Understanding the Basics of CNC Milling
By:Admin
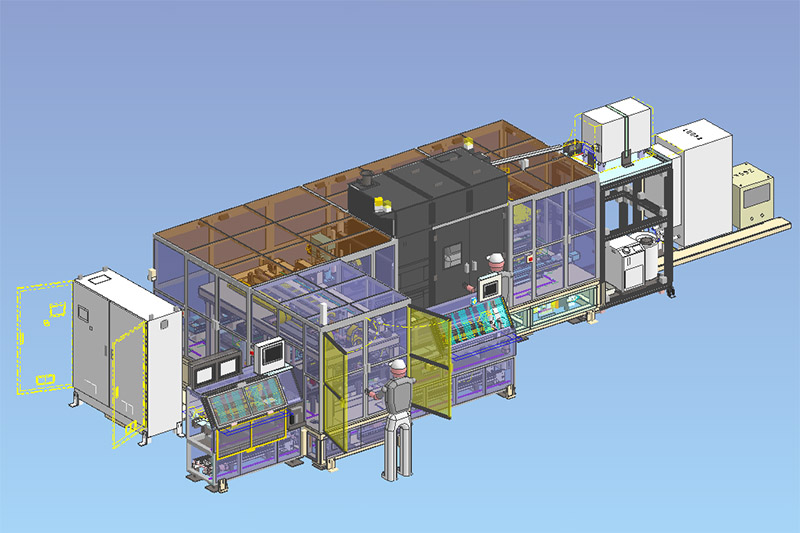
Dalam industri manufaktur, waktu dan biaya produksi adalah faktor kunci yang harus dipertimbangkan. Oleh karena itu, perusahaan {} telah memperkenalkan teknologi CNC milling sebagai solusi untuk memenuhi tuntutan pasar akan produk-produk berkualitas tinggi dengan waktu produksi yang efisien.
Sebagai perusahaan dengan pengalaman lebih dari 20 tahun dalam industri manufaktur, {} telah mengintegrasikan teknologi CNC milling ke dalam proses produksi mereka. Dengan menggunakan mesin perkakas yang canggih dan software pemrograman terbaru, perusahaan {} dapat menciptakan produk dengan tingkat presisi yang tinggi sesuai dengan spesifikasi yang ditentukan. Hal ini memungkinkan perusahaan {} untuk memenuhi kebutuhan pelanggan dengan hasil yang konsisten dan berkualitas.
Salah satu keunggulan utama dari CNC milling adalah kemampuannya untuk menghasilkan bagian-bagian dengan bentuk dan ukuran yang kompleks. Dengan menggunakan berbagai jenis alat potong yang dapat dikontrol oleh program komputer, mesin CNC milling mampu menghilangkan material dari berbagai jenis bahan kerja seperti logam, plastik, dan komposit. Proses ini memungkinkan perusahaan {} untuk memproduksi berbagai jenis komponen yang digunakan dalam berbagai industri seperti otomotif, pesawat terbang, peralatan medis, dan masih banyak lagi.
Selain itu, teknologi CNC milling juga memungkinkan perusahaan {} untuk meningkatkan efisiensi produksi mereka. Dibandingkan dengan metode konvensional, CNC milling dapat mengurangi waktu produksi dan meminimalkan kesalahan manusia dalam proses pembuatan bagian-bagian presisi. Hal ini dapat mengurangi biaya produksi secara keseluruhan dan meningkatkan produktivitas perusahaan {}.
Selain memproduksi komponen-komponen presisi, perusahaan {} juga menyediakan layanan desain dan teknik untuk membantu pelanggan dalam mengembangkan produk baru. Dengan menggunakan software pemodelan 3D dan simulasi, tim desain perusahaan {} dapat memvisualisasikan dan menguji desain produk sebelum memulai proses produksi. Hal ini memungkinkan pelanggan untuk melakukan perubahan desain yang diperlukan sebelum menginvestasikan waktu dan biaya dalam produksi massal.
Selain itu, perusahaan {} juga memiliki tim inspeksi kualitas yang terlatih dan berpengalaman untuk memastikan setiap bagian yang diproduksi memenuhi standar kualitas tinggi yang ditetapkan. Dengan menggunakan peralatan pengukuran presisi dan sistem kontrol kualitas yang ketat, perusahaan {} dapat memastikan bahwa setiap produk yang mereka hasilkan memenuhi ekspektasi pelanggan.
