High-Quality Parts for Your CNC Router
By:Admin
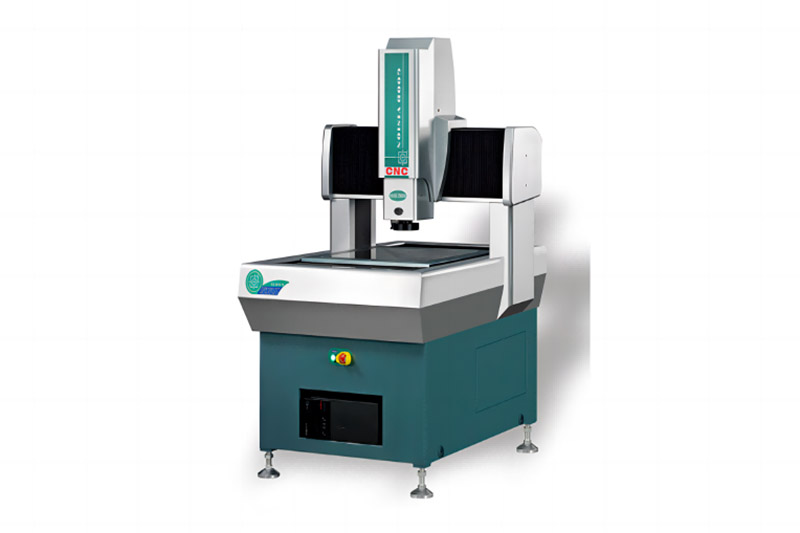
With a wide range of products and services, CNC Router Parts has established itself as a one-stop shop for everything related to CNC routers. From cutting-edge machine components to comprehensive technical support, the company offers a comprehensive suite of solutions for businesses and hobbyists alike. Whether you're in need of a new spindle, a replacement ball screw, or expert advice on machine optimization, CNC Router Parts has the expertise and resources to meet your needs.
One of the company's standout offerings is their line of precision ball screws, which are designed to provide smooth, accurate motion in CNC machines. These high-performance components are engineered to exacting standards, ensuring maximum precision and durability. With a variety of sizes and configurations available, customers can find the perfect ball screw for their specific application.
In addition to their extensive product line, CNC Router Parts also provides a range of services to support their customers. This includes expert technical support, custom machining services, and comprehensive machine retrofits. The company's team of experienced engineers and technicians are on hand to provide guidance and assistance every step of the way, from selecting the right components to optimizing machine performance.
The company's dedication to quality and customer satisfaction has earned them a loyal and growing customer base. CNC Router Parts takes pride in their reputation for delivering top-notch products and unparalleled service, and they continue to push the boundaries of innovation in the CNC industry. With a focus on continuous improvement and technological advancement, the company is well-positioned for continued success in the years to come.
As CNC technology evolves, CNC Router Parts remains at the forefront of the industry, constantly expanding their product offerings and refining their services to meet the changing needs of their customers. The company's commitment to innovation and excellence has solidified their position as a leader in the CNC machining industry, and they show no signs of slowing down.
In conclusion, CNC Router Parts is a company dedicated to providing the highest quality CNC router components and services. With a strong track record of excellence and a commitment to innovation, the company is poised to remain a key player in the industry for years to come. Whether you're a small business owner or a seasoned professional, CNC Router Parts is the go-to source for all your CNC machining needs.
