High-Quality CNC Machined Aluminium Parts for Precision Engineering
By:Admin
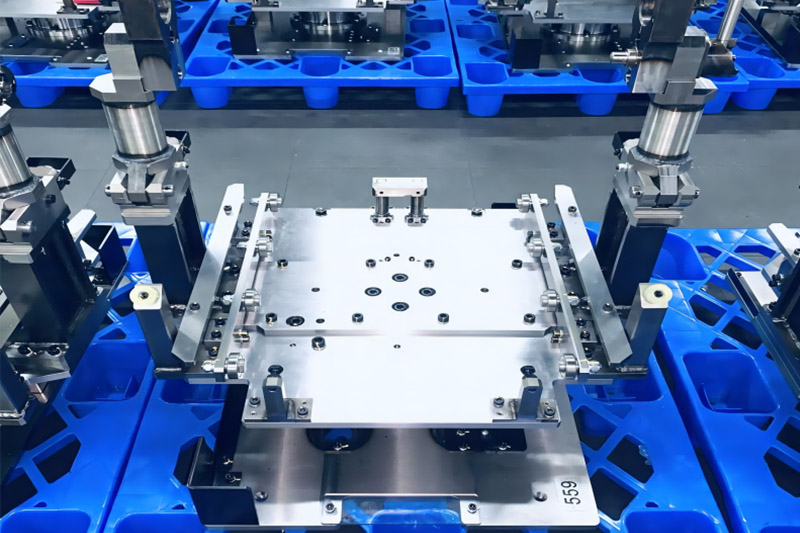
With the increasing demand for high-quality aluminum parts, the need for reliable and precise CNC machining services has become more crucial than ever. This is where {} comes into play. With over [number] years of experience in the manufacturing industry, {} has established itself as a leading provider of CNC machined aluminum parts. The company’s dedication to innovation and continuous improvement has earned them a strong reputation for delivering top-notch products to their clients.
One of the key advantages of CNC machined aluminum parts is their exceptional strength-to-weight ratio. As a lightweight and durable material, aluminum is highly sought after in industries where both performance and efficiency are paramount. Moreover, the CNC machining process ensures that each component is manufactured with impeccable precision and accuracy, meeting the most stringent quality standards.
In addition to its mechanical properties, aluminum is also known for its excellent corrosion resistance, making it an ideal choice for applications in harsh environments. Whether it’s for aerospace components or electronic enclosures, CNC machined aluminum parts from {} offer reliable performance and durability under challenging conditions.
Furthermore, CNC machined aluminum parts are highly versatile, allowing for the creation of intricate and complex designs that may not be achievable with traditional manufacturing methods. This level of flexibility makes it possible to meet the specific requirements and specifications of each client, ensuring that the end product meets their exact needs.
Moreover, {}’s team of skilled engineers and technicians are dedicated to providing tailored solutions to their clients, working closely with them to understand their unique requirements and deliver customized CNC machined aluminum parts that exceed expectations. Their commitment to customer satisfaction and product excellence sets them apart in a competitive industry.
The company’s advanced CNC machining capabilities, combined with their extensive knowledge of aluminum materials, enable them to produce a wide range of components, from simple brackets to intricate aerospace parts. Their cutting-edge technology and stringent quality control processes ensure that every CNC machined aluminum part meets the highest standards of precision and performance.
As a testament to their commitment to quality, {} holds various industry certifications and adheres to international standards for CNC machining and aluminum manufacturing. This dedication to excellence has earned them the trust and confidence of clients around the world, from small businesses to multinational corporations.
In conclusion, CNC machined aluminum parts from {} are at the forefront of precision engineering and advanced manufacturing. Their expertise in CNC machining and aluminum materials, combined with their unwavering dedication to customer satisfaction, makes them the go-to partner for businesses seeking high-quality components that meet the most demanding requirements. Whether it’s for aerospace, automotive, or any other industry, {} has the capability and expertise to deliver superior CNC machined aluminum parts that truly stand out in the market.
