Understanding the Different Axis of CNC Milling: A Comprehensive Guide
By:Admin
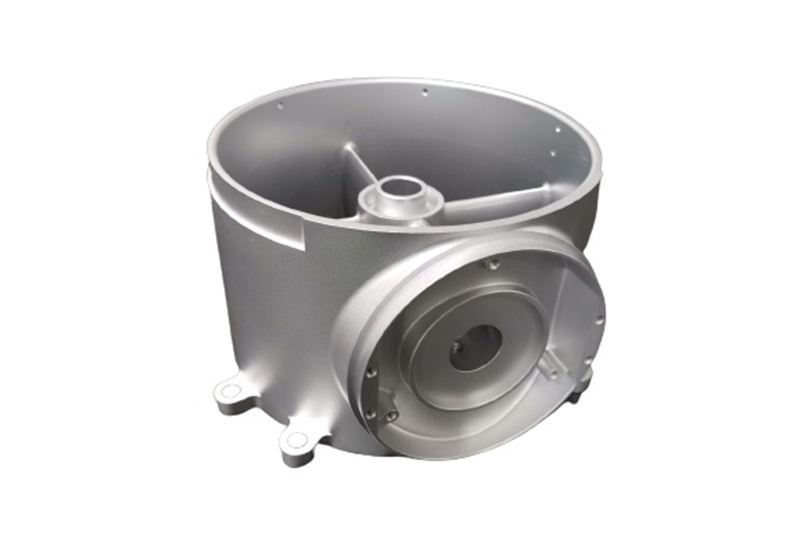
In today's rapidly evolving world, technology continues to reshape industries, and the manufacturing sector is no exception. With the advent of Computer Numerical Control (CNC) machines, precision and efficiency in manufacturing have reached new heights. Among the various CNC machines available, CNC Milling Axis has emerged as a game-changer in this highly competitive field. Its cutting-edge capabilities and superior performance have revolutionized the manufacturing processes, empowering companies to achieve greater productivity and accuracy.
CNC Milling Axis, developed by a leading innovator in the industry, has garnered widespread recognition for its exceptional quality and reliability. Riding on the cutting edge of technology, it has become the go-to choice for manufacturers across diverse sectors. The integrated software and hardware systems have been carefully designed to streamline operations and deliver outstanding results consistently. This has made CNC Milling Axis an indispensable tool for companies focused on maximizing production efficiency.
One of the key advantages of CNC Milling Axis is the flexibility it offers in terms of both complex designs and materials. Whether it's prototyping or mass production, this machine possesses the capability to handle intricate shapes and structures with ease. With advanced software and precision engineering, manufacturers can now create customized components and parts efficiently, meeting the unique requirements of their clients.
Another significant benefit of CNC Milling Axis is its exceptional accuracy. Traditional manufacturing processes often involve human errors, resulting in inconsistent product quality. However, with the precision and repeatability offered by CNC Milling Axis, manufacturers can ensure consistent and precise results every time. This not only reduces waste and rework but also enhances the overall quality of the end product.
Furthermore, CNC Milling Axis enables manufacturers to optimize their production schedules and meet tight deadlines. Its cutting-edge technology allows for fast machining speeds while maintaining uncompromised quality. Companies can now achieve higher output and faster turnaround times, leading to improved customer satisfaction and increased profitability.
In addition to efficiency and accuracy, CNC Milling Axis also prioritizes operator safety. The machine is equipped with advanced safety features that protect operators from potential hazards. As workplace safety becomes a crucial aspect of any manufacturing operation, the integration of these safety measures underscores the commitment of the company to providing a secure working environment.
The company behind CNC Milling Axis has a rich legacy of innovation and technological advancement. With decades of experience, they have remained at the forefront of the industry, consistently exceeding customer expectations. Their commitment to research and development ensures that their products always incorporate the latest advancements, enabling manufacturers to stay ahead in a fiercely competitive market.