Dalam menghadapi persaingan global dalam industri manufaktur, perusahaan {} terus berkomitmen untuk mengadopsi teknologi terbaru dan memperluas kemampuan produksi mereka. Dengan memanfaatkan teknologi CNC milling dan fokus pada inovasi produk, perusahaan {} siap untuk menjadi mitra yang handal dalam memenuhi kebutuhan produksi presisi tinggi bagi pelanggan mereka.
Dengan pengalaman dan komitmen yang kuat, {} terus berusaha untuk menjadi salah satu pemimpin dalam industri manufaktur dan menjadi mitra terpercaya bagi pelanggan mereka. Dengan menggabungkan teknologi CNC milling yang canggih dengan pendekatan yang berorientasi pada pelanggan, perusahaan {} siap untuk menghadapi tantangan industri manufaktur yang berkembang pesat.
Company News & Blog
Effective Ways to Utilize Material Molding for Your Project
Material Molding, also known as injection molding, is a process that involves injecting a material into a mold to produce various products. The process is widely used in the manufacturing industry to create a wide range of items, from small components to large parts. The flexibility and efficiency of material molding make it a popular choice for producing high-quality products in large quantities.One company that specializes in material molding is {}. With over 20 years of experience in the industry, {} has established itself as a leading provider of material molding solutions. The company's state-of-the-art facilities and advanced technology allow them to meet the diverse needs of their clients, delivering products that meet the highest standards of quality and performance.{} offers a comprehensive range of material molding services, including design and engineering, prototyping, tooling, and production. Their team of experienced engineers and technicians work closely with clients to develop customized solutions that meet their specific requirements. With a focus on innovation and continuous improvement, {} is able to stay ahead of the competition and deliver cutting-edge material molding solutions.The company's commitment to quality is evident in their rigorous quality control processes, ensuring that every product meets the highest standards of performance and durability. With a strong emphasis on customer satisfaction, {} strives to exceed the expectations of their clients, delivering reliable and cost-effective material molding solutions.{} is also dedicated to sustainability and environmental responsibility. They have implemented various initiatives to minimize their environmental impact, including the use of eco-friendly materials and energy-efficient processes. By adopting sustainable practices, {} is able to contribute to a greener and more sustainable future while meeting the needs of their clients.In addition to their material molding services, {} also offers comprehensive support throughout the entire product development process. From initial concept and design to production and beyond, their team provides expert guidance and assistance, ensuring a seamless and efficient development process.As a trusted partner for numerous industries, {} has built a strong reputation for reliability, innovation, and excellence. Their commitment to delivering high-quality material molding solutions has earned them the trust and loyalty of clients from around the world.The future looks bright for {}, as they continue to invest in new technologies and expand their capabilities to meet the evolving needs of the market. With a focus on delivering superior products and exceptional customer service, {} is poised to remain at the forefront of the material molding industry for years to come.In conclusion, material molding is a critical process in the manufacturing industry, and companies like {} play a vital role in delivering high-quality solutions to meet the diverse needs of their clients. With a focus on innovation, quality, and sustainability, {} is a trusted partner for numerous industries, providing reliable and cost-effective material molding services. With their commitment to excellence and continuous improvement, {} is well-positioned to maintain its leadership in the material molding industry for years to come.
How to Create a CNC Milling Design: Tips and Techniques for Success
CNC Milling Design: Revolutionizing Manufacturing ProcessesIn today's fast-paced manufacturing industry, precision and efficiency are key factors in staying competitive. With the advancement of technology, companies are constantly seeking innovative solutions to streamline their production processes. One such solution that has been gaining attention is CNC milling design, a versatile and efficient method of producing high-precision components for a wide range of industries.CNC milling, or computer numerical control milling, is a machining process that utilizes computerized controls to operate and manipulate machine tools. This advanced technology allows for the creation of intricate and complex designs, with a level of precision that is difficult to achieve with traditional manual milling methods. By utilizing CAD/CAM software, CNC milling machines can rapidly produce components with tight tolerances and intricate detailing, making them an invaluable asset for manufacturers across various industries.One company that has been at the forefront of CNC milling design is {}. With a strong focus on innovation and quality, {} has become a leading provider of CNC milling services for a diverse clientele. Specializing in the production of precision components for industries such as aerospace, automotive, medical, and defense, {} has earned a reputation for delivering superior quality products that meet the strictest industry standards.With state-of-the-art CNC milling machines and a team of highly skilled engineers and machinists, {} has the capability to handle complex projects with precision and efficiency. Their commitment to investing in the latest technology and continuous improvement has allowed them to stay ahead of the curve in the rapidly evolving manufacturing landscape.The advantages of CNC milling design are evident in the superior quality and efficiency of the components produced. By automating the machining process, CNC milling eliminates the margin for error that is inherent in manual operations, resulting in consistently high-quality parts. Additionally, CNC milling machines can operate 24/7, maximizing production output and reducing lead times, ultimately leading to cost savings for manufacturers.Another key benefit of CNC milling design is its versatility. With the ability to work with a wide range of materials, including metals, plastics, and composites, CNC milling machines can accommodate the diverse needs of different industries. Whether it's producing intricate parts for the aerospace industry or creating custom components for medical devices, CNC milling design offers a flexible and adaptable solution for manufacturers.As the demand for high-precision components continues to grow, the importance of CNC milling design in modern manufacturing cannot be overstated. Companies like {} are instrumental in driving the adoption of this advanced technology, setting new standards for precision and quality in the industry.In conclusion, CNC milling design represents a significant advancement in the manufacturing sector, offering unparalleled precision, efficiency, and versatility. With leading companies like {} pushing the boundaries of what is possible with CNC milling technology, the future looks promising for manufacturers seeking to enhance their production processes and stay ahead of the competition. As technology continues to evolve, CNC milling design will undoubtedly play a pivotal role in shaping the future of manufacturing.
