Precision Titanium Machining Services: The Ultimate Guide
By:Admin
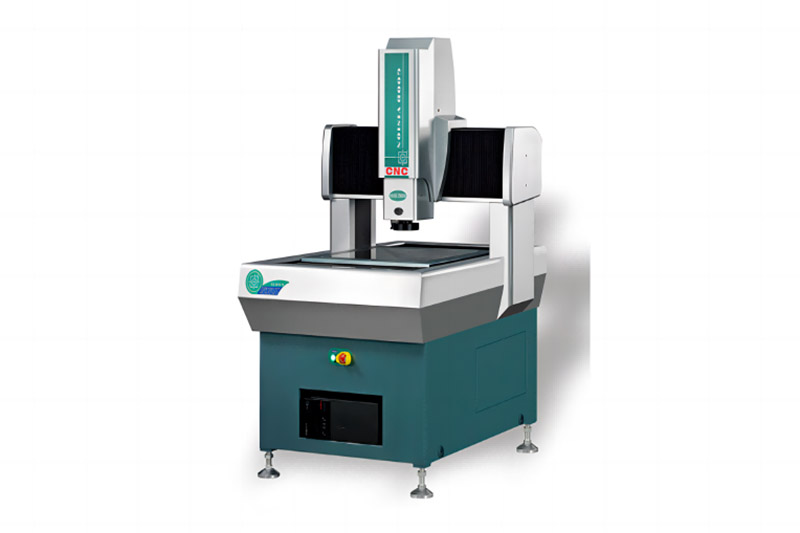
As the aerospace industry continues to advance and evolve, the demand for high-quality, precision machined components has never been greater. This is where () comes in. Specializing in titanium machining, () has quickly become a trusted partner for aerospace manufacturers around the globe. With state-of-the-art technology and a commitment to excellence, () is leading the way in the advancement of aerospace manufacturing.
With a history dating back to 1995, () has established itself as a premier provider of precision machined components for a wide range of industries, including aerospace, automotive, and medical. The company's dedication to quality and innovation has allowed it to stay at the forefront of technological advancements in manufacturing.
One of the key areas of expertise for () is titanium machining. Titanium is a popular material in the aerospace industry due to its high strength-to-weight ratio and excellent corrosion resistance. However, titanium is also known for being a challenging material to machine due to its high strength and low thermal conductivity. This is where ()'s advanced machining capabilities come into play.
By leveraging state-of-the-art CNC machining equipment and cutting-edge tooling, () is able to precisely machine titanium components to the tight tolerances required for aerospace applications. This allows aerospace manufacturers to benefit from the unique properties of titanium while ensuring the highest level of quality and reliability in their components.
In addition to its expertise in titanium machining, () also offers a range of other services to support the aerospace industry. From 5-axis machining to complex assembly and inspection services, () is equipped to handle the most demanding aerospace manufacturing requirements.
One of the key differentiators for () is its commitment to continuous improvement and innovation. The company invests heavily in research and development to stay ahead of the curve in manufacturing technology. This has allowed () to develop advanced machining processes and techniques that are specifically tailored to the unique properties of titanium and other challenging materials.
In recent years, () has also expanded its capabilities to include additive manufacturing, also known as 3D printing. This technology has revolutionized the aerospace industry by allowing for the production of complex geometries and lightweight structures that were previously impossible to achieve through traditional machining methods. ()'s investment in additive manufacturing further demonstrates its commitment to pushing the boundaries of what is possible in aerospace manufacturing.
The aerospace industry is known for its rigorous quality and regulatory requirements, and () takes these standards seriously. The company is AS9100 and ISO 9001 certified, ensuring that its manufacturing processes adhere to the highest standards of quality and consistency. This commitment to quality has earned () a reputation as a trusted partner for aerospace manufacturers who require the utmost reliability in their components.
Looking to the future, () is poised to continue leading the way in aerospace manufacturing. With its strong focus on technological advancement and commitment to quality, () is well-positioned to meet the evolving needs of the aerospace industry. As the demand for lightweight, high-performance components continues to grow, () is prepared to deliver the precision machined solutions that will drive the future of aerospace engineering.
In conclusion, ()'s expertise in titanium machining and dedication to innovation make it a key player in the aerospace manufacturing industry. With a track record of excellence and a commitment to continuous improvement, () is well-equipped to meet the evolving needs of the aerospace industry and drive the future of aerospace manufacturing.
