Top Workholding Fixtures for CNC Machines: Everything You Need to Know
By:Admin
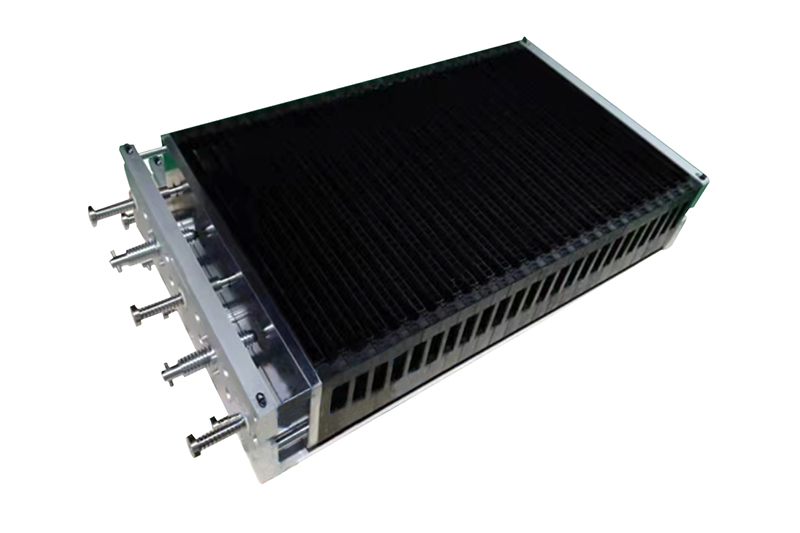
In today's fast-paced manufacturing industry, precision and efficiency are paramount. With the advancement in technology, companies are constantly seeking innovative solutions to improve their manufacturing processes. CNC workholding fixtures have emerged as a game-changer in the industry, offering a more efficient, accurate, and cost-effective way to hold and secure workpieces during machining operations.
{Company name}, a leading provider of CNC workholding fixtures, has been at the forefront of this revolution, offering a wide range of solutions designed to meet the diverse needs of the manufacturing industry.
The company's state-of-the-art CNC workholding fixtures are designed to ensure the highest levels of precision and repeatability, ultimately leading to improved productivity and reduced downtime. These fixtures are engineered to withstand the rigors of high-speed machining operations, offering unmatched stability and reliability.
One of the key advantages of {company name}'s CNC workholding fixtures is their versatility. Whether it's a simple milling operation or a complex 5-axis machining process, these fixtures can be easily customized to accommodate different workpiece geometries and sizes. This flexibility allows manufacturers to streamline their production processes and adapt to changing demands with ease.
Moreover, {company name}'s CNC workholding fixtures are designed with a focus on ergonomics and user-friendly features. This not only ensures a safer working environment for operators but also reduces the setup time, ultimately leading to increased operational efficiency.
In addition to their standard range of CNC workholding fixtures, {company name} also offers custom design and manufacturing services to meet the unique requirements of their clients. Their team of skilled engineers and technicians work closely with customers to develop tailored solutions that optimize their manufacturing processes and enhance their competitive edge.
The impact of {company name}'s CNC workholding fixtures can be seen across various industries, including aerospace, automotive, medical, and energy. By implementing these advanced fixtures, companies have been able to achieve higher levels of precision, reduce scrap rates, and ultimately improve their bottom line.
With the ever-increasing demand for high-quality precision components, manufacturers are constantly looking for innovative solutions to stay ahead of the competition. {Company name}'s CNC workholding fixtures are a testament to their commitment to pushing the boundaries of technology and delivering superior solutions that meet the evolving needs of the industry.
Furthermore, with sustainability becoming a top priority for many companies, {company name} is also committed to developing eco-friendly solutions that minimize waste and energy consumption. Their CNC workholding fixtures are designed to optimize material usage and reduce the environmental impact of the manufacturing process.
Overall, {company name}'s CNC workholding fixtures have revolutionized the manufacturing industry by providing a more efficient, accurate, and sustainable solution to workpiece holding and securing. With their commitment to innovation and excellence, {company name} continues to play a pivotal role in shaping the future of manufacturing.
As the industry continues to evolve, companies can rely on {company name} to provide cutting-edge CNC workholding fixtures that meet the highest standards of quality and performance. With their expertise and dedication to customer satisfaction, {company name} is well-positioned to lead the way in the ever-changing world of manufacturing.
