- Precision Machining: A Guide to High-Quality Manufacturing
By:Admin
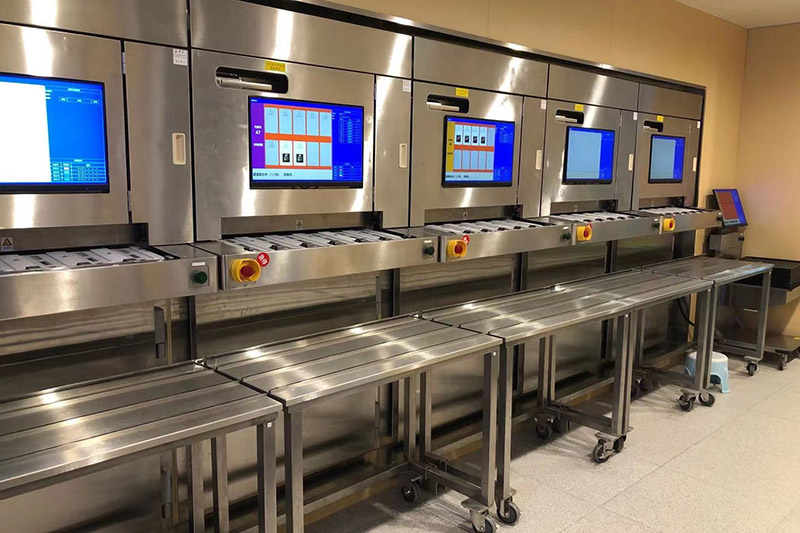
The company's precision machining capabilities are driven by advanced technologies and a team of highly skilled engineers and technicians. (remove brand name) specializes in producing complex components with tight tolerances and high surface finishes for a wide range of industries, including aerospace, automotive, medical, and defense.
One of the key factors that sets (remove brand name) apart from its competitors is its commitment to investing in the latest equipment and technology. The company's state-of-the-art manufacturing facilities are equipped with advanced CNC machinery, including multi-axis milling and turning centers, EDM machines, and inspection equipment. This enables (remove brand name) to consistently deliver precision parts that meet the most rigorous specifications and standards.
In addition to its cutting-edge technology, (remove brand name) places a strong emphasis on quality control and process optimization. The company follows strict quality management systems and adheres to industry best practices to ensure that every component that leaves its facility is of the highest quality. (remove brand name) also offers value-added services such as design for manufacturability and engineering support to assist customers in achieving their manufacturing goals.
Furthermore, (remove brand name) is known for its quick turnaround times and reliable delivery schedules. The company understands the importance of on-time delivery in the manufacturing industry and has implemented efficient production processes to meet the demands of its customers. (remove brand name) works closely with its clients to understand their specific needs and timeline requirements, and strives to exceed expectations with its fast and reliable service.
With a proven track record of delivering precision components to some of the most demanding industries, (remove brand name) has earned a reputation for excellence and reliability. The company's commitment to quality, innovation, and customer satisfaction has positioned it as a preferred partner for OEMs and manufacturers seeking high-precision machining solutions.
In addition to its technical capabilities, (remove brand name) takes pride in its commitment to sustainability and environmental stewardship. The company has implemented eco-friendly manufacturing practices and is dedicated to minimizing its environmental impact. (remove brand name) has also invested in energy-efficient equipment and processes to reduce its carbon footprint and contribute to a greener future.
Looking ahead, (remove brand name) is poised for continued growth and success in the precision machining industry. The company plans to expand its capabilities and capacity to meet the increasing demand for high-quality precision components. (remove brand name) also aims to further enhance its technological capabilities and explore new opportunities for innovation and efficiency.
In conclusion, (remove brand name) is a leading provider of high-precision machining services, known for its advanced technology, commitment to quality, and client-focused approach. With a strong track record of delivering superior products and exceeding customer expectations, (remove brand name) is well-positioned for a successful future in the manufacturing industry.