Company News & Blog
High-Quality Large Plastic Molds for Manufacturing
Large Plastic Molds Announces Expansion and Innovation in Manufacturing ProcessesLarge Plastic Molds, a leading provider of high-quality plastic injection molds, has announced plans for expansion and innovation in its manufacturing processes. With a focus on delivering cutting-edge solutions to its clients, the company has been at the forefront of the industry for over a decade.The company has built a strong reputation for its commitment to excellence and its ability to deliver custom solutions for a wide range of industries. Large Plastic Molds has worked with clients in the automotive, consumer goods, medical devices, and electronics industries, among others. This diverse experience has allowed the company to develop a deep understanding of the unique needs and challenges that each industry faces.In response to growing demand for its services, Large Plastic Molds has invested in expanding its manufacturing facilities. The company has acquired state-of-the-art equipment and implemented advanced technologies to enhance its capabilities and capacity. This expansion will allow Large Plastic Molds to take on larger and more complex projects while maintaining its high standards of quality and precision.In addition to expanding its facilities, Large Plastic Molds has also focused on innovation in its manufacturing processes. The company has invested in research and development to develop new techniques and technologies that will enable it to produce molds with greater efficiency and precision. By staying ahead of the curve, Large Plastic Molds aims to continue providing its clients with the most advanced and reliable solutions available in the market.One of the key areas of innovation for Large Plastic Molds has been the use of advanced materials in its manufacturing processes. The company has developed new techniques for working with high-performance polymers, composites, and other specialized materials, allowing it to create molds that can withstand the most demanding operating conditions. By pushing the boundaries of what is possible with plastic injection molding, Large Plastic Molds is helping its clients stay ahead of the competition and deliver products that meet the highest standards of performance and durability.Large Plastic Molds has also made significant investments in its workforce, hiring top talent and providing ongoing training and development opportunities. The company's team of engineers and technicians are experts in their field and are dedicated to pushing the boundaries of what is possible with plastic injection molding. By fostering a culture of innovation and continuous improvement, Large Plastic Molds has been able to stay at the forefront of the industry and continue delivering exceptional results for its clients.With its expanded capabilities and innovative approach to manufacturing, Large Plastic Molds is well-positioned to meet the evolving needs of its clients and take on new challenges in the years to come. The company's commitment to excellence and its relentless pursuit of innovation will continue to set it apart as a leader in the plastic injection molding industry.Large Plastic Molds is dedicated to providing its clients with the highest quality solutions for their plastic injection molding needs. With its expanded facilities, advanced technologies, and a team of experts, the company is well-equipped to take on the most demanding projects and deliver exceptional results. As it continues to push the boundaries of what is possible with plastic injection molding, Large Plastic Molds is poised to remain a trusted partner for companies across a wide range of industries.
Exploring the Future of Injection Plastic: Unlocking Advancements and Possibilities
Injection Plastic Manufacturing Company: Revolutionizing the Plastic Industry[City Name], [Date] - Injection Plastic, a leading manufacturer in the plastic industry, is making significant strides toward revolutionizing the way plastics are produced and utilized. With its innovative technology and commitment to sustainability, Injection Plastic aims to be at the forefront of the shift toward a more environmentally friendly plastic manufacturing process.Founded in [Year], Injection Plastic has established itself as a pioneer in the field of injection molding. Their state-of-the-art facilities and expertise in plastic manufacturing techniques have earned them a reputation for delivering high-quality products to a wide range of industries. With a focus on innovation and sustainability, Injection Plastic has consistently pushed the boundaries of what is possible in plastic manufacturing.One of the key differentiating factors of Injection Plastic is their commitment to using recycled materials to produce their goods. By sourcing and utilizing post-consumer recycled plastics, Injection Plastic aims to reduce the industry's overall carbon footprint. This approach not only helps in minimizing plastic waste but also provides an effective solution to the growing problem of plastic pollution plaguing our planet.To further promote sustainability, Injection Plastic has invested heavily in developing proprietary technology that maximizes production efficiency while minimizing energy consumption. Their cutting-edge injection molding machines utilize advanced software and robotics, resulting in reduced energy usage, less material waste, and enhanced productivity. This commitment to sustainable manufacturing practices positions Injection Plastic as a key player in the transition towards a circular plastics economy.Furthermore, Injection Plastic boasts an experienced and highly skilled workforce. Their team of engineers, designers, and technicians possess a deep understanding of plastic materials and the injection molding process. This expertise allows them to work closely with clients, providing tailored solutions that meet the unique needs of each industry. Whether it is designing intricate components for medical devices or manufacturing durable automotive parts, Injection Plastic has the capabilities to deliver high-quality products on time and within