The Ultimate Guide to Insert Molding Process for Manufacturing
By:Admin
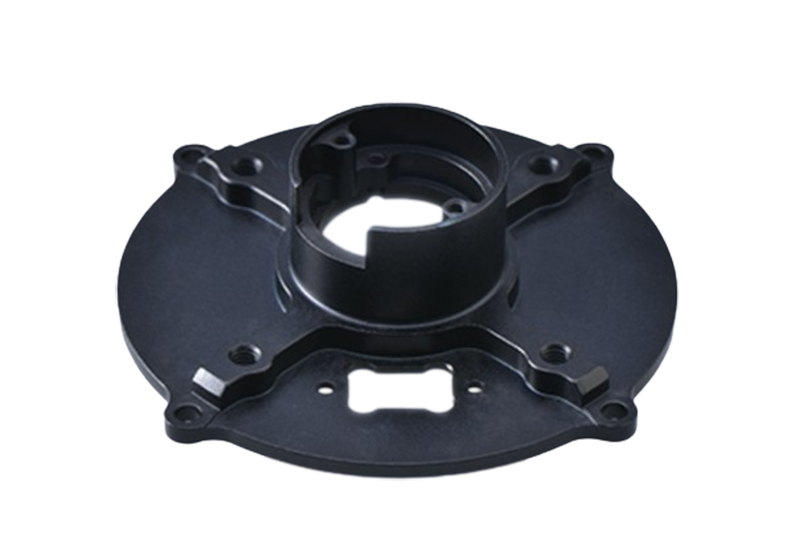
The Insert Molding Process has long been a key technology in the plastic injection molding industry. It involves the injection of plastic resin into a mold that contains pre-placed inserts, creating a single, integrated piece. This process is commonly used to encapsulate electronic components, create complex geometries, and improve part strength and reliability.
[Company], a pioneer in the field of plastic injection molding, has been utilizing the Insert Molding Process to produce a wide range of components for industries such as automotive, consumer electronics, and medical devices. By integrating metal, ceramic, or other materials into plastic components, the company has been able to produce durable and reliable parts that meet the stringent requirements of its diverse customer base.
The Insert Molding Process employed by [Company] is known for its precision and efficiency. It begins with the careful placement of the inserts into the mold, followed by the injection of molten plastic resin. The mold is then cooled and the finished part is extracted, resulting in a high-quality component with excellent dimensional stability and material integrity.
One of the key advantages of the Insert Molding Process is its ability to reduce assembly time and costs. By encapsulating multiple components into a single part, [Company] has been able to streamline production processes and minimize the need for additional assembly steps. This ultimately leads to cost savings for its customers and a more efficient supply chain.
Moreover, the Insert Molding Process allows for the creation of complex, multi-material components that would be difficult or impossible to produce through traditional manufacturing methods. This capability has enabled [Company] to offer innovative solutions to its customers, bringing their product designs to life in ways that were previously unattainable.
In addition to its technical capabilities, [Company] has also focused on sustainability in its Insert Molding Process. By optimizing material usage and reducing waste, the company has been able to minimize its environmental footprint while maintaining high-quality production standards. This commitment to sustainability has not only benefited the environment but has also resonated with customers and partners who value responsible manufacturing practices.
As [Company] continues to expand its presence in the global market, the Insert Molding Process has become an integral part of its manufacturing strategy. With a relentless focus on innovation and quality, the company has been able to leverage this technology to deliver superior products to its customers while staying ahead of the competition.
In conclusion, the Insert Molding Process has been a cornerstone of [Company]'s success in the plastic injection molding industry. By harnessing the capabilities of this technology, the company has been able to produce high-quality, cost-effective components for a wide range of industries. With a commitment to innovation, sustainability, and customer satisfaction, [Company] is poised to continue its leadership in the field of plastic injection molding for years to come.
