Custom Molding Services: A Comprehensive Guide to Molding Work
By:Admin
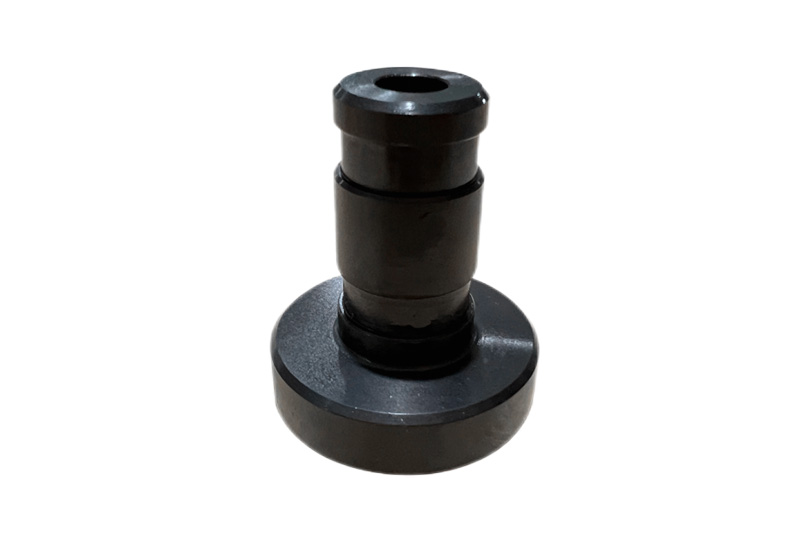
Molding Work is a leading company in the field of mold manufacturing, specializing in the production of high-quality molds for various industries. With a strong focus on precision and efficiency, Molding Work has established itself as a premier destination for businesses in need of top-notch molds.
Founded in 1995, Molding Work has been at the forefront of innovation in mold manufacturing for over 25 years. The company's dedication to excellence and commitment to meeting the diverse needs of its clients have earned it a stellar reputation in the industry. Whether it's a simple prototype or a complex, multi-cavity mold, Molding Work has the expertise and experience to deliver exceptional results.
The company's state-of-the-art facility is equipped with the latest technology, allowing it to provide a wide range of mold manufacturing services. From design and engineering to mold testing and validation, Molding Work's comprehensive capabilities ensure that its clients receive molds of the highest quality. In addition, the company's team of highly skilled engineers and technicians are dedicated to delivering precision-engineered molds that meet the exact specifications of its clients.
Molding Work's commitment to quality is evident in its rigorous quality control processes. The company adheres to the highest industry standards and uses advanced inspection equipment to ensure that every mold meets the strictest quality requirements. This unwavering dedication to quality has earned Molding Work the trust and loyalty of its clients, who rely on the company for their most critical mold manufacturing needs.
In addition to its technical expertise, Molding Work is also known for its exceptional customer service. The company works closely with its clients throughout the entire mold manufacturing process, providing regular updates and addressing any concerns in a timely and professional manner. This commitment to customer satisfaction has solidified Molding Work's position as a trusted partner for businesses in need of high-quality molds.
As a forward-thinking company, Molding Work is constantly investing in research and development to stay ahead of the curve in mold manufacturing. The company's team of experts is continuously exploring new technologies and techniques to improve its processes and enhance the performance of its molds. This commitment to innovation ensures that Molding Work remains at the forefront of the industry, offering its clients the most advanced and efficient mold solutions.
With its unwavering commitment to excellence, technical expertise, and exceptional customer service, Molding Work has become the go-to destination for businesses seeking top-quality molds. Whether it's for the automotive, medical, consumer goods, or any other industry, clients can trust Molding Work to deliver molds that meet their exact requirements and exceed their expectations.
In conclusion, Molding Work's dedication to quality, innovation, and customer satisfaction sets it apart as a leader in the mold manufacturing industry. The company's long-standing reputation for excellence, combined with its comprehensive capabilities and commitment to staying ahead of the curve, make it the premier destination for high-quality molds. Businesses in need of top-notch molds can rely on Molding Work to deliver exceptional results, every time.