To further enhance the customer experience, the company provides comprehensive support and after-sales service. This includes technical training, maintenance assistance, and software updates. The company's dedicated team of experts is always available to address any concerns or queries, ensuring that manufacturers get the most out of their CNC Milling Axis machine.
Looking ahead, the future of manufacturing will undoubtedly be shaped by CNC Milling Axis and similar cutting-edge technologies. As industries continue to evolve and demands for sophisticated products increase, companies that embrace CNC Milling Axis will have a significant advantage. By aligning themselves with the latest advancements in manufacturing technology, they can streamline processes, enhance efficiency, and stay ahead in an ever-changing landscape.
In conclusion, CNC Milling Axis is driving a new wave of innovation in the manufacturing sector. Its combination of precision, efficiency, and safety empowers manufacturers to achieve exceptional results while reducing costs. As the industry moves towards increased automation and digitization, CNC Milling Axis proves to be an invaluable asset, enabling companies to thrive in a competitive marketplace.
Company News & Blog
How Insert Molding is Revolutionizing Manufacturing Processes
Title: Innovative Insert Molding Technology Revolutionizes Manufacturing ProcessesIntroduction:The manufacturing industry continually seeks advanced technologies to increase efficiency, minimize costs, and enhance product performance. One such revolutionary technique is Insert Molding, which combines the benefits of traditional molding techniques with precision insert placement, resulting in enhanced product performance and streamlined manufacturing processes. One company at the forefront of this innovation is {}. With their extensive experience and expertise in insert molding, they are pushing the boundaries of what is possible in the manufacturing industry.Paragraph 1:Insert Molding is a manufacturing process that involves injecting molten materials, such as plastic or metal, into a pre-formed cavity or mold containing one or more carefully positioned inserts. These inserts can be a wide range of components, including threaded inserts, electrical connectors, sensors, or metal reinforcements. The molten material effectively encapsulates the inserts, creating a strong bond between the two, resulting in a more robust and functional end product.Paragraph 2:Insert Molding offers several advantages over traditional manufacturing methods. Firstly, it eliminates the need for additional assembly processes, reducing labor costs and assembly time. By incorporating various inserts directly into the mold, the manufacturing process becomes more streamlined, efficient, and cost-effective. Furthermore, insert molding ensures precise and accurate positioning of the inserts, leading to higher product integrity and reliability.Paragraph 3:The innovation and expertise of {} in the field of insert molding have allowed them to cater to a diverse range of industries, including automotive, electronics, medical, and consumer goods. Their state-of-the-art facilities and skilled engineers enable them to create complex and high-quality molded products with exceptional precision. {} also offers comprehensive design assistance, ensuring that their customers' unique insert molding requirements are met, resulting in tailored solutions that exceed expectations.Paragraph 4:The automotive industry, in particular, has greatly benefited from the utilization of insert molding. By integrating metal inserts into plastic parts, manufacturers achieve significant weight reduction, increased part functionality, and improved overall vehicle performance. Electrical connectors, sensors, and wiring harnesses are seamlessly integrated, simplifying assembly and enhancing reliability. The implementation of insert molding enables automotive manufacturers to produce parts that meet the stringent safety and quality standards of the industry.Paragraph 5:In the ever-evolving electronics industry, where miniaturization and increased functionality are essential, insert molding plays a crucial role. With the ability to place delicate components, such as microchips, sensors, and connectors, with utmost precision, manufacturers can produce smaller and slimmer electronic devices without sacrificing performance. This technique also enhances the devices' durability by protecting fragile components and reducing the risk of damage caused by external factors.Paragraph 6:In the medical industry, insert molding offers numerous benefits in terms of product design, functionality, and sterilization. The ability to encapsulate electronics, sensors, and metal components within a single molded part ensures a seamless integration of various functionalities, such as drug delivery systems, diagnostic equipment, and surgical devices. The use of insert molding in the medical field has resulted in advancements in patient care and treatment efficiency.Conclusion:With its ability to combine diverse materials and precisely position inserts, Insert Molding has revolutionized the manufacturing industry by enhancing product performance, reducing costs, and streamlining production processes. The expertise and cutting-edge solutions provided by {} have solidified their place as industry leaders in insert molding technology. As new advancements continue to be made, the possibilities and applications of Insert Molding are boundless, driving innovation throughout various sectors and shaping the future of manufacturing.