Company News & Blog
High-Quality Moulding Machine Parts for Your Industrial Needs
Moulding Machine Parts is celebrating a decade of supplying high-quality equipment and parts to the manufacturing industry. The company has been a key player in the industry, providing innovative solutions and top-of-the-line products to its customers. As part of its commitment to excellence, Moulding Machine Parts has continuously worked to improve its products and services, setting a benchmark for the industry.With a focus on quality, precision, and reliability, Moulding Machine Parts has positioned itself as a leading supplier of moulding machine parts in the market. The company's parts are used in a wide range of industries, including automotive, aerospace, and consumer goods manufacturing. Moulding Machine Parts has earned a reputation for delivering superior products that meet and exceed industry standards.The company's success can be attributed to its skilled team of engineers and technicians, as well as its state-of-the-art manufacturing facilities. Moulding Machine Parts invests heavily in research and development to ensure that its products are at the forefront of technological advancements. This dedication to innovation has enabled the company to stay ahead of the competition and maintain its position as a trusted partner to its customers.One of the company's flagship products is its range of injection moulding machine parts. These parts are essential for the efficient operation of the machines, and Moulding Machine Parts has developed a comprehensive line of components that are known for their durability and performance. The company's injection moulding machine parts are designed to withstand the rigors of high-volume production, delivering consistent results and minimizing downtime.In addition to injection moulding machine parts, Moulding Machine Parts also offers a wide selection of other components and accessories for moulding machines. From screws and barrels to heating elements and controls, the company's product range is designed to meet the diverse needs of its customers. Moulding Machine Parts understands that each manufacturing operation is unique, and its team works closely with clients to provide customized solutions that address their specific requirements.Moulding Machine Parts is committed to providing exceptional customer service, and the company's support team is always on hand to assist customers with technical inquiries, troubleshooting, and product recommendations. By prioritizing customer satisfaction, Moulding Machine Parts has built long-lasting relationships with clients and has established a loyal customer base.Looking ahead, Moulding Machine Parts remains dedicated to driving innovation and setting new standards in the industry. The company is continuously exploring new technologies and refining its manufacturing processes to deliver the next generation of moulding machine parts. With a focus on sustainability and efficiency, Moulding Machine Parts is poised to lead the way in providing environmentally friendly solutions that reduce waste and energy consumption.As Moulding Machine Parts celebrates its 10-year anniversary, the company is proud to reflect on its achievements and the milestones it has reached. With a solid foundation built on expertise, quality, and customer satisfaction, Moulding Machine Parts looks forward to the next decade of serving the manufacturing industry and exceeding expectations.In conclusion, Moulding Machine Parts has set the standard for excellence in the supply of moulding machine parts. With a commitment to innovation, quality, and customer service, the company has established itself as a trusted partner to its clients. As it celebrates a decade of success, Moulding Machine Parts is well-positioned to continue its legacy of delivering cutting-edge solutions to the manufacturing industry.
Achieve High Quality Results with Precision Forging Technology
Precision Forging Technologies, a leading manufacturer in the field of precision forging, has recently introduced a new line of advanced forging technology that is set to revolutionize the industry. The company, known for its high-quality products and innovative solutions, has been a key player in the precision forging market for over 20 years.Precision Forging Technologies has established itself as a leader in the industry, providing precision forging solutions for a wide range of applications including automotive, aerospace, industrial machinery, and more. With a strong focus on research and development, the company has continually pushed the boundaries of what is possible in precision forging, resulting in cutting-edge products that offer unparalleled performance and durability.The new line of advanced forging technology is the result of years of research and development, and represents a significant leap forward in the industry. The technology utilizes state-of-the-art equipment and advanced techniques to produce precision forged components with unmatched precision and strength. This allows for the production of complex shapes and intricate designs that were previously thought to be unattainable through traditional forging methods.In addition to its advanced technology, Precision Forging Technologies also offers a range of value-added services to its customers. These services include design assistance, material selection, and engineering support, ensuring that customers receive the optimal solution for their specific needs. The company's team of experts is dedicated to providing superior customer service, with a focus on delivering solutions that exceed expectations.With a commitment to quality and innovation, Precision Forging Technologies continues to lead the way in the precision forging industry. The company's products are trusted by some of the largest and most demanding customers in the market, and its reputation for excellence is well-known throughout the industry.In a statement regarding the new line of advanced forging technology, the CEO of Precision Forging Technologies expressed his excitement about the potential impact of the new technology. "We are thrilled to introduce this game-changing technology to the market," he said. "We believe that it will open up new possibilities for our customers and allow them to achieve new levels of performance and efficiency in their products."The company plans to showcase its new technology at several upcoming industry events, where it will have the opportunity to demonstrate the capabilities of the new technology to a wide audience of potential customers. By highlighting the benefits and advantages of the advanced forging technology, the company hopes to generate significant interest and demand for its products.As Precision Forging Technologies continues to push the boundaries of what is possible in precision forging, it remains committed to its core values of quality, innovation, and customer satisfaction. With its new line of advanced forging technology, the company is poised to continue its legacy of excellence and leadership in the industry for years to come.
