Guide to Thermoplastic Injection Molding: Benefits and Applications
By:Admin
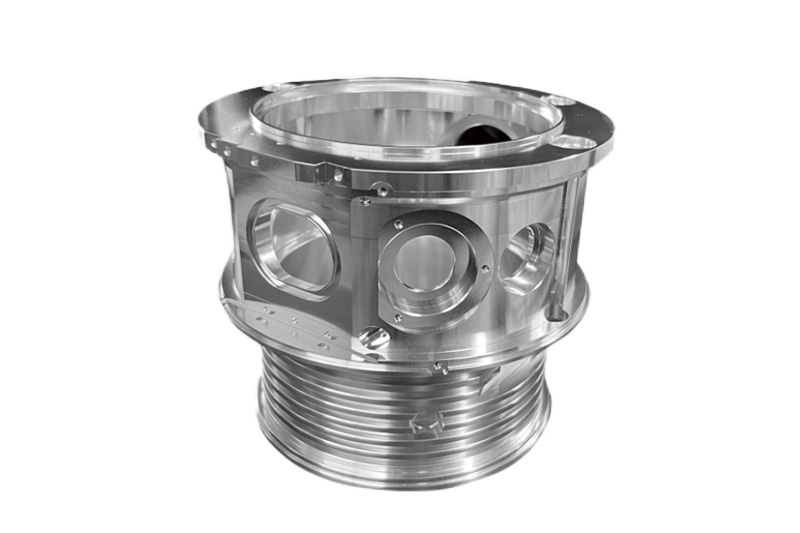
Thermoplastic injection molding is a manufacturing process in which plastic material is melted and injected into a mold at high pressure to create a wide range of products. This process is widely used in the production of consumer goods, automotive parts, medical devices, and more.
With a focus on precision and efficiency, [Company Name] has developed a reputation for delivering top-notch injection-molded products that meet the highest industry standards. The company's state-of-the-art facilities and advanced manufacturing processes allow them to produce complex and intricate parts with exceptional accuracy and consistency.
In addition to its cutting-edge manufacturing capabilities, [Company Name] also offers a comprehensive suite of services, including design assistance, prototyping, and tooling, to help its customers bring their concepts to life. The company's team of experienced engineers and designers work closely with clients to understand their specific needs and provide tailored solutions that align with their requirements and budget.
Furthermore, [Company Name] is committed to sustainability and environmentally-friendly practices. The company has invested in eco-friendly materials and processes to minimize its carbon footprint and reduce waste. By optimizing production efficiency and recycling scrap materials, [Company Name] is dedicated to promoting a greener and more sustainable manufacturing industry.
Recently, [Company Name] has expanded its capabilities in thermoplastic injection molding to meet the growing demand for custom-designed components across various industries. The company has invested in new technologies and equipment to enhance its production capacity and streamline its manufacturing processes. This investment has allowed [Company Name] to offer faster turnaround times and greater flexibility to its customers, while maintaining the highest quality standards.
One of the key factors driving [Company Name]'s success in thermoplastic injection molding is its unwavering commitment to innovation and continuous improvement. The company actively embraces new technologies and techniques to stay ahead of the curve and remain at the forefront of the industry. By staying abreast of the latest advancements in materials and manufacturing methods, [Company Name] is able to deliver cutting-edge solutions that meet the evolving needs of its clientele.
In addition to its technical prowess, [Company Name] takes great pride in its customer-centric approach. The company places a strong emphasis on building long-term partnerships with its clients, offering unparalleled support and guidance throughout every stage of the project. From initial concept development to final product delivery, [Company Name] ensures that its customers receive the attention and expertise they deserve, resulting in successful collaborations and satisfied outcomes.
Looking ahead, [Company Name] aims to further expand its footprint in the thermoplastic injection molding market and continue pushing the boundaries of what is achievable in the industry. With a relentless pursuit of excellence and a dedication to customer satisfaction, [Company Name] is poised to remain a driving force in the field of injection molding for years to come.
