Discover the Benefits of Plastic Insert Molding for Your Products
By:Admin
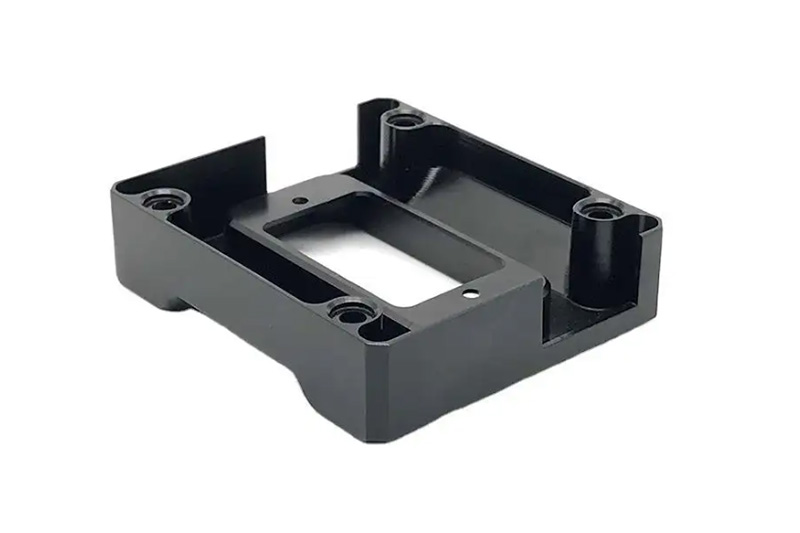
The field of plastic injection molding has taken a significant leap forward with the introduction of plastic insert molding by {}. This innovative process is set to revolutionize the industry, offering a range of benefits and possibilities for the manufacturing sector.
{} is a leading provider of advanced manufacturing solutions, specializing in plastic injection molding, rapid prototyping, and custom tooling. With over a decade of experience in the industry, the company has earned a reputation for delivering high-quality products and exceptional service to its clients.
The introduction of plastic insert molding is the result of extensive research and development by the company's team of engineers and designers. This groundbreaking process allows for the integration of metal, ceramic, or other materials into plastic parts during the molding process, resulting in a stronger, more durable finished product.
One of the key advantages of plastic insert molding is the ability to create complex, multi-material components with a high level of precision. This opens up a wealth of new possibilities for manufacturers in industries such as automotive, aerospace, electronics, and consumer goods.
With plastic insert molding, {} can offer its clients a cost-effective and efficient solution for producing parts with intricate geometries and tight tolerances. This process also eliminates the need for secondary assembly operations, reducing production time and costs.
Furthermore, plastic insert molding allows for the creation of components with a seamless integration of different materials, resulting in improved performance and functionality. This is particularly beneficial for products that require the combination of metal and plastic elements, such as electronic enclosures, automotive sensors, and medical devices.
In addition to the technical advantages, plastic insert molding also offers environmental benefits by reducing material waste and energy consumption. By streamlining the production process and minimizing the need for additional components, {} is contributing to sustainable manufacturing practices.
The introduction of plastic insert molding further solidifies {}'s position as a leader in the industry, setting a new standard for quality and innovation. By leveraging this advanced technology, the company is well-equipped to meet the evolving needs of its clients and deliver solutions that exceed expectations.
"We are excited to introduce plastic insert molding as part of our comprehensive suite of manufacturing services," said [Spokesperson], {}'s [Title]. "This breakthrough process allows us to offer our clients a truly integrated solution for their manufacturing needs, and we are confident that it will open up new possibilities for the industry as a whole."
With the launch of plastic insert molding, {} is poised to drive a new era of advancement in plastic injection molding, delivering superior products and unmatched capabilities to its clients. As the company continues to push the boundaries of what is possible, it is clear that {} is leading the way toward a brighter future for manufacturing.