Company News & Blog
Top Trends in the Injection Molding Industry for 2021
The Injection Molding Industry is a critical manufacturing sector that plays a vital role in producing a wide range of plastic products for various industries. This industry utilizes advanced technologies and techniques to efficiently and effectively produce high-quality plastic parts and components. One prominent player in the injection molding industry is {}. With a long-standing reputation for excellence and innovation, {} has solidified its position as a leading provider of injection molding solutions.With a rich history dating back to its inception, {} has continuously evolved and adapted to meet the changing needs of the industry. The company has established a strong presence in the market by consistently delivering cutting-edge products and services. Specializing in precision molding, over-molding, and insert molding, {} has the expertise and capabilities to cater to diverse client demands across different industries such as automotive, consumer goods, electronics, and medical devices.{}'s success can be attributed to its state-of-the-art manufacturing facilities, extensive experience, and unwavering commitment to quality. The company is equipped with a range of advanced injection molding machines, automated production lines, and quality control systems to ensure the highest standards of production. Moreover, {} employs a team of highly skilled engineers, technicians, and industry experts who are dedicated to delivering innovative solutions and exceeding customer expectations.In addition to its manufacturing capabilities, {} places a strong emphasis on research and development. The company invests significantly in advancing its technologies, materials, and processes to stay ahead of the competition and address emerging industry trends. This commitment to innovation enables {} to offer a diverse portfolio of injection molding solutions that are tailored to meet specific customer requirements.Furthermore, {} is deeply committed to sustainable and environmentally friendly practices. The company actively seeks ways to minimize its environmental impact through the responsible use of materials, energy-efficient manufacturing processes, and waste reduction initiatives. By incorporating sustainable practices into its operations, {} aims to set a benchmark for environmental stewardship within the injection molding industry.As a global player in the injection molding industry, {} has established a strong presence in international markets, serving clients across the globe. The company's dedication to quality, reliability, and customer satisfaction has earned it a stellar reputation and a loyal customer base. Through strategic partnerships and collaborations, {} continues to expand its reach and strengthen its position as a trusted provider of injection molding solutions.Looking ahead, {} is poised for further growth and success in the injection molding industry. The company remains committed to driving innovation, enhancing its capabilities, and delivering exceptional value to its customers. With a focus on excellence and a forward-thinking approach, {} is well-positioned to shape the future of the injection molding industry and set new standards for manufacturing excellence.In conclusion, the Injection Molding Industry is a dynamic and crucial sector that drives innovation and shapes the production of plastic products. With its remarkable achievements, dedication to quality, and commitment to sustainability, {} has emerged as a prominent leader in the industry. As the company continues to thrive and evolve, it is poised to make significant contributions to the advancement of injection molding technology, meeting the needs of industries and customers around the world.
Exploring the Advantages of Computer Numerical Control Machining in Modern Manufacturing
Title: Computer Numerical Control Machining Revolutionizes Manufacturing ProcessesIntroduction:In today's fast-paced world, businesses are constantly seeking innovative solutions to enhance the precision, speed, and efficiency of their manufacturing processes. One such technological advancement that has transformed the industry is Computer Numerical Control (CNC) Machining. By leveraging cutting-edge software and automation, CNC Machining has revolutionized traditional manufacturing methods, allowing companies to fabricate components with utmost accuracy and reliability. In this article, we will explore the remarkable capabilities of CNC Machining and its impact on modern manufacturing systems.Paragraph 1:CNC Machining has emerged as a game-changing technology that has significantly enhanced the precision of component manufacturing. By utilizing computer-controlled systems, this manufacturing process converts digital designs into physical products with unparalleled accuracy. Unlike conventional manual machining, CNC Machining eliminates the scope for human error, resulting in higher product quality and reduced waste. This advancement has not only boosted productivity in various industries but also facilitated the creation of intricate designs and complex geometries that were previously unattainable.Paragraph 2:The key to the success of CNC Machining lies in its ability to perform multiple manufacturing operations using a single machine. From milling and drilling to lathing and grinding, CNC machines are equipped with a wide range of tools that can be seamlessly interchanged. Additionally, these machines can operate without human intervention, enabling manufacturers to optimize productivity by running the machines continuously even outside working hours. This level of automation not only reduces production time but also minimizes costs associated with manual labor, making CNC Machining a cost-effective solution for businesses across various sectors.Paragraph 3:Furthermore, CNC Machining