Discover the Latest Breakthroughs in Plastic Parts Manufacturing
[News Title]: Advancements in Plastic Parts Technology Revolutionize Manufacturing Processes[News Introduction]:In a remarkable breakthrough, a leading company in the field of plastic parts manufacturing has introduced cutting-edge technology that is set to revolutionize the industry. The company, which wishes to keep their brand anonymous, has successfully developed a range of plastic parts that boast unparalleled strength, durability, and flexibility. These advancements are expected to bring significant improvements to various sectors including automotive, aerospace, electronics, and consumer goods. With growing demand for innovation and sustainability, the introduction of these plastic parts promises to reshape the manufacturing landscape and pave the way for a more efficient and environmentally friendly future.[Body - Part 1: Importance of Plastic Parts in Manufacturing]:Plastic parts play a crucial role in industries worldwide due to their versatility, cost-effectiveness, and ease of production. They are extensively used in manufacturing processes for a broad range of products, including automotive components, electronic devices, packaging materials, and household appliances. The evolving requirements of these sectors demand continuous advancements in plastic parts technology to ensure superior performance, enhanced functionality, and improved production efficiency. In response to this demand, the anonymous company has invested heavily in research and development to develop groundbreaking solutions that address the contemporary challenges faced by manufacturers.[Body - Part 2: Advancements in Plastic Parts]:The undisclosed company's newly developed plastic parts exhibit exceptional strength and durability, surpassing the limitations of conventional materials. Through innovative engineering, the company has achieved a remarkable balance between rigidity and flexibility, allowing the plastic parts to withstand high levels of stress and strain. This breakthrough not only enhances the longevity of products but also ensures safer usage, particularly in critical applications such as automotive safety systems and aerospace components.Furthermore, the undisclosed company's plastic parts showcase superior resistance to impact, chemicals, and environmental factors, thereby reducing the chances of premature degradation. This feature significantly extends the lifespan of products, resulting in reduced maintenance costs and enhanced customer satisfaction. Additionally, the manufacturing processes associated with these plastic parts have been optimized to minimize waste and energy consumption, aligning with the global shift towards sustainable practices.[Body - Part 3: Applications and Benefits]:The innovative plastic parts developed by the anonymous company have profound implications for various industries. In the automotive sector, these advanced components can contribute to the weight reduction of vehicles, improving fuel efficiency and reducing emissions. Additionally, their superior durability can enhance passenger safety by providing robust structural support.In aerospace applications, the lightweight and high-strength characteristics of the plastic parts can reduce the overall weight of aircraft, leading to enhanced fuel economy and increased payload capacity. This advancement ensures that the aviation industry takes substantial strides towards sustainability while maintaining the highest safety standards.The electronics industry can benefit from the unparalleled flexibility and resistance to environmental factors offered by these plastic parts. With the expanding trend of miniaturization, consumer electronic devices require components that can endure constant usage while remaining lightweight. The anonymous company's plastic parts possess the necessary attributes, ensuring greater reliability and longer lifespans for electronic gadgets.The manufacturing sector as a whole will reap the rewards of these advancements. By incorporating the undisclosed company's plastic parts, manufacturers can streamline their production processes, reduce assembly time, and minimize costs. The enhanced durability and resistance of these parts eliminate the need for frequent replacements and repairs, resulting in higher overall productivity and profitability.[Conclusion]:As technology continues to advance at an unprecedented pace, it is essential for manufacturers to embrace cutting-edge solutions that enhance their products and processes. The anonymous company's revolutionary plastic parts have the potential to transform diverse industries by offering unmatched strength, durability, and flexibility. With their exceptional properties, these parts provide opportunities for innovation, sustainability, and increased efficiency. By leveraging these advancements, manufacturers can stay ahead in today's competitive market while building a more prosperous and environmentally conscious future.