In conclusion, [Company Name] stands as a proven leader in thermoplastic injection molding, delivering exceptional products and services to a diverse range of industries. With a focus on innovation, sustainability, and customer satisfaction, the company has cemented its position as a trusted partner for businesses seeking top-tier injection-molded solutions. As [Company Name] continues to evolve and expand its capabilities, it is well-positioned to remain a powerhouse in the industry and a go-to provider for custom injection-molded products.
Company News & Blog
Expert insights on medical injection molding and its applications in the healthcare industry
Medical Injection Molding, a leading provider of precision injection molding solutions for the medical industry, has been making waves in the field of medical device manufacturing. With a strong focus on quality, precision, and innovation, Medical Injection Molding has established itself as a trusted partner for medical device companies around the world.With state-of-the-art facilities and a team of experienced engineers and technicians, Medical Injection Molding is able to provide a wide range of services, including tooling design, material selection, prototyping, and high-volume production. The company’s expertise in medical injection molding allows them to produce complex and intricate parts with tight tolerances, ensuring that the final products meet the rigorous standards of the medical industry.One of the key strengths of Medical Injection Molding is its ability to work closely with customers to develop custom solutions that meet their specific needs. The company’s team of engineers and designers are able to provide guidance and support throughout the entire product development process, from initial concept to final production. This collaborative approach has helped Medical Injection Molding to build strong and lasting relationships with its customers, many of whom rely on the company for the production of critical medical devices.In addition to its expertise in medical injection molding, the company also places a strong emphasis on quality and compliance. Medical Injection Molding is ISO 13485 certified, demonstrating its commitment to the highest standards of quality management for medical device manufacturing. The company also follows strict guidelines for cleanliness and contamination control in its facilities, ensuring that the products it manufactures are safe and reliable for use in medical applications.Medical Injection Molding’s commitment to quality and compliance has helped the company to gain the trust and confidence of its customers, who rely on its expertise to deliver high-quality, precision-molded components for a wide range of medical devices. From surgical instruments to diagnostic equipment to implantable devices, Medical Injection Molding is able to meet the unique needs of each customer with its advanced manufacturing capabilities and unwavering dedication to quality.With a focus on continuous improvement and innovation, Medical Injection Molding is constantly investing in new technology and production methods to stay at the forefront of the medical device manufacturing industry. The company’s dedication to staying ahead of the curve has enabled it to consistently deliver cutting-edge solutions that help its customers to bring new and innovative medical devices to market.As the demand for high-quality medical devices continues to grow, Medical Injection Molding is well positioned to meet the needs of the medical industry with its advanced capabilities, unwavering commitment to quality, and dedication to customer satisfaction. With a strong track record of success and a proven ability to deliver results, Medical Injection Molding is poised to remain a leader in the field of medical device manufacturing for years to come.In conclusion, Medical Injection Molding’s expertise in precision injection molding for the medical industry, combined with its dedication to quality, compliance, and innovation, has solidified its position as a trusted partner for medical device companies around the world. With a focus on delivering custom solutions that meet the unique needs of its customers, the company is well positioned to continue leading the way in the field of medical device manufacturing.