Company News & Blog
Top Quality Injection Molding Parts for Your Business
Injection Molding Parts Sees Significant Growth in {}'s BusinessWith the increasing demand for high-quality injection molding parts, {} has experienced significant growth in its business in recent years. As a leading provider of injection molding parts, {} has been able to create a niche for itself in the industry by offering top-notch products and exceptional customer service.{} has been in the injection molding industry for over a decade and has established itself as a reliable and trusted supplier of high-quality parts for various industries. The company's commitment to excellence and innovation has enabled it to stay ahead of the competition and meet the diverse needs of its customers.The injection molding process involves the use of molten materials, typically plastic, to create various components and parts for a wide range of applications. {} has invested heavily in advanced machinery and technology to ensure that it can produce parts that meet the highest standards of quality and precision. The company's manufacturing facilities are equipped with state-of-the-art injection molding machines and automated production lines, allowing it to deliver consistent and reliable results.One of the key factors that have contributed to {}'s success in the injection molding industry is its team of skilled engineers and technicians. The company's staff is highly knowledgeable and experienced in the injection molding process, enabling them to develop innovative solutions and produce complex parts with tight tolerances. {}'s team is dedicated to providing customized solutions to its customers, ensuring that their specific requirements are met with precision and efficiency.In addition to its technical expertise, {} also places a strong emphasis on customer service and satisfaction. The company prides itself on building long-term relationships with its clients, understanding their unique needs, and delivering tailored solutions that exceed their expectations. {}'s commitment to customer service has helped it build a loyal and satisfied customer base, driving its continued growth and success in the industry.{}'s injection molding parts are used in a wide range of applications, including automotive, electronics, consumer products, and medical devices. The company's ability to produce parts with complex geometries and tight tolerances has enabled it to serve diverse industries and cater to various production requirements. With a focus on continuous improvement and innovation, {} is constantly exploring new materials and techniques to expand its capabilities and offer cutting-edge solutions to its customers.As the demand for high-quality injection molding parts continues to grow, {} remains committed to investing in its people, technology, and processes to stay at the forefront of the industry. The company is dedicated to upholding the highest standards of quality and precision in its products, and it strives to be a reliable partner for its customers, offering them the solutions they need to succeed in their respective industries.In conclusion, {} has seen significant growth in its business as a leading provider of injection molding parts. With its focus on innovation, quality, and customer service, the company has been able to build a strong reputation and establish itself as a key player in the injection molding industry. As the demand for high-quality parts continues to rise, {} is well-positioned to meet the needs of its customers and drive continued success in the years to come.
Top Milling Centers for Precision Machining
Milling Centers Revolutionizing Precision MachiningIn the world of precision machining, milling centers have become a crucial component of the manufacturing process. These state-of-the-art machines have the capability to perform a wide range of tasks, from simple drilling and tapping to complex contouring and 5-axis machining. With their advanced technology and precision engineering, milling centers have revolutionized the way in which parts and components are manufactured.One company at the forefront of this revolution is {}. With decades of experience in the manufacturing industry, {} has established itself as a leader in the production of high-quality milling centers. Their machines are known for their exceptional accuracy, reliability, and versatility, making them the go-to choice for a wide range of industries, including aerospace, automotive, medical, and more.The key to the success of {}'s milling centers lies in their advanced features and capabilities. These machines are equipped with high-speed spindles, automatic tool changers, and sophisticated control systems that enable them to perform complex machining operations with ease. Additionally, {}'s milling centers are designed to be highly rigid and stable, ensuring that they can achieve the tight tolerances and superior surface finishes that are required in modern manufacturing.One of the most impressive aspects of {}'s milling centers is their ability to perform multi-axis machining. This capability allows for the production of highly complex parts and components that would be nearly impossible to manufacture using conventional machining methods. With multi-axis machining, {}'s milling centers can create intricate shapes and contours with precision and accuracy, opening up new possibilities for designers and engineers.In addition to their advanced technology, {}'s milling centers are also designed with efficiency and productivity in mind. These machines are equipped with features such as high-speed rapids, chip conveyors, and coolant systems that help to optimize the machining process and minimize downtime. This not only results in lower production costs but also allows manufacturers to meet tight production deadlines with ease.Another major advantage of {}'s milling centers is their user-friendly design. These machines are equipped with intuitive controls and interfaces that make them easy to operate, even for less experienced machinists. This means that manufacturers can quickly set up and program {}'s milling centers to produce high-quality parts and components with minimal training or supervision.Furthermore, {} provides comprehensive training and support to ensure that customers are able to get the most out of their milling centers. Whether it's troubleshooting technical issues, optimizing machining processes, or providing guidance on tooling and fixturing, {}'s team of experts is dedicated to helping their customers achieve success with their milling centers.With the increasing demand for complex and high-precision components, the role of milling centers in modern manufacturing is more important than ever. Companies like {} are continuously pushing the boundaries of what is possible with their innovative machines, allowing manufacturers to produce parts and components that were previously considered unfeasible. As the industry continues to evolve, milling centers will undoubtedly play a vital role in shaping the future of precision machining.