Company News & Blog
How Insert Molding is Revolutionizing Manufacturing Processes
Title: Innovative Insert Molding Technology Revolutionizes Manufacturing ProcessesIntroduction:The manufacturing industry continually seeks advanced technologies to increase efficiency, minimize costs, and enhance product performance. One such revolutionary technique is Insert Molding, which combines the benefits of traditional molding techniques with precision insert placement, resulting in enhanced product performance and streamlined manufacturing processes. One company at the forefront of this innovation is {}. With their extensive experience and expertise in insert molding, they are pushing the boundaries of what is possible in the manufacturing industry.Paragraph 1:Insert Molding is a manufacturing process that involves injecting molten materials, such as plastic or metal, into a pre-formed cavity or mold containing one or more carefully positioned inserts. These inserts can be a wide range of components, including threaded inserts, electrical connectors, sensors, or metal reinforcements. The molten material effectively encapsulates the inserts, creating a strong bond between the two, resulting in a more robust and functional end product.Paragraph 2:Insert Molding offers several advantages over traditional manufacturing methods. Firstly, it eliminates the need for additional assembly processes, reducing labor costs and assembly time. By incorporating various inserts directly into the mold, the manufacturing process becomes more streamlined, efficient, and cost-effective. Furthermore, insert molding ensures precise and accurate positioning of the inserts, leading to higher product integrity and reliability.Paragraph 3:The innovation and expertise of {} in the field of insert molding have allowed them to cater to a diverse range of industries, including automotive, electronics, medical, and consumer goods. Their state-of-the-art facilities and skilled engineers enable them to create complex and high-quality molded products with exceptional precision. {} also offers comprehensive design assistance, ensuring that their customers' unique insert molding requirements are met, resulting in tailored solutions that exceed expectations.Paragraph 4:The automotive industry, in particular, has greatly benefited from the utilization of insert molding. By integrating metal inserts into plastic parts, manufacturers achieve significant weight reduction, increased part functionality, and improved overall vehicle performance. Electrical connectors, sensors, and wiring harnesses are seamlessly integrated, simplifying assembly and enhancing reliability. The implementation of insert molding enables automotive manufacturers to produce parts that meet the stringent safety and quality standards of the industry.Paragraph 5:In the ever-evolving electronics industry, where miniaturization and increased functionality are essential, insert molding plays a crucial role. With the ability to place delicate components, such as microchips, sensors, and connectors, with utmost precision, manufacturers can produce smaller and slimmer electronic devices without sacrificing performance. This technique also enhances the devices' durability by protecting fragile components and reducing the risk of damage caused by external factors.Paragraph 6:In the medical industry, insert molding offers numerous benefits in terms of product design, functionality, and sterilization. The ability to encapsulate electronics, sensors, and metal components within a single molded part ensures a seamless integration of various functionalities, such as drug delivery systems, diagnostic equipment, and surgical devices. The use of insert molding in the medical field has resulted in advancements in patient care and treatment efficiency.Conclusion:With its ability to combine diverse materials and precisely position inserts, Insert Molding has revolutionized the manufacturing industry by enhancing product performance, reducing costs, and streamlining production processes. The expertise and cutting-edge solutions provided by {} have solidified their place as industry leaders in insert molding technology. As new advancements continue to be made, the possibilities and applications of Insert Molding are boundless, driving innovation throughout various sectors and shaping the future of manufacturing.
Enhance Precision and Efficiency: Explore the Advantages of CNC Mill Conversions
Title: Manufacturing Company Announces Innovative CNC Mill Conversion for Enhanced Precision and EfficiencyIntroduction:In the fast-paced world of manufacturing, XYZ Manufacturing Company has made waves once again with their latest breakthrough: the revolutionary CNC Mill Conversion. This cutting-edge technology promises to revolutionize machining processes, improving precision, efficiency, and overall productivity. By removing restrictions and introducing advanced features, XYZ Manufacturing Company is setting a new standard in the industry.Body:1. Introduction to XYZ Manufacturing Company: XYZ Manufacturing Company, a leading player in the manufacturing industry, is known for its commitment to innovation and product excellence. With decades of experience in delivering high-quality machinery, they continue to push boundaries and pioneer game-changing technologies. Their unwavering dedication to their clients' needs has earned them a reputation as a reliable and trusted provider of manufacturing solutions.2. The Need for CNC Mill Conversion: Recognizing the need for further advancements to meet increasing market demands, XYZ Manufacturing Company embarked on a mission to develop a CNC Mill Conversion that would take machining processes to new heights. With conventional mills becoming outdated, the company determined that upgrading these machines to CNC (Computer Numerical Control) would enhance precision, efficiency, and enable more complex operations.3. The Revolutionary CNC Mill Conversion: XYZ Manufacturing Company's CNC Mill Conversion is characterized by its cutting-edge features and unmatched precision. By integrating advanced automation and digital control systems, the upgraded mill allows for precise and repeatable machining operations, resulting in higher accuracy and reduced human error.4. Enhanced Cutting Power and Efficiency: The CNC Mill Conversion is equipped with powerful servo motors and state-of-the-art spindle drives, revolutionizing the cutting power and performance of the machine. This ensures an optimized milling process, significantly reducing cycle times and