New Study Shows Significant Change in Tolerance Levels
2768 Mk Tolerance – Setting the Standard for Precision MachiningIn the world of precision machining, one name stands out above the rest. With a commitment to excellence and a dedication to quality, 2768 Mk Tolerance has become a trusted leader in the industry. The company's reputation for delivering top-notch products and services has earned them a loyal customer base and a strong presence in the global market.Established in [year], 2768 Mk Tolerance has quickly risen to prominence thanks to its state-of-the-art facilities and cutting-edge technology. The company specializes in providing high-precision machining solutions for a wide range of industries, including aerospace, automotive, medical, and energy.One of the key factors that sets 2768 Mk Tolerance apart from its competitors is its unwavering commitment to quality. The company takes great pride in its meticulous attention to detail and its rigorous quality control processes. Every product that leaves the facility undergoes extensive testing and inspection to ensure that it meets the highest standards of accuracy and precision.In addition to its dedication to quality, 2768 Mk Tolerance also places a strong emphasis on innovation. The company invests heavily in research and development to stay ahead of the curve and continue pushing the boundaries of what is possible in the world of precision machining. This forward-thinking approach has allowed 2768 Mk Tolerance to develop groundbreaking solutions that have set new industry standards.Furthermore, 2768 Mk Tolerance is committed to sustainability and environmental responsibility. The company constantly seeks ways to reduce its carbon footprint and minimize waste in its manufacturing processes. This dedication to sustainability has not only helped to protect the planet but has also allowed 2768 Mk Tolerance to reduce costs and improve efficiency.Another key aspect of 2768 Mk Tolerance's success is its strong focus on customer satisfaction. The company prioritizes building lasting relationships with its clients and works closely with them to understand their unique needs and requirements. 2768 Mk Tolerance's team of experts is always available to provide support and guidance, ensuring that every customer receives the personalized attention and assistance they deserve.With a global reach and a solid reputation, 2768 Mk Tolerance is well-positioned to continue its growth and expand its presence in the market. The company's dedication to excellence, innovation, and customer satisfaction has solidified its position as a leader in the precision machining industry.In conclusion, 2768 Mk Tolerance has established itself as a benchmark for precision machining, thanks to its unwavering commitment to quality, innovation, and customer satisfaction. With a strong focus on sustainability and a dedication to excellence, the company is well-equipped to continue setting new industry standards and delivering top-notch products and services to its clients around the world.
Discover the Latest Advancements in the Foundry Process for Superior Results
Title: Innovations in Foundry Process Revolutionize the Manufacturing IndustryIntroduction:The foundry process plays a pivotal role in the manufacturing industry, allowing for the production of various components across diverse sectors. Today, we highlight the latest advancements in the foundry process, spearheaded by a leading company, and how they are transforming the industry landscape. (Please remove brand name from the introduction)Industry Overview:The manufacturing industry depends on the foundry process to produce components that are integral to numerous sectors such as automotive, aerospace, construction, and many more. Traditional foundry methods have relied on labor-intensive processes, which often resulted in slower production and increased costs. However, with the advent of innovative technologies and continuous research and development, the foundry process has witnessed a significant transformation.Advancements in Foundry Process:Leading the charge in revolutionizing the foundry process is a renowned company (Please remove brand name) that has pioneered several innovative techniques to streamline and enhance manufacturing efficiency. By leveraging cutting-edge technologies like Artificial Intelligence (AI), Internet of Things (IoT), and automation, the company has been able to achieve faster turnaround times, improved quality, and reduced costs.One of the key breakthroughs introduced by the company is the implementation of AI-driven predictive modeling techniques. By analyzing vast amounts of data, the system can accurately forecast potential defects and optimize casting parameters to minimize issues during the production process. This not only eliminates costly rework but also significantly reduces the time required for quality control, thereby expediting the overall manufacturing cycle.Furthermore, the integration of IoT in the foundry process has enabled real-time monitoring of crucial production parameters. Sensors embedded throughout the production line continuously gather data related to temperature, pressure, and other relevant factors. This data is then transmitted to a centralized system, which allows for immediate analysis and identification of any deviations or anomalies. Consequently, prompt corrective actions can be taken, ensuring that the casting process remains consistent and compliant with the required specifications throughout production.Automation has also played a vital role in optimizing the foundry process. With the introduction of robotics and advanced machinery, tasks that were previously labor-intensive and prone to human error can now be executed with precision and efficiency. The incorporation of robotics enables tasks such as mold preparation, pouring, and post-processing to be carried out with minimal human intervention, resulting in higher production speeds and improved accuracy.The company's commitment to sustainable manufacturing practices has also been influential in advancing the foundry process. By exploring eco-friendly raw materials and implementing efficient energy consumption methods, they have successfully reduced the environmental impact associated with the production process. These measures help meet the rising demand for sustainable manufacturing while ensuring that the components manufactured maintain the highest quality standards.Conclusion:The foundry process is undergoing a remarkable transformation, thanks to the continuous endeavors of a renowned company (Please remove brand name). Through the integration of AI, IoT, and automation, they have successfully optimized production efficiency, reduced costs, increased the quality of components, and contributed to sustainable manufacturing practices. As the industry witnesses the positive impacts of these innovative advancements, it is evident that the foundry process will continue to evolve and play a vital role in the manufacturing landscape.