Quality Plastic Injection Parts: Find Reliable Suppliers Here
Plastic Injection Parts have become an essential component in various industries around the world. These parts are used in manufacturing processes across different sectors, including automotive, electronics, medical, and consumer goods. The versatility of plastic injection parts makes them an indispensable tool for creating intricate and complex components that are integral to the functioning of many products.Company XXX is a leading manufacturer of plastic injection parts, specializing in providing high-quality and customized solutions for a wide range of industries. With state-of-the-art equipment and advanced technologies, Company XXX has established itself as a reliable and trusted partner for businesses seeking precision-engineered plastic components.The process of plastic injection molding is at the core of Company XXX's operations. This method involves melting plastic pellets and injecting the molten material into a mold, where it cools and solidifies into the desired shape. The ability to create complex geometries and intricate designs makes plastic injection molding the preferred choice for producing a vast array of components across different industries.Company XXX's expertise in plastic injection molding enables them to offer a comprehensive range of services to their clients. From design and prototyping to production and assembly, the company provides end-to-end solutions that meet the specific requirements of their customers. Their team of experienced engineers and technicians work closely with clients to understand their needs and deliver tailored solutions that meet the highest industry standards.The versatility of plastic injection parts is exemplified in the automotive industry, where these components play a crucial role in the manufacturing of vehicles. From interior and exterior trims to complex engine and transmission components, plastic injection parts are integral to the functionality and aesthetics of modern automobiles. Company XXX's extensive experience in the automotive sector has positioned them as a go-to supplier for high-quality plastic components that meet the stringent demands of the industry.In the electronics industry, the demand for precision-engineered plastic parts is driven by the need for smaller, lighter, and more durable components. Company XXX's expertise in producing intricate and high-precision parts makes them a valuable partner for electronics manufacturers looking to integrate plastic components into their products. From circuit board housings to connectors and enclosures, the company offers solutions that meet the stringent requirements of the electronics industry.The medical sector presents unique challenges when it comes to manufacturing plastic components. The need for strict tolerances, biocompatibility, and regulatory compliance makes it essential to work with a partner that has a deep understanding of the complexities of the medical industry. Company XXX's commitment to quality and precision makes them a preferred supplier for medical device manufacturers, providing them with the assurance that their plastic components meet the highest standards for safety and performance.Beyond these industries, Company XXX's capabilities extend to serving the needs of consumer goods manufacturers, where the demand for aesthetically pleasing and functional plastic parts is ever-growing. From household appliances and sporting goods to toys and packaging, the company's expertise in plastic injection molding enables them to deliver solutions that enhance the quality and appeal of consumer products.In conclusion, plastic injection parts have become an indispensable component of modern manufacturing across various industries. The ability to create complex geometries, precision-engineered designs, and high-quality components has made plastic injection molding a preferred choice for businesses seeking reliable and customized solutions. With its commitment to quality, precision, and customer satisfaction, Company XXX has established itself as a leading manufacturer of plastic injection parts, serving the diverse needs of industries around the world.
