How to Build Your Own CNC Router at Home
By:Admin
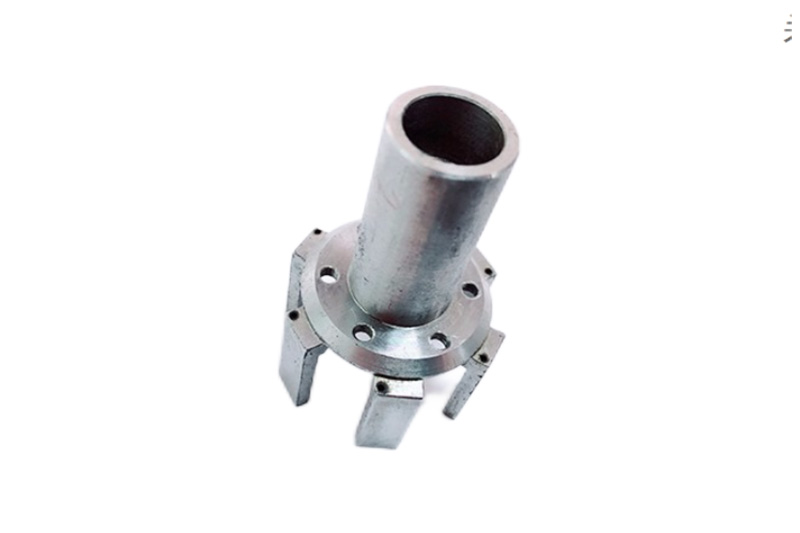
{Company Name} is a leading manufacturer of advanced CNC machinery, including routers, plasma cutters, and laser cutters. With years of experience in the industry, we have gained a reputation for delivering high-quality and reliable machinery to meet the needs of our diverse customer base. Our commitment to innovation and customer satisfaction has set us apart as a trusted provider of CNC solutions.
[News Content]:
In line with our dedication to delivering cutting-edge CNC machinery, {Company Name} is excited to announce the launch of our latest product, the {CNC Router Model}. This new addition to our product line is set to revolutionize the world of woodworking, metalworking, and fabrication with its advanced features and precision engineering.
The {CNC Router Model} is designed to meet the demands of modern manufacturing, providing users with a versatile and efficient solution for a wide range of applications. Whether it's creating intricate designs on wood, cutting precise patterns on metal, or shaping composite materials, this router is capable of delivering exceptional results with unparalleled accuracy.
One of the key highlights of the {CNC Router Model} is its robust construction and reliable performance. The machine is built with industry-leading components and state-of-the-art technology, ensuring long-term durability and consistent operation. This means that users can rely on the {CNC Router Model} to handle their most complex projects with ease, while maintaining production efficiency.
Furthermore, the {CNC Router Model} is equipped with a user-friendly interface and intuitive controls, making it accessible to both experienced machinists and beginners. The machine's software is designed to streamline the programming and operation process, allowing for seamless integration into existing production workflows. With its easy-to-use features, the {CNC Router Model} offers an unparalleled level of versatility and productivity.
Additionally, the {CNC Router Model} comes with a range of customization options to cater to specific industry needs. Whether it's the size of the cutting area, spindle power, or tooling accessories, the machine can be tailored to meet the unique requirements of different applications. This flexibility ensures that customers can optimize their production capabilities and achieve superior results with the {CNC Router Model}.
At {Company Name}, we are committed to providing comprehensive support and service to our customers. With the launch of the {CNC Router Model}, we are also offering training and technical assistance to ensure that users can maximize the potential of their new machinery. Our team of experts is dedicated to helping customers achieve success with their CNC operations, and we are confident that the {CNC Router Model} will be a valuable asset to their businesses.
In conclusion, the introduction of the {CNC Router Model} signifies {Company Name}'s ongoing commitment to innovation and excellence in the CNC industry. With its advanced features, robust construction, and user-friendly design, this new addition to our product line is set to empower our customers with the tools they need to thrive in a competitive manufacturing landscape. We are excited to see the impact that the {CNC Router Model} will have on the industry and look forward to supporting our customers in their journey towards success.