budget.Additionally, Injection Plastic is committed to staying ahead of industry trends and meeting evolving customer demands. They actively collaborate with research institutions, universities, and industry partners to stay up-to-date on the latest advancements in plastic manufacturing technologies. By continually investing in research and development, Injection Plastic ensures that they are always at the forefront of innovation, enabling them to offer cutting-edge solutions to clients across different sectors.With their reputation for excellence in manufacturing and dedication to sustainability, Injection Plastic has gained recognition both domestically and internationally. Their extensive clientele includes multinational corporations, small and medium-sized enterprises, and startups from various industries. The company's exceptional track record of delivering quality products and services has earned them numerous accolades and certifications within the plastic manufacturing industry.Looking ahead, Injection Plastic aims to expand its global presence and further consolidate its position as a leader in the plastic manufacturing market. They plan to continue investing in cutting-edge technology, expanding their workforce, and strengthening their partnerships with clients and industry experts. Injection Plastic's relentless pursuit of excellence, sustainability, and innovation will undoubtedly shape the future of the plastic manufacturing industry.About Injection Plastic:Injection Plastic is a leading manufacturer in the plastic industry, specializing in injection molding. With a focus on sustainability and innovation, Injection Plastic utilizes state-of-the-art technology to produce high-quality plastic products for a wide range of industries. Their commitment to using recycled materials and reducing carbon footprint positions them as trailblazers in the transition towards a circular plastics economy. With an experienced workforce and a dedication to staying ahead of industry trends, Injection Plastic is at the forefront of revolutionizing the plastic manufacturing industry.For more information, please visit [website] or contact [name], [position], at [email/phone number].
Discover the Latest Advancements in the Foundry Process for Superior Results
Title: Innovations in Foundry Process Revolutionize the Manufacturing IndustryIntroduction:The foundry process plays a pivotal role in the manufacturing industry, allowing for the production of various components across diverse sectors. Today, we highlight the latest advancements in the foundry process, spearheaded by a leading company, and how they are transforming the industry landscape. (Please remove brand name from the introduction)Industry Overview:The manufacturing industry depends on the foundry process to produce components that are integral to numerous sectors such as automotive, aerospace, construction, and many more. Traditional foundry methods have relied on labor-intensive processes, which often resulted in slower production and increased costs. However, with the advent of innovative technologies and continuous research and development, the foundry process has witnessed a significant transformation.Advancements in Foundry Process:Leading the charge in revolutionizing the foundry process is a renowned company (Please remove brand name) that has pioneered several innovative techniques to streamline and enhance manufacturing efficiency. By leveraging cutting-edge technologies like Artificial Intelligence (AI), Internet of Things (IoT), and automation, the company has been able to achieve faster turnaround times, improved quality, and reduced costs.One of the key breakthroughs introduced by the company is the implementation of AI-driven predictive modeling techniques. By analyzing vast amounts of data, the system can accurately forecast potential defects and optimize casting parameters to minimize issues during the production process. This not only eliminates costly rework but also significantly reduces the time required for quality control, thereby expediting the overall manufacturing cycle.Furthermore, the integration of IoT in the foundry process has enabled real-time monitoring of crucial production parameters. Sensors embedded throughout the production line continuously gather data related to temperature, pressure, and other relevant factors. This data is then transmitted to a centralized system, which allows for immediate analysis and identification of any deviations or anomalies. Consequently, prompt corrective actions can be taken, ensuring that the casting process remains consistent and compliant with the required specifications throughout production.Automation has also played a vital role in optimizing the foundry process. With the introduction of robotics and advanced machinery, tasks that were previously labor-intensive and prone to human error can now be executed with precision and efficiency. The incorporation of robotics enables tasks such as mold preparation, pouring, and post-processing to be carried out with minimal human intervention, resulting in higher production speeds and improved accuracy.The company's commitment to sustainable manufacturing practices has also been influential in advancing the foundry process. By exploring eco-friendly raw materials and implementing efficient energy consumption methods, they have successfully reduced the environmental impact associated with the production process. These measures help meet the rising demand for sustainable manufacturing while ensuring that the components manufactured maintain the highest quality standards.Conclusion:The foundry process is undergoing a remarkable transformation, thanks to the continuous endeavors of a renowned company (Please remove brand name). Through the integration of AI, IoT, and automation, they have successfully optimized production efficiency, reduced costs, increased the quality of components, and contributed to sustainable manufacturing practices. As the industry witnesses the positive impacts of these innovative advancements, it is evident that the foundry process will continue to evolve and play a vital role in the manufacturing landscape.