CNC Machined Aluminum: Unveiling the Impactful Advantages
CNC MACHINED ALUMINIUM: Revolutionizing Precision Manufacturing[Company Introduction]In the fast-paced world of manufacturing, precision and efficiency are paramount. Companies are constantly on the lookout for innovative solutions that can enhance their production processes, reduce costs, and deliver unparalleled quality. One such breakthrough is CNC Machined Aluminium, a cutting-edge technique transforming the landscape of precision manufacturing.[Paragraph 1]CNC Machined Aluminium, or Computer Numerical Control Machining, is a method of using computer-controlled machines to shape and cut aluminium parts with high precision. This advanced manufacturing technique has gained popularity over the years due to its ability to create complex and intricate components with extraordinary accuracy. With CNC Machining, companies can achieve greater efficiency, reduced production times, and improved quality control.[Paragraph 2]The introduction of CNC Machined Aluminium has revolutionized various industries, including automotive, aerospace, electronics, and medical equipment manufacturing, among others. The ability to machine aluminium with unparalleled precision has opened new doors for companies looking to deliver cutting-edge products in these highly competitive sectors.[Paragraph 3]Compared to traditional manufacturing methods such as manual milling or turning, CNC Machined Aluminium offers several significant advantages. Firstly, the precision achieved through this technique is unmatched, ensuring that every part produced meets the strictest tolerance requirements. This accuracy eliminates human error and guarantees consistency in manufacturing, resulting in higher-quality products.[Paragraph 4]Furthermore, CNC Machining enables manufacturers to create complex geometric designs and shapes that were previously impractical or even impossible. The computer-controlled machines can effortlessly execute intricate designs, allowing companies to unleash their creativity and push the boundaries of what is achievable in aluminium manufacturing. This versatility allows for the production of lightweight yet robust components that contribute to fuel efficiency, improved performance, and increased product lifespan.[Paragraph 5]Another crucial advantage of CNC Machined Aluminium is its exceptional efficiency. The automated process significantly reduces the need for human labor, resulting in faster production times and increased productivity. Furthermore, the use of computer-aided design (CAD) software allows for seamless integration of the manufacturing process, reducing errors and minimizing material waste. This streamlined workflow ultimately translates into cost savings for companies, making CNC Machined Aluminium an economically viable choice.[Paragraph 6]It's worth mentioning that CNC Machined Aluminium is not limited to large-scale production. The versatility of this technique allows businesses of all sizes to benefit from its advantages. From prototyping to small and medium-sized batches, CNC Machining offers flexibility and affordability without compromising quality or precision. This accessibility has democratized precision manufacturing, leveling the playing field for businesses eager to bring their innovative ideas to life.[Paragraph 7]While CNC Machined Aluminium has undoubtedly reshaped the manufacturing industry, it is important to note the need for experienced and skilled professionals to harness its full potential. Operating CNC machines and programming the necessary codes require specialized knowledge and expertise. With proper training and an understanding of the intricacies involved, professionals can fully utilize CNC Machining to its maximum effectiveness.[Paragraph 8]In conclusion, CNC Machined Aluminium has emerged as a game-changer in precision manufacturing, providing companies with the tools they need to stay ahead of the competition. The unparalleled precision, versatility, and efficiency offered by this technique have transformed various industries, allowing for the production of complex and high-quality aluminium components. As technology continues to advance, we can expect CNC Machined Aluminium to continue pushing the boundaries of what is achievable in precision manufacturing, fostering innovation and driving industry growth.