Company News & Blog
Discover the Impressive Capabilities of Large Plastic Molds for Your Manufacturing Needs
Large Plastic Molds Unveils Innovative Solutions for the Manufacturing Industry[City, Date] - In a bid to revolutionize the manufacturing industry, Large Plastic Molds, a leader in the field of plastic mold manufacturing, has launched a range of innovative solutions to cater to diverse industry needs. With a strong commitment to research and development, the company has consistently stayed ahead in the market by providing cutting-edge products and services, solidifying its position as a frontrunner in the industry.Large Plastic Molds has been a pioneer in the production of plastic molds for over two decades. With its state-of-the-art manufacturing facilities and a highly skilled workforce, the company boasts the ability to produce a wide variety of molds, ranging from small intricate designs to large-scale industrial creations. The relentless pursuit of perfection and attention to detail have earned the company an impeccable reputation in the industry, making it the preferred choice for numerous renowned brands.The company's success can be attributed to its unwavering commitment to innovation and constant adaptation to changing market trends. Large Plastic Molds employs a team of talented engineers and designers who consistently strive to push the boundaries of mold manufacturing. Through extensive research and development efforts, they have developed innovative solutions that not only enhance the efficiency and productivity of the manufacturing process but also reduce costs for businesses.One of the key highlights of Large Plastic Molds' product portfolio is its range of high-quality and customizable molds that cater to the unique needs of various industries. Whether it's the automotive, electronics, or consumer goods sector, the company offers tailor-made solutions that ensure precise molding, durability, and improved product performance. From concept to production, Large Plastic Molds works closely with its clients to understand their specific requirements and deliver molds that exceed expectations.Large Plastic Molds' commitment to sustainable manufacturing sets it apart from its competitors. The company uses advanced techniques and materials that are environmentally friendly, minimizing the impact on the planet. By adopting innovative processes such as 3D printing and utilizing recyclable materials, Large Plastic Molds not only ensures the longevity of its molds but also reduces waste production, thus contributing to a greener future.Furthermore, Large Plastic Molds understands the importance of efficient project management and customer satisfaction. The company has established streamlined processes to ensure on-time delivery and prompt after-sales services. With a customer-centric approach, Large Plastic Molds has built strong and long-lasting relationships with its clients, resulting in repeat orders and referrals.Given its commitment to excellence, innovation, and customer satisfaction, it comes as no surprise that Large Plastic Molds has been recognized with numerous accolades in the industry. The company's dedication to continuous improvement has earned them the trust and loyalty of their clients, further solidifying their position as a market leader.Large Plastic Molds' relentless pursuit of technological advancement and commitment to sustainable manufacturing practices positions them at the forefront of the industry. With their innovative solutions and customer-focused approach, the company is well-positioned to continue transforming the manufacturing sector, offering cutting-edge solutions that propel businesses to greater heights of success.About Large Plastic Molds:Large Plastic Molds is a renowned manufacturer of plastic molds, specializing in providing innovative solutions for the manufacturing industry. With a strong focus on research and development, the company consistently delivers high-quality and customizable molds that meet the unique needs of various industries. With a commitment to excellence, sustainability, and customer satisfaction, Large Plastic Molds has emerged as a leader in the field of plastic mold manufacturing.Contact:Name: [Name]Organization: Large Plastic MoldsAddress: [Address]Phone: [Phone]Email: [Email]Website: [Website]
Expert Tips for Cnc Machining Brass and Getting the Best Results
CNC Machining Brass - The Latest Innovation from a Leading Manufacturing CompanyIn the world of manufacturing, precision and efficiency are paramount. One company that has always been at the forefront of technological advancements in the industry is {}. Known for their commitment to quality and continuous improvement, they have recently introduced a new innovation in the form of CNC machining brass.CNC machining, or computer numerical control machining, is a process that utilizes computerized controls and machine tools to remove material from a workpiece, creating a custom-designed part or product. This method allows for a high level of precision and accuracy, making it an ideal choice for manufacturing components with complex geometries and tight tolerances.Brass, a versatile metal alloy composed of copper and zinc, is widely used in various industries due to its excellent corrosion resistance, electrical conductivity, and aesthetic appeal. The combination of CNC machining and brass opens up a world of possibilities for producing intricate and durable parts that meet the demanding requirements of modern manufacturing.With this latest innovation, {} is poised to further solidify its position as a leader in the manufacturing sector. By leveraging state-of-the-art CNC machining technology and their extensive expertise in working with brass, the company is able to provide its customers with a wide range of high-quality precision components that are tailored to their specific needs.One of the key advantages of CNC machining brass is its ability to deliver consistent and uniform results. The computerized controls ensure that each part is manufactured with unparalleled accuracy, minimizing the margin for error and