Understanding the Process of CNC Milling: A Guide
In the ever-evolving world of manufacturing and machining, CNC milling has become an essential process for creating precision parts and components. This advanced technology allows for the production of complex and intricate designs with unparalleled accuracy and efficiency. With the integration of innovative CNC milling technology, {Company Name} has established itself as a leader in the field of precision machining and manufacturing.{Company Name} specializes in providing high-quality CNC milling services for a wide range of industries, including aerospace, automotive, medical, and more. With a team of highly skilled engineers and machinists, the company has the capability to meet the most demanding requirements for precision and quality. By utilizing state-of-the-art CNC milling machines, {Company Name} is able to produce parts with tight tolerances and intricate geometries, ensuring that their customers receive top-notch products that meet their exact specifications.One of the key advantages of CNC milling is its ability to produce complex parts with a high degree of accuracy. This is achieved through the use of computer-aided design (CAD) software, which allows for the creation of detailed 3D models that can be translated directly to the CNC milling machine. This eliminates the need for manual intervention and reduces the margin of error, resulting in parts that are consistently precise and uniform.In addition to precision, CNC milling also offers unparalleled efficiency in the production process. With the ability to program the machining operations directly into the CNC milling machine, {Company Name} can streamline the manufacturing process and reduce lead times, ultimately delivering cost-effective solutions to their customers. This level of efficiency also allows for quick turnaround times on prototype and production runs, giving customers the flexibility to meet tight deadlines and adapt to changing market demands.Furthermore, CNC milling technology enables {Company Name} to work with a wide range of materials, including metals, plastics, and composites. This versatility allows them to cater to the diverse needs of their customers, whether it's producing lightweight components for the aerospace industry or durable parts for the automotive sector. With a comprehensive understanding of various materials and their machining properties, {Company Name} can ensure that their products meet the highest standards of quality and performance.Beyond its technical capabilities, {Company Name} takes pride in its commitment to customer satisfaction and continuous improvement. Their team of experienced engineers works closely with customers to understand their specific requirements and provide tailored solutions that meet their unique needs. This collaborative approach, combined with a dedication to continuous innovation, positions {Company Name} as a trusted partner in the industry, capable of delivering exceptional results time and time again.Looking ahead, {Company Name} is poised to continue leveraging the latest advancements in CNC milling technology to push the boundaries of what is possible in precision machining. With a focus on quality, efficiency, and customer-centric solutions, they are well-equipped to meet the evolving needs of the manufacturing industry and provide innovative solutions for a wide range of applications.As the demand for high-quality, precision parts continues to grow across various industries, companies like {Company Name} will play a crucial role in shaping the future of manufacturing. Through their expertise in CNC milling and dedication to excellence, they are positioned to make a lasting impact and contribute to the advancement of manufacturing technology.
High-Quality CNC Machining Prototyping Services for Rapid Product Development
CNC Machining Prototyping Technology Revolutionizes Manufacturing IndustryIn the modern manufacturing industry, precision and efficiency are crucial elements for success. With the advancement of technology, CNC machining prototyping has become an indispensable tool in the production of high-quality, custom-made parts and products. This cutting-edge technology has revolutionized the way companies approach prototyping and production, allowing them to create intricate and complex designs with unmatched precision and speed.With the ability to produce parts with incredibly tight tolerances and intricate geometries, CNC machining prototyping has become the go-to solution for companies looking to develop prototypes quickly and accurately. Unlike traditional prototyping methods, such as manual machining or 3D printing, CNC machining prototyping offers unparalleled precision, consistency, and repeatability. This has made it a popular choice for industries such as aerospace, automotive, medical, and electronics, where quality and precision are of utmost importance.One company leading the way in CNC machining prototyping is {}. With decades of experience in the manufacturing industry, they have established themselves as a trusted provider of high-quality CNC machining services. Their state-of-the-art facility is equipped with the latest CNC machines, allowing them to produce complex parts with unmatched precision and efficiency.Using advanced CAD/CAM software, their team of expert engineers can program intricate designs and use their CNC machines to produce prototypes with incredible accuracy. This combination of cutting-edge technology and skilled craftsmanship has enabled {} to deliver top-quality prototypes to their clients, helping them bring their ideas to life with ease.With the ability to work with a wide range of materials, including metals, plastics, and composites, CNC machining prototyping has enabled companies to explore new possibilities and push the boundaries of design and innovation. Whether it's developing a new medical device, creating a prototype for a cutting-edge automotive component, or crafting a custom piece for the aerospace industry, CNC machining prototyping has proven to be a versatile and reliable solution for companies of all sizes.Furthermore, the speed and efficiency of CNC machining prototyping have allowed companies to accelerate their product development timelines, bringing their ideas to market faster than ever before. By quickly iterating and refining prototypes, companies can reduce the time and cost associated with traditional prototyping methods, ultimately giving them a competitive edge in the market.In addition to its impact on prototyping, CNC machining technology has also revolutionized the production of end-use parts. With its ability to produce high-quality, custom-made components, CNC machining has become a preferred method for manufacturing final products in a wide range of industries. This has eliminated the need for expensive tooling and long lead times associated with traditional manufacturing methods, making it a cost-effective and efficient solution for companies looking to bring their products to market quickly.As the manufacturing industry continues to evolve, CNC machining prototyping will undoubtedly play a crucial role in driving innovation and fostering the development of groundbreaking products. With its unparalleled precision, speed, and efficiency, CNC machining prototyping has become a game-changer for companies seeking to push the boundaries of design and engineering.In conclusion, CNC machining prototyping has revolutionized the manufacturing industry, providing companies with the tools and capabilities to develop high-quality prototypes and end-use parts with unmatched precision and efficiency. As technology continues to advance, the impact of CNC machining prototyping will only grow, opening up new possibilities and opportunities for companies looking to innovate and thrive in the modern market.