Exploring the Benefits and Applications of Cnc Molding in Modern Manufacturing Processes
Title: Revolutionary Cnc Molding Technique Sets New Standards in ManufacturingIntroduction:In an era where innovation and efficiency drive the manufacturing industry, a breakthrough in the form of Cnc Molding technology is emerging as a game-changer. This revolutionary technique promises to reshape the way products are designed, developed, and produced. With its unparalleled precision, speed, and cost-effectiveness, Cnc Molding is poised to set new standards in the manufacturing field.Company Background and Expertise:{Company Name}, a prominent player in the manufacturing industry, has unveiled its cutting-edge Cnc Molding technology. With a rich history spanning several decades, {Company Name} has established itself as a pioneer in delivering excellence and embracing the latest technological advancements. Their expertise in the field, combined with their commitment to driving innovation, has paved the way for this groundbreaking development.Understanding Cnc Molding:Cnc Molding, also known as Computer Numerical Control Molding, is a state-of-the-art manufacturing process that utilizes computer-controlled machines to shape materials into desired forms. Unlike traditional molding techniques, Cnc Molding ensures unparalleled precision, efficiency, and repeatability. By following a digital design prototype, the technology enables manufacturers to produce highly intricate and complex components with utmost accuracy.Benefits of Cnc Molding:1. Enhanced Precision: The integration of computer control systems eliminates the possibility of human error, ensuring precise replication of designs and eliminating defects. This high level of precision ensures product consistency, reducing wastage and overall costs.2. Streamlined Production: Cnc Molding technology dramatically accelerates the production process. With its ability to perform multiple tasks simultaneously, the technology maximizes efficiency and reduces lead times. This streamlining of operations increases productivity, enabling manufacturers to meet market demands promptly.3. Cost-Effectiveness: By minimizing material wastage and requiring fewer human interventions, Cnc Molding significantly reduces production costs. The elimination of manual labor and the use of optimized resources result in improved cost-effectiveness, making it an attractive option for manufacturers across various industries.4. Design Freedom: Cnc Molding empowers designers to create innovative and intricate designs that were previously unachievable. With the ability to produce complex shapes and patterns with ease, this technology unlocks a new realm of possibilities, enabling manufacturers to create unique products that stand out in the market.Applications of Cnc Molding:The applications of Cnc Molding are vast and span across industries such as automotive, aerospace, electronics, medical, and consumer goods. Its usage is particularly prominent in the production of custom parts, prototypes, and intricate components that require high precision.Future Implications:As Cnc Molding continues to evolve, the implications for the manufacturing industry are immense. The integration of artificial intelligence, machine learning, and digital twins creates an even more robust system capable of even greater efficiency and accuracy. The technology's potential for customization and adaptability positions it as a frontrunner in the future of manufacturing.Conclusion:Cnc Molding technology, introduced by {Company Name}, is set to revolutionize the manufacturing industry. With its exceptional precision, streamlined production, cost-effectiveness, and design freedom, it promises to set new standards and transform the way products are made. As it continues to develop, this groundbreaking technology is poised to usher in a new era of manufacturing excellence.