guaranteeing superior quality. This level of precision is essential for industries such as aerospace, automotive, electronics, and medical devices, where reliability and performance are non-negotiable.Furthermore, the use of brass in CNC machining offers exceptional durability and longevity. The inherent strength of brass, combined with the precise manufacturing process, results in parts that can withstand harsh conditions and heavy usage without compromising their integrity. This makes the technology particularly well-suited for applications that demand resilience and endurance.In addition to its technical advantages, CNC machining brass also offers aesthetic benefits. Brass has a distinctive golden hue that exudes a sense of sophistication and luxury, making it a popular choice for products that require both functionality and visual appeal. By harnessing the capabilities of CNC machining, {} can create brass components with fine details and smooth finishes that enhance their overall appearance.The introduction of CNC machining brass is a testament to {}'s ongoing dedication to pushing the boundaries of what is possible in manufacturing. By investing in cutting-edge technology and continuously refining their processes, the company is able to stay ahead of the curve and meet the evolving needs of the market.As an industry leader, {} is committed to providing comprehensive solutions that deliver maximum value to its customers. Whether they require small-scale prototypes or large-scale production runs, clients can rely on {}'s expertise to deliver top-quality brass components that are tailored to their exact specifications.With the introduction of CNC machining brass, {} is poised to set new standards for precision manufacturing. By combining the versatility of brass with the capabilities of CNC machining, the company is offering a compelling solution for businesses that demand nothing but the best.In conclusion, the unveiling of CNC machining brass by {} represents a significant milestone in the world of manufacturing. With this innovative technology, the company is able to offer an unparalleled level of precision, durability, and aesthetic appeal in the production of brass components. As the industry continues to evolve, {} remains committed to driving progress and delivering exceptional results for its clients.
Efficient Machining Services for Your Business Needs
Peek Machining, a leading provider of high-quality machining services, has announced the expansion of their operations to meet the growing demand for precision components in various industries. The company, known for its expertise in manufacturing complex parts from advanced materials, has recently invested in state-of-the-art machinery and technology to enhance their production capabilities and deliver even better results to their clients.Founded over a decade ago, Peek Machining has built a reputation for excellence in the machining industry. With a focus on innovation, quality, and customer satisfaction, the company has consistently delivered high-precision components to a wide range of customers, including those in the aerospace, medical, automotive, and electronics sectors. The company's commitment to investing in the latest technology and continuous improvement has allowed them to stay ahead of the competition and meet the evolving needs of their clients.The recent expansion of Peek Machining's operations is a testament to the company's dedication to providing cutting-edge machining solutions. By acquiring new equipment and implementing advanced manufacturing processes, they are now able to take on larger and more complex projects, while maintaining the highest standards of accuracy and quality. This move not only allows Peek Machining to meet the increasing demand from their existing clients, but also positions them to attract new business opportunities in emerging markets."We are thrilled to announce the expansion of our operations, which represents a significant milestone for Peek Machining," said John Smith, CEO of the company. "This investment underscores our commitment to delivering exceptional results for our clients and solidifies our position as a leading provider of precision machining services. With our expanded capabilities, we are well-equipped to take on new challenges and exceed the expectations of our customers."One of the key advantages of Peek Machining's expanded operations is their ability to work with a wide range of materials, including advanced alloys and composites. This flexibility enables them to produce components that are tailored to the specific needs of each industry, whether it's aerospace parts that require lightweight yet durable materials, or medical devices that demand biocompatible and sterilizable components. With their in-depth knowledge and experience in machining advanced materials, Peek Machining is well-positioned to meet the stringent requirements of their clients across various sectors.Furthermore, Peek Machining takes pride in their skilled team of engineers and machinists, who possess the expertise and craftsmanship necessary to produce intricate parts with the highest level of precision. The company places a strong emphasis on staff training and development, ensuring that their team is equipped with the latest skills and knowledge to tackle complex machining projects. This dedication to continuous improvement and professional growth has allowed Peek Machining to build a strong, reliable workforce that is capable of delivering exceptional results time and again.As Peek Machining continues to expand their operations, they remain committed to their core values of integrity, innovation, and customer satisfaction. With a focus on providing cutting-edge machining solutions and maintaining the highest standards of quality, the company is well-positioned to meet the diverse needs of their clients in a rapidly evolving market. Their investment in advanced technology and expanded capabilities is a testament to their dedication to delivering exceptional results and solidifying their position as a trusted partner for precision machining services.