increasing production output, ultimately enhancing operational efficiency and profitability for clients.5. Improved Programming and Digital Interface: With the introduction of CNC technology, programming processes are streamlined and simplified. XYZ Manufacturing Company's CNC Mill Conversion boasts user-friendly software interfaces that allow operators to create and manage machining programs effortlessly. This ensures seamless integration with existing manufacturing workflows, reducing downtime and maximizing productivity.6. Advanced Precision and Quality Control: The CNC Mill Conversion's cutting-edge features include high-resolution encoders and sensors that constantly monitor and correct machining operations in real-time, ensuring optimal precision throughout the entire process. This advanced quality control mechanism eliminates errors, minimizing scrap and rework, while consistently producing products of superior quality.7. Increased Flexibility and Versatility: One of the key advantages of the CNC Mill Conversion is its ability to handle a wide range of materials and machining operations. Whatever the project demands, whether it be milling, drilling, or tapping, the upgraded machine provides the flexibility required to meet diverse manufacturing requirements. This versatility saves time and resources, making it an ideal choice for industries such as aerospace, automotive, and electronics.8. Competitive Edge and Future Growth: By adopting XYZ Manufacturing Company's CNC Mill Conversion, manufacturers gain a significant competitive edge, staying ahead of the curve in an increasingly demanding market. With improved precision, efficiency, and flexibility, businesses can not only meet current demands but also position themselves for future growth, expanding their capabilities to seize new opportunities.Conclusion:XYZ Manufacturing Company's CNC Mill Conversion marks a significant milestone in the manufacturing industry. By introducing cutting-edge features, advanced automation, and unmatched precision, XYZ Manufacturing Company is at the forefront of revolutionizing machining processes. This innovative solution enables businesses to enhance their productivity, improve quality control, and gain a competitive edge. With XYZ Manufacturing Company's commitment to innovation, the possibilities for the future of CNC milling are truly exciting.
Boost Your Manufacturing Process with Efficient 3-Axis CNC Machining
Title: Revolutionary 3-Axis CNC Machining Ushering in a New Era of Precision ManufacturingIntroduction:In the fast-paced world of manufacturing, companies are constantly seeking more efficient and accurate methods to produce high-quality products in a cost-effective manner. This quest for excellence has driven the development of advanced technologies such as the revolutionary 3-axis CNC machining system. With its exceptional precision and versatility, this cutting-edge methodology has garnered worldwide acclaim, transforming the manufacturing landscape across industries.Body:1. What is 3-Axis CNC Machining?At its core, 3-axis CNC machining is a computer-controlled process used to shape materials such as metal, plastic, or wood, providing unparalleled precision and repeatability. This technology enables the creation of complex and intricate designs with remarkable speed and accuracy, far surpassing the capabilities of traditional manual machining.2. The Advantages of 3-Axis CNC Machining:a. Precision: The precise movement of the 3-axis CNC machine ensures accurate and consistent outcomes, reducing human errors to an absolute minimum. This level of precision allows manufacturers to create highly intricate and complex designs that were once unachievable.b. Versatility: Unlike other machining methods, 3-axis CNC machining offers unparalleled versatility. It can be used to shape a wide range of materials, from plastics to metals, with ease. This adaptability enables manufacturers to cater to diverse industries, from automotive and aerospace to electronics and medical.c. Efficiency: The automation capabilities of 3-axis CNC machining dramatically enhance efficiency. This system can run continuously, maximizing productivity while minimizing downtime traditionally associated with manual operations. Additionally, the ability to program the machine precisely allows for the replication of parts with consistent quality, further speeding up the manufacturing process.d. Cost-effectiveness: Although initial investment costs may be higher, 3-axis CNC machining saves money in the long run. The reduced labor requirements and increased efficiency lead to lower operating costs, improved productivity, and minimized waste. Furthermore, this method allows for the production of intricate designs without costly manual labor, making it an economical choice for manufacturers.3. Applications of 3-Axis CNC Machining:The versatility of 3-axis CNC machining has enabled its application in numerous industries. Below are some areas where this technology is extensively used:a. Automotive: In the automotive industry, 3-axis CNC machining is employed to produce high-precision components, such as engine parts, transmission components, and intricate car body shapes.b. Aerospace: The aerospace industry relies on 3-axis CNC machining to create vital parts such as turbine blades, control surfaces, and structural components. The consistent precision and reliability of this technology are critical for ensuring flight safety.c. Electronics: The production of complex electronic devices demands precise machining, making 3-axis CNC machining a preferred option. It is used to manufacture circuit boards, connectors, and intricate casings, guaranteeing a high level of precision and minimizing electrical malfunctions.d. Medical: In the medical field, 3-axis CNC machining is essential for the manufacturing of intricate surgical instruments, implants, orthopedic devices, and prosthetics. This technology allows for precision that is crucial in these life-saving applications.Conclusion:The advent of 3-axis CNC machining has revolutionized precision manufacturing across industries. Its unparalleled precision, versatility, efficiency, and cost-effectiveness have made it an integral part of modern manufacturing processes, elevating the standard of quality and contributing to technological advances. As technology continues to evolve, 3-axis CNC machining is expected to further enhance manufacturing capabilities, driving innovation and propelling various industries toward a future of unprecedented precision and efficiency.