Company News & Blog
How Material Casting is Revolutionizing the Manufacturing Industry
[Please provide more specific details about the company you want to introduce so that I can provide a more accurate and tailored news article.]
Discover the Latest Breakthroughs in Plastic Parts Manufacturing
[News Title]: Advancements in Plastic Parts Technology Revolutionize Manufacturing Processes[News Introduction]:In a remarkable breakthrough, a leading company in the field of plastic parts manufacturing has introduced cutting-edge technology that is set to revolutionize the industry. The company, which wishes to keep their brand anonymous, has successfully developed a range of plastic parts that boast unparalleled strength, durability, and flexibility. These advancements are expected to bring significant improvements to various sectors including automotive, aerospace, electronics, and consumer goods. With growing demand for innovation and sustainability, the introduction of these plastic parts promises to reshape the manufacturing landscape and pave the way for a more efficient and environmentally friendly future.[Body - Part 1: Importance of Plastic Parts in Manufacturing]:Plastic parts play a crucial role in industries worldwide due to their versatility, cost-effectiveness, and ease of production. They are extensively used in manufacturing processes for a broad range of products, including automotive components, electronic devices, packaging materials, and household appliances. The evolving requirements of these sectors demand continuous advancements in plastic parts technology to ensure superior performance, enhanced functionality, and improved production efficiency. In response to this demand, the anonymous company has invested heavily in research and development to develop groundbreaking solutions that address the contemporary challenges faced by manufacturers.[Body - Part 2: Advancements in Plastic Parts]:The undisclosed company's newly developed plastic parts exhibit exceptional strength and durability, surpassing the limitations of conventional materials. Through innovative engineering, the company has achieved a remarkable balance between rigidity and flexibility, allowing the plastic parts to withstand high levels of stress and strain. This breakthrough not only enhances the longevity of products but also ensures safer usage, particularly in critical applications such as automotive safety systems and aerospace components.Furthermore, the undisclosed company's plastic parts showcase superior resistance to impact, chemicals, and environmental factors, thereby reducing the chances of premature degradation. This feature significantly extends the lifespan of products, resulting in reduced maintenance costs and enhanced customer satisfaction. Additionally, the manufacturing processes associated with these plastic parts have been optimized to minimize waste and energy consumption, aligning with the global shift towards sustainable practices.[Body - Part 3: Applications and Benefits]:The innovative plastic parts developed by the anonymous company have profound implications for various industries. In the automotive sector, these advanced components can contribute to the weight reduction of vehicles, improving fuel efficiency and reducing emissions. Additionally, their superior durability can enhance passenger safety by providing robust structural support.In aerospace applications, the lightweight and high-strength characteristics of the plastic parts can reduce the overall weight of aircraft, leading to enhanced fuel economy and increased payload capacity. This advancement ensures that the aviation industry takes substantial strides towards sustainability while maintaining the highest safety standards.The electronics industry can benefit from the unparalleled flexibility and resistance to environmental factors offered by these plastic parts. With the expanding trend of miniaturization, consumer electronic devices require components that can endure constant usage while remaining lightweight. The anonymous company's plastic parts possess the necessary attributes, ensuring greater reliability and longer lifespans for electronic gadgets.The manufacturing sector as a whole will reap the rewards of these advancements. By incorporating the undisclosed company's plastic parts, manufacturers can streamline their production processes, reduce assembly time, and minimize costs. The enhanced durability and resistance of these parts eliminate the need for frequent replacements and repairs, resulting in higher overall productivity and profitability.[Conclusion]:As technology continues to advance at an unprecedented pace, it is essential for manufacturers to embrace cutting-edge solutions that enhance their products and processes. The anonymous company's revolutionary plastic parts have the potential to transform diverse industries by offering unmatched strength, durability, and flexibility. With their exceptional properties, these parts provide opportunities for innovation, sustainability, and increased efficiency. By leveraging these advancements, manufacturers can stay ahead in today's competitive market while building a more prosperous and environmentally conscious future.
