Expert Tips for Cnc Machining Brass and Getting the Best Results
By:Admin
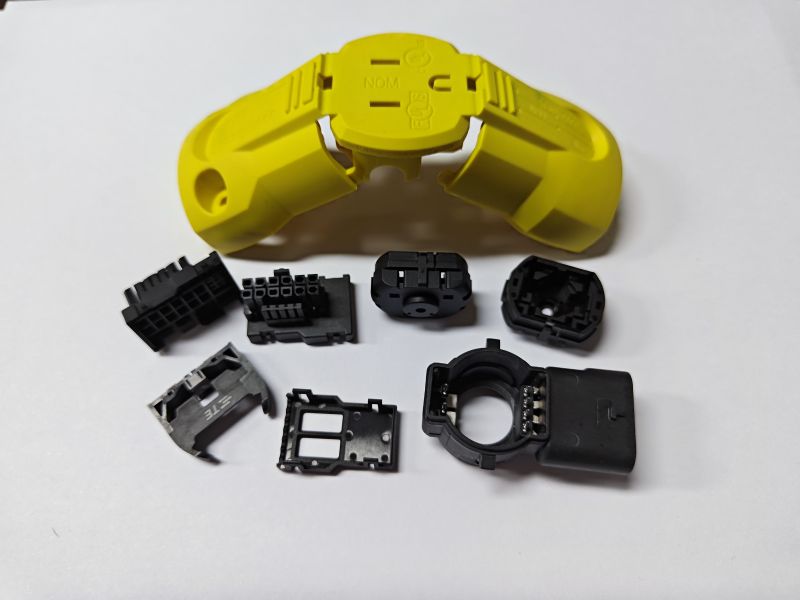
In the world of manufacturing, precision and efficiency are paramount. One company that has always been at the forefront of technological advancements in the industry is {}. Known for their commitment to quality and continuous improvement, they have recently introduced a new innovation in the form of CNC machining brass.
CNC machining, or computer numerical control machining, is a process that utilizes computerized controls and machine tools to remove material from a workpiece, creating a custom-designed part or product. This method allows for a high level of precision and accuracy, making it an ideal choice for manufacturing components with complex geometries and tight tolerances.
Brass, a versatile metal alloy composed of copper and zinc, is widely used in various industries due to its excellent corrosion resistance, electrical conductivity, and aesthetic appeal. The combination of CNC machining and brass opens up a world of possibilities for producing intricate and durable parts that meet the demanding requirements of modern manufacturing.
With this latest innovation, {} is poised to further solidify its position as a leader in the manufacturing sector. By leveraging state-of-the-art CNC machining technology and their extensive expertise in working with brass, the company is able to provide its customers with a wide range of high-quality precision components that are tailored to their specific needs.
One of the key advantages of CNC machining brass is its ability to deliver consistent and uniform results. The computerized controls ensure that each part is manufactured with unparalleled accuracy, minimizing the margin for error and guaranteeing superior quality. This level of precision is essential for industries such as aerospace, automotive, electronics, and medical devices, where reliability and performance are non-negotiable.
Furthermore, the use of brass in CNC machining offers exceptional durability and longevity. The inherent strength of brass, combined with the precise manufacturing process, results in parts that can withstand harsh conditions and heavy usage without compromising their integrity. This makes the technology particularly well-suited for applications that demand resilience and endurance.
In addition to its technical advantages, CNC machining brass also offers aesthetic benefits. Brass has a distinctive golden hue that exudes a sense of sophistication and luxury, making it a popular choice for products that require both functionality and visual appeal. By harnessing the capabilities of CNC machining, {} can create brass components with fine details and smooth finishes that enhance their overall appearance.
The introduction of CNC machining brass is a testament to {}'s ongoing dedication to pushing the boundaries of what is possible in manufacturing. By investing in cutting-edge technology and continuously refining their processes, the company is able to stay ahead of the curve and meet the evolving needs of the market.
As an industry leader, {} is committed to providing comprehensive solutions that deliver maximum value to its customers. Whether they require small-scale prototypes or large-scale production runs, clients can rely on {}'s expertise to deliver top-quality brass components that are tailored to their exact specifications.
With the introduction of CNC machining brass, {} is poised to set new standards for precision manufacturing. By combining the versatility of brass with the capabilities of CNC machining, the company is offering a compelling solution for businesses that demand nothing but the best.