Company News & Blog
Unlocking the Secrets of the Innovative Insert Molding Process
[Title]: Innovative Insert Molding Process Enhances Manufacturing Efficiency[Subtitle]: Taking Manufacturing Precision to New Heights[Date]: [Insert Date][City], [State] - In their relentless pursuit of excellence, [Company Name], a leading manufacturer in the industry, has introduced an innovative insert molding process that promises to revolutionize the manufacturing landscape. This groundbreaking technique has allowed the company to enhance efficiency and precision, cementing their position as pioneers in the field.[Company Name], with their rich history of delivering cutting-edge solutions, has consistently demonstrated their commitment to pushing the boundaries of what is possible. By successfully implementing the insert molding process, they aim to revolutionize the way manufacturing operations are conducted.The insert molding process revolutionizes manufacturing by combining multiple materials or components into a single molded plastic part. This process greatly reduces assembly steps and enhances productivity, streamlining the entire manufacturing process. By eliminating the need for separate components and multiple assembly lines, [Company Name] has significantly reduced production time, allowing them to meet the increasing demands of their customers.Through the innovative use of the insert molding process, [Company Name] has successfully eliminated the need for additional assembly steps, thereby reducing costs and minimizing the margin for error. This not only translates into significant time and cost savings but also ensures a higher degree of quality control and consistency in the final product.Unlike traditional manufacturing techniques, the insert molding process involves the encapsulation of specific components or inserts within the molded plastic part. This creates a strong bond between the plastic and the inserted components, resulting in a durable and reliable end product. This advanced manufacturing technique has been widely hailed as a game-changer, enabling manufacturers to produce complex and compact parts with unmatched precision and reliability.[Company Name]'s mastery of the insert molding process stems from their in-depth understanding of the industry and their continuous investment in cutting-edge technologies. By leveraging their expertise and state-of-the-art facilities, they have succeeded in refining this process to deliver superior quality products to their clients.Furthermore, the insert molding process offers numerous design possibilities, enabling manufacturers to create products that are aesthetically pleasing while maintaining functionality. By seamlessly integrating various materials and components, manufacturers can achieve a more sophisticated and versatile end product.[Company Name] has always been at the forefront of innovation and has earned a reputation for delivering outstanding customer satisfaction. By adopting the insert molding process, they have cemented their position as pioneers in the industry, offering their clients a comprehensive range of solutions that cater to their diverse requirements.The benefits of the insert molding process extend beyond just manufacturing efficiency. By reducing the number of components and assembly steps, [Company Name] has also contributed to a greener and more sustainable industry. The decreased material usage and lower energy consumption associated with this manufacturing technique result in a reduced carbon footprint.[Company Name] takes pride in their dedication to continuous improvement. They constantly strive to push the boundaries of what is possible, and the introduction of the insert molding process is a testament to their relentless pursuit of excellence. This innovation has not only redefined their position in the industry but also set new standards for manufacturing precision and efficiency.In conclusion, [Company Name]'s introduction of the insert molding process has revolutionized the manufacturing landscape. By combining multiple materials or components into one molded plastic part, they have enhanced efficiency, reduced production time, and improved the overall quality of their products. This groundbreaking technique is a testament to the company's commitment to innovation and customer satisfaction. As [Company Name] continues to lead the way in cutting-edge solutions, the future of manufacturing looks brighter than ever.