Expert Guide to 3-Axis CNC Machining: What You Need to Know
{[Company Name] is proud to announce that it has recently invested in state-of-the-art 3 axis CNC machining technology. This investment will allow the company to enhance its manufacturing capabilities and provide more precise and efficient services to its customers.3 axis CNC machining is a cutting-edge technology that enables high-precision manufacturing of various components and parts. The technology utilizes computer numerical control (CNC) to automate the machining process, resulting in superior accuracy and repeatability. This makes it an ideal solution for a wide range of industries, including aerospace, automotive, medical, and more.With the addition of 3 axis CNC machining, [Company Name] will be able to expand its manufacturing capabilities and offer new product lines to its customers. This technology will enable the company to produce complex and intricate components with ease, allowing for greater design flexibility and faster turnaround times.In addition to enhancing its manufacturing capabilities, [Company Name] is also committed to maintaining the highest quality standards. The company takes pride in ensuring that all products meet or exceed industry regulations and customer specifications. With 3 axis CNC machining, [Company Name] will be able to further guarantee the precision and quality of its products, setting a new standard for excellence in the industry.Moreover, [Company Name] has always been dedicated to continuous improvement and technological innovation. By investing in the latest 3 axis CNC machining technology, the company is demonstrating its commitment to staying at the forefront of industry advancements. This will not only benefit the company and its customers, but also contribute to the overall advancement of manufacturing technology.Furthermore, the investment in 3 axis CNC machining technology demonstrates [Company Name]'s dedication to sustainability and efficiency. The technology allows for the optimization of material usage and reduction of waste, contributing to a more environmentally friendly manufacturing process. This aligns with the company's values and commitment to responsible and sustainable business practices.In conclusion, the addition of 3 axis CNC machining technology is a significant milestone for [Company Name]. It represents the company's dedication to providing the highest quality products and services to its customers, as well as its commitment to innovation and sustainability. With this new technology, [Company Name] is poised to elevate its manufacturing capabilities and set new industry standards for precision and efficiency.Stay tuned for more updates as [Company Name] continues to leverage the latest advancements in technology to deliver unparalleled solutions to its customers.About [Company Name]:[Company Name] is a leading manufacturing company that specializes in providing high-quality components and parts to a diverse range of industries. With a focus on precision, quality, and innovation, the company is dedicated to meeting the unique needs of its customers and delivering exceptional products and services. [Company Name] is committed to continuous improvement and invests in cutting-edge technologies to ensure that it remains at the forefront of industry advancements.
How Insert Molding is Revolutionizing Manufacturing Processes
Title: Innovative Insert Molding Technology Revolutionizes Manufacturing ProcessesIntroduction:The manufacturing industry continually seeks advanced technologies to increase efficiency, minimize costs, and enhance product performance. One such revolutionary technique is Insert Molding, which combines the benefits of traditional molding techniques with precision insert placement, resulting in enhanced product performance and streamlined manufacturing processes. One company at the forefront of this innovation is {}. With their extensive experience and expertise in insert molding, they are pushing the boundaries of what is possible in the manufacturing industry.Paragraph 1:Insert Molding is a manufacturing process that involves injecting molten materials, such as plastic or metal, into a pre-formed cavity or mold containing one or more carefully positioned inserts. These inserts can be a wide range of components, including threaded inserts, electrical connectors, sensors, or metal reinforcements. The molten material effectively encapsulates the inserts, creating a strong bond between the two, resulting in a more robust and functional end product.Paragraph 2:Insert Molding offers several advantages over traditional manufacturing methods. Firstly, it eliminates the need for additional assembly processes, reducing labor costs and assembly time. By incorporating various inserts directly into the mold, the manufacturing process becomes more streamlined, efficient, and cost-effective. Furthermore, insert molding ensures precise and accurate positioning of the inserts, leading to higher product integrity and reliability.Paragraph 3:The innovation and expertise of {} in the field of insert molding have allowed them to cater to a diverse range of industries, including automotive, electronics, medical, and consumer goods. Their state-of-the-art facilities and skilled engineers enable them to create complex and high-quality molded products with exceptional precision. {} also offers