How to Create a CNC Milling Design: Tips and Techniques for Success
CNC Milling Design: Revolutionizing Manufacturing ProcessesIn today's fast-paced manufacturing industry, precision and efficiency are key factors in staying competitive. With the advancement of technology, companies are constantly seeking innovative solutions to streamline their production processes. One such solution that has been gaining attention is CNC milling design, a versatile and efficient method of producing high-precision components for a wide range of industries.CNC milling, or computer numerical control milling, is a machining process that utilizes computerized controls to operate and manipulate machine tools. This advanced technology allows for the creation of intricate and complex designs, with a level of precision that is difficult to achieve with traditional manual milling methods. By utilizing CAD/CAM software, CNC milling machines can rapidly produce components with tight tolerances and intricate detailing, making them an invaluable asset for manufacturers across various industries.One company that has been at the forefront of CNC milling design is {}. With a strong focus on innovation and quality, {} has become a leading provider of CNC milling services for a diverse clientele. Specializing in the production of precision components for industries such as aerospace, automotive, medical, and defense, {} has earned a reputation for delivering superior quality products that meet the strictest industry standards.With state-of-the-art CNC milling machines and a team of highly skilled engineers and machinists, {} has the capability to handle complex projects with precision and efficiency. Their commitment to investing in the latest technology and continuous improvement has allowed them to stay ahead of the curve in the rapidly evolving manufacturing landscape.The advantages of CNC milling design are evident in the superior quality and efficiency of the components produced. By automating the machining process, CNC milling eliminates the margin for error that is inherent in manual operations, resulting in consistently high-quality parts. Additionally, CNC milling machines can operate 24/7, maximizing production output and reducing lead times, ultimately leading to cost savings for manufacturers.Another key benefit of CNC milling design is its versatility. With the ability to work with a wide range of materials, including metals, plastics, and composites, CNC milling machines can accommodate the diverse needs of different industries. Whether it's producing intricate parts for the aerospace industry or creating custom components for medical devices, CNC milling design offers a flexible and adaptable solution for manufacturers.As the demand for high-precision components continues to grow, the importance of CNC milling design in modern manufacturing cannot be overstated. Companies like {} are instrumental in driving the adoption of this advanced technology, setting new standards for precision and quality in the industry.In conclusion, CNC milling design represents a significant advancement in the manufacturing sector, offering unparalleled precision, efficiency, and versatility. With leading companies like {} pushing the boundaries of what is possible with CNC milling technology, the future looks promising for manufacturers seeking to enhance their production processes and stay ahead of the competition. As technology continues to evolve, CNC milling design will undoubtedly play a pivotal role in shaping the future of manufacturing.