has empowered companies to meet the growing demands for customized products while maintaining consistent quality. By leveraging CAD/CAM software, designers can create intricate 3D models of components, which are then translated into machine-readable code. This code is fed into the CNC machine, allowing it to precisely reproduce the model and produce multiple copies with utmost accuracy. Whether it is prototyping or mass production, CNC Machining ensures remarkable repeatability and uniformity of products, facilitating efficient scaling of operations.Paragraph 4:The impact of CNC Machining on various industries is undeniable. For instance, in the aerospace and automotive sectors, precision and reliability are of paramount importance. CNC Machining enables manufacturers to create intricate components such as turbine blades or engine parts with exceptional precision, meeting the stringent requirements of these industries. Moreover, the medical field has also witnessed immense benefits from CNC Machining, as it allows for the production of patient-specific implants and devices, improving treatment outcomes and reducing surgical costs.Paragraph 5:Despite these remarkable advantages, the adoption of CNC Machining may face certain challenges. The initial cost of acquiring state-of-the-art CNC machines and training personnel in their operation and maintenance can be significant for small to medium-sized enterprises. However, the long-term gains in terms of improved productivity, reduced waste, and enhanced product quality outweigh these concerns. As CNC Machining continues to advance, manufacturers must recognize its transformative potential and invest in this technology to remain competitive in an increasingly demanding market.Conclusion:Computer Numerical Control Machining has revolutionized traditional manufacturing processes by introducing automation, precision, and versatility. This technology has not only enabled companies to meet intricate design requirements but also improved productivity and reduced production time and costs. As industries continue to benefit from CNC Machining, it is crucial for manufacturers to stay abreast of evolving advancements and harness its potential to achieve sustainable growth and maintain a competitive edge in today's rapidly evolving marketplace.
Top 5 CNC Milling Lathes for Precision Engineering
In today's fast-paced and demanding industrial environment, precision and efficiency are key factors in staying competitive. This is where the CNC milling lathe from {} comes into play. With its advanced technology and superior performance, this innovative machine is transforming the way companies produce and manufacture their products. Let's take a closer look at how this CNC milling lathe is revolutionizing the industry.{} has been a leading provider of advanced manufacturing solutions for over two decades. The company's commitment to innovation and excellence has earned them a reputation for delivering cutting-edge technology to their clients. Their CNC milling lathe is a testament to their dedication to pushing the boundaries of what is possible in the manufacturing world.This CNC milling lathe is equipped with state-of-the-art features that set it apart from traditional milling machines. Its precision engineering allows for incredibly tight tolerances and flawless surface finishes, ensuring that every part produced is of the highest quality. The machine's high-speed capabilities and multi-axis functionality also enable complex and intricate parts to be manufactured with ease and efficiency. This level of precision and speed is unparalleled in the industry and has significantly enhanced the productivity of companies that have implemented this technology into their operations.One of the standout features of this CNC milling lathe is its user-friendly interface and intuitive programming capabilities. This allows operators to easily input complex designs and geometries, simplifying the manufacturing process and reducing the margin for error. Additionally, the machine's automation and self-monitoring capabilities minimize downtime and optimize production, making it a valuable asset for any company looking to streamline their manufacturing processes.Furthermore, {} has a team of experienced engineers and technical support staff who are dedicated to providing exceptional service and assistance to their clients. From installation and training to ongoing maintenance and support, {} ensures that their customers are fully equipped to harness the full potential of their CNC milling lathe. This level of support and expertise sets {} apart from its competitors and has made them a trusted partner for companies looking to invest in advanced manufacturing technology.The impact of this CNC milling lathe on the industry has been significant. Companies that have integrated this technology into their operations have reported substantial improvements in their production processes. The machine's ability to produce high-precision components with minimal lead time has allowed companies to meet the growing demands of their customers while maintaining the highest standards of quality. This has not only enhanced their competitiveness in the market but has also opened up new opportunities for growth and expansion.In conclusion, the CNC milling lathe from {} is a game-changer in the manufacturing industry. Its advanced technology, precision engineering, and user-friendly interface have set a new standard for efficiency and quality in production processes. With {}'s commitment to providing exceptional service and support, companies have a reliable partner to help them navigate the complexities of integrating this innovative technology into their operations. As the industry continues to evolve, it is clear that the CNC milling lathe from {} will play a pivotal role in shaping the future of manufacturing.