comprehensive design assistance, ensuring that their customers' unique insert molding requirements are met, resulting in tailored solutions that exceed expectations.Paragraph 4:The automotive industry, in particular, has greatly benefited from the utilization of insert molding. By integrating metal inserts into plastic parts, manufacturers achieve significant weight reduction, increased part functionality, and improved overall vehicle performance. Electrical connectors, sensors, and wiring harnesses are seamlessly integrated, simplifying assembly and enhancing reliability. The implementation of insert molding enables automotive manufacturers to produce parts that meet the stringent safety and quality standards of the industry.Paragraph 5:In the ever-evolving electronics industry, where miniaturization and increased functionality are essential, insert molding plays a crucial role. With the ability to place delicate components, such as microchips, sensors, and connectors, with utmost precision, manufacturers can produce smaller and slimmer electronic devices without sacrificing performance. This technique also enhances the devices' durability by protecting fragile components and reducing the risk of damage caused by external factors.Paragraph 6:In the medical industry, insert molding offers numerous benefits in terms of product design, functionality, and sterilization. The ability to encapsulate electronics, sensors, and metal components within a single molded part ensures a seamless integration of various functionalities, such as drug delivery systems, diagnostic equipment, and surgical devices. The use of insert molding in the medical field has resulted in advancements in patient care and treatment efficiency.Conclusion:With its ability to combine diverse materials and precisely position inserts, Insert Molding has revolutionized the manufacturing industry by enhancing product performance, reducing costs, and streamlining production processes. The expertise and cutting-edge solutions provided by {} have solidified their place as industry leaders in insert molding technology. As new advancements continue to be made, the possibilities and applications of Insert Molding are boundless, driving innovation throughout various sectors and shaping the future of manufacturing.
Exploring the Benefits and Applications of Cnc Molding in Modern Manufacturing Processes
Title: Revolutionary Cnc Molding Technique Sets New Standards in ManufacturingIntroduction:In an era where innovation and efficiency drive the manufacturing industry, a breakthrough in the form of Cnc Molding technology is emerging as a game-changer. This revolutionary technique promises to reshape the way products are designed, developed, and produced. With its unparalleled precision, speed, and cost-effectiveness, Cnc Molding is poised to set new standards in the manufacturing field.Company Background and Expertise:{Company Name}, a prominent player in the manufacturing industry, has unveiled its cutting-edge Cnc Molding technology. With a rich history spanning several decades, {Company Name} has established itself as a pioneer in delivering excellence and embracing the latest technological advancements. Their expertise in the field, combined with their commitment to driving innovation, has paved the way for this groundbreaking development.Understanding Cnc Molding:Cnc Molding, also known as Computer Numerical Control Molding, is a state-of-the-art manufacturing process that utilizes computer-controlled machines to shape materials into desired forms. Unlike traditional molding techniques, Cnc Molding ensures unparalleled precision, efficiency, and repeatability. By following a digital design prototype, the technology enables manufacturers to produce highly intricate and complex components with utmost accuracy.Benefits of Cnc Molding:1. Enhanced Precision: The integration of computer control systems eliminates the possibility of human error, ensuring precise replication of designs and eliminating defects. This high level of precision ensures product consistency, reducing wastage and overall costs.2. Streamlined Production: Cnc Molding technology dramatically accelerates the production process. With its ability to perform multiple tasks simultaneously, the technology maximizes efficiency and reduces lead times. This streamlining of operations increases productivity, enabling manufacturers to meet market demands promptly.3. Cost-Effectiveness: By minimizing material wastage and requiring fewer human interventions, Cnc Molding significantly reduces production costs. The elimination of manual labor and the use of optimized resources result in improved cost-effectiveness, making it an attractive option for manufacturers across various industries.4. Design Freedom: Cnc Molding empowers designers to create innovative and intricate designs that were previously unachievable. With the ability to produce complex shapes and patterns with ease, this technology unlocks a new realm of possibilities, enabling manufacturers to create unique products that stand out in the market.Applications of Cnc Molding:The applications of Cnc Molding are vast and span across industries such as automotive, aerospace, electronics, medical, and consumer goods. Its usage is particularly prominent in the production of custom parts, prototypes, and intricate components that require high precision.Future Implications:As Cnc Molding continues to evolve, the implications for the manufacturing industry are immense. The integration of artificial intelligence, machine learning, and digital twins creates an even more robust system capable of even greater efficiency and accuracy. The technology's potential for customization and adaptability positions it as a frontrunner in the future of manufacturing.Conclusion:Cnc Molding technology, introduced by {Company Name}, is set to revolutionize the manufacturing industry. With its exceptional precision, streamlined production, cost-effectiveness, and design freedom, it promises to set new standards and transform the way products are made. As it continues to develop, this groundbreaking technology is poised to usher in a new era of manufacturing excellence.