In conclusion, the unveiling of CNC machining brass by {} represents a significant milestone in the world of manufacturing. With this innovative technology, the company is able to offer an unparalleled level of precision, durability, and aesthetic appeal in the production of brass components. As the industry continues to evolve, {} remains committed to driving progress and delivering exceptional results for its clients.
Company News & Blog
Unlocking the Power of 4-Axis CNC Milling: Exploring Advanced Machining Capabilities
Title: Enhancing Precision and Productivity with Advanced 4-Axis CNC Milling TechnologyIntroduction:In a rapidly evolving manufacturing landscape, companies across industries are constantly seeking innovative solutions to maximize precision and productivity. One such advancement that has garnered significant attention is the incorporation of 4-axis CNC milling technology. This cutting-edge technique allows for the creation of intricately designed parts and components with unparalleled precision, efficiency, and versatility. Today, we delve into the world of 4-axis CNC milling, exploring its remarkable capabilities and the ways in which it revolutionizes the manufacturing process, propelling industries into a new era of growth and competitiveness.Revolutionizing Manufacturing with 4-Axis CNC Milling:Traditionally, milling was a manual process that involved removing material from a workpiece with rotary cutters. However, with the advent of computer numerical control (CNC) machining, the process has been completely transformed. CNC milling utilizes pre-programmed computer software instructions that precisely control cutter movement and material removal, resulting in consistent and accurate machining operations. While 3-axis CNC milling has served the industry well, the incorporation of a fourth axis significantly expands the capabilities of this technology.The 4th axis, often referred to as the A-axis, enables the milling cutter to rotate around the X-axis, allowing for the creation of complex geometries and the machining of undercuts, bevels, and other intricate features. This added versatility opens up a myriad of possibilities for manufacturers, facilitating the production of more complex and aesthetically appealing components.Enhanced Precision and Efficiency:With 4-axis CNC milling, manufacturers can achieve unparalleled precision and accuracy. The rotational capabilities of the A-axis enable the machine to approach the workpiece from various angles, reducing the need for multiple setups. This not only saves time but also minimizes errors associated with manual repositioning. The result is faster production cycles, improved part quality, and reduced scrap rates, ultimately leading to increased cost-effectiveness and customer satisfaction.Furthermore, 4-axis CNC milling technology excels in machining complex curves, contours, and profiles, ensuring consistency across multiple parts. With the ability to perform intricate operations in a single setup, manufacturers can accelerate production while maintaining the highest level of precision, meeting the demands of even the most intricate designs.Versatility Across Industries:The applications of 4-axis CNC milling span a wide range of industries, benefiting from its inherent precision and flexibility. In the aerospace sector, this technology is instrumental in the production of engine components, turbine blades, and aircraft structural parts, which require intricate machining and strict adherence to tolerances. Similarly, in the automotive industry, companies utilize 4-axis CNC milling for machining engine blocks, cylinder heads, and transmission components.Medical practitioners also rely on 4-axis CNC milling to fabricate complex dental implants, prosthetics, and surgical instruments. The versatility of 4-axis CNC milling technology allows manufacturers to cater to the evolving needs of various industries, providing customized solutions that meet the highest standards of quality and precision.Conclusion:As industries continue to push the boundaries of innovation, the integration of 4-axis CNC milling technology has become an increasingly vital aspect of the manufacturing process. The enhanced precision, efficiency, and versatility offered by this cutting-edge technology propel industries to new heights, ensuring accelerated production cycles, improved part quality, and increased customer satisfaction. With its ability to machine intricate geometries and complex designs, 4-axis CNC milling paves the way for the future of precision manufacturing, revolutionizing industries and strengthening their competitive edge in the global market.