Highly Efficient Metal CNC Milling Machine for Precision Manufacturing
The importance of precision and efficiency in the manufacturing industry cannot be overstated. With the increasing demand for high-quality metal components, companies are constantly seeking ways to improve their production processes. One such company that has made significant strides in this area is {Company Name}.{Company Name} has recently invested in a state-of-the-art CNC milling machine to further improve its metal fabrication capabilities. The new machine is a game-changer for the company, as it allows for more precise and efficient metal cutting and shaping.CNC, or computer numerical control, milling machines are a staple in the manufacturing industry. They are capable of performing a wide range of tasks, from simple drilling to complex machining operations. With the latest advancements in technology, CNC milling machines have become even more versatile and precise, making them the go-to choice for companies looking to enhance their metal fabrication capabilities.{Company Name} has always been committed to staying ahead of the curve when it comes to technology and innovation. The investment in the new CNC milling machine is a testament to this commitment. By leveraging the latest advancements in CNC technology, {Company Name} is able to offer its clients even higher quality and more intricate metal components.The new CNC milling machine boasts several key features that set it apart from traditional milling machines. One of the most notable features is its ability to automatically change tools, reducing the need for manual intervention and increasing overall efficiency. Additionally, the machine is equipped with advanced software that allows for real-time monitoring and adjustments, ensuring that the final product meets the highest quality standards.In addition to the technological advancements, the CNC milling machine also offers a higher level of precision. This is particularly important for {Company Name}, as many of its clients require metal components with extremely tight tolerances. The new machine is capable of producing parts with exceptional accuracy, meeting even the most stringent specifications.The investment in the new CNC milling machine has already yielded positive results for {Company Name}. With the increased efficiency and precision, the company has been able to take on more complex projects and deliver them within shorter timeframes. This has not only strengthened its relationships with existing clients but has also attracted new business opportunities.Furthermore, the new machine has opened up possibilities for {Company Name} to explore new markets and industries. With its enhanced capabilities, the company is now able to cater to a wider range of clients, from aerospace and automotive to medical and telecommunications.The CNC milling machine has also had a positive impact on {Company Name}'s internal operations. The increased efficiency and precision have streamlined the production process, allowing the company to optimize its workflow and reduce lead times. This has translated into cost savings and improved overall productivity.Looking ahead, {Company Name} is committed to further leveraging the capabilities of the new CNC milling machine. The company has plans to explore additional applications and industries where the machine can make a significant impact. Additionally, {Company Name} is actively investing in training and development for its employees to ensure they are equipped with the necessary skills to maximize the potential of the new machine.In conclusion, the investment in the new CNC milling machine has solidified {Company Name}'s position as a leader in the metal fabrication industry. With its enhanced capabilities, the company is well-positioned to meet the evolving needs of its clients and capitalize on new business opportunities. As technology continues to advance, {Company Name} remains committed to staying at the forefront of innovation, delivering high-quality metal components with the utmost precision and efficiency.
Designing Molds for Injection Molding: A Guide for Efficient Production
Mold Design For Injection Molding – Innovating for the FutureInjection molding is a manufacturing process used to produce parts by injecting material into a mold. This process requires a high level of precision and expertise, particularly in mold design. One company that is leading the way in innovative mold design for injection molding is [Company Name].[Company Name] is a global leader in the injection molding industry, with a strong reputation for producing high-quality molds and parts for a wide range of industries. With over [number] years of experience, the company has developed a deep understanding of the injection molding process and has continually pushed the boundaries of mold design to meet the evolving needs of its customers.The company's dedication to innovation and quality has led to the development of cutting-edge mold designs that optimize the injection molding process. These designs not only improve the efficiency of production but also enhance the overall quality and precision of the molded parts.One of the key factors that set [Company Name] apart is its focus on custom mold design. The company works closely with its clients to understand their specific requirements and then develops tailored mold designs to meet those needs. This personalized approach ensures that each mold is optimized for the specific material, part geometry, and production volume, resulting in the highest quality finished products.In addition to custom mold design, [Company Name] also offers a range of standardized mold designs that have been proven to deliver exceptional results. These designs have been meticulously developed and tested to ensure consistent and reliable performance, making them an ideal solution for a wide range of injection molding applications.Furthermore, [Company Name] utilizes state-of-the-art technology and advanced engineering techniques in the mold design process. The company's team of experienced engineers and designers utilize the latest software and simulation tools to optimize mold designs for maximum performance and efficiency, ultimately reducing production time and costs for their customers.By staying at the forefront of mold design innovation, [Company Name] has been able to meet the ever-increasing demands of the injection molding industry. With a commitment to quality, precision, and customer satisfaction, the company continues to drive forward in developing new and improved mold designs that provide optimal results for its clients.One of the biggest challenges in mold design for injection molding is achieving the precise balance between part design and mold flow analysis. To address this challenge, [Company Name] has developed a unique approach that involves thorough analysis of the part design and material behavior, leading to the development of molds that produce consistent and high-quality parts.Moreover, [Company Name] has a strong focus on sustainability and environmental responsibility in its mold design processes. The company actively explores ways to minimize material waste and energy consumption in its mold designs, ultimately reducing the environmental impact of injection molding production.In conclusion, [Company Name] is a leading force in innovative mold design for injection molding, with a strong commitment to meeting the unique needs of its customers. Through custom and standardized mold designs, advanced engineering techniques, and a focus on sustainability, the company continues to drive forward in the development of cutting-edge solutions that deliver exceptional results in the injection molding industry. With a track record of excellence and a dedication to continuous improvement, [Company Name] is poised to remain a key player in the future of mold design for injection molding.