Revolutionizing Rail Industry: The Future of Rail Machining Unveiled
Rail Machining & Company IntroductionRail Machining, a leading provider of rail maintenance solutions, is revolutionizing the rail industry with its cutting-edge technology and innovative solutions. With a commitment to excellence and a focus on delivering exceptional results, Rail Machining has become a trusted partner for many rail operators worldwide.Established in [year], Rail Machining has quickly risen to prominence in the rail industry, thanks to its state-of-the-art equipment and team of highly skilled professionals. The company specializes in providing an array of rail maintenance services, including rail profiling, rail grinding, rail milling, and rail inspection.Rail profiling is an essential process in maintaining the integrity of the railway tracks. Rail Machining utilizes advanced profiling technology to ensure that the rails are perfectly aligned and properly contoured. This precision profiling not only enhances the safety and performance of the tracks but also reduces wear and tear on the rolling stock.Rail grinding is another crucial service offered by Rail Machining. It involves the removal of surface irregularities and defects on the rail, resulting in a smoother and more even surface. This process is essential in preventing accidents caused by rail surface irregularities and reducing noise pollution. Rail Machining's grinding equipment is designed to deliver exceptional results while minimizing downtime and disruption to rail operations.Rail milling is a relatively new method used in rail maintenance. It involves the removal of a thin layer of rail material, resulting in a smoother and more even surface. This process eliminates the need for grinding and provides a longer-lasting solution. Rail Machining's milling technology is at the forefront of the industry, ensuring precise and efficient milling operations.In addition to its maintenance services, Rail Machining offers comprehensive rail inspection solutions. The company's advanced inspection technology can detect various railway defects, such as track misalignment, cracks, and wear. This proactive approach allows rail operators to identify potential issues before they escalate into major problems, reducing the risk of accidents and minimizing maintenance costs.Rail Machining's commitment to excellence extends beyond its cutting-edge technology. The company places a strong emphasis on safety and environmental sustainability. All operations are conducted in compliance with the highest safety standards, and environmentally friendly practices are implemented throughout the entire process. Rail Machining continually invests in research and development to develop innovative, eco-friendly solutions that minimize the environmental impact of rail maintenance.To cater to the global demand for rail maintenance services, Rail Machining has established a wide network of offices and facilities worldwide. With a strong presence in [countries], the company is well-positioned to serve the needs of rail operators in different regions and to provide timely and efficient maintenance solutions.Rail Machining takes pride in its team of experts who possess extensive knowledge and experience in rail maintenance. The company invests in training and development to ensure that its professionals stay up-to-date with the latest industry advancements. This expertise, combined with state-of-the-art technology, allows Rail Machining to deliver exceptional results and exceed customer expectations.As Rail Machining continues to innovate and develop new solutions, the company remains dedicated to its core values of quality, safety, and customer satisfaction. With its commitment to excellence and passion for the rail industry, Rail Machining is well-positioned to shape the future of rail maintenance and contribute to the continued growth and development of the global rail sector.