The Future of Injection Molding Industry: Trends and Growth Opportunities
The Injection Molding Industry is currently enjoying a surge in growth, thanks to the continuous technological advancements and increasing demand in different sectors such as automotive, packaging, healthcare, and consumer goods. As a prominent player in this industry, {Company Name} has continued to maintain its market leadership by delivering high-quality products and excellent customer service.{Company Name} has established itself as a reliable and innovative injection molding solution provider, offering a wide range of products and services to meet the diverse needs of its clients. With a strong focus on research and development, the company has been able to stay ahead of the competition by continuously introducing new and advanced molding techniques and processes. This has enabled {Company Name} to expand its product offerings and cater to a wider client base.In addition to its dedication to technological advancements, {Company Name} has also prioritized sustainability and environmental responsibility in its operations. The company has implemented eco-friendly manufacturing practices and has invested in state-of-the-art equipment to minimize energy consumption and reduce its carbon footprint. This commitment to sustainability has not only enhanced the company's reputation but has also positioned them as a preferred partner for clients who prioritize environmentally conscious suppliers.One of the key factors contributing to {Company Name}'s success is its commitment to understanding and meeting the specific needs of its clients. The company works closely with its customers to provide customized injection molding solutions that are tailored to their unique requirements. This personalized approach has earned {Company Name} a loyal customer base and has led to long-standing partnerships with reputable companies across various industries.Moreover, {Company Name} has also kept pace with the digital transformation in the manufacturing industry by incorporating cutting-edge technologies into its operations. The company has embraced automation and data-driven processes to streamline its production and enhance efficiency. This strategic adoption of Industry 4.0 practices has allowed {Company Name} to improve its production capabilities and deliver cost-effective solutions to its clients.Despite the challenges posed by the global pandemic, {Company Name} has demonstrated resilience and agility in maintaining a stable supply chain and meeting its clients' needs. The company has implemented robust safety measures to ensure the well-being of its employees and has adapted its operations to accommodate the changing market dynamics. As a result, {Company Name} has been able to navigate through the uncertainties and emerge as a reliable partner for its customers during these unprecedented times.Looking ahead, {Company Name} remains committed to furthering its position in the injection molding industry by continuously innovating and expanding its capabilities. With strategic investments in talent, technology, and infrastructure, the company aims to solidify its market presence and explore new growth opportunities. Additionally, {Company Name} is also exploring partnerships and collaborations to tap into emerging markets and offer its expertise to a broader global audience.In conclusion, {Company Name} stands as a frontrunner in the injection molding industry, driven by its steadfast commitment to innovation, sustainability, customer satisfaction, and operational excellence. With its strong industry presence, diverse product portfolio, and forward-thinking approach, {Company Name} is well-positioned to capitalize on the growing market demand and lead the way in shaping the future of injection molding.
Top 5 Tips for Perfecting Molding Work
Molding Work, a prominent leader in the manufacturing industry, is dedicated to providing high-quality and efficient molding services to its clients. With decades of experience and a team of skilled professionals, Molding Work has proven to be a reliable and trustworthy partner for businesses looking to bring their products to life.The company takes pride in its state-of-the-art facilities and cutting-edge technology, which allow them to offer a wide range of molding services, including injection molding, blow molding, and compression molding. Their extensive capabilities make them a one-stop shop for all molding needs, catering to a diverse range of industries such as automotive, consumer goods, and medical devices.At the heart of Molding Work’s success is their unwavering commitment to excellence and customer satisfaction. They strive to understand the unique needs and specifications of each client, ensuring that the final product meets their exact requirements. This dedication to quality has earned them a stellar reputation in the industry, with many clients choosing to partner with Molding Work time and time again.In addition to their exceptional technical capabilities, Molding Work places a strong emphasis on sustainability and environmental responsibility. They have implemented various measures to minimize waste and reduce their environmental footprint, aligning with the growing demand for eco-friendly manufacturing practices.But perhaps the most impressive aspect of Molding Work is their ability to adapt and innovate in a rapidly evolving industry. They continuously invest in research and development, staying ahead of the curve with the latest advancements in materials, technology, and processes. This forward-thinking approach allows them to offer innovative solutions and stay competitive in an increasingly global marketplace.Recently, Molding Work has made headlines with the acquisition of cutting-edge machinery that has bolstered their production capabilities. This investment has allowed them to increase efficiency and quality, further solidifying their position as a leader in the industry. Additionally, they have expanded their workforce, welcoming new talent and expertise to the team, ensuring that they remain at the forefront of molding technology.Furthermore, Molding Work has taken steps to expand their global reach, forging partnerships and collaborations with international clients and suppliers. This strategic approach has opened up new opportunities for growth and diversification, positioning the company for continued success in the years to come.As a testament to their dedication to excellence, Molding Work has received numerous accolades and certifications, further cementing their reputation as a top-tier molding provider. Their commitment to quality, innovation, and sustainability has set them apart in the industry, earning the trust and confidence of clients around the world.Looking ahead, Molding Work shows no signs of slowing down. With a focus on continuous improvement and a dedication to meeting the needs of an ever-changing market, they are poised to maintain their position as a leader in the industry. Their unwavering commitment to excellence and customer satisfaction ensures that they will remain a trusted partner for businesses seeking top-notch molding services.In conclusion, Molding Work’s dedication to quality, innovation, and sustainability has established them as a powerhouse in the manufacturing industry. With a steadfast commitment to meeting and exceeding the needs of their clients, combined with their state-of-the-art facilities and cutting-edge technology, they have proven themselves as a reliable and trustworthy partner for businesses looking to bring their products to life. As they continue to adapt and innovate in a rapidly evolving industry, Molding Work is set to maintain its position as a leader in molding services for years to come.