DIY Plastic Injection Molding: How to Set Up Your Own Molding Station at Home
Home plastic injection molding has become a popular and cost-effective way for hobbyists and small businesses to produce their own plastic products. With the use of a desktop injection molding machine, individuals can create custom plastic parts in the comfort of their own home, without the need for expensive industrial machinery.One company that has made a name for itself in the home plastic injection molding industry is {}. They have designed and manufactured a compact and user-friendly injection molding machine that is perfect for beginners and experienced molders alike. This machine allows users to produce high-quality plastic parts using a variety of thermoplastic materials, including ABS, PE, and PVC.With the increasing demand for custom plastic parts, home injection molding is quickly gaining traction as a viable alternative to traditional manufacturing methods. The ability to create small to medium-sized batches of plastic parts at home provides individuals with a level of flexibility and control that is not possible with larger-scale production methods. This has led to a surge in interest from small businesses, makers, and industry professionals who are looking for a cost-effective and efficient way to produce plastic parts.One of the key advantages of home plastic injection molding is the ability to iterate on designs quickly and cost-effectively. With a desktop injection molding machine, individuals can test and refine their designs in a matter of hours, rather than waiting weeks for samples to be produced by a third-party manufacturer. This allows for greater innovation and creativity in the product development process, as well as the ability to respond quickly to changes in market demand.In addition to the machine, {Company} also offers a range of support and training materials for home molders. Their website features a wealth of resources, including tutorials, troubleshooting guides, and design tips, to help individuals get the most out of their injection molding machine. They also provide ongoing technical support to ensure that users are able to overcome any challenges they may encounter during the molding process.As the home plastic injection molding industry continues to grow, {Company} is at the forefront of innovation and development in this space. Their commitment to providing high-quality, user-friendly machines and comprehensive support services has made them a trusted name in the industry. With a focus on accessibility and affordability, they are helping to democratize the plastic manufacturing process, making it accessible to a wide range of individuals and businesses.The future of home plastic injection molding looks bright, with more and more individuals and businesses recognizing the value of this innovative manufacturing method. As technology continues to advance, and the barriers to entry continue to lower, we can expect to see even greater adoption of home injection molding in the years to come. With companies like {Company} leading the way, the possibilities for custom plastic part production are endless.