High-Quality Machining Parts for Optimal Performance
Title: Industry-Leading Company Paving the Way in Precision Brass Machining PartsIntroduction:In today's rapidly evolving industrial landscape, the demand for high-quality and precision machined parts continues to rise. With this in mind, one company stands tall as a leader in the industry, offering unparalleled expertise and innovation in brass machining parts. With a commitment to delivering exceptional products and dedicating themselves to customer satisfaction, this industry giant has become a go-to source for clients looking to meet their brass machining needs.[Company Name], a globally renowned manufacturer and supplier of brass machining parts, has carved a niche for itself through its dedication to excellence. With cutting-edge facilities, state-of-the-art technology, and a team of highly skilled professionals, the company has the capabilities to produce intricate and sophisticated brass components that meet the highest standards of quality.Offering a wide range of brass machining parts, [Company Name] has become a trusted partner for industries ranging from automotive and aerospace to medical and electronics. The expertise of their engineering team allows them to cater to the unique specifications and requirements of each client, ensuring precise solutions that enhance the efficiency and effectiveness of their operations.Industry-Leading Capabilities:With an unwavering commitment to technological advancements, [Company Name] has continuously invested in state-of-the-art machinery and equipment. This extensive assortment of high-precision CNC machines empowers the company to undertake complex machining projects with ease, delivering exceptional results time and again.To further enhance their capabilities, [Company Name] has established a stringent quality control system. Every brass machining part undergoes rigorous inspection and testing at various stages of the production process, guaranteeing products that exceed industry standards. By adhering to these strict quality control protocols, the company ensures the durability, precision, and reliability of every single part that they deliver.Innovation and Customization:Understanding that industries thrive on innovation, [Company Name] constantly seeks opportunities to push the boundaries of brass machining. The company's research and development team is at the forefront of exploring new materials, techniques, and processes that can enhance the functionality and performance of their brass parts.Moreover, [Company Name] places great emphasis on customization, recognizing that each client may have unique requirements. By working closely with their customers, the company tailors their brass machining parts to exact specifications, providing bespoke solutions that perfectly align with individual needs. This personalized approach enables them to create components that seamlessly integrate into clients' assembly lines, resulting in optimized productivity and seamless operations.Global Reach and Sustainable Practices:With a global footprint, [Company Name] has successfully established a strong presence in various markets around the world. By catering to the needs of diverse industries, they have built trust and credibility as a reliable partner in the field of brass machining parts manufacturing.Furthermore, [Company Name] places great importance on sustainability and environmental responsibility. In their manufacturing processes, they prioritize the use of eco-friendly materials and adhere to stringent waste management practices. By ensuring that their operations have minimal impact on the environment, they set an example for the industry and contribute towards a greener future.Conclusion:As the demand for precision brass machining parts intensifies, [Company Name] continues to lead the industry with its unwavering dedication to quality, innovation, and customer satisfaction. With a globally recognized presence, cutting-edge technology, and a commitment to sustainability, they remain steadfast in delivering the highest-quality brass machining parts that meet the evolving needs of industries around the world.
Ultimate Guide on Building Your Own CNC Router - Unleash Your Creativity
[Company Name], a leading provider of advanced industrial machinery, has recently introduced its latest product, the CNC Router. This state-of-the-art machine is designed to revolutionize the manufacturing industry by offering precision, speed, and versatility like never before.The CNC Router, short for Computer Numerical Control Router, is a computer-controlled cutting machine that combines high-speed routing and intricate cutting capabilities. This powerful tool is capable of shaping, drilling, and cutting a variety of materials, including wood, plastic, metal, and composites, with exceptional accuracy and efficiency. Its ability to work with different materials makes it a valuable asset for industries such as furniture manufacturing, sign-making, aerospace, and automotive sectors.One of the key advantages of the CNC Router is its ability to automate the manufacturing process, saving significant time and labor costs. The machine is equipped with cutting-edge software that allows users to program intricate designs and complex patterns, ensuring precise cuts and flawless finishes. This automation minimizes human error, guaranteeing consistent quality throughout the production process. Additionally, the