Learn About Injection Overmolding: What It Is and How It Works
Injection Overmolding: Revolutionizing Plastic ManufacturingIn today's fast-paced and ever-changing world, the demand for high-quality, innovative products is at an all-time high. As a result, manufacturers are continually seeking new and efficient ways to produce top-of-the-line goods that meet the needs and expectations of consumers. One of the latest developments in the field of plastic manufacturing is Injection Overmolding.Injection Overmolding is a cutting-edge process that involves the injection of molten plastic over a pre-formed substrate or insert. This unique method allows for the creation of complex and multi-material parts, resulting in durable, high-performance products. The process begins with the production of a pre-formed component, which serves as the substrate for the overmolding. This component is then placed within a mold cavity, and molten plastic is injected to encapsulate and bond with the pre-formed substrate, creating a seamless and integrated final product.This advanced manufacturing technique offers a wide range of benefits, including improved product durability, enhanced design flexibility, and reduced production costs. Furthermore, Injection Overmolding allows for the integration of multiple materials, such as rubber, metal, and plastic, resulting in parts with superior functionality and performance.One company at the forefront of Injection Overmolding is {}. With a strong commitment to innovation and excellence, {} has become a leader in the field, providing high-quality overmolding solutions to a diverse range of industries, including automotive, electronics, healthcare, and consumer goods.The company's state-of-the-art facilities and cutting-edge technology enable {} to deliver superior overmolding solutions that meet the specific needs and requirements of their clients. From prototype development to full-scale production, {} offers a comprehensive range of services, including design assistance, material selection, and custom tooling, ensuring that each project is tailored to the unique specifications of the customer.With a team of experienced engineers and technicians, {} has the expertise and capabilities to tackle even the most challenging overmolding projects. The company's relentless pursuit of excellence and continuous investment in research and development have positioned {} as a trusted partner for businesses seeking high-quality, innovative overmolding solutions.In addition to its advanced manufacturing capabilities, {} is also committed to sustainability and environmental responsibility. By utilizing efficient production processes and eco-friendly materials, the company strives to minimize its environmental footprint while delivering top-tier products to its customers. With a focus on innovation, quality, and sustainability, {} is paving the way for the future of plastic manufacturing.As the demand for high-performance, multi-material products continues to grow, Injection Overmolding is poised to revolutionize the plastic manufacturing industry. With its ability to create durable, complex, and integrated parts, Injection Overmolding offers a solution that meets the evolving needs of today's consumers and businesses.In conclusion, Injection Overmolding represents the next frontier in plastic manufacturing, and companies like {} are leading the charge in delivering innovative overmolding solutions to a wide range of industries. With its advanced technology, commitment to excellence, and dedication to sustainability, {} is well-positioned to shape the future of plastic manufacturing and continue to meet the evolving needs of its customers.