Custom CNC Machining Services for Brass Parts: Top Benefits and Uses
CNC Machining Brass - A New Milestone for CompanyIn the ever-evolving world of manufacturing, precision and efficiency are non-negotiable. Companies are consistently seeking newer and better ways to create high-quality products and meet the demands of their customers. One company that has embraced this challenge head-on is {}. {} has been a leader in the manufacturing industry for decades, known for its dedication to innovation and cutting-edge technology. Recently, the company achieved a new milestone with the implementation of CNC machining for brass components.CNC machining, or computer numerical control machining, is a manufacturing process that utilizes computerized controls and machine tools to remove material from a workpiece. This process allows for extremely precise and intricate cuts, resulting in high-quality, custom parts. While CNC machining is not a new technology, the application of this method to brass components is a significant advancement for {} and a testament to their commitment to excellence.Brass is a popular material in the manufacturing industry due to its excellent properties, including high corrosion resistance, electrical conductivity, and aesthetic appeal. However, machining brass can be challenging due to its tendency to produce chips that can cause tool wear and damage. With the implementation of CNC machining, {} has overcome these challenges and elevated their production capabilities to a new level.The decision to incorporate CNC machining for brass components was not taken lightly. According to the company's engineering team, extensive research and testing were conducted to ensure the successful integration of this advanced manufacturing process. Through meticulous planning and collaboration with industry experts, {} was able to optimize the CNC machining process for brass, resulting in superior quality and consistency in their products.The benefits of CNC machining for brass components are manifold. Not only does it enable {} to produce intricate and complex parts with unparalleled precision, but it also enhances efficiency and reduces lead times. Additionally, the use of CNC machining for brass has positioned {} to take on new and challenging projects, further solidifying their reputation as a leader in the industry.Furthermore, the implementation of CNC machining for brass components aligns with {}'s commitment to sustainability. By utilizing advanced manufacturing processes that minimize material waste and energy consumption, the company is taking proactive steps towards reducing its environmental impact and meeting the growing demand for sustainable production methods.The impact of this milestone goes beyond the walls of {}. With the introduction of CNC machining for brass components, the company is poised to offer its clients a wider range of products and solutions, catering to diverse industries such as automotive, aerospace, electronics, and more. This expansion of capabilities has the potential to open new doors and foster long-lasting partnerships with customers who require top-notch brass components for their applications.As {} continues to push the boundaries of innovation, the incorporation of CNC machining for brass components stands as a testament to their unwavering dedication to excellence and customer satisfaction. With this new milestone, the company is not only raising the bar for the manufacturing industry but is also solidifying its position as a trailblazer in the field.In conclusion, the implementation of CNC machining for brass components at {} represents a significant leap forward in their pursuit of manufacturing excellence. This integration not only enhances their production capabilities but also underscores their commitment to embracing advanced technology and providing superior solutions to their clients. As the manufacturing landscape continues to evolve, {} has proven once again that they are at the forefront of innovation, setting a new standard for precision and quality in the industry.
Precision Titanium Machining Services: The Ultimate Guide
Titanium Machining: The Future of Aerospace ManufacturingAs the aerospace industry continues to advance and evolve, the demand for high-quality, precision machined components has never been greater. This is where () comes in. Specializing in titanium machining, () has quickly become a trusted partner for aerospace manufacturers around the globe. With state-of-the-art technology and a commitment to excellence, () is leading the way in the advancement of aerospace manufacturing.With a history dating back to 1995, () has established itself as a premier provider of precision machined components for a wide range of industries, including aerospace, automotive, and medical. The company's dedication to quality and innovation has allowed it to stay at the forefront of technological advancements in manufacturing.One of the key areas of expertise for () is titanium machining. Titanium is a popular material in the aerospace industry due to its high strength-to-weight ratio and excellent corrosion resistance. However, titanium is also known for being a challenging material to machine due to its high strength and low thermal conductivity. This is where ()'s advanced machining capabilities come into play.By leveraging state-of-the-art CNC machining equipment and cutting-edge tooling, () is able to precisely machine titanium components to the tight tolerances required for aerospace applications. This allows aerospace manufacturers to benefit from the unique properties of titanium while ensuring the highest level of quality and reliability in their components.In addition to its expertise in titanium machining, () also offers a range of other services to support the aerospace industry. From 5-axis machining to complex assembly and inspection services, () is equipped to handle the most demanding aerospace manufacturing requirements.One of the key differentiators for () is its commitment to continuous improvement and innovation. The company invests heavily in research and development to stay ahead of the curve in manufacturing technology. This has allowed () to develop advanced machining processes and techniques that are specifically tailored to the unique properties of titanium and other challenging materials.In recent years, () has also expanded its capabilities to include additive manufacturing, also known as 3D printing. This technology has revolutionized the aerospace industry by allowing for the production of complex geometries and lightweight structures that were previously impossible to achieve through traditional machining methods. ()'s investment in additive manufacturing further demonstrates its commitment to pushing the boundaries of what is possible in aerospace manufacturing.The aerospace industry is known for its rigorous quality and regulatory requirements, and () takes these standards seriously. The company is AS9100 and ISO 9001 certified, ensuring that its manufacturing processes adhere to the highest standards of quality and consistency. This commitment to quality has earned () a reputation as a trusted partner for aerospace manufacturers who require the utmost reliability in their components.Looking to the future, () is poised to continue leading the way in aerospace manufacturing. With its strong focus on technological advancement and commitment to quality, () is well-positioned to meet the evolving needs of the aerospace industry. As the demand for lightweight, high-performance components continues to grow, () is prepared to deliver the precision machined solutions that will drive the future of aerospace engineering.In conclusion, ()'s expertise in titanium machining and dedication to innovation make it a key player in the aerospace manufacturing industry. With a track record of excellence and a commitment to continuous improvement, () is well-equipped to meet the evolving needs of the aerospace industry and drive the future of aerospace manufacturing.