Learn About Injection Overmolding: What It Is and How It Works
Injection Overmolding: Revolutionizing Plastic ManufacturingIn today's fast-paced and ever-changing world, the demand for high-quality, innovative products is at an all-time high. As a result, manufacturers are continually seeking new and efficient ways to produce top-of-the-line goods that meet the needs and expectations of consumers. One of the latest developments in the field of plastic manufacturing is Injection Overmolding.Injection Overmolding is a cutting-edge process that involves the injection of molten plastic over a pre-formed substrate or insert. This unique method allows for the creation of complex and multi-material parts, resulting in durable, high-performance products. The process begins with the production of a pre-formed component, which serves as the substrate for the overmolding. This component is then placed within a mold cavity, and molten plastic is injected to encapsulate and bond with the pre-formed substrate, creating a seamless and integrated final product.This advanced manufacturing technique offers a wide range of benefits, including improved product durability, enhanced design flexibility, and reduced production costs. Furthermore, Injection Overmolding allows for the integration of multiple materials, such as rubber, metal, and plastic, resulting in parts with superior functionality and performance.One company at the forefront of Injection Overmolding is {}. With a strong commitment to innovation and excellence, {} has become a leader in the field, providing high-quality overmolding solutions to a diverse range of industries, including automotive, electronics, healthcare, and consumer goods.The company's state-of-the-art facilities and cutting-edge technology enable {} to deliver superior overmolding solutions that meet the specific needs and requirements of their clients. From prototype development to full-scale production, {} offers a comprehensive range of services, including design assistance, material selection, and custom tooling, ensuring that each project is tailored to the unique specifications of the customer.With a team of experienced engineers and technicians, {} has the expertise and capabilities to tackle even the most challenging overmolding projects. The company's relentless pursuit of excellence and continuous investment in research and development have positioned {} as a trusted partner for businesses seeking high-quality, innovative overmolding solutions.In addition to its advanced manufacturing capabilities, {} is also committed to sustainability and environmental responsibility. By utilizing efficient production processes and eco-friendly materials, the company strives to minimize its environmental footprint while delivering top-tier products to its customers. With a focus on innovation, quality, and sustainability, {} is paving the way for the future of plastic manufacturing.As the demand for high-performance, multi-material products continues to grow, Injection Overmolding is poised to revolutionize the plastic manufacturing industry. With its ability to create durable, complex, and integrated parts, Injection Overmolding offers a solution that meets the evolving needs of today's consumers and businesses.In conclusion, Injection Overmolding represents the next frontier in plastic manufacturing, and companies like {} are leading the charge in delivering innovative overmolding solutions to a wide range of industries. With its advanced technology, commitment to excellence, and dedication to sustainability, {} is well-positioned to shape the future of plastic manufacturing and continue to meet the evolving needs of its customers.
Efficient Methods for Machining Large Parts Unveiled
Machining Large Parts: Revolutionizing Manufacturing with Precision and EfficiencyIn today's ever-evolving world of manufacturing, precision and efficiency remain the utmost priority for businesses. As industries continue to push the boundaries of innovation, the demand for machining large parts has soared remarkably. One company, known for its commitment to excellence and cutting-edge technology, has emerged as a leader in this field, providing innovative solutions that are revolutionizing the manufacturing industry. With a strong focus on pushing the limits of what is possible, this company has consistently delivered exceptional results. Through state-of-the-art facilities and a team of skilled professionals, they have perfected the art of machining large parts. Equipped with advanced CNC machines and a diverse range of cutting tools, they have the capability to manufacture components of extraordinary size and complexity, meeting the most stringent specifications and requirements of their clients.Harnessing the immense potential of computer-aided design (CAD) and computer-aided manufacturing (CAM), this company has paved the way for precision machining on an unprecedented scale. By utilizing powerful software solutions, they are able to seamlessly translate digital designs into tangible products, utilizing a streamlined and highly efficient process. This allows for increased accuracy and repeatability, ensuring that every machined part is an exact replica of the original design.One of the key advantages this company offers is their ability to handle large parts without compromising on quality. Their