Expert Guide to 3-Axis CNC Machining: What You Need to Know
{[Company Name] is proud to announce that it has recently invested in state-of-the-art 3 axis CNC machining technology. This investment will allow the company to enhance its manufacturing capabilities and provide more precise and efficient services to its customers.3 axis CNC machining is a cutting-edge technology that enables high-precision manufacturing of various components and parts. The technology utilizes computer numerical control (CNC) to automate the machining process, resulting in superior accuracy and repeatability. This makes it an ideal solution for a wide range of industries, including aerospace, automotive, medical, and more.With the addition of 3 axis CNC machining, [Company Name] will be able to expand its manufacturing capabilities and offer new product lines to its customers. This technology will enable the company to produce complex and intricate components with ease, allowing for greater design flexibility and faster turnaround times.In addition to enhancing its manufacturing capabilities, [Company Name] is also committed to maintaining the highest quality standards. The company takes pride in ensuring that all products meet or exceed industry regulations and customer specifications. With 3 axis CNC machining, [Company Name] will be able to further guarantee the precision and quality of its products, setting a new standard for excellence in the industry.Moreover, [Company Name] has always been dedicated to continuous improvement and technological innovation. By investing in the latest 3 axis CNC machining technology, the company is demonstrating its commitment to staying at the forefront of industry advancements. This will not only benefit the company and its customers, but also contribute to the overall advancement of manufacturing technology.Furthermore, the investment in 3 axis CNC machining technology demonstrates [Company Name]'s dedication to sustainability and efficiency. The technology allows for the optimization of material usage and reduction of waste, contributing to a more environmentally friendly manufacturing process. This aligns with the company's values and commitment to responsible and sustainable business practices.In conclusion, the addition of 3 axis CNC machining technology is a significant milestone for [Company Name]. It represents the company's dedication to providing the highest quality products and services to its customers, as well as its commitment to innovation and sustainability. With this new technology, [Company Name] is poised to elevate its manufacturing capabilities and set new industry standards for precision and efficiency.Stay tuned for more updates as [Company Name] continues to leverage the latest advancements in technology to deliver unparalleled solutions to its customers.About [Company Name]:[Company Name] is a leading manufacturing company that specializes in providing high-quality components and parts to a diverse range of industries. With a focus on precision, quality, and innovation, the company is dedicated to meeting the unique needs of its customers and delivering exceptional products and services. [Company Name] is committed to continuous improvement and invests in cutting-edge technologies to ensure that it remains at the forefront of industry advancements.
Discover a wide range of CNC parts on a reliable platform
CNC Parts Platform Enhances Manufacturing Efficiency for Industries WorldwideIn today's fast-paced and highly competitive manufacturing industry, companies are constantly seeking ways to improve efficiency and streamline their operations. One company at the forefront of this movement is {}, a leading provider of CNC parts and components for a wide range of industries.With a diverse range of high-quality products and a commitment to innovation, {} has become a trusted partner for manufacturers looking to optimize their production processes. Through their comprehensive online platform, customers can easily access a wide selection of CNC parts, including milling machines, lathes, and other essential components.The company's extensive product offerings are designed to meet the diverse needs of manufacturers across various industries, including automotive, aerospace, electronics, and more. By providing a one-stop solution for CNC parts and components, {} is empowering businesses to improve their manufacturing capabilities and stay ahead in an increasingly competitive market.To further enhance the customer experience, {} has implemented advanced search and filtering tools on their website, allowing users to quickly find the specific parts they need for their production processes. This level of accessibility and convenience is a testament to the company's dedication to customer satisfaction and efficiency.In addition to their impressive product range, {} is also known for their commitment to quality and reliability. The company works closely with leading manufacturers to source the best CNC parts and components, ensuring that their customers receive top-notch products that meet the highest standards of performance and durability.Furthermore, {} understands the importance of staying ahead of the curve when it comes to technological advancements in the manufacturing industry. As a result, the company continuously updates their product offerings to include the latest innovations in CNC technology, allowing their customers to benefit from the most cutting-edge solutions available.One of the key advantages of {}'s platform is the ability to provide custom solutions for specific manufacturing requirements. The company's team of experienced professionals is dedicated to working closely with customers to develop tailored solutions that address their unique needs, whether it's a custom machining project or a specialized component for a particular application.By leveraging their extensive expertise and industry knowledge, {} has positioned itself as a trusted partner for manufacturers seeking to enhance their production capabilities and achieve greater efficiency. The company's emphasis on collaboration and customization sets them apart in a competitive market, demonstrating their commitment to going above and beyond for their customers.Looking ahead, {} remains dedicated to driving innovation and supporting the evolving needs of the manufacturing industry. With a focus on quality, reliability, and customer satisfaction, the company is poised to continue making a significant impact on the global manufacturing landscape, empowering businesses to thrive in an increasingly competitive market.As manufacturing continues to evolve, companies like {} are essential partners for businesses looking to optimize their production processes and stay ahead of the curve. With a comprehensive range of high-quality CNC parts and a commitment to innovation, the company is well-positioned to lead the charge in driving efficiency and advancement in the manufacturing industry.