Understanding the Steps Involved in the Milling Process
[Company Name] Revolutionizes the Milling Process, Enhancing Efficiency and Quality[City, Date] - [Company Name], a leading innovator in the manufacturing industry, is making waves with its revolutionary milling process. By incorporating cutting-edge technology and advanced techniques, the company has accomplished remarkable improvements in efficiency and quality, setting new industry standards.The milling process is a crucial step in the manufacturing of various products, ranging from automotive components to consumer electronics. Traditionally, this process involves removing material from a workpiece using a rotating cutting tool. However, [Company Name] has taken this fundamental concept to new heights.With a focus on innovation, [Company Name] has developed a state-of-the-art milling process that surpasses traditional methods in terms of speed and precision. By leveraging advanced computer algorithms and artificial intelligence, the company has optimized the milling parameters to ensure the perfect balance between material removal and preservation.One key aspect of [Company Name]'s milling process is the integration of advanced sensors and monitoring systems. These sensors provide real-time feedback on crucial variables such as cutting forces, temperatures, and tool wear. By constantly monitoring these parameters, [Company Name] can make precise adjustments to the milling process, ensuring optimal performance and preventing any potential faults or errors.Additionally, [Company Name] has pioneered an intelligent tooling system that further enhances the efficiency of the milling process. This system utilizes smart tools equipped with sensors to continuously collect data during the machining operation. This data is then analyzed by sophisticated algorithms, allowing for predictive maintenance and precise tool life management. As a result, downtime due to unexpected tool failures is significantly reduced, leading to increased productivity and cost savings.Furthermore, [Company Name] has prioritized sustainability in its milling process. By implementing eco-friendly cutting fluids and optimizing the chip evacuation process, the company has minimized waste and reduced environmental impact. This commitment to sustainability aligns with [Company Name]'s corporate values and resonates with environmentally conscious clients.In terms of quality control, [Company Name] has introduced advanced inspection systems that guarantee the highest level of precision and accuracy. Through the utilization of non-contact measurement technologies, such as laser scanners and optical systems, the company can perform detailed inspections on complex components, ensuring conformity to the tightest tolerances.Customer satisfaction is paramount for [Company Name], and as such, the company provides comprehensive support throughout the milling process. Their team of highly skilled engineers assists clients in selecting the appropriate milling strategies and tools for their specific needs. Additionally, [Company Name] offers training programs and workshops to ensure that operators are well-equipped to utilize the milling process to its full potential.The impact of [Company Name]'s milling process is already being felt across a wide range of industries. Customers have praised the enhanced productivity, improved part quality, and reduced lead times resulting from the adoption of this innovative technology. Numerous companies have reported significant cost savings and increased competitiveness as a direct result of partnering with [Company Name].Looking towards the future, [Company Name] remains committed to pushing the boundaries of milling technology. Through ongoing research and development efforts, the company strives to introduce even more advanced milling techniques that will revolutionize the manufacturing industry once again.In conclusion, [Company Name]'s revolutionary milling process has transformed traditional machining into a high-tech, efficient, and sustainable practice. By seamlessly integrating cutting-edge technology and advanced techniques, the company has set a new industry standard for milling, driving productivity, quality, and cost-effectiveness to unparalleled heights.