state-of-the-art machining centers can accommodate components that weigh up to several tons, demonstrating their commitment to tackling even the most ambitious projects. By integrating cutting-edge technology with extensive knowledge and experience, they have eliminated the traditional limitations associated with machining large parts, opening up new possibilities for manufacturers across various industries.The company's dedication to excellence and innovation is further exemplified by their team of highly skilled engineers and technicians. With a deep understanding of the intricacies of machining large parts, they meticulously plan and execute each project, ensuring that every component meets the highest standards of quality. Their expertise extends beyond conventional methodologies, allowing them to develop customized solutions that address the unique challenges presented by each project.Furthermore, this company's commitment to sustainable practices sets them apart from their competitors. By leveraging advanced manufacturing techniques, such as near-net-shape machining and optimal material utilization, they reduce waste and minimize environmental impact. Additionally, they prioritize the use of recyclable materials, further contributing to a greener and more sustainable future.The applications of these machined large parts span across various industries, including aerospace, automotive, energy, and heavy machinery. From manufacturing precision-engineered components for aircraft engines to producing critical automotive components, this company's expertise and capabilities are highly sought-after by manufacturers worldwide.In conclusion, the demand for machining large parts continues to rise in today's competitive manufacturing landscape. This company, with its dedication to excellence, innovation, and sustainability, is at the forefront of this revolution. Through the utilization of advanced technology, a skilled workforce, and a commitment to exceptional quality, they have redefined what is possible in precision machining of large parts. As industries continue to evolve, they will undoubtedly remain a driving force in shaping the future of manufacturing, enabling businesses to achieve greater precision and efficiency in their operations.
High-Quality CNC Machined Aluminum Parts for Your Project
CNC Aluminum, a leading manufacturer in the industry, has recently made significant strides in the production of precision components using advanced CNC machining technology. The company has been at the forefront of innovation and has built a reputation for delivering high-quality, custom-made aluminum parts for a wide range of industries.With a state-of-the-art manufacturing facility and a team of highly skilled engineers and technicians, CNC Aluminum has the capability to produce complex components with tight tolerances and intricate designs. The company's CNC machining capabilities allow for the production of parts that meet the highest standards of quality and precision.CNC Aluminum's commitment to excellence is evident in its dedication to investing in the latest CNC machining equipment and technology. The company continuously upgrades its machinery and software to ensure that it stays at the cutting edge of the industry. This investment in technology has enabled CNC Aluminum to expand its capabilities and take on more challenging projects.One of the key strengths of CNC Aluminum is its ability to work closely with its customers to understand their specific requirements and design custom solutions that meet their needs. The company has a team of experienced engineers who are skilled in using advanced CAD/CAM software to create designs and prototypes that can be turned into finished products with a high degree of accuracy.In addition to its technical expertise, CNC Aluminum also places a strong emphasis on quality control and inspection processes. The company has strict quality standards in place to ensure that every component that leaves its facility meets the highest levels of precision and performance. From the initial raw material inspection to the final product testing, CNC Aluminum follows a comprehensive quality assurance process to maintain consistency and reliability in its outputs.Furthermore, CNC Aluminum is committed to sustainability and environmental responsibility. The company utilizes efficient manufacturing processes that minimize waste and energy consumption. It also ensures that its raw materials are sourced from reputable suppliers who adhere to ethical and environmentally friendly practices.As CNC Aluminum continues to grow and expand its capabilities, it remains dedicated to providing its customers with the highest levels of quality, precision, and service. The company's focus on innovation, technology, and customer collaboration sets it apart in the industry and has cemented its position as a leading provider of CNC-machined aluminum components.In conclusion, CNC Aluminum's advancements in precision CNC machining technology, coupled with its dedication to quality, innovation, and customer satisfaction, have positioned the company as a trusted partner for businesses seeking high-quality aluminum components. As the company continues to push the boundaries of what is possible with CNC machining, it is poised to make even greater contributions to the industries it serves.