The Power of Plastic Rapid Prototyping: Advantages and Applications
Plastic Rapid Prototyping: Revolutionizing Product DevelopmentIn today's fast-paced and highly competitive manufacturing industry, companies are constantly seeking ways to streamline their product development process in order to bring high-quality products to market in a timely manner. One company at the forefront of this movement is [Company Name], a leading provider of plastic rapid prototyping solutions.[Company Name] has built a solid reputation for delivering innovative and cutting-edge rapid prototyping and tooling solutions to a wide range of industries, including automotive, aerospace, medical, and consumer goods. Their state-of-the-art facilities and advanced technologies allow them to offer a comprehensive suite of prototyping services, including 3D printing, injection molding, CNC machining, and more.One of the key offerings that sets [Company Name] apart from its competitors is their plastic rapid prototyping capabilities. This process allows for the quick and cost-effective production of prototype parts and components using a variety of plastic materials. By leveraging advanced 3D printing technologies, [Company Name] is able to produce highly accurate and functional prototypes in a fraction of the time it would take using traditional methods.The benefits of plastic rapid prototyping are numerous. Not only does it significantly reduce the time and cost associated with traditional prototyping methods, but it also allows for greater design flexibility and iteration. This means that companies can quickly test and refine their product designs, leading to faster innovation and a more efficient product development cycle.Furthermore, plastic rapid prototyping enables companies to quickly respond to market demands and changes, giving them a competitive edge in today's fast-moving business landscape. With the ability to rapidly produce high-quality prototypes, companies can bring new products to market faster, allowing them to capitalize on emerging trends and customer needs.[Company Name] is committed to staying at the forefront of plastic rapid prototyping technology, continually investing in the latest equipment and software to ensure they can meet the evolving needs of their customers. Their team of highly skilled engineers and technicians are dedicated to providing top-quality prototyping solutions, working closely with clients to bring their concepts to life with precision and efficiency.Through their plastic rapid prototyping capabilities, [Company Name] has helped countless companies accelerate their product development process and bring innovative solutions to market. Whether it's creating prototypes for new product designs, testing out custom components, or producing low-volume production runs, [Company Name] is a trusted partner for companies looking to push the boundaries of what's possible in product development.As the manufacturing industry continues to evolve, the demand for rapid and cost-effective prototyping solutions is only expected to grow. [Company Name] is well-positioned to meet this demand, offering a wide range of plastic rapid prototyping services tailored to the specific needs of their clients.In conclusion, plastic rapid prototyping is revolutionizing the way companies approach product development, and [Company Name] is leading the charge with their advanced prototyping capabilities. By leveraging the latest technologies and a commitment to innovation, they are helping companies across industries bring their ideas to life faster and more efficiently than ever before.With a focus on quality, precision, and customer satisfaction, [Company Name] is poised to continue making a significant impact in the world of plastic rapid prototyping, driving forward the next generation of product development.