CNC Turning Machining Services: Advanced Precision Techniques for Your Needs
Title: Revolutionizing Precision Manufacturing: Cutting-Edge CNC Turning Machining UnveiledIntroduction:In the ever-evolving landscape of modern manufacturing, precision and efficiency are paramount. Companies around the world are constantly searching for innovative solutions to meet the growing demands of customers while maintaining high-quality standards. One such groundbreaking technology that has been making waves in the manufacturing industry is CNC turning machining. This advanced process, when combined with the expertise and commitment of leading companies, is revolutionizing precision manufacturing like never before, ensuring both accuracy and speed in the production process.[Company Name] Leads the Way in CNC Turning Machining Excellence:As a pioneer in precision engineering, [Company Name] has emerged as a global leader in the implementation of CNC turning machining. With its unwavering commitment to cutting-edge technology and expertise in advanced manufacturing techniques, [Company Name] has consistently pushed boundaries and set new industry standards.State-of-the-Art CNC Turning Machining:CNC turning machining, standing for computer numerical control turning, refers to a manufacturing process involving the use of computer-controlled machines to produce custom-designed parts and components. This process utilizes lathes to shape and mold raw materials into intricate and precise forms. It offers unparalleled precision and repeatability, making it the go-to choice for companies operating in diverse sectors such as aerospace, automotive, medical, and more.Benefits of CNC Turning Machining:1. Enhanced Precision: CNC turning machining ensures exceptional accuracy in creating parts with minimal human intervention. The computerized controls enable precise measurements and tight tolerances, reducing the risk of errors typically associated with manual machining.2. Improved Efficiency: By eliminating the need for manual adjustments, CNC turning machining significantly increases productivity. The automated process allows for seamless production runs, reducing downtime and maximizing output.3. Versatility: CNC turning machining can be applied to a wide range of materials, giving manufacturers flexibility in accommodating various project requirements. Whether it is plastic, metal, or composite materials, this technology can shape and craft parts with intricate details and complex geometries.4. Cost Effectiveness: Although initially requiring a significant investment, CNC turning machining ultimately leads to cost savings in the long run. The precise, efficient, and automated nature of the process reduces material waste and labor costs, delivering enhanced profitability for companies.Applications of CNC Turning Machining:The versatility of CNC turning machining allows it to be applied to numerous industries:1. Aerospace: This technology proves vital in the manufacture of aircraft components, enabling the production of lightweight and durable parts that meet stringent industry standards.2. Automotive: CNC turning machining is central to automotive manufacturing, facilitating the creation of precise engine components, transmission parts, and more, ensuring durability and optimum performance.3. Medical: In the medical field, precision is of utmost importance. CNC turning machining provides the accuracy required to produce medical device components, implants, and surgical instruments that meet rigorous quality standards.4. Electronics: When it comes to manufacturing intricate electronic components, such as connectors, housings, and enclosures, CNC turning machining plays a pivotal role, ensuring consistent quality and meeting tight tolerances.[Company Name]: Driving Innovation:Renowned for its commitment to pushing the boundaries of conventional manufacturing techniques, [Company Name] has successfully integrated CNC turning machining into its operations. By investing in state-of-the-art machinery and employing highly skilled engineers, the company has achieved unmatched precision and meticulous craftsmanship."Our cutting-edge CNC turning machining capabilities allow us to bring our customers' visions to reality, ensuring the highest levels of quality and performance," said [Spokesperson Name], spokesperson for [Company Name]. "We are constantly evolving and embracing technological advancements to stay at the forefront of the industry."Conclusion:With CNC turning machining leading the way in precision manufacturing, companies like [Company Name] are at the forefront, driving innovation and raising industry standards. The unmatched precision, versatility, and cost-effectiveness of CNC turning machining enable manufacturers to deliver exceptional products across various sectors. As technology continues to advance, the possibilities for CNC turning machining are endless, transforming the manufacturing landscape and ensuring a brighter future for precision engineering.