CNC Machined Aluminum: Unveiling the Impactful Advantages
CNC MACHINED ALUMINIUM: Revolutionizing Precision Manufacturing[Company Introduction]In the fast-paced world of manufacturing, precision and efficiency are paramount. Companies are constantly on the lookout for innovative solutions that can enhance their production processes, reduce costs, and deliver unparalleled quality. One such breakthrough is CNC Machined Aluminium, a cutting-edge technique transforming the landscape of precision manufacturing.[Paragraph 1]CNC Machined Aluminium, or Computer Numerical Control Machining, is a method of using computer-controlled machines to shape and cut aluminium parts with high precision. This advanced manufacturing technique has gained popularity over the years due to its ability to create complex and intricate components with extraordinary accuracy. With CNC Machining, companies can achieve greater efficiency, reduced production times, and improved quality control.[Paragraph 2]The introduction of CNC Machined Aluminium has revolutionized various industries, including automotive, aerospace, electronics, and medical equipment manufacturing, among others. The ability to machine aluminium with unparalleled precision has opened new doors for companies looking to deliver cutting-edge products in these highly competitive sectors.[Paragraph 3]Compared to traditional manufacturing methods such as manual milling or turning, CNC Machined Aluminium offers several significant advantages. Firstly, the precision achieved through this technique is unmatched, ensuring that every part produced meets the strictest tolerance requirements. This accuracy eliminates human error and guarantees consistency in manufacturing, resulting in higher-quality products.[Paragraph 4]Furthermore, CNC Machining enables manufacturers to create complex geometric designs and shapes that were previously impractical or even impossible. The computer-controlled machines can effortlessly execute intricate designs, allowing companies to unleash their creativity and push the boundaries of what is achievable in aluminium manufacturing. This versatility allows for the production of lightweight yet robust components that contribute to fuel efficiency, improved performance, and increased product lifespan.[Paragraph 5]Another crucial advantage of CNC Machined Aluminium is its exceptional efficiency. The automated process significantly reduces the need for human labor, resulting in faster production times and increased productivity. Furthermore, the use of computer-aided design (CAD) software allows for seamless integration of the manufacturing process, reducing errors and minimizing material waste. This streamlined workflow ultimately translates into cost savings for companies, making CNC Machined Aluminium an economically viable choice.[Paragraph 6]It's worth mentioning that CNC Machined Aluminium is not limited to large-scale production. The versatility of this technique allows businesses of all sizes to benefit from its advantages. From prototyping to small and medium-sized batches, CNC Machining offers flexibility and affordability without compromising quality or precision. This accessibility has democratized precision manufacturing, leveling the playing field for businesses eager to bring their innovative ideas to life.[Paragraph 7]While CNC Machined Aluminium has undoubtedly reshaped the manufacturing industry, it is important to note the need for experienced and skilled professionals to harness its full potential. Operating CNC machines and programming the necessary codes require specialized knowledge and expertise. With proper training and an understanding of the intricacies involved, professionals can fully utilize CNC Machining to its maximum effectiveness.[Paragraph 8]In conclusion, CNC Machined Aluminium has emerged as a game-changer in precision manufacturing, providing companies with the tools they need to stay ahead of the competition. The unparalleled precision, versatility, and efficiency offered by this technique have transformed various industries, allowing for the production of complex and high-quality aluminium components. As technology continues to advance, we can expect CNC Machined Aluminium to continue pushing the boundaries of what is achievable in precision manufacturing, fostering innovation and driving industry growth.