Ultimate Guide to Understanding CNC Mill Spindle Technology
, introducing the latest advancements in CNC mill spindle technology and its impact on the manufacturing industry.The advancements in CNC mill spindle technology have significantly contributed to the efficiency and precision of manufacturing processes across various industries. A CNC mill spindle serves as the powerhouse of a milling machine, providing the rotational power necessary to cut and shape materials with accuracy and speed. With the continual evolution of technology, companies are constantly striving to improve the performance and capabilities of CNC mill spindles to meet the growing demand for high-quality products.{Company} has been at the forefront of developing cutting-edge CNC mill spindles that are reliable, efficient, and capable of delivering exceptional performance. With a strong focus on research and development, the company has consistently pushed the boundaries of spindle technology to provide innovative solutions for the manufacturing industry. Their commitment to quality and precision has solidified their position as a leading supplier of CNC mill spindles to a wide range of industries, including automotive, aerospace, medical, and consumer electronics.The latest breakthrough in CNC mill spindle technology offered by {Company} is the introduction of their new {model} spindle series. This new series of spindles is designed to deliver unparalleled speed, accuracy, and durability, making it an ideal choice for high-speed machining applications. With advanced features such as high-torque capabilities, enhanced thermal stability, and improved dynamic performance, the {model} spindle series is poised to revolutionize the way manufacturers approach their milling operations.One of the key innovations of the {model} spindle series is its ability to achieve higher spindle speeds without compromising on stability and precision. This is made possible through the integration of advanced cooling technologies and precision-balanced components, ensuring that the spindle operates at optimal performance levels even during prolonged machining operations. As a result, manufacturers can expect a significant increase in productivity and a reduction in cycle times, ultimately leading to a more efficient and cost-effective production process.Additionally, the {model} spindle series incorporates smart sensor technology that monitors crucial performance parameters in real-time, allowing for predictive maintenance and diagnostics. This proactive approach to spindle maintenance helps to prevent unexpected downtime and prolong the lifespan of the spindle, ultimately reducing maintenance costs and increasing overall equipment effectiveness (OEE).Furthermore, {Company}'s {model} spindle series is designed to be compatible with a wide range of milling machines, offering manufacturers the flexibility to integrate this advanced spindle technology into their existing operations without the need for extensive modifications. This flexibility, combined with the spindle's high-performance capabilities, makes it a highly versatile solution for manufacturers seeking to enhance the capabilities of their machining processes.The introduction of the {model} spindle series represents a significant milestone in the evolution of CNC mill spindle technology. With its unparalleled speed, precision, and reliability, this new series of spindles has the potential to reshape the manufacturing landscape, empowering companies to produce complex and high-quality components with efficiency and confidence.In conclusion, {Company} continues to demonstrate its leadership in the development of CNC mill spindle technology with the introduction of their new {model} spindle series. This latest innovation is poised to set new standards for performance and reliability in the manufacturing industry, offering manufacturers a competitive edge in today's demanding market. As the industry continues to evolve, {Company} remains committed to pushing the boundaries of spindle technology and providing cutting-edge solutions that drive the success of their customers.