Exploring the Advantages of Computer Numerical Control Machining in Modern Manufacturing
Title: Computer Numerical Control Machining Revolutionizes Manufacturing ProcessesIntroduction:In today's fast-paced world, businesses are constantly seeking innovative solutions to enhance the precision, speed, and efficiency of their manufacturing processes. One such technological advancement that has transformed the industry is Computer Numerical Control (CNC) Machining. By leveraging cutting-edge software and automation, CNC Machining has revolutionized traditional manufacturing methods, allowing companies to fabricate components with utmost accuracy and reliability. In this article, we will explore the remarkable capabilities of CNC Machining and its impact on modern manufacturing systems.Paragraph 1:CNC Machining has emerged as a game-changing technology that has significantly enhanced the precision of component manufacturing. By utilizing computer-controlled systems, this manufacturing process converts digital designs into physical products with unparalleled accuracy. Unlike conventional manual machining, CNC Machining eliminates the scope for human error, resulting in higher product quality and reduced waste. This advancement has not only boosted productivity in various industries but also facilitated the creation of intricate designs and complex geometries that were previously unattainable.Paragraph 2:The key to the success of CNC Machining lies in its ability to perform multiple manufacturing operations using a single machine. From milling and drilling to lathing and grinding, CNC machines are equipped with a wide range of tools that can be seamlessly interchanged. Additionally, these machines can operate without human intervention, enabling manufacturers to optimize productivity by running the machines continuously even outside working hours. This level of automation not only reduces production time but also minimizes costs associated with manual labor, making CNC Machining a cost-effective solution for businesses across various sectors.Paragraph 3:Furthermore, CNC Machining has empowered companies to meet the growing demands for customized products while maintaining consistent quality. By leveraging CAD/CAM software, designers can create intricate 3D models of components, which are then translated into machine-readable code. This code is fed into the CNC machine, allowing it to precisely reproduce the model and produce multiple copies with utmost accuracy. Whether it is prototyping or mass production, CNC Machining ensures remarkable repeatability and uniformity of products, facilitating efficient scaling of operations.Paragraph 4:The impact of CNC Machining on various industries is undeniable. For instance, in the aerospace and automotive sectors, precision and reliability are of paramount importance. CNC Machining enables manufacturers to create intricate components such as turbine blades or engine parts with exceptional precision, meeting the stringent requirements of these industries. Moreover, the medical field has also witnessed immense benefits from CNC Machining, as it allows for the production of patient-specific implants and devices, improving treatment outcomes and reducing surgical costs.Paragraph 5:Despite these remarkable advantages, the adoption of CNC Machining may face certain challenges. The initial cost of acquiring state-of-the-art CNC machines and training personnel in their operation and maintenance can be significant for small to medium-sized enterprises. However, the long-term gains in terms of improved productivity, reduced waste, and enhanced product quality outweigh these concerns. As CNC Machining continues to advance, manufacturers must recognize its transformative potential and invest in this technology to remain competitive in an increasingly demanding market.Conclusion:Computer Numerical Control Machining has revolutionized traditional manufacturing processes by introducing automation, precision, and versatility. This technology has not only enabled companies to meet intricate design requirements but also improved productivity and reduced production time and costs. As industries continue to benefit from CNC Machining, it is crucial for manufacturers to stay abreast of evolving advancements and harness its potential to achieve sustainable growth and maintain a competitive edge in today's rapidly evolving marketplace.