CNC Router's speed and efficiency allow businesses to meet tight deadlines while maintaining high production volumes.The CNC Router's versatility is another remarkable feature that sets it apart from conventional cutting machines. With its multi-axis functionality, this machine can perform intricate 3D cuts and engraving, adding intricate details and unique designs to any material. Whether it is creating intricate patterns for furniture or engraving precise logos on acrylic, the CNC Router offers limitless possibilities.Furthermore, the CNC Router's user-friendly interface and intuitive software make it accessible to users of all skill levels. The machine's precision and stability are complemented by its ease of use, making it suitable for both experienced professionals and newcomers to the industry. The comprehensive training and support provided by [Company Name] ensure that customers can tap into the full potential of this cutting-edge technology.[Company Name] is dedicated to delivering top-notch products that cater to the needs of its customers. With a legacy of innovation and excellence spanning over a decade, the company has established itself as a trusted partner in the manufacturing industry. By combining cutting-edge technology with exceptional customer service, the team at [Company Name] strives to meet and exceed the expectations of its clients.The launch of the CNC Router is a testament to [Company Name]'s commitment to revolutionizing the manufacturing industry. With its advanced features, this machine has the potential to streamline production processes and empower businesses to thrive in an increasingly competitive market. By investing in the CNC Router, businesses can enhance their efficiency, productivity, and ultimately, their profitability."We are thrilled to introduce the CNC Router to the market," said [Company Name]'s CEO. "Our goal is to provide our customers with the tools they need to succeed in their respective industries. The CNC Router is a result of our relentless dedication to innovation and our understanding of the evolving needs of the manufacturing sector."As the industry continues to evolve, businesses must embrace cutting-edge technologies to stay ahead of the curve. The CNC Router offered by [Company Name] is a game-changer that ensures precision, speed, and versatility in manufacturing processes. With this advanced tool at their disposal, manufacturers can unlock new possibilities and push the boundaries of what is possible in their respective fields.In conclusion, the introduction of [Company Name]'s CNC Router promises to revolutionize the manufacturing industry. Its precision, speed, and versatility make it a valuable asset for businesses across various sectors. By harnessing the power of this groundbreaking technology, manufacturers can achieve higher levels of efficiency, quality, and productivity. With [Company Name]'s proven track record of excellence and commitment to customer satisfaction, the CNC Router is poised to become an indispensable tool for businesses worldwide.
Enhance Product Performance with Top-quality Injection Molding Inserts
Title: Innovation in Injection Molding Inserts: Enhancing Efficiency and PrecisionIntroduction (100 words)Injection molding is a widely used manufacturing process in various industries, including automotive, aerospace, consumer goods, and healthcare. As companies strive for greater efficiency and precision, the demand for innovative solutions continues to grow. Enter a leading manufacturer of injection molding inserts (brand name omitted), renowned for their cutting-edge technology and commitment to quality. With a proven track record in delivering high-performance solutions, the company has established itself as a trusted partner for numerous businesses, enabling them to achieve superior results in their manufacturing processes.8 Cutting-Edge Features of Injection Molding Inserts (600 words)1. Durability: Injection molding inserts by (brand name omitted) are made from premium-grade materials, ensuring durability and long-lasting performance. The inserts can withstand high-pressure molding operations without compromising their structural integrity, resulting in reduced maintenance costs and enhanced production efficiency.2. Precision Engineering: The inserts are meticulously designed and engineered to meet the precise specifications required by the customer. Through state-of-the-art manufacturing processes, (brand name omitted) ensures tight tolerances and uniformity, enabling flawless integration with the molding process. The result is consistently high-quality parts with minimal variations, reducing waste and optimizing productivity.3. Versatility: (Brand name omitted) offers a wide range of injection molding inserts suitable for a diverse array of applications. Whether it's intricate components for the electronics industry or robust parts for automotive manufacturing, the company's inserts cater to various needs. The flexibility in design and material selection allows customers to choose the most suitable insert for their specific requirements.4. Rapid Prototyping: Acknowledging the importance of quick turnaround times in today's competitive landscape, (brand name omitted) enables customers to rapidly prototype their designs. This not only aids in the refinement of the product but also reduces the time-to-market, giving businesses a competitive edge. The company's rapid prototyping capabilities