Top 5 Applications of Injection Molding in Manufacturing
Injection Molding Application Brings Revolutionary Changes to Manufacturing ProcessesIn today's fast-paced world, manufacturers are constantly seeking new and innovative ways to improve their production processes. One such method that has been gaining widespread attention is injection molding. This advanced manufacturing technique has the potential to bring about revolutionary changes in the way products are designed and produced.Injection molding is a manufacturing process for producing parts by injecting molten material into a mold. It is commonly used for manufacturing a variety of products, including plastic parts, components for medical devices, automotive parts, and consumer goods. This process has gained popularity due to its ability to produce complex and intricate parts with high precision and consistency.One company that has been at the forefront of utilizing injection molding technology is {} (). The company, established in 1990, has carved a niche for itself in the manufacturing industry by providing high-quality injection-molded parts for a wide range of applications. With a state-of-the-art facility equipped with the latest injection molding machines and a team of experienced engineers, {} is able to deliver custom solutions to meet the unique needs of its clients.{} is committed to staying ahead of the curve in the ever-evolving manufacturing landscape. With a focus on innovation and customer satisfaction, the company has continually invested in advanced technologies to enhance its production capabilities. This forward-thinking approach has not only enabled {} to maintain its competitive edge but has also positioned the company as a leader in the injection molding industry.One of the key advantages of injection molding is its ability to produce parts with exceptional precision and accuracy. The process allows for the creation of intricate designs and complex geometries that would be challenging to achieve using traditional manufacturing methods. With the use of computer-aided design (CAD) software and advanced mold-making techniques, {} is able to manufacture high-quality parts with tight tolerances, ensuring superior performance and functionality.Another advantage of injection molding is its cost-effectiveness. The ability to produce large volumes of parts with minimal waste makes this manufacturing process highly efficient. {} has leveraged this advantage to offer competitive pricing to its customers, making it an attractive choice for businesses looking to streamline their production processes and reduce overall costs.Furthermore, injection molding is a versatile process that can accommodate a wide range of materials, including thermoplastics, thermosets, and elastomers. This flexibility allows {} to cater to diverse industry needs, from automotive and aerospace to medical and consumer products. By working closely with its customers, the company is able to recommend the most suitable materials for their specific applications, ensuring optimal performance and durability.In addition to its technical capabilities, {} is dedicated to sustainability and environmental responsibility. The company strives to minimize its environmental impact by implementing eco-friendly practices in its manufacturing processes. By using recyclable materials and optimizing energy consumption, {} is committed to promoting a greener and more sustainable future for the manufacturing industry.With its dedication to quality, innovation, and customer satisfaction, {} is poised to continue making significant contributions to the advancement of injection molding technology. As the manufacturing landscape continues to evolve, this company remains committed to staying ahead of the curve and delivering cutting-edge solutions to its clients.In conclusion, injection molding is a game-changer in the manufacturing industry, and {} is leading the charge in harnessing its potential. With its state-of-the-art facilities, technical expertise, and commitment to excellence, {} is well-positioned to continue driving revolutionary changes in the production of high-quality, precision-engineered parts. As the demand for complex and customized products continues to grow, injection molding is likely to play an even more prominent role in shaping the future of manufacturing.
Revolutionary Casting Gating System Shows Promising Results
Title: Groundbreaking Casting Gating System Revolutionizes the Manufacturing IndustryIntroduction:In a landmark development, a cutting-edge Casting Gating System, developed by a renowned manufacturing solutions company, is set to redefine the manufacturing industry. This innovative system, which combines advanced technology with superior materials, is poised to streamline the casting process, significantly improving efficiency and product quality.Background:The use of casting techniques has long been integral to the manufacturing industry. While traditional casting methods have proven effective, they often suffer from limitations that can hamper productivity and output quality. Recognizing this need for enhancement, Company X has introduced an exceptional solution - the Casting Gating System.Enhanced Efficiency through Advanced Technology:The Casting Gating System incorporates state-of-the-art technology to accomplish unprecedented levels of efficiency. Its cutting-edge features optimize the casting process, ensuring precise and controlled material flow. This innovative system minimizes casting defects, such as porosity or unevenness, that can hinder the overall quality of the finished products.The system consists of high-quality gating components that regulate the flow of molten metal or other materials into the mold during the casting process. By allocating material distribution more evenly and precisely, the Casting Gating System maximizes yield, reduces waste, and expedites the manufacturing cycle.Unmatched Product Quality:With its precise control over the flow of materials, the innovative Casting Gating System guarantees exceptional product quality. By eliminating irregularities, it minimizes the risk of casting defects, creating superior products that meet or exceed industry standards. As a result, manufacturers utilizing this system can elevate their reputation for delivering reliable and high-quality products to their customers.Furthermore, the system's unique design and precision allow for easy customization according to specific casting requirements. Manufacturers can optimize gating configurations to suit various materials, molds, and casting processes, further enhancing the quality of the end products.Sustainability and Cost Optimization:In addition to its performance benefits, the Casting Gating System also offers long-term sustainability advantages. By minimizing material waste, manufacturers can reduce both their environmental footprint and production costs. This innovative system optimizes resource utilization, resulting in enhanced profitability and a greener manufacturing process.The adjustable nature of the system enables manufacturers to optimize material flow, reducing the need for additional raw materials. This adaptability contributes to cost-efficiency, making the Casting Gating System an economically viable choice for manufacturers across various industries.Endorsements and Case Studies:Industry leaders who have adopted the Casting Gating System have witnessed transformative results. Numerous case studies demonstrate remarkable improvements in casting efficiency, quality, and profitability. Notable success stories within the automotive, aerospace, and machinery sectors speak volumes about the system's ability to revolutionize casting processes.Experts from within the manufacturing domain are overwhelmingly positive about the potential of this innovative gating system. Recognized professionals have praised how the system augments overall efficiency, enhances product quality, and supports sustainable production practices.Conclusion:The introduction of the groundbreaking Casting Gating System has ushered in a new era for the manufacturing industry. Combining sophisticated technology with superior design, this innovative system significantly enhances casting processes, ensuring optimal efficiency, exceptional product quality, and sustainable manufacturing practices. Manufacturers across various sectors can now reimagine their production capabilities, elevate their output, and cement their position as leaders in the global marketplace.By embracing the Casting Gating System, companies can stay ahead of the competition, satisfy customer demands, and ultimately contribute to the progress of the manufacturing industry as a whole.