The Complete Guide to Plastic Injection Process: Everything You Need to Know
Plastic Injection Process Revolutionizes Manufacturing at {Company Name}{Company Name} is revolutionizing the manufacturing industry with its cutting-edge plastic injection process. This process has enabled the company to produce high-quality plastic parts with unmatched precision and efficiency, making it a leader in the industry.The plastic injection process at {Company Name} begins with the design phase, where experienced engineers and designers work closely with clients to develop the perfect mold for their specific needs. The company utilizes state-of-the-art CAD/CAM software to ensure the accuracy of the design and to optimize the production process. Once the design is finalized, the mold is created using advanced CNC machining tools, which guarantees a flawless finish and precise dimensions.The next step in the plastic injection process is the actual injection molding, where the mold is loaded into the company's top-of-the-line injection molding machines. These machines are equipped with the latest technology, including high-speed, high-pressure injection capabilities, and advanced robotics for precise part removal. This ensures that each part is molded to perfection, with minimal waste and maximum efficiency.{Company Name} specializes in a wide range of plastic materials, including but not limited to, polyethylene, polypropylene, ABS, polycarbonate, and nylon. This versatility allows the company to cater to a diverse range of industries, from automotive and aerospace to consumer electronics and medical devices.The company's plastic injection process also includes comprehensive quality control measures to ensure that each part meets the highest standards. This includes in-process inspections as well as final inspections, where every part is meticulously tested for accuracy, strength, and durability. {Company Name} is committed to delivering flawless products that exceed customer expectations.One of the key advantages of {Company Name}'s plastic injection process is its ability to produce complex, intricate parts with unmatched precision. This has made the company a preferred supplier for clients with highly demanding design requirements. The ability to produce such complex parts has also opened up new opportunities for the company in industries such as aerospace, where precision and performance are paramount.In addition to its advanced manufacturing capabilities, {Company Name} also takes a proactive approach to sustainability and environmental responsibility. The company has implemented eco-friendly practices throughout its production process, including the use of recycled materials and energy-efficient manufacturing techniques. This commitment to sustainability has not only earned {Company Name} a reputation as a responsible manufacturer but has also opened up new opportunities in markets where environmental concerns are top priority.With its state-of-the-art plastic injection process, {Company Name} has established itself as a leader in the manufacturing industry. The company's dedication to precision, efficiency, and sustainability has set it apart from its competitors and has earned it the trust and loyalty of customers worldwide.As {Company Name} continues to push the boundaries of plastic injection technology, it is poised to remain at the forefront of the industry for years to come. With its unwavering commitment to innovation and excellence, the company is well-positioned to meet the evolving needs of its customers and to continue setting new standards for quality and performance in the manufacturing industry.
High-Quality Fixture Plate for CNC Machines: All You Need to Know
CNC Fixture Plate, essential equipment in precision machining, plays a crucial role in ensuring accurate and efficient manufacturing processes. {Company Name}, a leading manufacturer in the machining industry, is dedicated to providing high-quality CNC fixture plates to meet the diverse needs of its global customer base.The CNC Fixture Plate is designed to hold and secure workpieces during machining operations and is a fundamental component in the world of precision engineering. The fixture plate ensures that workpieces are held in place with precision and stability, allowing for the accurate machining of complex parts.{Company Name} has established a stellar reputation for producing state-of-the-art CNC fixtures that are known for their durability, precision, and versatility. The company's fixture plates are designed to withstand heavy loads and high-speed machining operations, making them ideal for a wide range of industrial applications.With a commitment to innovation and excellence, {Company Name} incorporates advanced manufacturing techniques and high-quality materials in the production of its CNC fixture plates. This dedication to quality has enabled the company to become a trusted name in the machining industry, with a strong presence in both domestic and international markets.The CNC Fixture Plate offered by {Company Name} is available in various sizes and configurations to accommodate different machining requirements. Whether it's for milling, drilling, or grinding operations, the company's fixture plates are designed to provide maximum flexibility and efficiency in manufacturing processes.In addition to its standard product range, {Company Name} also offers custom CNC fixture plates to meet specific customer needs. The company's team of experienced engineers and technicians works closely with clients to develop tailored solutions that align with their unique machining requirements.{Company Name}'s dedication to customer satisfaction is evident in its commitment to providing comprehensive support and technical assistance. The company's knowledgeable staff is readily available to offer guidance and advice on selecting the right CNC fixture plate for specific applications, ensuring that customers are able to make informed decisions.Furthermore, {Company Name} places a strong emphasis on quality control, with rigorous testing and inspection procedures in place to ensure that each CNC fixture plate meets the highest standards of precision and performance. This dedication to quality assurance has earned the company the trust and confidence of its customers, who rely on {Company Name} for reliable and consistent products.As an industry leader, {Company Name} is continuously investing in research and development to enhance the performance and functionality of its CNC fixture plates. The company remains at the forefront of technological advancements, embracing new innovations to meet the evolving needs of the machining industry.With a strong focus on customer satisfaction, product quality, and technological innovation, {Company Name} continues to set the standard for excellence in the manufacturing of CNC fixture plates. The company's commitment to delivering superior products and exceptional service has solidified its position as a trusted partner for businesses seeking reliable machining solutions.In conclusion, the CNC Fixture Plate offered by {Company Name} represents a pinnacle of quality, precision, and reliability in the machining industry. With a dedication to excellence and a passion for innovation, {Company Name} continues to play a vital role in shaping the future of precision engineering with its advanced CNC fixture plates.