Company News & Blog
Efficient Methods for Machining Large Parts Unveiled
Machining Large Parts: Revolutionizing Manufacturing with Precision and EfficiencyIn today's ever-evolving world of manufacturing, precision and efficiency remain the utmost priority for businesses. As industries continue to push the boundaries of innovation, the demand for machining large parts has soared remarkably. One company, known for its commitment to excellence and cutting-edge technology, has emerged as a leader in this field, providing innovative solutions that are revolutionizing the manufacturing industry. With a strong focus on pushing the limits of what is possible, this company has consistently delivered exceptional results. Through state-of-the-art facilities and a team of skilled professionals, they have perfected the art of machining large parts. Equipped with advanced CNC machines and a diverse range of cutting tools, they have the capability to manufacture components of extraordinary size and complexity, meeting the most stringent specifications and requirements of their clients.Harnessing the immense potential of computer-aided design (CAD) and computer-aided manufacturing (CAM), this company has paved the way for precision machining on an unprecedented scale. By utilizing powerful software solutions, they are able to seamlessly translate digital designs into tangible products, utilizing a streamlined and highly efficient process. This allows for increased accuracy and repeatability, ensuring that every machined part is an exact replica of the original design.One of the key advantages this company offers is their ability to handle large parts without compromising on quality. Their state-of-the-art machining centers can accommodate components that weigh up to several tons, demonstrating their commitment to tackling even the most ambitious projects. By integrating cutting-edge technology with extensive knowledge and experience, they have eliminated the traditional limitations associated with machining large parts, opening up new possibilities for manufacturers across various industries.The company's dedication to excellence and innovation is further exemplified by their team of highly skilled engineers and technicians. With a deep understanding of the intricacies of machining large parts, they meticulously plan and execute each project, ensuring that every component meets the highest standards of quality. Their expertise extends beyond conventional methodologies, allowing them to develop customized solutions that address the unique challenges presented by each project.Furthermore, this company's commitment to sustainable practices sets them apart from their competitors. By leveraging advanced manufacturing techniques, such as near-net-shape machining and optimal material utilization, they reduce waste and minimize environmental impact. Additionally, they prioritize the use of recyclable materials, further contributing to a greener and more sustainable future.The applications of these machined large parts span across various industries, including aerospace, automotive, energy, and heavy machinery. From manufacturing precision-engineered components for aircraft engines to producing critical automotive components, this company's expertise and capabilities are highly sought-after by manufacturers worldwide.In conclusion, the demand for machining large parts continues to rise in today's competitive manufacturing landscape. This company, with its dedication to excellence, innovation, and sustainability, is at the forefront of this revolution. Through the utilization of advanced technology, a skilled workforce, and a commitment to exceptional quality, they have redefined what is possible in precision machining of large parts. As industries continue to evolve, they will undoubtedly remain a driving force in shaping the future of manufacturing, enabling businesses to achieve greater precision and efficiency in their operations.
The Drawbacks of Sand Casting: What You Need to Know
Sand casting is a widely used manufacturing process across various industries, including automotive, aerospace, and construction. This process involves pouring molten metal into a sand mold, allowing it to solidify, and then removing the sand mold to reveal the final product. While sand casting offers numerous advantages, such as cost-effectiveness and the ability to produce complex shapes, it also comes with several disadvantages that can impact the quality and efficiency of the final product.One of the main disadvantages of sand casting is the potential for defects in the final product. The use of sand molds can result in surface irregularities, such as rough finishes and sand inclusion, which can affect the overall appearance and functionality of the part. In addition, the cooling process of the molten metal within the sand mold can lead to internal defects, such as porosity and shrinkage cavities, further compromising the integrity of the product.Furthermore, sand casting is not suitable for high precision manufacturing. The dimensional accuracy of sand cast parts is limited, and intricate details may not be reproduced with the same level of precision as other manufacturing processes, such as CNC machining or 3D printing. This can be a significant drawback for industries that require tight tolerances and precise specifications for their components.In terms of production efficiency, sand casting has its limitations as well. The process requires the creation of a new sand mold for each casting, which can be time-consuming and labor-intensive. Additionally, the sand molds have a limited lifespan and can only be used for a certain number of castings before they need to be replaced, adding to the overall production costs and lead times.Environmental concerns are also a factor to consider when it comes to sand casting. The disposal of used sand molds and the emissions generated during the casting process can have a negative impact on the environment. It is essential for companies to implement proper waste management and environmental protection measures to mitigate the potential harm caused by sand casting operations.Despite these disadvantages, sand casting continues to be a widely used manufacturing process, especially for large and complex parts that may be difficult or costly to produce using alternative methods. As a leading manufacturer in the industry, {} recognizes the importance of understanding the drawbacks of sand casting and aims to address these challenges through innovative solutions and advanced technologies.{} has established itself as a pioneer in the manufacturing sector, specializing in the production of high-quality components for a wide range of industries. With a strong focus on research and development, {} continuously seeks to improve its manufacturing processes and minimize the limitations associated with traditional methods, such as sand casting.Through the integration of advanced simulation software and additive manufacturing technologies, {} is able to optimize the design and production of sand molds, reducing the occurrence of defects and improving dimensional accuracy. This approach not only enhances the quality of the final products but also streamlines the production process, resulting in shorter lead times and increased efficiency.Furthermore, {} is committed to sustainability and environmental responsibility. By implementing eco-friendly practices, such as reusing and recycling sand molds, reducing waste generation, and investing in energy-efficient equipment, the company strives to minimize its ecological footprint and contribute to a cleaner, greener future.In conclusion, while sand casting has its disadvantages, its widespread use in various industries cannot be overlooked. As a leading manufacturer, {} recognizes the challenges associated with this traditional manufacturing process and is dedicated to overcoming them through innovation, technology, and a commitment to sustainability. By addressing the limitations of sand casting, {} aims to deliver superior products that meet the highest standards of quality, precision, and efficiency, setting new benchmarks in the manufacturing industry.