Custom CNC Machining Services for Brass Parts: Top Benefits and Uses
CNC Machining Brass - A New Milestone for CompanyIn the ever-evolving world of manufacturing, precision and efficiency are non-negotiable. Companies are consistently seeking newer and better ways to create high-quality products and meet the demands of their customers. One company that has embraced this challenge head-on is {}. {} has been a leader in the manufacturing industry for decades, known for its dedication to innovation and cutting-edge technology. Recently, the company achieved a new milestone with the implementation of CNC machining for brass components.CNC machining, or computer numerical control machining, is a manufacturing process that utilizes computerized controls and machine tools to remove material from a workpiece. This process allows for extremely precise and intricate cuts, resulting in high-quality, custom parts. While CNC machining is not a new technology, the application of this method to brass components is a significant advancement for {} and a testament to their commitment to excellence.Brass is a popular material in the manufacturing industry due to its excellent properties, including high corrosion resistance, electrical conductivity, and aesthetic appeal. However, machining brass can be challenging due to its tendency to produce chips that can cause tool wear and damage. With the implementation of CNC machining, {} has overcome these challenges and elevated their production capabilities to a new level.The decision to incorporate CNC machining for brass components was not taken lightly. According to the company's engineering team, extensive research and testing were conducted to ensure the successful integration of this advanced manufacturing process. Through meticulous planning and collaboration with industry experts, {} was able to optimize the CNC machining process for brass, resulting in superior quality and consistency in their products.The benefits of CNC machining for brass components are manifold. Not only does it enable {} to produce intricate and complex parts with unparalleled precision, but it also enhances efficiency and reduces lead times. Additionally, the use of CNC machining for brass has positioned {} to take on new and challenging projects, further solidifying their reputation as a leader in the industry.Furthermore, the implementation of CNC machining for brass components aligns with {}'s commitment to sustainability. By utilizing advanced manufacturing processes that minimize material waste and energy consumption, the company is taking proactive steps towards reducing its environmental impact and meeting the growing demand for sustainable production methods.The impact of this milestone goes beyond the walls of {}. With the introduction of CNC machining for brass components, the company is poised to offer its clients a wider range of products and solutions, catering to diverse industries such as automotive, aerospace, electronics, and more. This expansion of capabilities has the potential to open new doors and foster long-lasting partnerships with customers who require top-notch brass components for their applications.As {} continues to push the boundaries of innovation, the incorporation of CNC machining for brass components stands as a testament to their unwavering dedication to excellence and customer satisfaction. With this new milestone, the company is not only raising the bar for the manufacturing industry but is also solidifying its position as a trailblazer in the field.In conclusion, the implementation of CNC machining for brass components at {} represents a significant leap forward in their pursuit of manufacturing excellence. This integration not only enhances their production capabilities but also underscores their commitment to embracing advanced technology and providing superior solutions to their clients. As the manufacturing landscape continues to evolve, {} has proven once again that they are at the forefront of innovation, setting a new standard for precision and quality in the industry.