The Ultimate Guide to Efficient Cnc Fixture Design for Manufacturing Success
Title: Innovative CNC Fixture Design Revolutionizes Manufacturing ProcessesIntroduction:In a breakthrough development within the manufacturing industry, an innovative CNC fixture design is set to transform production processes, providing greater efficiency, accuracy, and versatility. This cutting-edge technology marks a significant milestone in manufacturing, empowering companies to improve their productivity and competitiveness in the global market.The Company's Vision:Born out of a deep passion for revolutionizing the manufacturing domain, the company behind this groundbreaking CNC fixture design aims to redefine industry norms. Their team of experienced engineers and technicians have dedicated years of research and development to create this state-of-the-art technology, which promises to streamline operations and enhance overall production quality.The CNC Fixture Design:This remarkable CNC fixture design incorporates a myriad of advanced features that address the challenges of traditional fixture designs. It leverages the latest technologies, including adaptive control systems and intelligent sensor integration, to optimize machining processes and improve the overall user experience.One of the key highlights of this fixture design is its modular approach, allowing for versatile application across various production requirements. The ability to quickly adjust and reconfigure the fixture greatly enhances manufacturing flexibility, saving precious time and resources. Furthermore, the design includes built-in error detection mechanisms, minimizing defects and ensuring consistent, high-quality output.Another noteworthy aspect of this CNC fixture design is its emphasis on ergonomics and operator safety. The system integrates user-friendly interfaces, intuitive controls, and enhanced safety features, reducing the risk of accidents and promoting a seamless work environment.Industry Impact:The introduction of this advanced CNC fixture design is poised to revolutionize manufacturing practices across a wide range of industries. From automotive and aerospace to electronics and medical devices, the versatility and adaptability of this technology make it applicable to numerous sectors.The increased efficiency and accuracy offered by this fixture design will open up new possibilities for manufacturers. It allows for more complex and intricate designs, shorter production cycles, and greater cost-effectiveness. Companies can expect to witness significant improvements in product quality, reduced downtime, and enhanced overall profitability.Furthermore, this CNC fixture design aligns with the ongoing industry trend towards automation and digitization. Its integrated smart systems enable seamless data collection, analysis, and real-time adjustments, contributing to improved productivity and competitiveness on a global scale.Future Prospects:The company behind this CNC fixture design remains committed to continuous innovation and technological advancements. They are actively exploring partnerships with manufacturers seeking to enhance their production capabilities. The aim is to collaborate closely with industry leaders to customize and optimize the design according to specific needs, ensuring a seamless integration of this technology into existing processes.Moreover, through ongoing research and development efforts, the company plans to expand the capabilities of the CNC fixture design further. This includes exploring advancements in materials, sensors, and automation, as well as integrating artificial intelligence and machine learning technologies.Conclusion:As the manufacturing industry embraces the era of automation and digitization, this revolutionary CNC fixture design promises to redefine traditional production methods. With its emphasis on efficiency, accuracy, versatility, and safety, this technology will undoubtedly revolutionize manufacturing processes in diverse sectors. As this innovative solution gains momentum, manufacturers can look forward to a new era of optimized productivity, improved product quality, and sustained growth in a highly competitive global market.