Exploring the Limitations of Sand Casting: Factors Hindering the Process
Title: Exploring Sand Casting Disadvantages in the Manufacturing IndustryIntroduction:In the realm of manufacturing, sand casting has long been a traditional and widely-used technique for creating intricate and durable metal components. Many companies, including {}, have successfully employed sand casting in their production processes. However, it is important to be aware of the disadvantages associated with this method in order to make informed decisions in the manufacturing industry.Sand Casting and its Application:Before delving into the drawbacks, it is crucial to understand the fundamentals of sand casting. The process involves pouring molten metal into a sand mold to create a desired shape. This method offers flexibility, affordability, and the ability to produce intricate components with various alloys. Sand casting is widely used in industries like automotive, aerospace, and construction, where complex parts are required.Disadvantage 1: Limited Surface Finish and Precision:One of the major shortcomings of sand casting is the limitation it presents in achieving high surface finish and precision. The texture of the sand mold often transfers inconsistencies onto the final product, resulting in a rougher surface finish. Moreover, the molding process may introduce slight variations in dimensions, making it challenging to achieve precise measurements and tight tolerances. These factors can be critical in industries where the aesthetics and precision of components are paramount, such as consumer electronics and medical devices.Disadvantage 2: Time and Labor Intensive:Sand casting is a time and labor-intensive process, which can significantly impact the overall production timeline and costs. Preparing the molds, including pattern creation, gating system design, and mold assembly, requires skilled labor and careful execution. Additionally, molten metal must be cooled and solidified in the mold, followed by the removal of excess sand and finishing operations. Addressing these steps can be time-consuming, leading to longer lead times and reduced efficiency, especially for industries characterized by high-volume production demands.Disadvantage 3: Limited Complexity and Assembly Integration:While sand casting is suitable for various complex shapes, it has limitations in terms of intricate designs and integration with assembly components. The mold's internal cavities can be challenging to achieve with precision, prohibiting the creation of intricate features. Furthermore, sand casting may not be ideal for components requiring internal passageways, such as cooling channels, as the removal of the sand mold can be difficult and may compromise the final product's integrity. For industries that heavily rely on intricate designs and integration, such as semiconductor manufacturing or advanced machinery, alternative production methods like precision machining may be preferred.Disadvantage 4: Material Waste and Environmental Concerns:Sand casting generates a significant amount of waste material. After each casting, sand molds become unusable and are discarded, contributing to environmental concerns. Additionally, the process can consume large quantities of sand, leading to mining activities and the depletion of natural resources. Companies like {} have been actively working towards sustainable solutions by implementing recycling processes and exploring environmentally-friendly alternatives to sand molds, such as 3D-printed molds or investment casting.Conclusion:Sand casting undeniably plays a crucial role in the manufacturing industry, with its affordability and flexibility making it an attractive choice for many companies, including {}. However, it is essential to be aware of its disadvantages, which include limited surface finish and precision, time and labor intensiveness, limited complexity and integration, and environmental concerns. By understanding these drawbacks, manufacturers can make more informed decisions when choosing their production methods, potentially optimizing their processes and meeting the demands of their respective industries while considering sustainability needs.