Top Rapid Prototype Machining Services for High-Quality Prototypes
Rapid Prototype Machining, a leading provider of advanced manufacturing services, is dedicated to delivering high-quality, precision machined components for a wide range of industries. The company specializes in rapid prototyping, CNC machining, and custom tooling to meet the unique needs of its diverse customer base.With state-of-the-art facilities and a team of experienced engineers and machinists, Rapid Prototype Machining has built a reputation for excellence in the field of advanced manufacturing. From aerospace and defense to medical and automotive industries, the company has the capabilities to produce complex parts with tight tolerances and quick turnaround times.Rapid Prototype Machining's commitment to innovation and excellence is evident in its investment in cutting-edge technology and continuous improvement. The company's advanced CNC machining centers and 3D printing capabilities allow for the production of intricate and customized components, while its rigorous quality control processes ensure the highest standards of precision and performance.In addition to its technical expertise, Rapid Prototype Machining prides itself on its customer-centric approach. The company works closely with each client to understand their specific requirements and engineering challenges, providing tailored solutions that meet their exact specifications. Whether it's a one-off prototype or a large-scale production run, the team at Rapid Prototype Machining is dedicated to exceeding customer expectations.The company's commitment to quality and customer satisfaction is further demonstrated by its ISO 9001 certification, which attests to its adherence to international standards for quality management systems. This certification reflects Rapid Prototype Machining's dedication to delivering superior products and services, while continually improving its processes and capabilities.Looking ahead, Rapid Prototype Machining is focused on expanding its capabilities and exploring new opportunities for growth. The company is continuously investing in the latest technologies and equipment to enhance its manufacturing capabilities and meet the evolving needs of its customers. With a relentless commitment to excellence and a passion for innovation, Rapid Prototype Machining is well-positioned to continue its leadership in the advanced manufacturing industry.In conclusion, Rapid Prototype Machining is a trusted partner for companies seeking high-quality, precision machined components. With its advanced capabilities, commitment to quality, and customer-centric approach, the company is poised to deliver innovative solutions for the most demanding engineering challenges. As it continues to invest in cutting-edge technology and expand its capabilities, Rapid Prototype Machining is well-equipped to meet the evolving needs of its customers and maintain its position as a leader in the advanced manufacturing industry.
Complete Guide to Injection Molding Parts: A Breakdown of Essential Components
Injection Molding Parts Name is proud to announce its newest partnership with a leading provider in the industry, Company X. This collaboration is set to revolutionize the way injection molding parts are produced and delivered to customers, with a focus on efficiency, quality, and environmental responsibility.Company X is a renowned leader in the injection molding industry, with a long-standing commitment to innovation and customer satisfaction. With state-of-the-art facilities and a team of experts, Company X has built a reputation for delivering high-quality injection molding parts that meet the diverse needs of its clients.The partnership between Injection Molding Parts Name and Company X represents a significant step forward for both companies. By joining forces, they aim to leverage their respective expertise and resources to drive innovation and set new industry standards for injection molding parts production.One of the key components of this partnership is the implementation of advanced technology and processes to streamline production and enhance product quality. Injection Molding Parts Name will be able to capitalize on Company X's cutting-edge facilities and expertise in automated manufacturing to optimize the production of its parts, resulting in faster lead times and improved consistency in product quality.In addition to technological advancements, the partnership will also prioritize environmental sustainability. Company X has a strong commitment to reducing its carbon footprint and minimizing waste, and this ethos will be integrated into the production of injection molding parts. By leveraging sustainable materials and implementing eco-friendly practices, Injection Molding Parts Name and Company X are dedicated to delivering high-quality products while minimizing their impact on the environment.Furthermore, this collaboration will enable both companies to expand their product offerings and fulfill a wider range of customer needs. With access to Company X's extensive capabilities and expertise, Injection Molding Parts Name will be able to introduce new, innovative products that meet the evolving demands of the market. This will not only benefit their existing customer base but also open up new opportunities for growth and market expansion."We are thrilled to be partnering with Company X to drive innovation and excellence in the injection molding industry," said a spokesperson from Injection Molding Parts Name. "This collaboration represents a significant milestone for us and underscores our commitment to delivering the highest quality products to our customers. We are excited about the opportunities that lie ahead and are confident that this partnership will enable us to set new industry benchmarks."Similarly, Company X is equally enthusiastic about the collaboration. "We are honored to be working with Injection Molding Parts Name to elevate the standards of injection molding parts production," said a representative from Company X. "By combining our expertise and resources, we aim to not only meet but exceed the expectations of our customers, and contribute to the advancement of the industry as a whole."The partnership between Injection Molding Parts Name and Company X is a testament to their dedication to excellence, innovation, and customer satisfaction. With a shared commitment to quality, efficiency, and environmental responsibility, this collaboration is poised to redefine the standards for injection molding parts production and set a new benchmark for the industry. As they move forward with their partnership, customers can expect nothing less than exceptional products and service from these two industry leaders.