Exploring the Benefits and Applications of Cnc Molding in Modern Manufacturing Processes
Title: Revolutionary Cnc Molding Technique Sets New Standards in ManufacturingIntroduction:In an era where innovation and efficiency drive the manufacturing industry, a breakthrough in the form of Cnc Molding technology is emerging as a game-changer. This revolutionary technique promises to reshape the way products are designed, developed, and produced. With its unparalleled precision, speed, and cost-effectiveness, Cnc Molding is poised to set new standards in the manufacturing field.Company Background and Expertise:{Company Name}, a prominent player in the manufacturing industry, has unveiled its cutting-edge Cnc Molding technology. With a rich history spanning several decades, {Company Name} has established itself as a pioneer in delivering excellence and embracing the latest technological advancements. Their expertise in the field, combined with their commitment to driving innovation, has paved the way for this groundbreaking development.Understanding Cnc Molding:Cnc Molding, also known as Computer Numerical Control Molding, is a state-of-the-art manufacturing process that utilizes computer-controlled machines to shape materials into desired forms. Unlike traditional molding techniques, Cnc Molding ensures unparalleled precision, efficiency, and repeatability. By following a digital design prototype, the technology enables manufacturers to produce highly intricate and complex components with utmost accuracy.Benefits of Cnc Molding:1. Enhanced Precision: The integration of computer control systems eliminates the possibility of human error, ensuring precise replication of designs and eliminating defects. This high level of precision ensures product consistency, reducing wastage and overall costs.2. Streamlined Production: Cnc Molding technology dramatically accelerates the production process. With its ability to perform multiple tasks simultaneously, the technology maximizes efficiency and reduces lead times. This streamlining of operations increases productivity, enabling manufacturers to meet market demands promptly.3. Cost-Effectiveness: By minimizing material wastage and requiring fewer human interventions, Cnc Molding significantly reduces production costs. The elimination of manual labor and the use of optimized resources result in improved cost-effectiveness, making it an attractive option for manufacturers across various industries.4. Design Freedom: Cnc Molding empowers designers to create innovative and intricate designs that were previously unachievable. With the ability to produce complex shapes and patterns with ease, this technology unlocks a new realm of possibilities, enabling manufacturers to create unique products that stand out in the market.Applications of Cnc Molding:The applications of Cnc Molding are vast and span across industries such as automotive, aerospace, electronics, medical, and consumer goods. Its usage is particularly prominent in the production of custom parts, prototypes, and intricate components that require high precision.Future Implications:As Cnc Molding continues to evolve, the implications for the manufacturing industry are immense. The integration of artificial intelligence, machine learning, and digital twins creates an even more robust system capable of even greater efficiency and accuracy. The technology's potential for customization and adaptability positions it as a frontrunner in the future of manufacturing.Conclusion:Cnc Molding technology, introduced by {Company Name}, is set to revolutionize the manufacturing industry. With its exceptional precision, streamlined production, cost-effectiveness, and design freedom, it promises to set new standards and transform the way products are made. As it continues to develop, this groundbreaking technology is poised to usher in a new era of manufacturing excellence.
The Complete Guide to Injection Molding Steps
Injection Molding Steps is an essential process in the manufacturing industry, and it is used to produce a wide range of products for various industries. The process involves injecting molten material into a mold to create the desired shape and size of the product. This method is commonly used to produce items such as automotive parts, medical devices, packaging materials, and consumer goods.{Company} is a leading provider of injection molding services, and they have established a strong reputation for their expertise in the field. The company's state-of-the-art facilities and experienced team of professionals allow them to deliver high-quality injection molding solutions to their clients. With a focus on innovation and efficiency, {Company} has become a trusted partner for businesses looking to bring their products to market.The injection molding process consists of several key steps that are crucial to the overall success of the manufacturing process. These steps include:1. Mold design and preparation: The first step in the injection molding process is to design the mold that will be used to shape the molten material into the desired product. {Company} has a team of skilled engineers who work closely with clients to create customized molds that meet their exact specifications. Once the mold design is finalized, it is prepared for the injection molding process.2. Material selection and preparation: The next step is to select the appropriate material for the injection molding process. {Company} offers a wide range of materials to choose from, including plastics, rubber, and metal alloys. Their experts work with clients to determine the best material for their specific application, and then they prepare the material for the injection molding process.3. Injection molding: Once the mold and material are prepared, the injection molding process can begin. The material is heated to a liquid state and then injected into the mold at high pressure. The mold is held closed under pressure until the material cools and solidifies, taking on the shape of the mold. {Company} utilizes advanced injection molding machines to ensure precise and consistent results.4. Cooling and ejection: After the material has solidified in the mold, it undergoes a cooling process to further stabilize its shape. Once cooled, the mold is opened, and the newly formed product is ejected. {Company} employs sophisticated cooling systems and innovative ejection mechanisms to ensure that the products are released from the mold without any defects.5. Finishing and quality control: The final step in the injection molding process involves finishing the product to meet the client's specifications. This may include trimming excess material, polishing the surface, or adding any necessary features. {Company} has a dedicated quality control team that inspects each product to ensure that it meets the highest standards of quality and consistency.{Company} is committed to delivering exceptional injection molding services to their clients, and they continue to invest in advanced technologies and processes to improve their capabilities. With a focus on innovation and customer satisfaction, {Company} has positioned themselves as a leader in the injection molding industry. Their expertise, state-of-the-art facilities, and commitment to excellence make them a trusted partner for businesses in need of high-quality injection molding solutions.