Discover a wide range of CNC parts on a reliable platform
CNC Parts Platform Enhances Manufacturing Efficiency for Industries WorldwideIn today's fast-paced and highly competitive manufacturing industry, companies are constantly seeking ways to improve efficiency and streamline their operations. One company at the forefront of this movement is {}, a leading provider of CNC parts and components for a wide range of industries.With a diverse range of high-quality products and a commitment to innovation, {} has become a trusted partner for manufacturers looking to optimize their production processes. Through their comprehensive online platform, customers can easily access a wide selection of CNC parts, including milling machines, lathes, and other essential components.The company's extensive product offerings are designed to meet the diverse needs of manufacturers across various industries, including automotive, aerospace, electronics, and more. By providing a one-stop solution for CNC parts and components, {} is empowering businesses to improve their manufacturing capabilities and stay ahead in an increasingly competitive market.To further enhance the customer experience, {} has implemented advanced search and filtering tools on their website, allowing users to quickly find the specific parts they need for their production processes. This level of accessibility and convenience is a testament to the company's dedication to customer satisfaction and efficiency.In addition to their impressive product range, {} is also known for their commitment to quality and reliability. The company works closely with leading manufacturers to source the best CNC parts and components, ensuring that their customers receive top-notch products that meet the highest standards of performance and durability.Furthermore, {} understands the importance of staying ahead of the curve when it comes to technological advancements in the manufacturing industry. As a result, the company continuously updates their product offerings to include the latest innovations in CNC technology, allowing their customers to benefit from the most cutting-edge solutions available.One of the key advantages of {}'s platform is the ability to provide custom solutions for specific manufacturing requirements. The company's team of experienced professionals is dedicated to working closely with customers to develop tailored solutions that address their unique needs, whether it's a custom machining project or a specialized component for a particular application.By leveraging their extensive expertise and industry knowledge, {} has positioned itself as a trusted partner for manufacturers seeking to enhance their production capabilities and achieve greater efficiency. The company's emphasis on collaboration and customization sets them apart in a competitive market, demonstrating their commitment to going above and beyond for their customers.Looking ahead, {} remains dedicated to driving innovation and supporting the evolving needs of the manufacturing industry. With a focus on quality, reliability, and customer satisfaction, the company is poised to continue making a significant impact on the global manufacturing landscape, empowering businesses to thrive in an increasingly competitive market.As manufacturing continues to evolve, companies like {} are essential partners for businesses looking to optimize their production processes and stay ahead of the curve. With a comprehensive range of high-quality CNC parts and a commitment to innovation, the company is well-positioned to lead the charge in driving efficiency and advancement in the manufacturing industry.
Revolutionizing Precision Machining: Unveiling the Power of Plastic CNC
Plastic CNC Provider Revolutionizes Manufacturing with Cutting-Edge TechnologyIn an era where manufacturing excellence and efficiency are highly prized, Plastic CNC, a leading provider of precision plastic machining solutions, has emerged as a game-changer in the industry. With their commitment to innovation and advanced technology, the company has established itself as a trusted partner for businesses seeking high-quality plastic components and parts.Since its inception, Plastic CNC has been at the forefront of revolutionizing the manufacturing process through their state-of-the-art machinery, skilled workforce, and dedication to customer satisfaction. Specializing in computer numerical control (CNC) machining, the company utilizes automated systems to precisely shape and mold plastic into intricate components with exceptional accuracy and consistency.Plastic CNC's commitment to technological innovation is evident through their extensive range of cutting-edge CNC machines. These machines are designed to handle various types of plastics, including but not limited to acrylic, polycarbonate, nylon, and polyethylene. The company's vast repertoire of machinery ensures that they can cater to the diverse needs and specifications of their clients, regardless of the complexity or intricacy of the desired components.One of the key advantages that sets Plastic CNC apart from its competitors is its dedicated team of highly skilled engineers and technicians. These professionals possess a deep understanding of the intricacies of plastic machining and are adept at leveraging the capabilities of their advanced machinery. Their expertise allows Plastic CNC to consistently deliver products of unmatched precision and quality, with tight tolerances and smooth finishes exceeding industry standards.Plastic CNC's commitment to customer satisfaction is reflected in their ability to handle projects of varying sizes and complexities. From prototyping and small-scale production runs to large-scale manufacturing projects, the company has the capability and capacity to accommodate the unique needs and timelines of their clients. Their advanced CNC machines and streamlined production processes ensure prompt delivery of products without compromising on quality.Furthermore, Plastic CNC's dedication to sustainability is commendable. By employing efficient manufacturing processes and optimizing material usage, the company minimizes waste and reduces its environmental footprint. Their commitment to responsible plastic machining aligns with the global efforts to promote sustainable practices in the manufacturing industry.Over the years, Plastic CNC has built a strong reputation among a diverse range of industries due to their unwavering commitment to excellence. The company has successfully served clients in sectors such as electronics, automotive, aerospace, medical, and consumer goods. Their ability to meet the stringent demands of these industries while maintaining competitive pricing has contributed to their long-term success and global reach.To ensure seamless collaboration with their clients, Plastic CNC offers comprehensive design and engineering support. By leveraging computer-aided design (CAD) software and working closely with clients during the initial design phase, the company can optimize the manufacturability of the desired components. This collaborative approach fosters innovation, reduces production costs, and allows for quicker turnaround times.In an evolving landscape where precision and efficiency are critical, Plastic CNC continues to redefine the manufacturing industry. Through its cutting-edge technology, skilled workforce, and customer-centric approach, the company consistently delivers top-notch plastic machining solutions. As they continue to push the boundaries of innovation, Plastic CNC remains a trusted partner for businesses seeking the highest quality plastic components and parts.