The Drawbacks of Sand Casting: What You Need to Know
Sand casting is a widely used manufacturing process across various industries, including automotive, aerospace, and construction. This process involves pouring molten metal into a sand mold, allowing it to solidify, and then removing the sand mold to reveal the final product. While sand casting offers numerous advantages, such as cost-effectiveness and the ability to produce complex shapes, it also comes with several disadvantages that can impact the quality and efficiency of the final product.One of the main disadvantages of sand casting is the potential for defects in the final product. The use of sand molds can result in surface irregularities, such as rough finishes and sand inclusion, which can affect the overall appearance and functionality of the part. In addition, the cooling process of the molten metal within the sand mold can lead to internal defects, such as porosity and shrinkage cavities, further compromising the integrity of the product.Furthermore, sand casting is not suitable for high precision manufacturing. The dimensional accuracy of sand cast parts is limited, and intricate details may not be reproduced with the same level of precision as other manufacturing processes, such as CNC machining or 3D printing. This can be a significant drawback for industries that require tight tolerances and precise specifications for their components.In terms of production efficiency, sand casting has its limitations as well. The process requires the creation of a new sand mold for each casting, which can be time-consuming and labor-intensive. Additionally, the sand molds have a limited lifespan and can only be used for a certain number of castings before they need to be replaced, adding to the overall production costs and lead times.Environmental concerns are also a factor to consider when it comes to sand casting. The disposal of used sand molds and the emissions generated during the casting process can have a negative impact on the environment. It is essential for companies to implement proper waste management and environmental protection measures to mitigate the potential harm caused by sand casting operations.Despite these disadvantages, sand casting continues to be a widely used manufacturing process, especially for large and complex parts that may be difficult or costly to produce using alternative methods. As a leading manufacturer in the industry, {} recognizes the importance of understanding the drawbacks of sand casting and aims to address these challenges through innovative solutions and advanced technologies.{} has established itself as a pioneer in the manufacturing sector, specializing in the production of high-quality components for a wide range of industries. With a strong focus on research and development, {} continuously seeks to improve its manufacturing processes and minimize the limitations associated with traditional methods, such as sand casting.Through the integration of advanced simulation software and additive manufacturing technologies, {} is able to optimize the design and production of sand molds, reducing the occurrence of defects and improving dimensional accuracy. This approach not only enhances the quality of the final products but also streamlines the production process, resulting in shorter lead times and increased efficiency.Furthermore, {} is committed to sustainability and environmental responsibility. By implementing eco-friendly practices, such as reusing and recycling sand molds, reducing waste generation, and investing in energy-efficient equipment, the company strives to minimize its ecological footprint and contribute to a cleaner, greener future.In conclusion, while sand casting has its disadvantages, its widespread use in various industries cannot be overlooked. As a leading manufacturer, {} recognizes the challenges associated with this traditional manufacturing process and is dedicated to overcoming them through innovation, technology, and a commitment to sustainability. By addressing the limitations of sand casting, {} aims to deliver superior products that meet the highest standards of quality, precision, and efficiency, setting new benchmarks in the manufacturing industry.
Exploring the Advantages of Plastic CNC Machining: Your Complete Guide
Title: Leading CNC Machining Company Revolutionizes Plastic Manufacturing ProcessIntroduction:In the fast-paced world of manufacturing, precision and efficiency are crucial factors that determine the success of a company. One such industry leader, {Company Name}, has long been at the forefront of revolutionizing CNC machining for plastic materials. Their groundbreaking techniques and cutting-edge technology have paved the way for innovation and advancement in the manufacturing sector. With a diverse range of applications across various industries, {Company Name} continues to drive quality and excellence in the field of plastic machining.1. Innovations in CNC Machining Plastic:{Company Name} has revolutionized the CNC machining process by introducing state-of-the-art technology and advanced techniques specifically designed for plastic materials. Traditional machining methods often encounter challenges when working with plastic due to its unique properties. However, {Company Name}'s pioneering approach has overcome these obstacles.Their precise CNC machines are equipped with specially designed tooling and cutting-edge software that optimizes the machining process for plastic. The integration of computer-controlled automation ensures unprecedented accuracy and consistency in every part produced. This