High-Quality Machining Components: Essential for Precision Manufacturing
Machining Components, a leading precision engineering company, is making a significant impact in the manufacturing industry with its advanced machining technology and high-quality components. With a strong focus on innovation and customer satisfaction, Machining Components has quickly become a trusted partner for businesses looking to enhance their manufacturing operations.Established in [year], Machining Components has built a solid reputation for delivering top-notch machining solutions to a wide range of industries, including aerospace, automotive, medical, and defense. The company's state-of-the-art facility is equipped with the latest CNC machines, robotic automation, and advanced inspection tools, allowing them to produce complex components with the highest degree of precision and accuracy.At the core of Machining Components' success is its team of highly skilled engineers and technicians who are dedicated to pushing the boundaries of machining technology. Through ongoing training and professional development, the company ensures that its staff is always up to date with the latest industry trends and best practices. This commitment to excellence has enabled Machining Components to consistently meet and exceed the expectations of its clients.Machining Components offers a wide range of machining services, including milling, turning, grinding, and EDM, to accommodate various customer requirements. Whether it's prototyping, small-batch production, or high-volume manufacturing, the company has the expertise and capabilities to deliver exceptional results. Additionally, Machining Components is well-versed in working with a variety of materials, including aluminum, steel, titanium, and exotic alloys, further expanding its capacity to handle diverse projects.One of the key differentiators of Machining Components is its dedication to quality control and assurance. The company has implemented rigorous inspection and testing protocols throughout the manufacturing process to ensure that every component meets the highest standards of accuracy and performance. By adhering to stringent quality management systems, Machining Components has been able to consistently deliver parts that not only meet but often exceed industry specifications.In addition to its commitment to precision engineering, Machining Components places a strong emphasis on building long-term partnerships with its clients. The company works closely with its customers from the initial concept stage through to the final production, providing valuable technical expertise and support along the way. This collaborative approach has earned Machining Components a solid reputation for excellence and reliability in the manufacturing community.Furthermore, Machining Components is deeply invested in sustainability and environmentally friendly practices. The company has implemented various initiatives to reduce waste, conserve energy, and minimize its environmental impact. Through responsible manufacturing processes, Machining Components is not only contributing to a healthier planet but also helping its clients meet their own sustainability goals.As Machining Components continues to grow and evolve, it remains committed to being at the forefront of machining technology and innovation. The company regularly invests in research and development to explore new techniques and technologies that can further enhance its capabilities and offerings. By staying ahead of the curve, Machining Components is poised to continue driving advancements in the manufacturing industry.In conclusion, Machining Components is a forward-thinking precision engineering company that has established itself as a leader in the manufacturing sector. With its cutting-edge technology, unwavering commitment to quality, and customer-centric approach, the company is well-positioned to meet the evolving needs of its clients and contribute to the advancement of the industry as a whole. As Machining Components continues to push the boundaries of what's possible in machining, it is poised to make an even greater impact in the years to come.