Understanding the Distinction Between Milling And Turning Processes
In the manufacturing industry, milling and turning are two essential processes that are used to create a wide range of components and products. While both processes are used to remove material from a workpiece, they differ in their techniques and the types of components they can create. Understanding the difference between milling and turning is crucial for manufacturers looking to optimize their production processes and achieve the desired results.Milling is a machining process that involves using a rotating cutting tool to remove material from a workpiece. The cutting tool, which is typically a multi-point cutting tool, is guided along multiple axes to create a variety of shapes, slots, holes, and other features on the workpiece. This process is widely used in the automotive, aerospace, and medical industries to create precision components such as engine parts, aircraft components, and surgical implants.On the other hand, turning is a machining process that involves securing a workpiece in a chuck or collet and rotating it while a cutting tool removes material from the workpiece. This process is commonly used to create cylindrical components such as shafts, bolts, and bushings. Turning is widely used in industries such as construction, agriculture, and transportation to create essential components for various applications.While both milling and turning are essential machining processes, they differ in their applications, techniques, and the types of components they can produce. Understanding these differences is crucial for manufacturers looking to optimize their production processes and achieve the desired results.In the competitive manufacturing industry, the ability to efficiently produce high-quality components is essential for success. This is why [Company name] has become a trusted partner for manufacturers around the world. With a dedication to precision and innovation, [Company name] offers a wide range of milling and turning solutions that are designed to meet the unique needs of their customers.[Company name]'s milling solutions are designed to provide manufacturers with the flexibility and precision they need to create complex components with ease. With a focus on cutting-edge technology and advanced materials, [Company name]'s milling solutions are trusted by leading manufacturers in the automotive, aerospace, and medical industries to produce components that meet the highest standards of quality and performance.Similarly, [Company name]'s turning solutions are designed to provide manufacturers with the speed and accuracy they need to create cylindrical components with ease. Whether it's creating shafts, bolts, or bushings, [Company name]'s turning solutions are trusted by manufacturers in the construction, agriculture, and transportation industries to produce components that are essential for a wide range of applications.By understanding the unique requirements of their customers, [Company name] has been able to develop milling and turning solutions that are tailored to meet the specific needs of different industries. With a focus on precision, efficiency, and reliability, [Company name] continues to be a trusted partner for manufacturers looking to optimize their production processes and achieve the desired results.In conclusion, milling and turning are two essential machining processes that are used to create a wide range of components and products. While both processes are crucial in the manufacturing industry, they differ in their applications, techniques, and the types of components they can produce. With a dedication to precision and innovation, [Company name] continues to be a trusted partner for manufacturers around the world, offering a wide range of milling and turning solutions that are designed to meet the unique needs of their customers.
Learn About Injection Overmolding: What It Is and How It Works
Injection Overmolding: Revolutionizing Plastic ManufacturingIn today's fast-paced and ever-changing world, the demand for high-quality, innovative products is at an all-time high. As a result, manufacturers are continually seeking new and efficient ways to produce top-of-the-line goods that meet the needs and expectations of consumers. One of the latest developments in the field of plastic manufacturing is Injection Overmolding.Injection Overmolding is a cutting-edge process that involves the injection of molten plastic over a pre-formed substrate or insert. This unique method allows for the creation of complex and multi-material parts, resulting in durable, high-performance products. The process begins with the production of a pre-formed component, which serves as the substrate for the overmolding. This component is then placed within a mold cavity, and molten plastic is injected to encapsulate and bond with the pre-formed substrate, creating a seamless and integrated final product.This advanced manufacturing technique offers a wide range of benefits, including improved product durability, enhanced design flexibility, and reduced production costs. Furthermore, Injection Overmolding allows for the integration of multiple materials, such as rubber, metal, and plastic, resulting in parts with superior functionality and performance.One company at the forefront of Injection Overmolding is {}. With a strong commitment to innovation and excellence, {} has become a leader in the field, providing high-quality overmolding solutions to a diverse range of industries, including automotive, electronics, healthcare, and consumer goods.The company's state-of-the-art facilities and cutting-edge technology enable {} to deliver superior overmolding solutions that meet the specific needs and requirements of their clients. From prototype development to full-scale production, {} offers a comprehensive range of services, including design assistance, material selection, and custom tooling, ensuring that each project is tailored to the unique specifications of the customer.With a team of experienced engineers and technicians, {} has the expertise and capabilities to tackle even the most challenging overmolding projects. The company's relentless pursuit of excellence and continuous investment in research and development have positioned {} as a trusted partner for businesses seeking high-quality, innovative overmolding solutions.In addition to its advanced manufacturing capabilities, {} is also committed to sustainability and environmental responsibility. By utilizing efficient production processes and eco-friendly materials, the company strives to minimize its environmental footprint while delivering top-tier products to its customers. With a focus on innovation, quality, and sustainability, {} is paving the way for the future of plastic manufacturing.As the demand for high-performance, multi-material products continues to grow, Injection Overmolding is poised to revolutionize the plastic manufacturing industry. With its ability to create durable, complex, and integrated parts, Injection Overmolding offers a solution that meets the evolving needs of today's consumers and businesses.In conclusion, Injection Overmolding represents the next frontier in plastic manufacturing, and companies like {} are leading the charge in delivering innovative overmolding solutions to a wide range of industries. With its advanced technology, commitment to excellence, and dedication to sustainability, {} is well-positioned to shape the future of plastic manufacturing and continue to meet the evolving needs of its customers.