Revolutionary Casting Gating System Shows Promising Results
Title: Groundbreaking Casting Gating System Revolutionizes the Manufacturing IndustryIntroduction:In a landmark development, a cutting-edge Casting Gating System, developed by a renowned manufacturing solutions company, is set to redefine the manufacturing industry. This innovative system, which combines advanced technology with superior materials, is poised to streamline the casting process, significantly improving efficiency and product quality.Background:The use of casting techniques has long been integral to the manufacturing industry. While traditional casting methods have proven effective, they often suffer from limitations that can hamper productivity and output quality. Recognizing this need for enhancement, Company X has introduced an exceptional solution - the Casting Gating System.Enhanced Efficiency through Advanced Technology:The Casting Gating System incorporates state-of-the-art technology to accomplish unprecedented levels of efficiency. Its cutting-edge features optimize the casting process, ensuring precise and controlled material flow. This innovative system minimizes casting defects, such as porosity or unevenness, that can hinder the overall quality of the finished products.The system consists of high-quality gating components that regulate the flow of molten metal or other materials into the mold during the casting process. By allocating material distribution more evenly and precisely, the Casting Gating System maximizes yield, reduces waste, and expedites the manufacturing cycle.Unmatched Product Quality:With its precise control over the flow of materials, the innovative Casting Gating System guarantees exceptional product quality. By eliminating irregularities, it minimizes the risk of casting defects, creating superior products that meet or exceed industry standards. As a result, manufacturers utilizing this system can elevate their reputation for delivering reliable and high-quality products to their customers.Furthermore, the system's unique design and precision allow for easy customization according to specific casting requirements. Manufacturers can optimize gating configurations to suit various materials, molds, and casting processes, further enhancing the quality of the end products.Sustainability and Cost Optimization:In addition to its performance benefits, the Casting Gating System also offers long-term sustainability advantages. By minimizing material waste, manufacturers can reduce both their environmental footprint and production costs. This innovative system optimizes resource utilization, resulting in enhanced profitability and a greener manufacturing process.The adjustable nature of the system enables manufacturers to optimize material flow, reducing the need for additional raw materials. This adaptability contributes to cost-efficiency, making the Casting Gating System an economically viable choice for manufacturers across various industries.Endorsements and Case Studies:Industry leaders who have adopted the Casting Gating System have witnessed transformative results. Numerous case studies demonstrate remarkable improvements in casting efficiency, quality, and profitability. Notable success stories within the automotive, aerospace, and machinery sectors speak volumes about the system's ability to revolutionize casting processes.Experts from within the manufacturing domain are overwhelmingly positive about the potential of this innovative gating system. Recognized professionals have praised how the system augments overall efficiency, enhances product quality, and supports sustainable production practices.Conclusion:The introduction of the groundbreaking Casting Gating System has ushered in a new era for the manufacturing industry. Combining sophisticated technology with superior design, this innovative system significantly enhances casting processes, ensuring optimal efficiency, exceptional product quality, and sustainable manufacturing practices. Manufacturers across various sectors can now reimagine their production capabilities, elevate their output, and cement their position as leaders in the global marketplace.By embracing the Casting Gating System, companies can stay ahead of the competition, satisfy customer demands, and ultimately contribute to the progress of the manufacturing industry as a whole.