Custom CNC Machining Services for Brass Parts: Top Benefits and Uses
CNC Machining Brass - A New Milestone for CompanyIn the ever-evolving world of manufacturing, precision and efficiency are non-negotiable. Companies are consistently seeking newer and better ways to create high-quality products and meet the demands of their customers. One company that has embraced this challenge head-on is {}. {} has been a leader in the manufacturing industry for decades, known for its dedication to innovation and cutting-edge technology. Recently, the company achieved a new milestone with the implementation of CNC machining for brass components.CNC machining, or computer numerical control machining, is a manufacturing process that utilizes computerized controls and machine tools to remove material from a workpiece. This process allows for extremely precise and intricate cuts, resulting in high-quality, custom parts. While CNC machining is not a new technology, the application of this method to brass components is a significant advancement for {} and a testament to their commitment to excellence.Brass is a popular material in the manufacturing industry due to its excellent properties, including high corrosion resistance, electrical conductivity, and aesthetic appeal. However, machining brass can be challenging due to its tendency to produce chips that can cause tool wear and damage. With the implementation of CNC machining, {} has overcome these challenges and elevated their production capabilities to a new level.The decision to incorporate CNC machining for brass components was not taken lightly. According to the company's engineering team, extensive research and testing were conducted to ensure the successful integration of this advanced manufacturing process. Through meticulous planning and collaboration with industry experts, {} was able to optimize the CNC machining process for brass, resulting in superior quality and consistency in their products.The benefits of CNC machining for brass components are manifold. Not only does it enable {} to produce intricate and complex parts with unparalleled precision, but it also enhances efficiency and reduces lead times. Additionally, the use of CNC machining for brass has positioned {} to take on new and challenging projects, further solidifying their reputation as a leader in the industry.Furthermore, the implementation of CNC machining for brass components aligns with {}'s commitment to sustainability. By utilizing advanced manufacturing processes that minimize material waste and energy consumption, the company is taking proactive steps towards reducing its environmental impact and meeting the growing demand for sustainable production methods.The impact of this milestone goes beyond the walls of {}. With the introduction of CNC machining for brass components, the company is poised to offer its clients a wider range of products and solutions, catering to diverse industries such as automotive, aerospace, electronics, and more. This expansion of capabilities has the potential to open new doors and foster long-lasting partnerships with customers who require top-notch brass components for their applications.As {} continues to push the boundaries of innovation, the incorporation of CNC machining for brass components stands as a testament to their unwavering dedication to excellence and customer satisfaction. With this new milestone, the company is not only raising the bar for the manufacturing industry but is also solidifying its position as a trailblazer in the field.In conclusion, the implementation of CNC machining for brass components at {} represents a significant leap forward in their pursuit of manufacturing excellence. This integration not only enhances their production capabilities but also underscores their commitment to embracing advanced technology and providing superior solutions to their clients. As the manufacturing landscape continues to evolve, {} has proven once again that they are at the forefront of innovation, setting a new standard for precision and quality in the industry.
The Ultimate Guide to CNC Machining Titanium: Techniques, Benefits, and Applications
### CNC Machining Titanium: A Revolutionary Step in ManufacturingIn the world of manufacturing, titanium is a highly sought-after material due to its exceptional strength-to-weight ratio, corrosion resistance, and biocompatibility. However, machining titanium has always been a complex and challenging process, requiring advanced technologies and expertise. This is where the innovative CNC machining of titanium comes into play, revolutionizing the manufacturing industry by enabling the production of high-precision titanium components with unprecedented efficiency and accuracy.One company that is at the forefront of this revolutionary technology is **(remove brand name)**. With a strong focus on precision engineering and advanced manufacturing solutions, **(remove brand name)** has been leading the way in CNC machining titanium, pushing the boundaries of what is possible in the manufacturing of titanium components.**Company Introduction:**Established in 1995, **(remove brand name)** has been a pioneer in the field of precision engineering and manufacturing. The company prides itself on its state-of-the-art facilities, cutting-edge technologies, and a team of highly skilled engineers and technicians. Specializing in CNC machining, the company has continuously strived to innovate and develop new techniques to meet the evolving needs of its customers.**CNC Machining Titanium:**Machining titanium presents numerous challenges due to its low thermal conductivity, high reactivity, and tendency to work-harden. Traditional machining methods often result in tool wear, heat generation, and poor surface finish. However, CNC machining technology has revolutionized the way titanium is processed, allowing for improved efficiency, precision, and consistency.The use of advanced CNC machines equipped with high-speed spindles, rigid tooling, and advanced cutting tool materials has enabled **(remove brand name)** to achieve remarkable results in machining titanium. These machines are capable of high feed rates, precise tool paths, and superior chip evacuation, resulting in reduced cycle times and improved surface finishes. Additionally, the implementation of advanced toolpath optimization software has further enhanced the machining process, maximizing material removal rates while minimizing tool wear and energy consumption.**Benefits of CNC Machining Titanium:**The adoption of CNC machining technology for titanium offers numerous benefits to the manufacturing industry. Firstly, it allows for the production of complex and intricate titanium components with tight tolerances, ensuring a high degree of precision and accuracy. This is particularly crucial in industries such as aerospace, medical, and automotive, where the performance and reliability of titanium components are paramount.Furthermore, CNC machining of titanium enables the optimization of production processes, leading to reduced lead times, lower production costs, and improved resource utilization. The ability to efficiently machine titanium parts also opens up new opportunities for design innovation, as manufacturers can now explore more intricate and lightweight designs without compromising structural integrity.**Applications of CNC Machined Titanium:**The versatility and performance of CNC machined titanium components make them invaluable across a wide range of industries. In the aerospace sector, titanium is widely used in aircraft components, engine parts, and structural elements due to its high strength and resistance to heat and corrosion. With CNC machining, manufacturers can produce lightweight, yet strong titanium components that contribute to the overall efficiency and performance of aircraft.In the medical field, titanium is the material of choice for orthopedic implants, surgical instruments, and dental prosthetics due to its biocompatibility and resistance to bodily fluids. CNC machining of titanium ensures that these critical medical devices are manufactured with the highest level of precision and quality, meeting the stringent requirements of the healthcare industry.Additionally, the automotive industry benefits from CNC machined titanium components in high-performance vehicles, where the material's strength and lightweight properties are leveraged to enhance speed, fuel efficiency, and overall performance.**Conclusion:**The advancement of CNC machining technology has undoubtedly revolutionized the manufacturing of titanium components, paving the way for new possibilities and opportunities in various industries. With **(remove brand name)** at the forefront of this innovation, the future of precision engineering and manufacturing looks promising, as the company continues to push the boundaries of what is achievable in CNC machining titanium. As the demand for high-precision, high-performance titanium components continues to grow, CNC machining technology will play a pivotal role in meeting the evolving needs of the manufacturing industry.