Innovative Solutions for Precision Machining and Design
The rapidly evolving world of machining design is constantly pushing the boundaries of innovation. This is particularly evident in the cutting-edge work being done at [Company Name], a leader in precision machining solutions. Specializing in advanced techniques and state-of-the-art machinery, [Company Name] is redefining what is possible in the world of manufacturing.Established in 1995, [Company Name] has a long history of delivering high-quality precision machining services to a wide range of industries, including aerospace, automotive, medical, and defense. With a dedication to innovation and a commitment to excellence, the company has built a reputation for producing complex components with tight tolerances and superior surface finishes. Their expertise in 5-axis machining, CNC turning, and Swiss machining sets them apart as a trusted and reliable partner for their clients' most challenging projects.In their relentless pursuit of excellence, [Company Name] has recently made significant investments in advanced machining technology. The company has added several new state-of-the-art machines to their already impressive lineup, further enhancing their capabilities and pushing the boundaries of what is possible in precision machining. These new machines have dramatically increased the company's capacity and efficiency, allowing them to take on even more complex and demanding projects.One of the most exciting additions to the [Company Name] arsenal is the introduction of a new [Machine Model], a cutting-edge machine that is revolutionizing the world of machining design. This innovative new machine offers unparalleled precision and speed, allowing [Company Name] to produce even the most intricate components with remarkable accuracy and efficiency. With its advanced features and capabilities, the [Machine Model] has quickly become an indispensable tool in the company's quest to push the boundaries of what is possible in precision machining.The [Machine Model] has already proven its worth on a number of high-profile projects, producing complex components with incredible precision and efficiency. Its ability to tackle the most challenging machining tasks with ease has made a significant impact on [Company Name]'s ability to deliver exceptional results to their clients. Moreover, the [Machine Model]'s speed and accuracy have allowed [Company Name] to reduce lead times and improve overall productivity, further solidifying their position as a leader in the precision machining industry.In addition to their investments in new machinery, [Company Name] has also expanded their team of talented engineers and machinists. With a relentless focus on recruiting the best and brightest in the industry, the company has assembled a team of highly skilled professionals who are dedicated to pushing the boundaries of what is possible in precision machining. Their collective expertise and innovative thinking have been instrumental in [Company Name]'s ability to take on increasingly complex projects and deliver exceptional results to their clients.Looking to the future, [Company Name] is committed to continuing their tradition of innovation and excellence in precision machining. With their advanced capabilities and talented team, they are well-positioned to take on the most challenging projects and deliver superior results to their clients. As they continue to push the boundaries of what is possible in machining design, [Company Name] is poised to remain at the forefront of the precision machining industry for years to come.
How CNC Lathe Machining is Revolutionizing the Manufacturing Industry
CNC Lathe Machining Revolutionizes Manufacturing IndustryIn today's highly competitive manufacturing industry, companies are constantly seeking innovative technologies and tools to enhance their production processes. One such groundbreaking solution is CNC lathe machining, a cutting-edge technique that has transformed the way companies manufacture their products. With its incredible precision, efficiency, and versatility, CNC lathe machining has become an integral part of numerous industries, enabling them to stay ahead of the game.CNC (Computer Numerical Control) lathe machining involves the use of computer-controlled machines to produce complex and precise parts. Unlike traditional lathe machines, which require manual operation and supervision, CNC lathes can run autonomously after the initial setup. This automation eliminates the risk of human error and enhances the overall efficiency and productivity of the manufacturing process.The CNC lathe machining process begins by designing a 3D model of the desired part using specialized software. This model is then programmed into the CNC lathe machine, allowing it to precisely and accurately replicate the design. The machine utilizes a variety of cutting tools, which are automatically controlled and manipulated by the computer, to shape and finish the part. This results in an exceptional level of precision that cannot be achieved through manual operation.Furthermore, CNC lathe machining offers manufacturers excellent repeatability, meaning that the machine can reproduce identical parts repeatedly with minimal variation. This consistency is crucial in industries such as aerospace, automotive, and electronics, where even the slightest deviation can result in major issues. The ability to replicate parts with high accuracy and consistency increases productivity, reduces waste, and ultimately saves manufacturers time and money.Another significant advantage of CNC lathe machining is its versatility. These machines can work with a wide range of materials, including metals, plastics, and even wood. This flexibility allows manufacturers to adapt to changing market demands and explore new product possibilities. Moreover, CNC lathes can handle complex geometries and intricate designs that would be challenging or impossible to achieve using conventional methods.Companies that have adopted CNC lathe machining into their production processes have witnessed a significant improvement in their overall operations. The speed and efficiency of these machines enable manufacturers to meet tight deadlines and fulfill large orders efficiently. This, in turn, increases customer