Exploring the Limitations of Sand Casting: Factors Hindering the Process
Title: Exploring Sand Casting Disadvantages in the Manufacturing IndustryIntroduction:In the realm of manufacturing, sand casting has long been a traditional and widely-used technique for creating intricate and durable metal components. Many companies, including {}, have successfully employed sand casting in their production processes. However, it is important to be aware of the disadvantages associated with this method in order to make informed decisions in the manufacturing industry.Sand Casting and its Application:Before delving into the drawbacks, it is crucial to understand the fundamentals of sand casting. The process involves pouring molten metal into a sand mold to create a desired shape. This method offers flexibility, affordability, and the ability to produce intricate components with various alloys. Sand casting is widely used in industries like automotive, aerospace, and construction, where complex parts are required.Disadvantage 1: Limited Surface Finish and Precision:One of the major shortcomings of sand casting is the limitation it presents in achieving high surface finish and precision. The texture of the sand mold often transfers inconsistencies onto the final product, resulting in a rougher surface finish. Moreover, the molding process may introduce slight variations in dimensions, making it challenging to achieve precise measurements and tight tolerances. These factors can be critical in industries where the aesthetics and precision of components are paramount, such as consumer electronics and medical devices.Disadvantage 2: Time and Labor Intensive:Sand casting is a time and labor-intensive process, which can significantly impact the overall production timeline and costs. Preparing the molds, including pattern creation, gating system design, and mold assembly, requires skilled labor and careful execution. Additionally, molten metal must be cooled and solidified in the mold, followed by the removal of excess sand and finishing operations. Addressing these steps can be time-consuming, leading to longer lead times and reduced efficiency, especially for industries characterized by high-volume production demands.Disadvantage 3: Limited Complexity and Assembly Integration:While sand casting is suitable for various complex shapes, it has limitations in terms of intricate designs and integration with assembly components. The mold's internal cavities can be challenging to achieve with precision, prohibiting the creation of intricate features. Furthermore, sand casting may not be ideal for components requiring internal passageways, such as cooling channels, as the removal of the sand mold can be difficult and may compromise the final product's integrity. For industries that heavily rely on intricate designs and integration, such as semiconductor manufacturing or advanced machinery, alternative production methods like precision machining may be preferred.Disadvantage 4: Material Waste and Environmental Concerns:Sand casting generates a significant amount of waste material. After each casting, sand molds become unusable and are discarded, contributing to environmental concerns. Additionally, the process can consume large quantities of sand, leading to mining activities and the depletion of natural resources. Companies like {} have been actively working towards sustainable solutions by implementing recycling processes and exploring environmentally-friendly alternatives to sand molds, such as 3D-printed molds or investment casting.Conclusion:Sand casting undeniably plays a crucial role in the manufacturing industry, with its affordability and flexibility making it an attractive choice for many companies, including {}. However, it is essential to be aware of its disadvantages, which include limited surface finish and precision, time and labor intensiveness, limited complexity and integration, and environmental concerns. By understanding these drawbacks, manufacturers can make more informed decisions when choosing their production methods, potentially optimizing their processes and meeting the demands of their respective industries while considering sustainability needs.
