse Industry Applications:With an extensive portfolio of successful projects, Rapid CNC Machining serves various industries, including aerospace, automotive, medical, electronics, and more. Their expertise in machining a wide range of materials, including aluminum, stainless steel, titanium, plastics, and composites, enables them to meet the unique requirements of each industry. Whether it is complex aerospace components or intricate medical device parts, Rapid CNC Machining ensures the highest standards of accuracy, functionality, and durability.4. Commitment to Quality Assurance:Rapid CNC Machining places great emphasis on quality assurance throughout the manufacturing process. From initial design analysis to final inspection, the company employs rigorous quality control measures to guarantee adherence to specifications and customer expectations. Their ISO 9001-certified facility ensures consistent quality and compliance with industry standards, earning them a reputation for excellence.5. Customer-Centric Approach:Understanding the importance of strong customer relationships, Rapid CNC Machining prioritizes open communication and collaboration with clients. Their skilled project management team ensures seamless coordination, from project initiation to product delivery. With a commitment to transparency, Rapid CNC Machining provides regular progress updates, addresses any concerns promptly, and maintains strict confidentiality protocols.6. Sustainable Manufacturing Practices:In an era of growing environmental consciousness, Rapid CNC Machining strives to implement sustainable manufacturing practices. By optimizing material utilization, reducing waste, and utilizing energy-efficient machinery, the company minimizes its environmental footprint. Moreover, investing in research and development, Rapid CNC Machining actively explores greener alternatives, ensuring its manufacturing processes are aligned with sustainability goals.7. Global Reach and Future Outlook:Rapid CNC Machining has established a global footprint by serving clients from various countries and regions. Their commitment to delivering exceptional value and their strong reputation for reliable service has positioned them as a preferred CNC machining partner worldwide. As the company continues to expand its capabilities, invest in technology, and nurture customer relationships, Rapid CNC Machining aims to remain at the forefront of the industry.Conclusion:Through consistent innovation, dedication to customer satisfaction, and a focus on precision and efficiency, Rapid CNC Machining has solidified its position as a leading provider of CNC machining services. Their state-of-the-art facility, diverse industry applications, and commitment to sustainable practices set them apart from competitors. As industrial manufacturing continues to evolve, the company's unwavering commitment to quality and customer-centricity ensures they will remain a trusted partner for businesses seeking superior CNC machining solutions.