Advanced CNC Machine Technology for Increased Precision and Efficiency
CNC Machine Technology Revolutionizes Manufacturing IndustryIn today's modern manufacturing industry, efficiency and precision are essential in producing high-quality products. The advent of CNC (Computer Numerical Control) machine technology has revolutionized the way manufacturers approach production, leading to increased productivity, reduced costs, and higher quality products.CNC machines have become an integral part of the manufacturing process, allowing for automated and precise machining of various materials, including metal, plastic, and wood. These machines are operated by computer programs that control the movement and operation of the cutting tools, resulting in highly accurate and consistent production.One of the leading providers of CNC machine technology, {}, has been at the forefront of innovation in this field. With a comprehensive range of CNC machines and cutting-edge technology, they have been empowering manufacturers to achieve greater efficiency and precision in their production processes.The company's CNC machines are equipped with advanced features such as multi-axis control, automatic tool changers, and high-speed machining capabilities, allowing for complex and intricate parts to be manufactured with ease. Furthermore, their CNC systems are designed to be user-friendly, with intuitive interfaces and programming software that streamline the production process.The introduction of CNC machine technology has significantly reduced the reliance on manual labor in manufacturing, leading to increased productivity and higher output levels. Additionally, the precision and accuracy of CNC machines have resulted in a decrease in material waste and rework, leading to cost savings for manufacturers.With the integration of CAD (Computer-Aided Design) and CAM (Computer-Aided Manufacturing) software, CNC machines can produce complex and intricate parts with ease. This synergy between design and production has allowed for rapid prototyping and shorter lead times, enabling manufacturers to bring their products to market faster.The widespread adoption of CNC machine technology has also opened up new possibilities in terms of customization and variability in manufacturing. With the ability to easily reprogram CNC machines, manufacturers can quickly adjust production parameters to accommodate design changes or fulfill custom orders, providing greater flexibility in the production process.Furthermore, the advancements in CNC machine technology have also led to improvements in the overall quality of manufactured products. The precision and consistency of CNC machining result in higher quality parts, reducing the likelihood of defects and errors in production.The impact of CNC machine technology extends beyond just the manufacturing industry. With the ability to produce parts with high precision and accuracy, CNC machines have found applications in various industries, including aerospace, automotive, medical, and consumer goods.As the demand for high-quality and complex parts continues to grow, the role of CNC machine technology in manufacturing will only become more prominent. With continued advancements in automation, connectivity, and artificial intelligence, the future of CNC machining is poised to further revolutionize the manufacturing industry.In conclusion, CNC machine technology has reshaped the landscape of manufacturing, empowering manufacturers to achieve higher levels of efficiency, precision, and quality in their production processes. The advancements made by companies like {} have propelled the industry into a new era of manufacturing, where automation, customization, and innovation are driving forces. As we look to the future, the influence of CNC machine technology in manufacturing will continue to grow, shaping the way products are designed, produced, and brought to market.
Durable Stainless Steel: The Ultimate Material for CNC Machining
CNC Stainless Steel, a leading global provider of high-quality stainless steel products, has recently made waves in the industry with its latest innovation. The company, known for its precision engineering and cutting-edge technology, has managed to revolutionize the stainless steel manufacturing process.With over 20 years of experience in the industry, CNC Stainless Steel has been at the forefront of delivering top-notch stainless steel solutions to a wide range of industries, including aerospace, automotive, medical, and more. The company prides itself on its commitment to quality, precision, and reliability, which has earned it a sterling reputation among its clients and peers.One of CNC Stainless Steel's most recent developments is a breakthrough in the CNC machining of stainless steel components. The company has introduced state-of-the-art equipment and techniques that allow for unparalleled precision and efficiency in the production of stainless steel parts. This advancement has not only improved the quality of their products but has also significantly reduced lead times, allowing CNC Stainless Steel to better meet the demands of its customers.In addition to its cutting-edge machining capabilities, CNC Stainless Steel also places a strong emphasis on innovation and sustainable practices. The company is constantly researching and developing new processes to minimize waste, reduce energy consumption, and improve the environmental footprint of its operations. This commitment to sustainability has not only positioned CNC Stainless Steel as an industry leader but has also garnered praise and recognition from various environmental organizations.Furthermore, CNC Stainless Steel has strategically invested in its workforce, ensuring that its team is comprised of highly skilled and experienced professionals. The company provides ongoing training and professional development opportunities to its employees, fostering a culture of continuous improvement and innovation. This dedication to its workforce has not only resulted in a highly efficient and capable team but has also contributed to CNC Stainless Steel's ability to deliver superior products and services to its clients.With its latest breakthrough in CNC machining and its unwavering dedication to quality, precision, and sustainability, CNC Stainless Steel is poised to maintain its position as a top contender in the global stainless steel market. The company's commitment to innovation and its ability to adapt to the ever-changing needs of its clients make it a formidable force in the industry.Looking ahead, CNC Stainless Steel aims to continue pushing the boundaries of stainless steel manufacturing, seeking new opportunities to improve its products and processes. The company remains focused on providing its customers with the highest quality stainless steel components while remaining environmentally conscious and efficient in its operations.In conclusion, CNC Stainless Steel has once again proven itself as a leader in the stainless steel industry with its latest advancements in CNC machining. The company's dedication to quality, precision, and sustainability, combined with its ongoing commitment to innovation and excellence, solidify its position as a trusted partner for businesses seeking high-quality stainless steel products. As the industry continues to evolve, CNC Stainless Steel remains at the forefront, setting the standard for excellence in stainless steel manufacturing.