High-Quality Precision Injection Molding for Your Manufacturing Needs
Precision Injection Molding is a highly specialized manufacturing process that is utilized in a wide range of industries to create plastic components with exceptional accuracy and repeatability. This advanced technology enables manufacturers to produce complex and intricate parts that meet the highest quality standards, making it an essential tool for businesses looking to stay competitive in today's fast-paced market.As an industry leader in precision injection molding, [company name] has established itself as a go-to supplier for companies seeking high-quality plastic components. With a state-of-the-art facility and a team of highly skilled engineers and technicians, [company name] is able to deliver custom solutions for a wide variety of applications, ranging from automotive and aerospace to medical and consumer goods.The company's commitment to quality and precision is evident in every aspect of its operation, from the design and engineering process to the final production of parts. Using the latest in injection molding technology, [company name] is able to achieve tight tolerances and superior surface finishes, ensuring that each component meets the exact specifications of its customers.In addition to its cutting-edge manufacturing capabilities, [company name] also offers a range of value-added services to its clients. These include design assistance, material selection, and rapid prototyping, allowing customers to bring their concepts to life in a cost-effective and efficient manner. With a strong focus on innovation and continuous improvement, [company name] is dedicated to providing its customers with the best possible solutions for their plastic injection molding needs.One of the key advantages of partnering with [company name] is its ability to handle complex projects with ease. Whether it's a small-scale production run or a large-scale manufacturing operation, the company has the expertise and infrastructure to meet the demands of its customers. By utilizing advanced mold flow analysis and process optimization techniques, [company name] is able to maximize efficiency and minimize waste, ultimately driving down costs for its clients.Furthermore, [company name] places a strong emphasis on quality control and assurance. Its ISO 9001-certified facility is equipped with the latest inspection equipment and testing procedures, ensuring that each component meets the highest standards for performance and reliability. This commitment to quality has earned [company name] a reputation for excellence in the industry, making it a trusted partner for businesses seeking top-tier injection molding solutions.In today's rapidly evolving marketplace, precision injection molding is more important than ever for manufacturers looking to gain a competitive edge. With its unwavering dedication to quality, innovation, and customer satisfaction, [company name] is poised to remain at the forefront of the industry for years to come. Whether it's a small-scale prototype or a high-volume production run, the company has the expertise and resources to deliver outstanding results for its clients.In conclusion, [company name] is a leading provider of precision injection molding services, offering a comprehensive range of capabilities to meet the diverse needs of its customers. With a focus on quality, efficiency, and innovation, the company is well-positioned to continue its success in the dynamic world of plastic manufacturing. For businesses seeking a reliable and experienced partner for their injection molding needs, [company name] is the ideal choice.
How to Build Your Own CNC Router at Home
[Company Introduction]: {Company Name} is a leading manufacturer of advanced CNC machinery, including routers, plasma cutters, and laser cutters. With years of experience in the industry, we have gained a reputation for delivering high-quality and reliable machinery to meet the needs of our diverse customer base. Our commitment to innovation and customer satisfaction has set us apart as a trusted provider of CNC solutions.[News Content]:In line with our dedication to delivering cutting-edge CNC machinery, {Company Name} is excited to announce the launch of our latest product, the {CNC Router Model}. This new addition to our product line is set to revolutionize the world of woodworking, metalworking, and fabrication with its advanced features and precision engineering.The {CNC Router Model} is designed to meet the demands of modern manufacturing, providing users with a versatile and efficient solution for a wide range of applications. Whether it's creating intricate designs on wood, cutting precise patterns on metal, or shaping composite materials, this router is capable of delivering exceptional results with unparalleled accuracy.One of the key highlights of the {CNC Router Model} is its robust construction and reliable performance. The machine is built with industry-leading components and state-of-the-art technology, ensuring long-term durability and consistent operation. This means that users can rely on the {CNC Router Model} to handle their most complex projects with ease, while maintaining production efficiency.Furthermore, the {CNC Router Model} is equipped with a user-friendly interface and intuitive controls, making it accessible to both experienced machinists and beginners. The machine's software is designed to streamline the programming and operation process, allowing for seamless integration into existing production workflows. With its easy-to-use features, the {CNC Router Model} offers an unparalleled level of versatility and productivity.Additionally, the {CNC Router Model} comes with a range of customization options to cater to specific industry needs. Whether it's the size of the cutting area, spindle power, or tooling accessories, the machine can be tailored to meet the unique requirements of different applications. This flexibility ensures that customers can optimize their production capabilities and achieve superior results with the {CNC Router Model}.At {Company Name}, we are committed to providing comprehensive support and service to our customers. With the launch of the {CNC Router Model}, we are also offering training and technical assistance to ensure that users can maximize the potential of their new machinery. Our team of experts is dedicated to helping customers achieve success with their CNC operations, and we are confident that the {CNC Router Model} will be a valuable asset to their businesses.In conclusion, the introduction of the {CNC Router Model} signifies {Company Name}'s ongoing commitment to innovation and excellence in the CNC industry. With its advanced features, robust construction, and user-friendly design, this new addition to our product line is set to empower our customers with the tools they need to thrive in a competitive manufacturing landscape. We are excited to see the impact that the {CNC Router Model} will have on the industry and look forward to supporting our customers in their journey towards success.