Exploring the Advantages of Plastic CNC Machining: Your Complete Guide
Title: Leading CNC Machining Company Revolutionizes Plastic Manufacturing ProcessIntroduction:In the fast-paced world of manufacturing, precision and efficiency are crucial factors that determine the success of a company. One such industry leader, {Company Name}, has long been at the forefront of revolutionizing CNC machining for plastic materials. Their groundbreaking techniques and cutting-edge technology have paved the way for innovation and advancement in the manufacturing sector. With a diverse range of applications across various industries, {Company Name} continues to drive quality and excellence in the field of plastic machining.1. Innovations in CNC Machining Plastic:{Company Name} has revolutionized the CNC machining process by introducing state-of-the-art technology and advanced techniques specifically designed for plastic materials. Traditional machining methods often encounter challenges when working with plastic due to its unique properties. However, {Company Name}'s pioneering approach has overcome these obstacles.Their precise CNC machines are equipped with specially designed tooling and cutting-edge software that optimizes the machining process for plastic. The integration of computer-controlled automation ensures unprecedented accuracy and consistency in every part produced. This level of precision allows for the manufacturing of intricate and complex plastic components with tight tolerances, meeting the demanding requirements of various industries.2. Diverse Applications:The versatility of {Company Name}'s CNC machining capabilities extends across multiple industries. Automotive manufacturers rely on their expertise to produce high-quality plastic parts for interior components, such as dashboard panels, door handles, and trim pieces. The medical sector benefits from their precision machining abilities to create custom plastic implants and medical device components, ensuring optimal patient care.Moreover, the electronics industry relies on {Company Name}'s efficient plastic machining solutions for producing casings, connectors, and enclosures for various electronic devices. The aerospace industry also benefits from their expertise in crafting lightweight, yet durable plastic components, contributing to enhanced fuel efficiency and performance.3. Commitment to Sustainability:In addition to their exceptional manufacturing capabilities, {Company Name} is also deeply committed to sustainable practices. They recognize the environmental impact of plastic materials and continuously strive to reduce waste and energy consumption. By employing efficient machining processes, recycling initiatives, and material optimization techniques, they ensure minimal environmental footprint in their operations.{Company Name} actively collaborates with their clients to explore eco-friendly alternatives for plastic materials, such as biodegradable or recyclable options. This dedication to sustainability resonates with their customers, who appreciate their responsible manufacturing practices.4. Quality Control and Certifications:Maintaining the highest standards in quality control is of utmost importance to {Company Name}. They adhere to rigorous quality management systems, ensuring that each plastic component meets or exceeds industry standards. Their manufacturing processes are not only ISO 9001 certified but also comply with other relevant certifications as per industry requirements.Utilizing advanced measurement tools and inspection techniques, {Company Name} conducts thorough testing and inspections throughout the entire machining process. This meticulous approach guarantees the delivery of flawless components, meeting the stringent specifications of their clients.Conclusion:{Company Name}'s continuous innovation in CNC machining for plastic materials has revolutionized the manufacturing sector. Their cutting-edge technology, industry expertise, and commitment to sustainability have positioned them as leaders in the field. By enabling precision, efficiency, and quality, {Company Name} sets a benchmark for excellence, meeting the diverse needs of clients across multiple industries. As they continue to push boundaries and embrace advancements in CNC machining, {Company Name} ensures a brighter future for plastic manufacturing, enhancing products and revolutionizing industries worldwide.