Revolutionizing Rail Industry: The Future of Rail Machining Unveiled
Rail Machining & Company IntroductionRail Machining, a leading provider of rail maintenance solutions, is revolutionizing the rail industry with its cutting-edge technology and innovative solutions. With a commitment to excellence and a focus on delivering exceptional results, Rail Machining has become a trusted partner for many rail operators worldwide.Established in [year], Rail Machining has quickly risen to prominence in the rail industry, thanks to its state-of-the-art equipment and team of highly skilled professionals. The company specializes in providing an array of rail maintenance services, including rail profiling, rail grinding, rail milling, and rail inspection.Rail profiling is an essential process in maintaining the integrity of the railway tracks. Rail Machining utilizes advanced profiling technology to ensure that the rails are perfectly aligned and properly contoured. This precision profiling not only enhances the safety and performance of the tracks but also reduces wear and tear on the rolling stock.Rail grinding is another crucial service offered by Rail Machining. It involves the removal of surface irregularities and defects on the rail, resulting in a smoother and more even surface. This process is essential in preventing accidents caused by rail surface irregularities and reducing noise pollution. Rail Machining's grinding equipment is designed to deliver exceptional results while minimizing downtime and disruption to rail operations.Rail milling is a relatively new method used in rail maintenance. It involves the removal of a thin layer of rail material, resulting in a smoother and more even surface. This process eliminates the need for grinding and provides a longer-lasting solution. Rail Machining's milling technology is at the forefront of the industry, ensuring precise and efficient milling operations.In addition to its maintenance services, Rail Machining offers comprehensive rail inspection solutions. The company's advanced inspection technology can detect various railway defects, such as track misalignment, cracks, and wear. This proactive approach allows rail operators to identify potential issues before they escalate into major problems, reducing the risk of accidents and minimizing maintenance costs.Rail Machining's commitment to excellence extends beyond its cutting-edge technology. The company places a strong emphasis on safety and environmental sustainability. All operations are conducted in compliance with the highest safety standards, and environmentally friendly practices are implemented throughout the entire process. Rail Machining continually invests in research and development to develop innovative, eco-friendly solutions that minimize the environmental impact of rail maintenance.To cater to the global demand for rail maintenance services, Rail Machining has established a wide network of offices and facilities worldwide. With a strong presence in [countries], the company is well-positioned to serve the needs of rail operators in different regions and to provide timely and efficient maintenance solutions.Rail Machining takes pride in its team of experts who possess extensive knowledge and experience in rail maintenance. The company invests in training and development to ensure that its professionals stay up-to-date with the latest industry advancements. This expertise, combined with state-of-the-art technology, allows Rail Machining to deliver exceptional results and exceed customer expectations.As Rail Machining continues to innovate and develop new solutions, the company remains dedicated to its core values of quality, safety, and customer satisfaction. With its commitment to excellence and passion for the rail industry, Rail Machining is well-positioned to shape the future of rail maintenance and contribute to the continued growth and development of the global rail sector.