Efficient Machining Services for Your Business Needs
Peek Machining, a leading provider of high-quality machining services, has announced the expansion of their operations to meet the growing demand for precision components in various industries. The company, known for its expertise in manufacturing complex parts from advanced materials, has recently invested in state-of-the-art machinery and technology to enhance their production capabilities and deliver even better results to their clients.Founded over a decade ago, Peek Machining has built a reputation for excellence in the machining industry. With a focus on innovation, quality, and customer satisfaction, the company has consistently delivered high-precision components to a wide range of customers, including those in the aerospace, medical, automotive, and electronics sectors. The company's commitment to investing in the latest technology and continuous improvement has allowed them to stay ahead of the competition and meet the evolving needs of their clients.The recent expansion of Peek Machining's operations is a testament to the company's dedication to providing cutting-edge machining solutions. By acquiring new equipment and implementing advanced manufacturing processes, they are now able to take on larger and more complex projects, while maintaining the highest standards of accuracy and quality. This move not only allows Peek Machining to meet the increasing demand from their existing clients, but also positions them to attract new business opportunities in emerging markets."We are thrilled to announce the expansion of our operations, which represents a significant milestone for Peek Machining," said John Smith, CEO of the company. "This investment underscores our commitment to delivering exceptional results for our clients and solidifies our position as a leading provider of precision machining services. With our expanded capabilities, we are well-equipped to take on new challenges and exceed the expectations of our customers."One of the key advantages of Peek Machining's expanded operations is their ability to work with a wide range of materials, including advanced alloys and composites. This flexibility enables them to produce components that are tailored to the specific needs of each industry, whether it's aerospace parts that require lightweight yet durable materials, or medical devices that demand biocompatible and sterilizable components. With their in-depth knowledge and experience in machining advanced materials, Peek Machining is well-positioned to meet the stringent requirements of their clients across various sectors.Furthermore, Peek Machining takes pride in their skilled team of engineers and machinists, who possess the expertise and craftsmanship necessary to produce intricate parts with the highest level of precision. The company places a strong emphasis on staff training and development, ensuring that their team is equipped with the latest skills and knowledge to tackle complex machining projects. This dedication to continuous improvement and professional growth has allowed Peek Machining to build a strong, reliable workforce that is capable of delivering exceptional results time and again.As Peek Machining continues to expand their operations, they remain committed to their core values of integrity, innovation, and customer satisfaction. With a focus on providing cutting-edge machining solutions and maintaining the highest standards of quality, the company is well-positioned to meet the diverse needs of their clients in a rapidly evolving market. Their investment in advanced technology and expanded capabilities is a testament to their dedication to delivering exceptional results and solidifying their position as a trusted partner for precision machining services.
Top Milling Centers for Precision Machining
Milling Centers Revolutionizing Precision MachiningIn the world of precision machining, milling centers have become a crucial component of the manufacturing process. These state-of-the-art machines have the capability to perform a wide range of tasks, from simple drilling and tapping to complex contouring and 5-axis machining. With their advanced technology and precision engineering, milling centers have revolutionized the way in which parts and components are manufactured.One company at the forefront of this revolution is {}. With decades of experience in the manufacturing industry, {} has established itself as a leader in the production of high-quality milling centers. Their machines are known for their exceptional accuracy, reliability, and versatility, making them the go-to choice for a wide range of industries, including aerospace, automotive, medical, and more.The key to the success of {}'s milling centers lies in their advanced features and capabilities. These machines are equipped with high-speed spindles, automatic tool changers, and sophisticated control systems that enable them to perform complex machining operations with ease. Additionally, {}'s milling centers are designed to be highly rigid and stable, ensuring that they can achieve the tight tolerances and superior surface finishes that are required in modern manufacturing.One of the most impressive aspects of {}'s milling centers is their ability to perform multi-axis machining. This capability allows for the production of highly complex parts and components that would be nearly impossible to manufacture using conventional machining methods. With multi-axis machining, {}'s milling centers can create