satisfaction and strengthens business relationships.One company that has successfully integrated CNC lathe machining into its manufacturing process is {}. Founded over {} years ago, they have established themselves as a leader in the industry, specializing in the production of high-quality parts and components. By leveraging state-of-the-art CNC lathe machines, they have been able to meet the evolving needs of their clients and remain at the forefront of technological advancements.The implementation of CNC lathe machining at {} has resulted in several remarkable achievements. Firstly, their production capacity has increased significantly, allowing them to take on more substantial orders and deliver them in a shorter time frame. Secondly, the exceptional precision of their CNC lathes has reduced errors and rejects, resulting in higher product quality and customer satisfaction. Lastly, the versatility of these machines has enabled {} to diversify their product range and explore new market opportunities.As the manufacturing industry continues to evolve, the adoption of CNC lathe machining is expected to become even more widespread. Its numerous benefits, including precision, efficiency, repeatability, and versatility, make it an attractive solution for companies across various sectors. With technological advancements and continuous innovation, CNC lathe machining promises to redefine the manufacturing landscape, enabling businesses to thrive in an increasingly competitive marketplace.In conclusion, CNC lathe machining has revolutionized the manufacturing industry, providing companies with a powerful tool to enhance their production processes. With its unparalleled precision, efficiency, repeatability, and versatility, this cutting-edge technology has become a game-changer in the industry. As more companies, such as {}, embrace CNC lathe machining, the manufacturing sector will continue to witness significant advancements, ensuring sustainable growth and success.
Expert Tips for Machining Metal: The Ultimate Guide for Precision Metalwork
Title: Revolutionizing Metal Machining: Company X Introduces Cutting-Edge InnovationIntroduction:In the dynamic world of metal machining, Company X has emerged as a leading pioneer, focusing on elevating precision and efficiency to new heights. With their unwavering commitment to research and development, they have introduced groundbreaking technologies that are poised to revolutionize the industry. In this article, we delve into Company X's latest innovation in machining metal, its features, and the potential implications on industries worldwide.Enhancing Precision and Efficiency:Building on their expertise in metal machining, Company X has unveiled a cutting-edge technology that promises enhanced precision and efficiency in the manufacturing process. By combining advanced robotics, artificial intelligence, and state-of-the-art algorithms, their innovation ensures unrivaled accuracy and repeatability.The integration of robotics enables Company X to carry out intricate machining tasks with unprecedented precision. These robots are equipped with advanced sensors that constantly monitor the machining process, making real-time adjustments to ensure optimal results. Moreover, with the use of artificial intelligence, the machines are capable of learning and adapting, further improving their precision over time.Additionally, Company X's innovation incorporates proprietary algorithms, specifically designed to optimize machining parameters. By analyzing vast amounts of data generated during the machining process, these algorithms can identify the ideal conditions for different applications. This results in reduced waste, improved surface finishes, and increased overall efficiency.Addressing Cost and Time Constraints:Recognizing the time and cost implications involved in traditional metal machining processes, Company X's new technology aims to alleviate these concerns. With their advanced automation systems, machining processes are streamlined, eliminating manual errors and reducing human intervention. This automation not only saves time but also minimizes labor costs, ultimately enhancing cost-effectiveness for businesses.Moreover, Company X's technology enables a significant reduction in lead times. By implementing predictive maintenance through continuous monitoring, downtime due to machinery failures is minimized. Consequently, businesses can maintain optimal productivity, meeting tight delivery deadlines without compromising on quality.Application across Industries:Company X's innovation transcends the constraints of a single industry. This breakthrough technology is applicable across diverse sectors such as automotive, aerospace, medical, and electronics, just to name a few.In the automotive sector, for instance, precision machining is crucial for the production of engine components, ensuring optimal performance and longevity. With Company X's technology, manufacturers can achieve unparalleled precision, resulting in improved efficiency, reduced friction, and lower emissions.Likewise, in the aerospace industry, where precision and safety are paramount, Company X's innovation brings unparalleled advantages. From manufacturing turbine blades to intricate structural components, their technology guarantees precise tolerances, which are critical for aircraft performance and passenger safety.Looking Ahead:With their latest innovation in metal machining, Company X has showcased their dedication to pushing the boundaries of what is possible. This advanced technology not only enhances precision and efficiency but also addresses cost and time constraints, positioning Company X as a trailblazer in the industry.As businesses across industries seek to stay competitive in a rapidly changing market, Company X's technology presents a compelling solution. By embracing this revolutionary approach to metal machining, businesses can unlock new levels of productivity, quality, and profitability.In conclusion, Company X has boldly redefined the metal machining landscape with its cutting-edge innovation. As this technology becomes more widespread, it has the potential to transform industries worldwide by revolutionizing the production process, streamlining operations, and elevating the standards of precision and efficiency.