How Insert Molding is Revolutionizing Manufacturing Processes
Title: Innovative Insert Molding Technology Revolutionizes Manufacturing ProcessesIntroduction:The manufacturing industry continually seeks advanced technologies to increase efficiency, minimize costs, and enhance product performance. One such revolutionary technique is Insert Molding, which combines the benefits of traditional molding techniques with precision insert placement, resulting in enhanced product performance and streamlined manufacturing processes. One company at the forefront of this innovation is {}. With their extensive experience and expertise in insert molding, they are pushing the boundaries of what is possible in the manufacturing industry.Paragraph 1:Insert Molding is a manufacturing process that involves injecting molten materials, such as plastic or metal, into a pre-formed cavity or mold containing one or more carefully positioned inserts. These inserts can be a wide range of components, including threaded inserts, electrical connectors, sensors, or metal reinforcements. The molten material effectively encapsulates the inserts, creating a strong bond between the two, resulting in a more robust and functional end product.Paragraph 2:Insert Molding offers several advantages over traditional manufacturing methods. Firstly, it eliminates the need for additional assembly processes, reducing labor costs and assembly time. By incorporating various inserts directly into the mold, the manufacturing process becomes more streamlined, efficient, and cost-effective. Furthermore, insert molding ensures precise and accurate positioning of the inserts, leading to higher product integrity and reliability.Paragraph 3:The innovation and expertise of {} in the field of insert molding have allowed them to cater to a diverse range of industries, including automotive, electronics, medical, and consumer goods. Their state-of-the-art facilities and skilled engineers enable them to create complex and high-quality molded products with exceptional precision. {} also offers comprehensive design assistance, ensuring that their customers' unique insert molding requirements are met, resulting in tailored solutions that exceed expectations.Paragraph 4:The automotive industry, in particular, has greatly benefited from the utilization of insert molding. By integrating metal inserts into plastic parts, manufacturers achieve significant weight reduction, increased part functionality, and improved overall vehicle performance. Electrical connectors, sensors, and wiring harnesses are seamlessly integrated, simplifying assembly and enhancing reliability. The implementation of insert molding enables automotive manufacturers to produce parts that meet the stringent safety and quality standards of the industry.Paragraph 5:In the ever-evolving electronics industry, where miniaturization and increased functionality are essential, insert molding plays a crucial role. With the ability to place delicate components, such as microchips, sensors, and connectors, with utmost precision, manufacturers can produce smaller and slimmer electronic devices without sacrificing performance. This technique also enhances the devices' durability by protecting fragile components and reducing the risk of damage caused by external factors.Paragraph 6:In the medical industry, insert molding offers numerous benefits in terms of product design, functionality, and sterilization. The ability to encapsulate electronics, sensors, and metal components within a single molded part ensures a seamless integration of various functionalities, such as drug delivery systems, diagnostic equipment, and surgical devices. The use of insert molding in the medical field has resulted in advancements in patient care and treatment efficiency.Conclusion:With its ability to combine diverse materials and precisely position inserts, Insert Molding has revolutionized the manufacturing industry by enhancing product performance, reducing costs, and streamlining production processes. The expertise and cutting-edge solutions provided by {} have solidified their place as industry leaders in insert molding technology. As new advancements continue to be made, the possibilities and applications of Insert Molding are boundless, driving innovation throughout various sectors and shaping the future of manufacturing.
Understanding the Key Components of a CNC Lathe
[Company Introduction: The {Company} is a leading manufacturer of CNC machines, specializing in producing high-quality and innovative machining solutions. With a strong emphasis on research and development, the company has continuously pushed the boundaries of CNC technology, making its machines highly sought after by manufacturers worldwide.]The {Company} has been at the forefront of the CNC machine industry, providing state-of-the-art solutions for manufacturers across various sectors. One of its most notable offerings is the CNC lathe, a versatile machine tool used for shaping metal, wood, or other materials. The CNC lathe is known for its precision, efficiency, and capability to perform a wide range of machining operations.While the CNC lathe is a complex machine, it is composed of several key parts that work together to achieve precise and efficient turning operations. These parts include:1. Bed: The bed is the base of the CNC lathe and provides a stable platform for supporting all other components. It is usually made of high-quality cast iron to ensure rigidity and stability during machining operations.2. Headstock: The headstock houses the main spindle, which is responsible for rotating the workpiece at high speeds. It also contains the gear train, which allows for speed changes and power transmission to the spindle.3. Tailstock: The tailstock is located at the opposite end of the headstock and serves as a support for long workpieces. It can be moved along the bed to accommodate different lengths of materials and can be adjusted to hold the workpiece firmly in place.4. Tool turret: The tool turret holds various cutting tools that are used for shaping the workpiece. It can be indexed to bring different tools into the cutting position, allowing for complex machining operations to be performed without manual tool changes.5. Slide: The slide is responsible for the movement of the cutting tool relative to the workpiece. It consists of a saddle and cross-slide, which can be controlled and programmed to achieve precise cutting dimensions.6. Control panel: The control panel is the interface through which the operator can input commands and program the CNC lathe. It contains a display screen, keyboard, and control buttons, allowing for the input of cutting parameters, tool movements, and other machining instructions.7. Chuck: The chuck is a device used for holding the workpiece securely in place during machining operations. It can be either manual or automatic, and it provides the necessary grip to prevent the workpiece from moving during turning.8. Coolant system: The coolant system is responsible for maintaining the temperature of the cutting tools and workpiece during machining. It also helps to flush away chips and debris, improving the overall surface finish and prolonging tool life.The {Company} has incorporated advanced technologies and innovative design features into its CNC lathes, making them highly efficient and reliable for a wide range of machining applications. With a commitment to quality and precision, the company continues to set the benchmark for CNC machine tools, providing manufacturers with the best-in-class solutions for their production needs.In conclusion, the CNC lathe is a highly versatile and essential machine tool for the manufacturing industry, and its component parts play a crucial role in achieving precise and efficient turning operations. The {Company} has been at the forefront of CNC lathe technology, offering advanced solutions that meet the evolving needs of manufacturers worldwide. With a focus on innovation and quality, the company has established itself as a leader in the CNC machine industry, providing cutting-edge solutions that enhance productivity and efficiency in manufacturing operations.