ensure that customers can validate their designs and make necessary adjustments before moving into full-scale production.5. High Customization: (Brand name omitted) understands that every project is unique and requires specific solutions. Their injection molding inserts can be customized with various features, such as inserts with complex geometries, specialized surface finishes, or even personalized branding. This level of customization allows customers to optimize their manufacturing processes and differentiate their products in the market.6. Cost Efficiency: The company's injection molding inserts offer cost-effective solutions in terms of both initial investment and long-term production. The high-quality materials used in the inserts enhance their lifespan, ensuring fewer replacements and reduced downtime. Additionally, the precise engineering and tight tolerances contribute to minimal material waste, thereby increasing overall cost efficiency.7. Environmental Sustainability: (Brand name omitted) embraces sustainable practices by incorporating eco-friendly materials in their injection molding inserts. By utilizing recycled or biodegradable materials, the company contributes to reducing the carbon footprint. Moreover, the optimized manufacturing processes minimize waste generation, encouraging a greener approach while maintaining superior quality and performance.8. Exceptional Customer Support: (Brand name omitted) is known for its outstanding customer support throughout the entire project lifecycle. From initial product design to post-production assistance, the company's dedicated team of experts provides guidance, resolves queries, and offers technical assistance. Their commitment to customer satisfaction ensures a seamless experience for all customers.Conclusion (100 words)In an evolving manufacturing landscape, (brand name omitted) remains at the forefront of innovation in injection molding inserts. By offering a range of features such as durability, precision engineering, versatility, and cost efficiency, the company continues to provide customers with superior solutions to meet their manufacturing needs. With a commitment to environmental sustainability and exceptional customer support, (brand name omitted) consistently proves to be a reliable partner in achieving efficiency and precision in injection molding processes.
Ultimate Guide to CNC Mechanical Engineering: Unveiling the Secrets of This Revolutionary Field
Title: Revolutionizing CNC Mechanical Engineering: A Glimpse into Cutting-Edge InnovationsIntroduction:In today's fast-paced world of technology and automation, the field of CNC (Computer Numerical Control) Mechanical Engineering continues to push boundaries. With industry demands constantly evolving, companies like {} are leading the way in developing cutting-edge solutions that transform manufacturing processes. This article delves into the world of CNC Mechanical Engineering, shedding light on the vital role it plays and highlighting the innovative contributions made by {}.1. Understanding CNC Mechanical Engineering:CNC Mechanical Engineering involves the design, development, and operation of computer-controlled machinery utilized in manufacturing. These systems employ pre-programmed instructions to dictate the movement of cutting tools, thereby automating the fabrication process. By harnessing a combination of hardware and intelligent software integration, CNC machines offer exceptional precision, efficiency, and repeatability, revolutionizing industrial production.2. Pioneering Innovations by {}:{} is a renowned industry player at the forefront of CNC Mechanical Engineering advancements. With a focus on developing state-of-the-art machinery, they have consistently delivered remarkable manufacturing solutions. By embracing emerging technologies and evolving market needs, {} has demonstrated their commitment to ensuring superior performance and productivity in every aspect of their products.3. Intelligent Automation for Enhanced Efficiency:{} has successfully integrated advanced automation into their CNC machining solutions. Through the implementation of Artificial Intelligence (AI) and Machine Learning (ML) algorithms, their machines can analyze and optimize manufacturing processes in real-time. This results in enhanced efficiency, reduced material wastage, and superior quality control. The intelligent automation offered by {} is a game-changer in the field, streamlining operations for manufacturers worldwide.4. Sustainable Manufacturing Practices:In an era where sustainability is paramount, {} has pioneered eco-conscious manufacturing technologies within the CNC Mechanical Engineering domain. By incorporating energy-efficient components, optimizing material usage, and reducing waste generation, their machines contribute to a greener manufacturing ecosystem. {}'s commitment to sustainability underscores their dedication to responsible business practices and a more sustainable future.5. Industry 4.0 Integration:Remaining at the forefront of industry trends, {} has embraced the concept of Industry 4.0, the fourth industrial revolution. By interconnecting CNC machines, data analysis systems, and intelligent software, they have created a fully digitalized and interconnected manufacturing environment. This seamless integration enables real-time data sharing, predictive maintenance, and remote accessibility, revolutionizing traditional production processes.6. Disruptive