Boost Your Manufacturing Process with Efficient 3-Axis CNC Machining
Title: Revolutionary 3-Axis CNC Machining Ushering in a New Era of Precision ManufacturingIntroduction:In the fast-paced world of manufacturing, companies are constantly seeking more efficient and accurate methods to produce high-quality products in a cost-effective manner. This quest for excellence has driven the development of advanced technologies such as the revolutionary 3-axis CNC machining system. With its exceptional precision and versatility, this cutting-edge methodology has garnered worldwide acclaim, transforming the manufacturing landscape across industries.Body:1. What is 3-Axis CNC Machining?At its core, 3-axis CNC machining is a computer-controlled process used to shape materials such as metal, plastic, or wood, providing unparalleled precision and repeatability. This technology enables the creation of complex and intricate designs with remarkable speed and accuracy, far surpassing the capabilities of traditional manual machining.2. The Advantages of 3-Axis CNC Machining:a. Precision: The precise movement of the 3-axis CNC machine ensures accurate and consistent outcomes, reducing human errors to an absolute minimum. This level of precision allows manufacturers to create highly intricate and complex designs that were once unachievable.b. Versatility: Unlike other machining methods, 3-axis CNC machining offers unparalleled versatility. It can be used to shape a wide range of materials, from plastics to metals, with ease. This adaptability enables manufacturers to cater to diverse industries, from automotive and aerospace to electronics and medical.c. Efficiency: The automation capabilities of 3-axis CNC machining dramatically enhance efficiency. This system can run continuously, maximizing productivity while minimizing downtime traditionally associated with manual operations. Additionally, the ability to program the machine precisely allows for the replication of parts with consistent quality, further speeding up the manufacturing process.d. Cost-effectiveness: Although initial investment costs may be higher, 3-axis CNC machining saves money in the long run. The reduced labor requirements and increased efficiency lead to lower operating costs, improved productivity, and minimized waste. Furthermore, this method allows for the production of intricate designs without costly manual labor, making it an economical choice for manufacturers.3. Applications of 3-Axis CNC Machining:The versatility of 3-axis CNC machining has enabled its application in numerous industries. Below are some areas where this technology is extensively used:a. Automotive: In the automotive industry, 3-axis CNC machining is employed to produce high-precision components, such as engine parts, transmission components, and intricate car body shapes.b. Aerospace: The aerospace industry relies on 3-axis CNC machining to create vital parts such as turbine blades, control surfaces, and structural components. The consistent precision and reliability of this technology are critical for ensuring flight safety.c. Electronics: The production of complex electronic devices demands precise machining, making 3-axis CNC machining a preferred option. It is used to manufacture circuit boards, connectors, and intricate casings, guaranteeing a high level of precision and minimizing electrical malfunctions.d. Medical: In the medical field, 3-axis CNC machining is essential for the manufacturing of intricate surgical instruments, implants, orthopedic devices, and prosthetics. This technology allows for precision that is crucial in these life-saving applications.Conclusion:The advent of 3-axis CNC machining has revolutionized precision manufacturing across industries. Its unparalleled precision, versatility, efficiency, and cost-effectiveness have made it an integral part of modern manufacturing processes, elevating the standard of quality and contributing to technological advances. As technology continues to evolve, 3-axis CNC machining is expected to further enhance manufacturing capabilities, driving innovation and propelling various industries toward a future of unprecedented precision and efficiency.