Unlocking the Secrets of the Innovative Insert Molding Process
[Title]: Innovative Insert Molding Process Enhances Manufacturing Efficiency[Subtitle]: Taking Manufacturing Precision to New Heights[Date]: [Insert Date][City], [State] - In their relentless pursuit of excellence, [Company Name], a leading manufacturer in the industry, has introduced an innovative insert molding process that promises to revolutionize the manufacturing landscape. This groundbreaking technique has allowed the company to enhance efficiency and precision, cementing their position as pioneers in the field.[Company Name], with their rich history of delivering cutting-edge solutions, has consistently demonstrated their commitment to pushing the boundaries of what is possible. By successfully implementing the insert molding process, they aim to revolutionize the way manufacturing operations are conducted.The insert molding process revolutionizes manufacturing by combining multiple materials or components into a single molded plastic part. This process greatly reduces assembly steps and enhances productivity, streamlining the entire manufacturing process. By eliminating the need for separate components and multiple assembly lines, [Company Name] has significantly reduced production time, allowing them to meet the increasing demands of their customers.Through the innovative use of the insert molding process, [Company Name] has successfully eliminated the need for additional assembly steps, thereby reducing costs and minimizing the margin for error. This not only translates into significant time and cost savings but also ensures a higher degree of quality control and consistency in the final product.Unlike traditional manufacturing techniques, the insert molding process involves the encapsulation of specific components or inserts within the molded plastic part. This creates a strong bond between the plastic and the inserted components, resulting in a durable and reliable end product. This advanced manufacturing technique has been widely hailed as a game-changer, enabling manufacturers to produce complex and compact parts with unmatched precision and reliability.[Company Name]'s mastery of the insert molding process stems from their in-depth understanding of the industry and their continuous investment in cutting-edge technologies. By leveraging their expertise and state-of-the-art facilities, they have succeeded in refining this process to deliver superior quality products to their clients.Furthermore, the insert molding process offers numerous design possibilities, enabling manufacturers to create products that are aesthetically pleasing while maintaining functionality. By seamlessly integrating various materials and components, manufacturers can achieve a more sophisticated and versatile end product.[Company Name] has always been at the forefront of innovation and has earned a reputation for delivering outstanding customer satisfaction. By adopting the insert molding process, they have cemented their position as pioneers in the industry, offering their clients a comprehensive range of solutions that cater to their diverse requirements.The benefits of the insert molding process extend beyond just manufacturing efficiency. By reducing the number of components and assembly steps, [Company Name] has also contributed to a greener and more sustainable industry. The decreased material usage and lower energy consumption associated with this manufacturing technique result in a reduced carbon footprint.[Company Name] takes pride in their dedication to continuous improvement. They constantly strive to push the boundaries of what is possible, and the introduction of the insert molding process is a testament to their relentless pursuit of excellence. This innovation has not only redefined their position in the industry but also set new standards for manufacturing precision and efficiency.In conclusion, [Company Name]'s introduction of the insert molding process has revolutionized the manufacturing landscape. By combining multiple materials or components into one molded plastic part, they have enhanced efficiency, reduced production time, and improved the overall quality of their products. This groundbreaking technique is a testament to the company's commitment to innovation and customer satisfaction. As [Company Name] continues to lead the way in cutting-edge solutions, the future of manufacturing looks brighter than ever.