level of precision allows for the manufacturing of intricate and complex plastic components with tight tolerances, meeting the demanding requirements of various industries.2. Diverse Applications:The versatility of {Company Name}'s CNC machining capabilities extends across multiple industries. Automotive manufacturers rely on their expertise to produce high-quality plastic parts for interior components, such as dashboard panels, door handles, and trim pieces. The medical sector benefits from their precision machining abilities to create custom plastic implants and medical device components, ensuring optimal patient care.Moreover, the electronics industry relies on {Company Name}'s efficient plastic machining solutions for producing casings, connectors, and enclosures for various electronic devices. The aerospace industry also benefits from their expertise in crafting lightweight, yet durable plastic components, contributing to enhanced fuel efficiency and performance.3. Commitment to Sustainability:In addition to their exceptional manufacturing capabilities, {Company Name} is also deeply committed to sustainable practices. They recognize the environmental impact of plastic materials and continuously strive to reduce waste and energy consumption. By employing efficient machining processes, recycling initiatives, and material optimization techniques, they ensure minimal environmental footprint in their operations.{Company Name} actively collaborates with their clients to explore eco-friendly alternatives for plastic materials, such as biodegradable or recyclable options. This dedication to sustainability resonates with their customers, who appreciate their responsible manufacturing practices.4. Quality Control and Certifications:Maintaining the highest standards in quality control is of utmost importance to {Company Name}. They adhere to rigorous quality management systems, ensuring that each plastic component meets or exceeds industry standards. Their manufacturing processes are not only ISO 9001 certified but also comply with other relevant certifications as per industry requirements.Utilizing advanced measurement tools and inspection techniques, {Company Name} conducts thorough testing and inspections throughout the entire machining process. This meticulous approach guarantees the delivery of flawless components, meeting the stringent specifications of their clients.Conclusion:{Company Name}'s continuous innovation in CNC machining for plastic materials has revolutionized the manufacturing sector. Their cutting-edge technology, industry expertise, and commitment to sustainability have positioned them as leaders in the field. By enabling precision, efficiency, and quality, {Company Name} sets a benchmark for excellence, meeting the diverse needs of clients across multiple industries. As they continue to push boundaries and embrace advancements in CNC machining, {Company Name} ensures a brighter future for plastic manufacturing, enhancing products and revolutionizing industries worldwide.
How CNC Lathe Machining is Revolutionizing the Manufacturing Industry
CNC Lathe Machining Revolutionizes Manufacturing IndustryIn today's highly competitive manufacturing industry, companies are constantly seeking innovative technologies and tools to enhance their production processes. One such groundbreaking solution is CNC lathe machining, a cutting-edge technique that has transformed the way companies manufacture their products. With its incredible precision, efficiency, and versatility, CNC lathe machining has become an integral part of numerous industries, enabling them to stay ahead of the game.CNC (Computer Numerical Control) lathe machining involves the use of computer-controlled machines to produce complex and precise parts. Unlike traditional lathe machines, which require manual operation and supervision, CNC lathes can run autonomously after the initial setup. This automation eliminates the risk of human error and enhances the overall efficiency and productivity of the manufacturing process.The CNC lathe machining process begins by designing a 3D model of the desired part using specialized software. This model is then programmed into the CNC lathe machine, allowing it to precisely and accurately replicate the design. The machine utilizes a variety of cutting tools, which are automatically controlled and manipulated by the computer, to shape and finish the part. This results in an exceptional level of precision that cannot be achieved through manual operation.Furthermore, CNC lathe machining offers manufacturers excellent repeatability, meaning that the machine can reproduce identical parts repeatedly with minimal variation. This consistency is crucial in industries such as aerospace, automotive, and electronics, where even the slightest deviation can result in major issues. The ability to replicate parts with high accuracy and consistency increases productivity, reduces waste, and ultimately saves manufacturers time and money.Another significant advantage of CNC lathe machining is its versatility. These machines can work with a wide range of materials, including metals, plastics, and even wood. This flexibility allows manufacturers to adapt to changing market demands and explore new product possibilities. Moreover, CNC lathes can handle complex geometries and intricate designs that would be challenging or impossible to achieve using conventional methods.Companies that have adopted CNC lathe machining into their production processes have witnessed a significant improvement in their overall operations. The speed and efficiency of these machines