Ultimate Guide to CNC Mechanical Engineering: Unveiling the Secrets of This Revolutionary Field
Title: Revolutionizing CNC Mechanical Engineering: A Glimpse into Cutting-Edge InnovationsIntroduction:In today's fast-paced world of technology and automation, the field of CNC (Computer Numerical Control) Mechanical Engineering continues to push boundaries. With industry demands constantly evolving, companies like {} are leading the way in developing cutting-edge solutions that transform manufacturing processes. This article delves into the world of CNC Mechanical Engineering, shedding light on the vital role it plays and highlighting the innovative contributions made by {}.1. Understanding CNC Mechanical Engineering:CNC Mechanical Engineering involves the design, development, and operation of computer-controlled machinery utilized in manufacturing. These systems employ pre-programmed instructions to dictate the movement of cutting tools, thereby automating the fabrication process. By harnessing a combination of hardware and intelligent software integration, CNC machines offer exceptional precision, efficiency, and repeatability, revolutionizing industrial production.2. Pioneering Innovations by {}:{} is a renowned industry player at the forefront of CNC Mechanical Engineering advancements. With a focus on developing state-of-the-art machinery, they have consistently delivered remarkable manufacturing solutions. By embracing emerging technologies and evolving market needs, {} has demonstrated their commitment to ensuring superior performance and productivity in every aspect of their products.3. Intelligent Automation for Enhanced Efficiency:{} has successfully integrated advanced automation into their CNC machining solutions. Through the implementation of Artificial Intelligence (AI) and Machine Learning (ML) algorithms, their machines can analyze and optimize manufacturing processes in real-time. This results in enhanced efficiency, reduced material wastage, and superior quality control. The intelligent automation offered by {} is a game-changer in the field, streamlining operations for manufacturers worldwide.4. Sustainable Manufacturing Practices:In an era where sustainability is paramount, {} has pioneered eco-conscious manufacturing technologies within the CNC Mechanical Engineering domain. By incorporating energy-efficient components, optimizing material usage, and reducing waste generation, their machines contribute to a greener manufacturing ecosystem. {}'s commitment to sustainability underscores their dedication to responsible business practices and a more sustainable future.5. Industry 4.0 Integration:Remaining at the forefront of industry trends, {} has embraced the concept of Industry 4.0, the fourth industrial revolution. By interconnecting CNC machines, data analysis systems, and intelligent software, they have created a fully digitalized and interconnected manufacturing environment. This seamless integration enables real-time data sharing, predictive maintenance, and remote accessibility, revolutionizing traditional production processes.6. Disruptive Additive Manufacturing Solutions:In addition to traditional subtractive manufacturing techniques, {} has ventured into additive manufacturing, commonly known as 3D printing. The company's additive manufacturing solutions offer unparalleled design flexibility, reduced material waste, and faster prototyping capabilities. {}'s foray into the realm of 3D printing exemplifies their commitment to pushing boundaries and exploring new frontiers in CNC Mechanical Engineering.7. Global Impact and Collaborations:{}'s innovative solutions have made a significant impact on the global manufacturing landscape. By collaborating with industry partners, research institutions, and universities, they strive to foster a culture of knowledge exchange and collective growth. These collaborative efforts have not only contributed to breakthroughs in CNC Mechanical Engineering but have also propelled the industry as a whole towards greater heights.Conclusion:In the ever-evolving world of CNC Mechanical Engineering, {} stands as a beacon of innovation and excellence. Their relentless pursuit of cutting-edge solutions has revolutionized manufacturing processes, introducing intelligent automation, sustainable practices, and additive manufacturing techniques. By embracing Industry 4.0 and collaborating with stakeholders worldwide, {} continues to shape the future of CNC Mechanical Engineering, driving industry advancements and inspiring manufacturers to embark on a path of transformation.