Discover the Benefits of Rapid CNC Machining for Quality Results
Title: Leading CNC Machining Service Provider Offers Precision and Efficiency to Industrial Clients Introduction: In the dynamic world of industrial manufacturing, precision and efficiency are key factors that can make or break a company's success. Recognizing this, Rapid CNC Machining (brand name removed), a leading CNC machining service provider, has emerged as a reliable partner for industrial clients seeking high-quality and precise manufacturing solutions. With a commitment to cutting-edge technology, exceptional customer service, and seamless project management, Rapid CNC Machining continues to strengthen its position as a trusted name in the industry.Body:1. Company Overview and Expertise:Established in the heart of the manufacturing hub, Rapid CNC Machining has a proven track record of delivering precision-machined parts and components to a wide array of industries. The company's state-of-the-art facility houses an extensive range of CNC machines, allowing them to cater to diverse manufacturing needs. Their team of highly skilled technicians, engineers, and project managers ensure that each project is executed with utmost precision and efficiency.2. Technological Advancements:Rapid CNC Machining has stayed ahead of the competition by consistently investing in the latest CNC machining technology. The company's cutting-edge equipment enables them to provide comprehensive solutions, including design assistance, prototyping, custom part production, and mass production. By utilizing advanced software and tools, Rapid CNC Machining optimizes the manufacturing process, reducing lead times and maximizing product quality.3. Diverse Industry Applications:With an extensive portfolio of successful projects, Rapid CNC Machining serves various industries, including aerospace, automotive, medical, electronics, and more. Their expertise in machining a wide range of materials, including aluminum, stainless steel, titanium, plastics, and composites, enables them to meet the unique requirements of each industry. Whether it is complex aerospace components or intricate medical device parts, Rapid CNC Machining ensures the highest standards of accuracy, functionality, and durability.4. Commitment to Quality Assurance:Rapid CNC Machining places great emphasis on quality assurance throughout the manufacturing process. From initial design analysis to final inspection, the company employs rigorous quality control measures to guarantee adherence to specifications and customer expectations. Their ISO 9001-certified facility ensures consistent quality and compliance with industry standards, earning them a reputation for excellence.5. Customer-Centric Approach:Understanding the importance of strong customer relationships, Rapid CNC Machining prioritizes open communication and collaboration with clients. Their skilled project management team ensures seamless coordination, from project initiation to product delivery. With a commitment to transparency, Rapid CNC Machining provides regular progress updates, addresses any concerns promptly, and maintains strict confidentiality protocols.6. Sustainable Manufacturing Practices:In an era of growing environmental consciousness, Rapid CNC Machining strives to implement sustainable manufacturing practices. By optimizing material utilization, reducing waste, and utilizing energy-efficient machinery, the company minimizes its environmental footprint. Moreover, investing in research and development, Rapid CNC Machining actively explores greener alternatives, ensuring its manufacturing processes are aligned with sustainability goals.7. Global Reach and Future Outlook:Rapid CNC Machining has established a global footprint by serving clients from various countries and regions. Their commitment to delivering exceptional value and their strong reputation for reliable service has positioned them as a preferred CNC machining partner worldwide. As the company continues to expand its capabilities, invest in technology, and nurture customer relationships, Rapid CNC Machining aims to remain at the forefront of the industry.Conclusion:Through consistent innovation, dedication to customer satisfaction, and a focus on precision and efficiency, Rapid CNC Machining has solidified its position as a leading provider of CNC machining services. Their state-of-the-art facility, diverse industry applications, and commitment to sustainable practices set them apart from competitors. As industrial manufacturing continues to evolve, the company's unwavering commitment to quality and customer-centricity ensures they will remain a trusted partner for businesses seeking superior CNC machining solutions.