Discover the Benefits of Rapid CNC Machining for Quality Results
Title: Leading CNC Machining Service Provider Offers Precision and Efficiency to Industrial Clients Introduction: In the dynamic world of industrial manufacturing, precision and efficiency are key factors that can make or break a company's success. Recognizing this, Rapid CNC Machining (brand name removed), a leading CNC machining service provider, has emerged as a reliable partner for industrial clients seeking high-quality and precise manufacturing solutions. With a commitment to cutting-edge technology, exceptional customer service, and seamless project management, Rapid CNC Machining continues to strengthen its position as a trusted name in the industry.Body:1. Company Overview and Expertise:Established in the heart of the manufacturing hub, Rapid CNC Machining has a proven track record of delivering precision-machined parts and components to a wide array of industries. The company's state-of-the-art facility houses an extensive range of CNC machines, allowing them to cater to diverse manufacturing needs. Their team of highly skilled technicians, engineers, and project managers ensure that each project is executed with utmost precision and efficiency.2. Technological Advancements:Rapid CNC Machining has stayed ahead of the competition by consistently investing in the latest CNC machining technology. The company's cutting-edge equipment enables them to provide comprehensive solutions, including design assistance, prototyping, custom part production, and mass production. By utilizing advanced software and tools, Rapid CNC Machining optimizes the manufacturing process, reducing lead times and maximizing product quality.3. Diverse Industry Applications:With an extensive portfolio of successful projects, Rapid CNC Machining serves various industries, including aerospace, automotive, medical, electronics, and more. Their expertise in machining a wide range of materials, including aluminum, stainless steel, titanium, plastics, and composites, enables them to meet the unique requirements of each industry. Whether it is complex aerospace components or intricate medical device parts, Rapid CNC Machining ensures the highest standards of accuracy, functionality, and durability.4. Commitment to Quality Assurance:Rapid CNC Machining places great emphasis on quality assurance throughout the manufacturing process. From initial design analysis to final inspection, the company employs rigorous quality control measures to guarantee adherence to specifications and customer expectations. Their ISO 9001-certified facility ensures consistent quality and compliance with industry standards, earning them a reputation for excellence.5. Customer-Centric Approach:Understanding the importance of strong customer relationships, Rapid CNC Machining prioritizes open communication and collaboration with clients. Their skilled project management team ensures seamless coordination, from project initiation to product delivery. With a commitment to transparency, Rapid CNC Machining provides regular progress updates, addresses any concerns promptly, and maintains strict confidentiality protocols.6. Sustainable Manufacturing Practices:In an era of growing environmental consciousness, Rapid CNC Machining strives to implement sustainable manufacturing practices. By optimizing material utilization, reducing waste, and utilizing energy-efficient machinery, the company minimizes its environmental footprint. Moreover, investing in research and development, Rapid CNC Machining actively explores greener alternatives, ensuring its manufacturing processes are aligned with sustainability goals.7. Global Reach and Future Outlook:Rapid CNC Machining has established a global footprint by serving clients from various countries and regions. Their commitment to delivering exceptional value and their strong reputation for reliable service has positioned them as a preferred CNC machining partner worldwide. As the company continues to expand its capabilities, invest in technology, and nurture customer relationships, Rapid CNC Machining aims to remain at the forefront of the industry.Conclusion:Through consistent innovation, dedication to customer satisfaction, and a focus on precision and efficiency, Rapid CNC Machining has solidified its position as a leading provider of CNC machining services. Their state-of-the-art facility, diverse industry applications, and commitment to sustainable practices set them apart from competitors. As industrial manufacturing continues to evolve, the company's unwavering commitment to quality and customer-centricity ensures they will remain a trusted partner for businesses seeking superior CNC machining solutions.