intricate shapes and contours with precision and accuracy, opening up new possibilities for designers and engineers.In addition to their advanced technology, {}'s milling centers are also designed with efficiency and productivity in mind. These machines are equipped with features such as high-speed rapids, chip conveyors, and coolant systems that help to optimize the machining process and minimize downtime. This not only results in lower production costs but also allows manufacturers to meet tight production deadlines with ease.Another major advantage of {}'s milling centers is their user-friendly design. These machines are equipped with intuitive controls and interfaces that make them easy to operate, even for less experienced machinists. This means that manufacturers can quickly set up and program {}'s milling centers to produce high-quality parts and components with minimal training or supervision.Furthermore, {} provides comprehensive training and support to ensure that customers are able to get the most out of their milling centers. Whether it's troubleshooting technical issues, optimizing machining processes, or providing guidance on tooling and fixturing, {}'s team of experts is dedicated to helping their customers achieve success with their milling centers.With the increasing demand for complex and high-precision components, the role of milling centers in modern manufacturing is more important than ever. Companies like {} are continuously pushing the boundaries of what is possible with their innovative machines, allowing manufacturers to produce parts and components that were previously considered unfeasible. As the industry continues to evolve, milling centers will undoubtedly play a vital role in shaping the future of precision machining.
Complete Guide to Injection Molding Parts: A Breakdown of Essential Components
Injection Molding Parts Name is proud to announce its newest partnership with a leading provider in the industry, Company X. This collaboration is set to revolutionize the way injection molding parts are produced and delivered to customers, with a focus on efficiency, quality, and environmental responsibility.Company X is a renowned leader in the injection molding industry, with a long-standing commitment to innovation and customer satisfaction. With state-of-the-art facilities and a team of experts, Company X has built a reputation for delivering high-quality injection molding parts that meet the diverse needs of its clients.The partnership between Injection Molding Parts Name and Company X represents a significant step forward for both companies. By joining forces, they aim to leverage their respective expertise and resources to drive innovation and set new industry standards for injection molding parts production.One of the key components of this partnership is the implementation of advanced technology and processes to streamline production and enhance product quality. Injection Molding Parts Name will be able to capitalize on Company X's cutting-edge facilities and expertise in automated manufacturing to optimize the production of its parts, resulting in faster lead times and improved consistency in product quality.In addition to technological advancements, the partnership will also prioritize environmental sustainability. Company X has a strong commitment to reducing its carbon footprint and minimizing waste, and this ethos will be integrated into the production of injection molding parts. By leveraging sustainable materials and implementing eco-friendly practices, Injection Molding Parts Name and Company X are dedicated to delivering high-quality products while minimizing their impact on the environment.Furthermore, this collaboration will enable both companies to expand their product offerings and fulfill a wider range of customer needs. With access to Company X's extensive capabilities and expertise, Injection Molding Parts Name will be able to introduce new, innovative products that meet the evolving demands of the market. This will not only benefit their existing customer base but also open up new opportunities for growth and market expansion."We are thrilled to be partnering with Company X to drive innovation and excellence in the injection molding industry," said a spokesperson from Injection Molding Parts Name. "This collaboration represents a significant milestone for us and underscores our commitment to delivering the highest quality products to our customers. We are excited about the opportunities that lie ahead and are confident that this partnership will enable us to set new industry benchmarks."Similarly, Company X is equally enthusiastic about the collaboration. "We are honored to be working with Injection Molding Parts Name to elevate the standards of injection molding parts production," said a representative from Company X. "By combining our expertise and resources, we aim to not only meet but exceed the expectations of our customers, and contribute to the advancement of the industry as a whole."The partnership between Injection Molding Parts Name and Company X is a testament to their dedication to excellence, innovation, and customer satisfaction. With a shared commitment to quality, efficiency, and environmental responsibility, this collaboration is poised to redefine the standards for injection molding parts production and set a new benchmark for the industry. As they move forward with their partnership, customers can expect nothing less than exceptional products and service from these two industry leaders.