High-Quality Aerospace CNC Machining Services for Precision Parts
Aerospace CNC Machining Company (ACM) has recently announced its expansion plans with the introduction of new state-of-the-art machining processes and capabilities. The company, known for its high-quality precision components for the aerospace industry, has been a leading supplier for several major aerospace firms.With a growing demand for more complex and advanced aerospace components, ACM has recognized the need to invest in cutting-edge CNC machining technology to meet the evolving needs of the industry. The company has therefore made significant investments in new machinery and equipment, along with the implementation of advanced machining processes to enhance its capabilities.The expansion of ACM's CNC machining capabilities is a strategic move to position the company as a leading provider of precision aerospace components. The new machinery and processes will allow ACM to produce components with tighter tolerances and more intricate geometries, meeting the high standards and requirements of the aerospace industry.One of the key advantages of the new CNC machining capabilities is the ability to produce complex and high-precision components with faster turnaround times. This will enable ACM to better meet the increasing demands of its customers and to stay ahead of the competition in the aerospace industry.In addition to the new machinery and advanced machining processes, ACM has also invested in training and development programs for its team of engineers and technicians. This will ensure that the company's workforce is equipped with the necessary skills and expertise to operate the new CNC machinery and to consistently deliver high-quality components to its customers.The expansion of ACM's CNC machining capabilities is a testament to the company's commitment to staying at the forefront of technological advancements in the aerospace industry. By embracing the latest machining technology and processes, ACM is well-positioned to continue providing its customers with innovative and high-quality aerospace components.The president of ACM, John Smith, expressed his excitement about the company's expansion plans and the potential for growth in the aerospace industry. "We are continuously looking for ways to improve our capabilities and better serve our customers," said Smith. "The investment in new CNC machining technology is a testament to our dedication to providing the highest quality components to the aerospace industry."The expansion of ACM's CNC machining capabilities has already garnered positive attention from its existing customer base, as well as from potential new clients in the aerospace sector. With the new machinery and advanced processes in place, the company is well-positioned to take on larger and more complex projects, further solidifying its reputation as a leading provider of precision aerospace components.In conclusion, the expansion of ACM's CNC machining capabilities marks an exciting milestone for the company and the aerospace industry as a whole. With the new machinery and advanced processes in place, ACM is poised to meet the increasing demands and evolving needs of the aerospace industry, while continuing to deliver high-quality precision components to its customers.
Exploring the Limitations of Sand Casting: Factors Hindering the Process
Title: Exploring Sand Casting Disadvantages in the Manufacturing IndustryIntroduction:In the realm of manufacturing, sand casting has long been a traditional and widely-used technique for creating intricate and durable metal components. Many companies, including {}, have successfully employed sand casting in their production processes. However, it is important to be aware of the disadvantages associated with this method in order to make informed decisions in the manufacturing industry.Sand Casting and its Application:Before delving into the drawbacks, it is crucial to understand the fundamentals of sand casting. The process involves pouring molten metal into a sand mold to create a desired shape. This method offers flexibility, affordability, and the ability to produce intricate components with various alloys. Sand casting is widely used in industries like automotive, aerospace, and construction, where complex parts are required.Disadvantage 1: Limited Surface Finish and Precision:One of the major shortcomings of sand casting is the limitation it presents in achieving high surface finish and precision. The texture of the sand mold often transfers inconsistencies onto the final product, resulting in a rougher surface finish. Moreover, the molding process may introduce slight variations in dimensions, making it challenging to achieve precise measurements and tight tolerances. These factors can be critical in industries where the aesthetics and precision of components are paramount, such as consumer electronics and medical devices.Disadvantage 2: Time and Labor Intensive:Sand casting is a time and labor-intensive process, which can significantly impact the overall production timeline and costs. Preparing the molds, including pattern creation, gating system design, and mold assembly, requires skilled labor and careful execution. Additionally, molten metal must be cooled and solidified in the mold, followed by the removal of excess sand and finishing operations. Addressing these steps can be time-consuming, leading to longer lead times and reduced efficiency, especially for industries characterized by high-volume production demands.Disadvantage 3: Limited Complexity and Assembly Integration:While sand casting is suitable for various complex shapes, it has limitations in terms of intricate designs and integration with assembly components. The mold's internal cavities can be challenging to achieve with precision, prohibiting the creation of intricate features. Furthermore, sand casting may not be ideal for components requiring internal passageways, such as cooling channels, as the removal of the sand mold can be difficult and may compromise the final product's integrity. For industries that heavily rely on intricate designs and integration, such as semiconductor manufacturing or advanced machinery, alternative production methods like precision machining may be preferred.Disadvantage 4: Material Waste and Environmental Concerns:Sand casting generates a significant amount of waste material. After each casting, sand molds become unusable and are discarded, contributing to environmental concerns. Additionally, the process can consume large quantities of sand, leading to mining activities and the depletion of natural resources. Companies like {} have been actively working towards sustainable solutions by implementing recycling processes and exploring environmentally-friendly alternatives to sand molds, such as 3D-printed molds or investment casting.Conclusion:Sand casting undeniably plays a crucial role in the manufacturing industry, with its affordability and flexibility making it an attractive choice for many companies, including {}. However, it is essential to be aware of its disadvantages, which include limited surface finish and precision, time and labor intensiveness, limited complexity and integration, and environmental concerns. By understanding these drawbacks, manufacturers can make more informed decisions when choosing their production methods, potentially optimizing their processes and meeting the demands of their respective industries while considering sustainability needs.