Designing Molds for Injection Molding: A Guide for Efficient Production
Mold Design For Injection Molding – Innovating for the FutureInjection molding is a manufacturing process used to produce parts by injecting material into a mold. This process requires a high level of precision and expertise, particularly in mold design. One company that is leading the way in innovative mold design for injection molding is [Company Name].[Company Name] is a global leader in the injection molding industry, with a strong reputation for producing high-quality molds and parts for a wide range of industries. With over [number] years of experience, the company has developed a deep understanding of the injection molding process and has continually pushed the boundaries of mold design to meet the evolving needs of its customers.The company's dedication to innovation and quality has led to the development of cutting-edge mold designs that optimize the injection molding process. These designs not only improve the efficiency of production but also enhance the overall quality and precision of the molded parts.One of the key factors that set [Company Name] apart is its focus on custom mold design. The company works closely with its clients to understand their specific requirements and then develops tailored mold designs to meet those needs. This personalized approach ensures that each mold is optimized for the specific material, part geometry, and production volume, resulting in the highest quality finished products.In addition to custom mold design, [Company Name] also offers a range of standardized mold designs that have been proven to deliver exceptional results. These designs have been meticulously developed and tested to ensure consistent and reliable performance, making them an ideal solution for a wide range of injection molding applications.Furthermore, [Company Name] utilizes state-of-the-art technology and advanced engineering techniques in the mold design process. The company's team of experienced engineers and designers utilize the latest software and simulation tools to optimize mold designs for maximum performance and efficiency, ultimately reducing production time and costs for their customers.By staying at the forefront of mold design innovation, [Company Name] has been able to meet the ever-increasing demands of the injection molding industry. With a commitment to quality, precision, and customer satisfaction, the company continues to drive forward in developing new and improved mold designs that provide optimal results for its clients.One of the biggest challenges in mold design for injection molding is achieving the precise balance between part design and mold flow analysis. To address this challenge, [Company Name] has developed a unique approach that involves thorough analysis of the part design and material behavior, leading to the development of molds that produce consistent and high-quality parts.Moreover, [Company Name] has a strong focus on sustainability and environmental responsibility in its mold design processes. The company actively explores ways to minimize material waste and energy consumption in its mold designs, ultimately reducing the environmental impact of injection molding production.In conclusion, [Company Name] is a leading force in innovative mold design for injection molding, with a strong commitment to meeting the unique needs of its customers. Through custom and standardized mold designs, advanced engineering techniques, and a focus on sustainability, the company continues to drive forward in the development of cutting-edge solutions that deliver exceptional results in the injection molding industry. With a track record of excellence and a dedication to continuous improvement, [Company Name] is poised to remain a key player in the future of mold design for injection molding.