Discover the Latest Advancements in the Foundry Process for Superior Results
Title: Innovations in Foundry Process Revolutionize the Manufacturing IndustryIntroduction:The foundry process plays a pivotal role in the manufacturing industry, allowing for the production of various components across diverse sectors. Today, we highlight the latest advancements in the foundry process, spearheaded by a leading company, and how they are transforming the industry landscape. (Please remove brand name from the introduction)Industry Overview:The manufacturing industry depends on the foundry process to produce components that are integral to numerous sectors such as automotive, aerospace, construction, and many more. Traditional foundry methods have relied on labor-intensive processes, which often resulted in slower production and increased costs. However, with the advent of innovative technologies and continuous research and development, the foundry process has witnessed a significant transformation.Advancements in Foundry Process:Leading the charge in revolutionizing the foundry process is a renowned company (Please remove brand name) that has pioneered several innovative techniques to streamline and enhance manufacturing efficiency. By leveraging cutting-edge technologies like Artificial Intelligence (AI), Internet of Things (IoT), and automation, the company has been able to achieve faster turnaround times, improved quality, and reduced costs.One of the key breakthroughs introduced by the company is the implementation of AI-driven predictive modeling techniques. By analyzing vast amounts of data, the system can accurately forecast potential defects and optimize casting parameters to minimize issues during the production process. This not only eliminates costly rework but also significantly reduces the time required for quality control, thereby expediting the overall manufacturing cycle.Furthermore, the integration of IoT in the foundry process has enabled real-time monitoring of crucial production parameters. Sensors embedded throughout the production line continuously gather data related to temperature, pressure, and other relevant factors. This data is then transmitted to a centralized system, which allows for immediate analysis and identification of any deviations or anomalies. Consequently, prompt corrective actions can be taken, ensuring that the casting process remains consistent and compliant with the required specifications throughout production.Automation has also played a vital role in optimizing the foundry process. With the introduction of robotics and advanced machinery, tasks that were previously labor-intensive and prone to human error can now be executed with precision and efficiency. The incorporation of robotics enables tasks such as mold preparation, pouring, and post-processing to be carried out with minimal human intervention, resulting in higher production speeds and improved accuracy.The company's commitment to sustainable manufacturing practices has also been influential in advancing the foundry process. By exploring eco-friendly raw materials and implementing efficient energy consumption methods, they have successfully reduced the environmental impact associated with the production process. These measures help meet the rising demand for sustainable manufacturing while ensuring that the components manufactured maintain the highest quality standards.Conclusion:The foundry process is undergoing a remarkable transformation, thanks to the continuous endeavors of a renowned company (Please remove brand name). Through the integration of AI, IoT, and automation, they have successfully optimized production efficiency, reduced costs, increased the quality of components, and contributed to sustainable manufacturing practices. As the industry witnesses the positive impacts of these innovative advancements, it is evident that the foundry process will continue to evolve and play a vital role in the manufacturing landscape.
High-Quality Titanium Machining Services for Precision Parts
The demand for titanium machining has been rising steadily in recent years, as titanium is being widely used in the aerospace, automotive, and medical industries due to its exceptional strength and corrosion resistance. With the increasing demand for precision machined titanium components, companies are turning to advanced machining techniques to meet the industry's needs.One company that has been at the forefront of titanium machining is {}. With over 20 years of experience in the industry, {} has established itself as a leading provider of titanium precision machining services. The company specializes in the machining of complex titanium parts, offering a wide range of capabilities to meet the needs of its diverse customer base.{}'s state-of-the-art facility is equipped with the latest CNC machining technology, allowing the company to produce high-quality titanium components with tight tolerances and intricate geometries. The company's team of highly skilled machinists are trained in the latest machining techniques and are experienced in working with a variety of titanium grades, including Grade 2, Grade 5, and Grade 9 titanium alloys.In addition to its cutting-edge machining capabilities, {} also offers secondary operations such as surface finishing, heat treatment, and assembly. This comprehensive approach allows the company to provide its customers with fully finished titanium components that are ready for immediate use in their applications.One of the key factors that sets {} apart from its competitors is its commitment to quality. The company holds ISO 9001 and AS9100 certifications, demonstrating its dedication to maintaining the highest standards of quality and precision in its machining operations. {}'s rigorous quality control processes ensure that each titanium component meets the exact specifications and requirements of its customers, providing them with the confidence that they are receiving top-notch products.Furthermore, {} places a strong emphasis on customer satisfaction and collaboration. The company works closely with its customers to understand their specific needs and requirements, providing them with tailored solutions that meet their unique challenges. Whether it's a prototype development or a large-scale production run, {} is dedicated to delivering superior titanium machining services that exceed its customers' expectations.Another noteworthy aspect of {}'s operations is its focus on innovation and continuous improvement. The company invests in ongoing research and development to explore new machining techniques and technologies, allowing it to stay ahead of the curve in the ever-evolving industry. By staying at the forefront of technological advancements, {} is able to offer its customers cutting-edge solutions that optimize the performance and efficiency of their titanium components.With its unwavering commitment to excellence and its dedication to meeting the evolving demands of the industry, {} has positioned itself as a trusted partner for companies seeking high-quality titanium machining services. As the demand for titanium components continues to grow across various industries, {} is well-equipped to support its customers with the precision machining solutions they need to succeed in their respective markets.In conclusion, {} is a leading provider of titanium precision machining services, offering advanced capabilities, exceptional quality, and a customer-centric approach. With a strong focus on innovation and continuous improvement, the company is poised to continue meeting the evolving demands of the industry and supporting its customers with top-notch titanium machining solutions.