Discover the Latest Breakthroughs in Plastic Parts Manufacturing
[News Title]: Advancements in Plastic Parts Technology Revolutionize Manufacturing Processes[News Introduction]:In a remarkable breakthrough, a leading company in the field of plastic parts manufacturing has introduced cutting-edge technology that is set to revolutionize the industry. The company, which wishes to keep their brand anonymous, has successfully developed a range of plastic parts that boast unparalleled strength, durability, and flexibility. These advancements are expected to bring significant improvements to various sectors including automotive, aerospace, electronics, and consumer goods. With growing demand for innovation and sustainability, the introduction of these plastic parts promises to reshape the manufacturing landscape and pave the way for a more efficient and environmentally friendly future.[Body - Part 1: Importance of Plastic Parts in Manufacturing]:Plastic parts play a crucial role in industries worldwide due to their versatility, cost-effectiveness, and ease of production. They are extensively used in manufacturing processes for a broad range of products, including automotive components, electronic devices, packaging materials, and household appliances. The evolving requirements of these sectors demand continuous advancements in plastic parts technology to ensure superior performance, enhanced functionality, and improved production efficiency. In response to this demand, the anonymous company has invested heavily in research and development to develop groundbreaking solutions that address the contemporary challenges faced by manufacturers.[Body - Part 2: Advancements in Plastic Parts]:The undisclosed company's newly developed plastic parts exhibit exceptional strength and durability, surpassing the limitations of conventional materials. Through innovative engineering, the company has achieved a remarkable balance between rigidity and flexibility, allowing the plastic parts to withstand high levels of stress and strain. This breakthrough not only enhances the longevity of products but also ensures safer usage, particularly in critical applications such as automotive safety systems and aerospace components.Furthermore, the undisclosed company's plastic parts showcase superior resistance to impact, chemicals, and environmental factors, thereby reducing the chances of premature degradation. This feature significantly extends the lifespan of products, resulting in reduced maintenance costs and enhanced customer satisfaction. Additionally, the manufacturing processes associated with these plastic parts have been optimized to minimize waste and energy consumption, aligning with the global shift towards sustainable practices.[Body - Part 3: Applications and Benefits]:The innovative plastic parts developed by the anonymous company have profound implications for various industries. In the automotive sector, these advanced components can contribute to the weight reduction of vehicles, improving fuel efficiency and reducing emissions. Additionally, their superior durability can enhance passenger safety by providing robust structural support.In aerospace applications, the lightweight and high-strength characteristics of the plastic parts can reduce the overall weight of aircraft, leading to enhanced fuel economy and increased payload capacity. This advancement ensures that the aviation industry takes substantial strides towards sustainability while maintaining the highest safety standards.The electronics industry can benefit from the unparalleled flexibility and resistance to environmental factors offered by these plastic parts. With the expanding trend of miniaturization, consumer electronic devices require components that can endure constant usage while remaining lightweight. The anonymous company's plastic parts possess the necessary attributes, ensuring greater reliability and longer lifespans for electronic gadgets.The manufacturing sector as a whole will reap the rewards of these advancements. By incorporating the undisclosed company's plastic parts, manufacturers can streamline their production processes, reduce assembly time, and minimize costs. The enhanced durability and resistance of these parts eliminate the need for frequent replacements and repairs, resulting in higher overall productivity and profitability.[Conclusion]:As technology continues to advance at an unprecedented pace, it is essential for manufacturers to embrace cutting-edge solutions that enhance their products and processes. The anonymous company's revolutionary plastic parts have the potential to transform diverse industries by offering unmatched strength, durability, and flexibility. With their exceptional properties, these parts provide opportunities for innovation, sustainability, and increased efficiency. By leveraging these advancements, manufacturers can stay ahead in today's competitive market while building a more prosperous and environmentally conscious future.