High-Quality Machining Parts for Optimal Performance
Title: Industry-Leading Company Paving the Way in Precision Brass Machining PartsIntroduction:In today's rapidly evolving industrial landscape, the demand for high-quality and precision machined parts continues to rise. With this in mind, one company stands tall as a leader in the industry, offering unparalleled expertise and innovation in brass machining parts. With a commitment to delivering exceptional products and dedicating themselves to customer satisfaction, this industry giant has become a go-to source for clients looking to meet their brass machining needs.[Company Name], a globally renowned manufacturer and supplier of brass machining parts, has carved a niche for itself through its dedication to excellence. With cutting-edge facilities, state-of-the-art technology, and a team of highly skilled professionals, the company has the capabilities to produce intricate and sophisticated brass components that meet the highest standards of quality.Offering a wide range of brass machining parts, [Company Name] has become a trusted partner for industries ranging from automotive and aerospace to medical and electronics. The expertise of their engineering team allows them to cater to the unique specifications and requirements of each client, ensuring precise solutions that enhance the efficiency and effectiveness of their operations.Industry-Leading Capabilities:With an unwavering commitment to technological advancements, [Company Name] has continuously invested in state-of-the-art machinery and equipment. This extensive assortment of high-precision CNC machines empowers the company to undertake complex machining projects with ease, delivering exceptional results time and again.To further enhance their capabilities, [Company Name] has established a stringent quality control system. Every brass machining part undergoes rigorous inspection and testing at various stages of the production process, guaranteeing products that exceed industry standards. By adhering to these strict quality control protocols, the company ensures the durability, precision, and reliability of every single part that they deliver.Innovation and Customization:Understanding that industries thrive on innovation, [Company Name] constantly seeks opportunities to push the boundaries of brass machining. The company's research and development team is at the forefront of exploring new materials, techniques, and processes that can enhance the functionality and performance of their brass parts.Moreover, [Company Name] places great emphasis on customization, recognizing that each client may have unique requirements. By working closely with their customers, the company tailors their brass machining parts to exact specifications, providing bespoke solutions that perfectly align with individual needs. This personalized approach enables them to create components that seamlessly integrate into clients' assembly lines, resulting in optimized productivity and seamless operations.Global Reach and Sustainable Practices:With a global footprint, [Company Name] has successfully established a strong presence in various markets around the world. By catering to the needs of diverse industries, they have built trust and credibility as a reliable partner in the field of brass machining parts manufacturing.Furthermore, [Company Name] places great importance on sustainability and environmental responsibility. In their manufacturing processes, they prioritize the use of eco-friendly materials and adhere to stringent waste management practices. By ensuring that their operations have minimal impact on the environment, they set an example for the industry and contribute towards a greener future.Conclusion:As the demand for precision brass machining parts intensifies, [Company Name] continues to lead the industry with its unwavering dedication to quality, innovation, and customer satisfaction. With a globally recognized presence, cutting-edge technology, and a commitment to sustainability, they remain steadfast in delivering the highest-quality brass machining parts that meet the evolving needs of industries around the world.