Top Quality Plastic Parts for Various Applications
Plastic Parts, a leading manufacturer in the automotive industry, has recently made significant strides in the development of innovative plastic components for a range of vehicles. The company, known for its commitment to quality and cutting-edge technology, has been dedicated to pushing the boundaries of what is possible in the world of automotive plastics. With a focus on sustainability and efficiency, Plastic Parts has been at the forefront of creating solutions that not only meet the highest industry standards but also contribute to a greener and more eco-friendly future.With a history of excellence and a track record of delivering top-notch products, Plastic Parts has solidified its position as a go-to supplier for many major automotive companies. As the demand for lightweight and durable materials continues to grow in the automotive industry, the company has risen to the challenge by investing in state-of-the-art technology and recruiting top talent in the field.One of the key areas of focus for Plastic Parts has been the development of plastic components for electric vehicles. With the global shift towards more sustainable forms of transportation, the demand for electric vehicles has been steadily rising. In response, Plastic Parts has been working tirelessly to develop high-performance plastic parts that are specifically designed to meet the unique needs of electric vehicles. From battery housing to interior components, the company has been pioneering new solutions that are both lightweight and strong, contributing to the overall efficiency and performance of electric vehicles.In addition to its work in the electric vehicle sector, Plastic Parts has also been making waves in the development of plastic components for traditional internal combustion engine vehicles. With a keen eye on reducing vehicle weight and improving fuel efficiency, the company has been working closely with automotive manufacturers to develop innovative solutions that meet their specific needs. From engine components to exterior body panels, Plastic Parts has been utilizing advanced materials and manufacturing techniques to deliver products that not only meet industry standards but also exceed customer expectations.Furthermore, Plastic Parts has been a trailblazer in the realm of sustainable plastics. The company has been dedicated to the use of recycled and bio-based materials in its manufacturing processes, with a goal of reducing its environmental impact. By incorporating these sustainable materials into its products, Plastic Parts has not only been able to reduce its carbon footprint but has also been able to deliver high-quality, eco-friendly solutions to its customers.With a focus on continuous improvement and innovation, Plastic Parts has been able to stay ahead of the curve in the automotive industry. The company's commitment to research and development, coupled with its investment in cutting-edge technology, has allowed it to remain competitive in a fast-paced and ever-changing market. By staying at the forefront of industry trends and customer needs, Plastic Parts has been able to consistently deliver products that are not only reliable and efficient but also environmentally responsible.Looking ahead, Plastic Parts is poised to continue its upward trajectory in the automotive industry. With a strong focus on sustainability, innovation, and customer satisfaction, the company is well-positioned to meet the evolving needs of the automotive market. As the demand for high-quality plastic components continues to rise, Plastic Parts is ready and equipped to lead the way, setting new standards for excellence in the industry.