The Power of Plastic Rapid Prototyping: Advantages and Applications
Plastic Rapid Prototyping: Revolutionizing Product DevelopmentIn today's fast-paced and highly competitive manufacturing industry, companies are constantly seeking ways to streamline their product development process in order to bring high-quality products to market in a timely manner. One company at the forefront of this movement is [Company Name], a leading provider of plastic rapid prototyping solutions.[Company Name] has built a solid reputation for delivering innovative and cutting-edge rapid prototyping and tooling solutions to a wide range of industries, including automotive, aerospace, medical, and consumer goods. Their state-of-the-art facilities and advanced technologies allow them to offer a comprehensive suite of prototyping services, including 3D printing, injection molding, CNC machining, and more.One of the key offerings that sets [Company Name] apart from its competitors is their plastic rapid prototyping capabilities. This process allows for the quick and cost-effective production of prototype parts and components using a variety of plastic materials. By leveraging advanced 3D printing technologies, [Company Name] is able to produce highly accurate and functional prototypes in a fraction of the time it would take using traditional methods.The benefits of plastic rapid prototyping are numerous. Not only does it significantly reduce the time and cost associated with traditional prototyping methods, but it also allows for greater design flexibility and iteration. This means that companies can quickly test and refine their product designs, leading to faster innovation and a more efficient product development cycle.Furthermore, plastic rapid prototyping enables companies to quickly respond to market demands and changes, giving them a competitive edge in today's fast-moving business landscape. With the ability to rapidly produce high-quality prototypes, companies can bring new products to market faster, allowing them to capitalize on emerging trends and customer needs.[Company Name] is committed to staying at the forefront of plastic rapid prototyping technology, continually investing in the latest equipment and software to ensure they can meet the evolving needs of their customers. Their team of highly skilled engineers and technicians are dedicated to providing top-quality prototyping solutions, working closely with clients to bring their concepts to life with precision and efficiency.Through their plastic rapid prototyping capabilities, [Company Name] has helped countless companies accelerate their product development process and bring innovative solutions to market. Whether it's creating prototypes for new product designs, testing out custom components, or producing low-volume production runs, [Company Name] is a trusted partner for companies looking to push the boundaries of what's possible in product development.As the manufacturing industry continues to evolve, the demand for rapid and cost-effective prototyping solutions is only expected to grow. [Company Name] is well-positioned to meet this demand, offering a wide range of plastic rapid prototyping services tailored to the specific needs of their clients.In conclusion, plastic rapid prototyping is revolutionizing the way companies approach product development, and [Company Name] is leading the charge with their advanced prototyping capabilities. By leveraging the latest technologies and a commitment to innovation, they are helping companies across industries bring their ideas to life faster and more efficiently than ever before.With a focus on quality, precision, and customer satisfaction, [Company Name] is poised to continue making a significant impact in the world of plastic rapid prototyping, driving forward the next generation of product development.