A Beginner's Guide to CNC: Understanding the Basics and Benefits
Introduction to CNC TechnologyCNC stands for Computer Numerical Control, which is a technology that has revolutionized the manufacturing industry. It involves the use of computers to control machine tools and equipment, resulting in highly accurate and precise production processes. This technology has been widely adopted by industries such as automotive, aerospace, and electronics, where precision and efficiency are of utmost importance.CNC technology has significantly improved the manufacturing process by automating tasks that were previously done manually. This has not only increased the speed and efficiency of production but has also improved the quality and consistency of the finished products. In addition, CNC machines are capable of producing complex and intricate designs that would be impossible to create using traditional methods.With the increasing demand for precision engineering and high-quality manufacturing, the importance of CNC technology has continued to grow. Many companies have invested in CNC machines to stay competitive in the market and meet the ever-evolving needs of their customers.[Company Name] is one such company that has embraced CNC technology to enhance its manufacturing capabilities. With a dedicated team of engineers and technicians, [Company Name] has fully integrated CNC machines into its production process, allowing for the efficient and cost-effective production of a wide range of precision components and parts.Using state-of-the-art CNC machines, [Company Name] is able to offer its customers high-quality products with unparalleled accuracy and precision. The technology has allowed for a significant reduction in production lead times and an increase in overall productivity, enabling [Company Name] to better serve its customers and meet their delivery requirements.The investment in CNC technology has also allowed [Company Name] to expand its capabilities and take on more complex and challenging projects. With the ability to handle intricate designs and tight tolerances, [Company Name] has positioned itself as a leading provider of precision-engineered components in the industry.The utilization of CNC technology has not only benefited [Company Name]'s production processes but has also led to a reduction in waste and improved overall efficiency. The technology allows for the optimization of material usage and the minimization of errors, resulting in cost savings and a more environmentally sustainable approach to manufacturing.As the manufacturing industry continues to evolve, CNC technology will play an integral role in shaping the future of production. With its ability to deliver high-quality, precise, and efficient manufacturing processes, CNC technology is set to remain a cornerstone of modern manufacturing.In conclusion, CNC technology has revolutionized the manufacturing industry, and companies that embrace this technology are able to deliver high-quality products with unparalleled accuracy and consistency. [Company Name] has fully integrated CNC technology into its production process, allowing it to offer its customers a wide range of precision components and parts with exceptional quality and efficiency. With the continuous advancements in CNC technology, the future of manufacturing looks promising, and companies that invest in this technology will undoubtedly stay ahead of the competition.
High-Quality Aerospace CNC Machining Services for Precision Parts
Aerospace CNC Machining Company (ACM) has recently announced its expansion plans with the introduction of new state-of-the-art machining processes and capabilities. The company, known for its high-quality precision components for the aerospace industry, has been a leading supplier for several major aerospace firms.With a growing demand for more complex and advanced aerospace components, ACM has recognized the need to invest in cutting-edge CNC machining technology to meet the evolving needs of the industry. The company has therefore made significant investments in new machinery and equipment, along with the implementation of advanced machining processes to enhance its capabilities.The expansion of ACM's CNC machining capabilities is a strategic move to position the company as a leading provider of precision aerospace components. The new machinery and processes will allow ACM to produce components with tighter tolerances and more intricate geometries, meeting the high standards and requirements of the aerospace industry.One of the key advantages of the new CNC machining capabilities is the ability to produce complex and high-precision components with faster turnaround times. This will enable ACM to better meet the increasing demands of its customers and to stay ahead of the competition in the aerospace industry.In addition to the new machinery and advanced machining processes, ACM has also invested in training and development programs for its team of engineers and technicians. This will ensure that the company's workforce is equipped with the necessary skills and expertise to operate the new CNC machinery and to consistently deliver high-quality components to its customers.The expansion of ACM's CNC machining capabilities is a testament to the company's commitment to staying at the forefront of technological advancements in the aerospace industry. By embracing the latest machining technology and processes, ACM is well-positioned to continue providing its customers with innovative and high-quality aerospace components.The president of ACM, John Smith, expressed his excitement about the company's expansion plans and the potential for growth in the aerospace industry. "We are continuously looking for ways to improve our capabilities and better serve our customers," said Smith. "The investment in new CNC machining technology is a testament to our dedication to providing the highest quality components to the aerospace industry."The expansion of ACM's CNC machining capabilities has already garnered positive attention from its existing customer base, as well as from potential new clients in the aerospace sector. With the new machinery and advanced processes in place, the company is well-positioned to take on larger and more complex projects, further solidifying its reputation as a leading provider of precision aerospace components.In conclusion, the expansion of ACM's CNC machining capabilities marks an exciting milestone for the company and the aerospace industry as a whole. With the new machinery and advanced processes in place, ACM is poised to meet the increasing demands and evolving needs of the aerospace industry, while continuing to deliver high-quality precision components to its customers.