Additive Manufacturing Solutions:In addition to traditional subtractive manufacturing techniques, {} has ventured into additive manufacturing, commonly known as 3D printing. The company's additive manufacturing solutions offer unparalleled design flexibility, reduced material waste, and faster prototyping capabilities. {}'s foray into the realm of 3D printing exemplifies their commitment to pushing boundaries and exploring new frontiers in CNC Mechanical Engineering.7. Global Impact and Collaborations:{}'s innovative solutions have made a significant impact on the global manufacturing landscape. By collaborating with industry partners, research institutions, and universities, they strive to foster a culture of knowledge exchange and collective growth. These collaborative efforts have not only contributed to breakthroughs in CNC Mechanical Engineering but have also propelled the industry as a whole towards greater heights.Conclusion:In the ever-evolving world of CNC Mechanical Engineering, {} stands as a beacon of innovation and excellence. Their relentless pursuit of cutting-edge solutions has revolutionized manufacturing processes, introducing intelligent automation, sustainable practices, and additive manufacturing techniques. By embracing Industry 4.0 and collaborating with stakeholders worldwide, {} continues to shape the future of CNC Mechanical Engineering, driving industry advancements and inspiring manufacturers to embark on a path of transformation.
Discover the Latest Advancements in the Foundry Process for Superior Results
Title: Innovations in Foundry Process Revolutionize the Manufacturing IndustryIntroduction:The foundry process plays a pivotal role in the manufacturing industry, allowing for the production of various components across diverse sectors. Today, we highlight the latest advancements in the foundry process, spearheaded by a leading company, and how they are transforming the industry landscape. (Please remove brand name from the introduction)Industry Overview:The manufacturing industry depends on the foundry process to produce components that are integral to numerous sectors such as automotive, aerospace, construction, and many more. Traditional foundry methods have relied on labor-intensive processes, which often resulted in slower production and increased costs. However, with the advent of innovative technologies and continuous research and development, the foundry process has witnessed a significant transformation.Advancements in Foundry Process:Leading the charge in revolutionizing the foundry process is a renowned company (Please remove brand name) that has pioneered several innovative techniques to streamline and enhance manufacturing efficiency. By leveraging cutting-edge technologies like Artificial Intelligence (AI), Internet of Things (IoT), and automation, the company has been able to achieve faster turnaround times, improved quality, and reduced costs.One of the key breakthroughs introduced by the company is the implementation of AI-driven predictive modeling techniques. By analyzing vast amounts of data, the system can accurately forecast potential defects and optimize casting parameters to minimize issues during the production process. This not only eliminates costly rework but also significantly reduces the time required for quality control, thereby expediting the overall manufacturing cycle.Furthermore, the integration of IoT in the foundry process has enabled real-time monitoring of crucial production parameters. Sensors embedded throughout the production line continuously gather data related to temperature, pressure, and other relevant factors. This data is then transmitted to a centralized system, which allows for immediate analysis and identification of any deviations or anomalies. Consequently, prompt corrective actions can be taken, ensuring that the casting process remains consistent and compliant with the required specifications throughout production.Automation has also played a vital role in optimizing the foundry process. With the introduction of robotics and advanced machinery, tasks that were previously labor-intensive and prone to human error can now be executed with precision and efficiency. The incorporation of robotics enables tasks such as mold preparation, pouring, and post-processing to be carried out with minimal human intervention, resulting in higher production speeds and improved accuracy.The company's commitment to sustainable manufacturing practices has also been influential in advancing the foundry process. By exploring eco-friendly raw materials and implementing efficient energy consumption methods, they have successfully reduced the environmental impact associated with the production process. These measures help meet the rising demand for sustainable manufacturing while ensuring that the components manufactured maintain the highest quality standards.Conclusion:The foundry process is undergoing a remarkable transformation, thanks to the continuous endeavors of a renowned company (Please remove brand name). Through the integration of AI, IoT, and automation, they have successfully optimized production efficiency, reduced costs, increased the quality of components, and contributed to sustainable manufacturing practices. As the industry witnesses the positive impacts of these innovative advancements, it is evident that the foundry process will continue to evolve and play a vital role in the manufacturing landscape.