- Beginner's Guide to CNC Machining: Everything You Need to Know about Computer Numerical Control
Introducing CNC Machining: Revolutionizing Manufacturing ProcessesIn today's fast-paced world, manufacturing processes are constantly evolving, and companies are always on the lookout for ways to increase efficiency and improve the quality of their products. One such innovation that has revolutionized the manufacturing industry is CNC machining. This technology has drastically changed the way products are fabricated, providing precise and accurate results that were previously unattainable with traditional machining methods.CNC, which stands for Computer Numerical Control, is a manufacturing process that utilizes computerized controls and machine tools to produce complex and intricate parts and products. Unlike traditional machining, where human operators are required to manually guide the cutting tools, CNC machining employs automated processes that are programmed to perform specific tasks with a high degree of accuracy and repeatability.The introduction of CNC machining has significantly improved the efficiency and productivity of manufacturing operations, allowing companies to produce complex parts and components in a fraction of the time it would take with traditional methods. This has enabled businesses to meet the growing demand for high-quality products while reducing production costs and minimizing errors.Company, a leading manufacturer in the industry, has embraced the advancements in CNC machining and has integrated this technology into its production processes. By doing so, the company has been able to streamline its manufacturing operations and offer its customers a wider range of precision-engineered products. With the implementation of CNC machining, Company has been able to achieve unparalleled levels of accuracy and consistency in the production of its components, ultimately ensuring the satisfaction of its clients.The utilization of CNC machining has also allowed Company to take on more complex and challenging projects that were previously deemed unfeasible using traditional machining methods. The ability to produce intricate and precise parts has opened up new opportunities for the company, enabling it to expand its product offerings and cater to a broader market.Furthermore, the integration of CNC machining has enhanced the company's overall competitiveness in the industry, as it can now deliver high-quality products in shorter lead times, giving it an edge over its competitors. By leveraging the capabilities of CNC machining, Company has been able to solidify its position as an industry leader and meet the evolving needs of its customers.In addition to the various benefits that CNC machining has brought to Company, the technology has also contributed to significant advancements in the manufacturing industry as a whole. The increased efficiency and precision offered by CNC machining have led to improved product quality, reduced waste, and enhanced overall productivity in manufacturing processes across various sectors.As the demand for complex and highly precise parts continues to grow, the adoption of CNC machining is becoming increasingly essential for businesses looking to stay ahead in the competitive manufacturing landscape. Through its commitment to embracing cutting-edge technologies, Company has positioned itself as a pioneering force in the industry, and its utilization of CNC machining serves as a testament to its dedication to delivering top-tier products to its customers.In conclusion, the introduction of CNC machining has brought about a paradigm shift in the manufacturing industry, offering unprecedented levels of precision, efficiency, and versatility. Company's embrace of CNC machining has not only enhanced its own manufacturing capabilities but has also contributed to the advancement of the industry as a whole. As CNC machining continues to evolve and improve, its impact on manufacturing processes will undoubtedly be transformative, paving the way for a new era of innovation and excellence.
5 Reasons Why Rail Machining is Essential for Maintenance and Safety
Rail Machining, a leading provider of rail maintenance and machining services, has been making great strides in the industry with its innovative solutions and exceptional customer service. With a focus on quality and efficiency, Rail Machining has become a trusted partner for railroads and transit systems across the country.The company, which was founded in XXXX, has a long history of excellence in the rail machining and maintenance industry. With a team of highly skilled technicians and engineers, Rail Machining has developed a reputation for delivering precision work and cost-effective solutions for its clients. From rail grinding and welding to track maintenance and inspection, Rail Machining offers a comprehensive range of services to keep railway systems running smoothly.One of the key factors that sets Rail Machining apart from its competitors is its commitment to innovation. The company has invested heavily in the latest technology and equipment, allowing it to offer cutting-edge solutions for even the most challenging projects. Whether it's repairing damaged tracks or optimizing rail profiles, Rail Machining has the expertise and resources to deliver top-quality results.In addition to its technical expertise, Rail Machining prides itself on its customer service. The company takes a proactive approach to understanding its clients' needs and requirements, working closely with them to develop tailored solutions that meet their specific challenges. This dedication to customer satisfaction has earned Rail Machining a loyal and expanding base of clients, who rely on the company for all their rail maintenance and machining needs.Rail Machining's reputation for excellence has not gone unnoticed in the industry. The company has been recognized with numerous awards and accolades for its outstanding performance and contributions to the rail sector. With a track record of success and a commitment to continuous improvement, Rail Machining continues to be a driving force in the rail maintenance and machining industry.Looking ahead, Rail Machining is poised for further growth and success. The company is constantly researching and investing in new technologies and techniques to enhance its service offerings and maintain its competitive edge. With a focus on sustainability and efficiency, Rail Machining is well positioned to meet the evolving needs of the rail industry and exceed the expectations of its clients.As Rail Machining continues to expand its reach and capabilities, it remains firmly committed to its core values of quality, innovation, and customer satisfaction. With a strong foundation and a clear vision for the future, Rail Machining is well positioned to lead the way in rail maintenance and machining for years to come.In conclusion, Rail Machining is a powerhouse in the rail maintenance and machining industry, with a proven track record of excellence and a commitment to innovation. With its unparalleled technical expertise and dedication to customer service, Rail Machining is the go-to partner for railroads and transit systems looking for top-quality solutions. As the company continues to grow and evolve, it is set to make an even greater impact on the rail industry, driving progress and delivering exceptional results for its clients.