enable manufacturers to meet tight deadlines and fulfill large orders efficiently. This, in turn, increases customer satisfaction and strengthens business relationships.One company that has successfully integrated CNC lathe machining into its manufacturing process is {}. Founded over {} years ago, they have established themselves as a leader in the industry, specializing in the production of high-quality parts and components. By leveraging state-of-the-art CNC lathe machines, they have been able to meet the evolving needs of their clients and remain at the forefront of technological advancements.The implementation of CNC lathe machining at {} has resulted in several remarkable achievements. Firstly, their production capacity has increased significantly, allowing them to take on more substantial orders and deliver them in a shorter time frame. Secondly, the exceptional precision of their CNC lathes has reduced errors and rejects, resulting in higher product quality and customer satisfaction. Lastly, the versatility of these machines has enabled {} to diversify their product range and explore new market opportunities.As the manufacturing industry continues to evolve, the adoption of CNC lathe machining is expected to become even more widespread. Its numerous benefits, including precision, efficiency, repeatability, and versatility, make it an attractive solution for companies across various sectors. With technological advancements and continuous innovation, CNC lathe machining promises to redefine the manufacturing landscape, enabling businesses to thrive in an increasingly competitive marketplace.In conclusion, CNC lathe machining has revolutionized the manufacturing industry, providing companies with a powerful tool to enhance their production processes. With its unparalleled precision, efficiency, repeatability, and versatility, this cutting-edge technology has become a game-changer in the industry. As more companies, such as {}, embrace CNC lathe machining, the manufacturing sector will continue to witness significant advancements, ensuring sustainable growth and success.
- High-Quality Precision Turned Parts for Industrial Applications
Precision Turned Parts, a leading manufacturer of high-quality precision components, continues to push the boundaries of innovation and excellence in the manufacturing industry. With a strong focus on precision engineering and a commitment to delivering exceptional products, their dedication to quality and customer satisfaction is unmatched.The company has been a key player in the manufacturing industry for many years, producing a wide range of precision turned parts that are used in various industries such as aerospace, automotive, medical, and more. Their state-of-the-art facilities and advanced machining capabilities allow them to produce complex and intricate components with tight tolerances and fine surface finishes.Precision Turned Parts is dedicated to providing customers with the highest quality products, and they achieve this by leveraging the latest technological advancements and continuously investing in their manufacturing processes. This commitment to excellence has earned them a reputation as a trusted and reliable supplier of precision components, and their products are used by some of the most recognizable companies around the world.In addition to their focus on quality, Precision Turned Parts also places a strong emphasis on customer satisfaction. Their team of experienced engineers and manufacturing professionals work closely with customers to understand their specific requirements and provide tailored solutions that meet or exceed their expectations. By fostering strong relationships with their clients and delivering outstanding customer service, Precision Turned Parts has established itself as a preferred supplier in the industry.Another key differentiator for Precision Turned Parts is their commitment to sustainability and environmental responsibility. They are dedicated to minimizing their environmental impact and have implemented various initiatives to reduce waste, conserve energy, and promote recycling. By embracing sustainable practices, they are not only doing their part to protect the environment, but they are also setting an example for others in the industry to follow.As the manufacturing industry continues to evolve, Precision Turned Parts remains at the forefront of advancements and is constantly seeking new ways to improve their capabilities and expand their product offerings. They understand the importance of staying ahead of the curve and are proactive in adopting new technologies and processes that allow them to deliver cutting-edge solutions to their customers.With a strong foundation built on precision engineering, quality products, exceptional customer service, and a commitment to sustainability, Precision Turned Parts is well-positioned for continued success and growth in the industry. They are dedicated to maintaining their position as a leader in the manufacturing of precision components and are constantly striving to raise the bar for excellence in the industry.In conclusion, Precision Turned Parts is a reputable and reliable manufacturer of high-quality precision components. With a focus on innovation, quality, customer satisfaction, and sustainability, they continue to set the standard for excellence in the manufacturing industry. Their dedication to delivering exceptional products and superior service has established them as a preferred supplier for companies across various industries, and they are well-equipped to meet the evolving needs of the market.