How Material Casting is Revolutionizing the Manufacturing Industry
[Please provide more specific details about the company you want to introduce so that I can provide a more accurate and tailored news article.]
The Ultimate Guide to Efficient Cnc Fixture Design for Manufacturing Success
Title: Innovative CNC Fixture Design Revolutionizes Manufacturing ProcessesIntroduction:In a breakthrough development within the manufacturing industry, an innovative CNC fixture design is set to transform production processes, providing greater efficiency, accuracy, and versatility. This cutting-edge technology marks a significant milestone in manufacturing, empowering companies to improve their productivity and competitiveness in the global market.The Company's Vision:Born out of a deep passion for revolutionizing the manufacturing domain, the company behind this groundbreaking CNC fixture design aims to redefine industry norms. Their team of experienced engineers and technicians have dedicated years of research and development to create this state-of-the-art technology, which promises to streamline operations and enhance overall production quality.The CNC Fixture Design:This remarkable CNC fixture design incorporates a myriad of advanced features that address the challenges of traditional fixture designs. It leverages the latest technologies, including adaptive control systems and intelligent sensor integration, to optimize machining processes and improve the overall user experience.One of the key highlights of this fixture design is its modular approach, allowing for versatile application across various production requirements. The ability to quickly adjust and reconfigure the fixture greatly enhances manufacturing flexibility, saving precious time and resources. Furthermore, the design includes built-in error detection mechanisms, minimizing defects and ensuring consistent, high-quality output.Another noteworthy aspect of this CNC fixture design is its emphasis on ergonomics and operator safety. The system integrates user-friendly interfaces, intuitive controls, and enhanced safety features, reducing the risk of accidents and promoting a seamless work environment.Industry Impact:The introduction of this advanced CNC fixture design is poised to revolutionize manufacturing practices across a wide range of industries. From automotive and aerospace to electronics and medical devices, the versatility and adaptability of this technology make it applicable to numerous sectors.The increased efficiency and accuracy offered by this fixture design will open up new possibilities for manufacturers. It allows for more complex and intricate designs, shorter production cycles, and greater cost-effectiveness. Companies can expect to witness significant improvements in product quality, reduced downtime, and enhanced overall profitability.Furthermore, this CNC fixture design aligns with the ongoing industry trend towards automation and digitization. Its integrated smart systems enable seamless data collection, analysis, and real-time adjustments, contributing to improved productivity and competitiveness on a global scale.Future Prospects:The company behind this CNC fixture design remains committed to continuous innovation and technological advancements. They are actively exploring partnerships with manufacturers seeking to enhance their production capabilities. The aim is to collaborate closely with industry leaders to customize and optimize the design according to specific needs, ensuring a seamless integration of this technology into existing processes.Moreover, through ongoing research and development efforts, the company plans to expand the capabilities of the CNC fixture design further. This includes exploring advancements in materials, sensors, and automation, as well as integrating artificial intelligence and machine learning technologies.Conclusion:As the manufacturing industry embraces the era of automation and digitization, this revolutionary CNC fixture design promises to redefine traditional production methods. With its emphasis on efficiency, accuracy, versatility, and safety, this technology will undoubtedly revolutionize manufacturing processes in diverse sectors. As this innovative solution gains momentum, manufacturers can look forward to a new era of optimized productivity, improved product quality, and sustained growth in a highly competitive global market.