The Ultimate Guide to CNC: Everything You Need to Know
As a leader in the CNC industry, {} has consistently demonstrated its commitment to innovation and excellence. The company has been at the forefront of developing cutting-edge CNC technology, providing state-of-the-art solutions to its customers. Recently, {} has launched a new CNC guide that is set to revolutionize the way operators interact with CNC machines.The new CNC guide is an advanced software system that provides a user-friendly interface for operating CNC machines. It is designed to simplify the programming and operation of CNC equipment, making it more accessible to a wider range of users. With its intuitive design and advanced features, the CNC guide enables operators to perform complex tasks with ease, ultimately improving productivity and efficiency in manufacturing processes.One of the key features of the new CNC guide is its comprehensive library of pre-programmed templates and tool paths. This library allows operators to quickly and accurately program CNC machines without the need for extensive manual input. This not only saves time but also reduces the potential for errors, ensuring a higher level of precision in the machining process.In addition, the CNC guide incorporates advanced visualization tools that provide operators with real-time feedback on the machining process. This includes 3D simulations of tool paths and cutting operations, allowing operators to visually inspect and optimize their programs before running them on the machine. This level of visual feedback enhances the overall machining experience, giving operators greater control over the end result.Furthermore, the new CNC guide is equipped with smart sensors and monitoring capabilities that continuously track the performance of the CNC machine. This allows operators to detect any issues or anomalies in the machining process, enabling them to take corrective action in real time. As a result, machine downtime is minimized, and the overall reliability of the CNC system is significantly improved.The launch of the new CNC guide is a testament to {}'s ongoing dedication to creating innovative solutions that drive progress in the CNC industry. By leveraging the latest advancements in software and technology, {} is empowering its customers to achieve new levels of efficiency and precision in their manufacturing operations.In a statement, the CEO of {} expressed his enthusiasm for the new CNC guide, highlighting its potential to transform the way CNC machines are operated. He emphasized the company's commitment to continuous improvement and stated that the CNC guide is just one example of {}'s ongoing efforts to push the boundaries of what is possible in CNC technology.Customers who have had the opportunity to test the new CNC guide have already provided positive feedback, noting its user-friendly interface and powerful capabilities. Many have expressed their excitement about the potential impact of this technology on their own manufacturing processes, recognizing the significant benefits it offers in terms of productivity and quality.Looking ahead, {} plans to continue refining and expanding the capabilities of the CNC guide, with a focus on further enhancing its ease of use and performance. The company remains dedicated to maintaining its position as a trusted partner for CNC solutions, providing its customers with the tools they need to succeed in today's competitive manufacturing environment.In conclusion, the launch of the new CNC guide represents a major milestone for the CNC industry, and {} is proud to be at the forefront of this innovation. By combining its expertise in CNC technology with a commitment to excellence, {} has once again demonstrated its ability to deliver cutting-edge solutions that empower its customers to achieve greater success. The CNC guide is poised to make a significant impact on the way CNC machines are operated, setting a new standard for efficiency and precision in manufacturing.