Expert Tips for Machining Metal: The Ultimate Guide for Precision Metalwork
Title: Revolutionizing Metal Machining: Company X Introduces Cutting-Edge InnovationIntroduction:In the dynamic world of metal machining, Company X has emerged as a leading pioneer, focusing on elevating precision and efficiency to new heights. With their unwavering commitment to research and development, they have introduced groundbreaking technologies that are poised to revolutionize the industry. In this article, we delve into Company X's latest innovation in machining metal, its features, and the potential implications on industries worldwide.Enhancing Precision and Efficiency:Building on their expertise in metal machining, Company X has unveiled a cutting-edge technology that promises enhanced precision and efficiency in the manufacturing process. By combining advanced robotics, artificial intelligence, and state-of-the-art algorithms, their innovation ensures unrivaled accuracy and repeatability.The integration of robotics enables Company X to carry out intricate machining tasks with unprecedented precision. These robots are equipped with advanced sensors that constantly monitor the machining process, making real-time adjustments to ensure optimal results. Moreover, with the use of artificial intelligence, the machines are capable of learning and adapting, further improving their precision over time.Additionally, Company X's innovation incorporates proprietary algorithms, specifically designed to optimize machining parameters. By analyzing vast amounts of data generated during the machining process, these algorithms can identify the ideal conditions for different applications. This results in reduced waste, improved surface finishes, and increased overall efficiency.Addressing Cost and Time Constraints:Recognizing the time and cost implications involved in traditional metal machining processes, Company X's new technology aims to alleviate these concerns. With their advanced automation systems, machining processes are streamlined, eliminating manual errors and reducing human intervention. This automation not only saves time but also minimizes labor costs, ultimately enhancing cost-effectiveness for businesses.Moreover, Company X's technology enables a significant reduction in lead times. By implementing predictive maintenance through continuous monitoring, downtime due to machinery failures is minimized. Consequently, businesses can maintain optimal productivity, meeting tight delivery deadlines without compromising on quality.Application across Industries:Company X's innovation transcends the constraints of a single industry. This breakthrough technology is applicable across diverse sectors such as automotive, aerospace, medical, and electronics, just to name a few.In the automotive sector, for instance, precision machining is crucial for the production of engine components, ensuring optimal performance and longevity. With Company X's technology, manufacturers can achieve unparalleled precision, resulting in improved efficiency, reduced friction, and lower emissions.Likewise, in the aerospace industry, where precision and safety are paramount, Company X's innovation brings unparalleled advantages. From manufacturing turbine blades to intricate structural components, their technology guarantees precise tolerances, which are critical for aircraft performance and passenger safety.Looking Ahead:With their latest innovation in metal machining, Company X has showcased their dedication to pushing the boundaries of what is possible. This advanced technology not only enhances precision and efficiency but also addresses cost and time constraints, positioning Company X as a trailblazer in the industry.As businesses across industries seek to stay competitive in a rapidly changing market, Company X's technology presents a compelling solution. By embracing this revolutionary approach to metal machining, businesses can unlock new levels of productivity, quality, and profitability.In conclusion, Company X has boldly redefined the metal machining landscape with its cutting-edge innovation. As this technology becomes more widespread, it has the potential to transform industries worldwide by revolutionizing the production process, streamlining operations, and elevating the standards of precision and efficiency.
DIY Plastic Injection Molding: How to Set Up Your Own Molding Station at Home
Home plastic injection molding has become a popular and cost-effective way for hobbyists and small businesses to produce their own plastic products. With the use of a desktop injection molding machine, individuals can create custom plastic parts in the comfort of their own home, without the need for expensive industrial machinery.One company that has made a name for itself in the home plastic injection molding industry is {}. They have designed and manufactured a compact and user-friendly injection molding machine that is perfect for beginners and experienced molders alike. This machine allows users to produce high-quality plastic parts using a variety of thermoplastic materials, including ABS, PE, and PVC.With the increasing demand for custom plastic parts, home injection molding is quickly gaining traction as a viable alternative to traditional manufacturing methods. The ability to create small to medium-sized batches of plastic parts at home provides individuals with a level of flexibility and control that is not possible with larger-scale production methods. This has led to a surge in interest from small businesses, makers, and industry professionals who are looking for a cost-effective and efficient way to produce plastic parts.One of the key advantages of home plastic injection molding is the ability to iterate on designs quickly and cost-effectively. With a desktop injection molding machine, individuals can test and refine their designs in a matter of hours, rather than waiting weeks for samples to be produced by a third-party manufacturer. This allows for greater innovation and creativity in the product development process, as well as the ability to respond quickly to changes in market demand.In addition to the machine, {Company} also offers a range of support and training materials for home molders. Their website features a wealth of resources, including tutorials, troubleshooting guides, and design tips, to help individuals get the most out of their injection molding machine. They also provide ongoing technical support to ensure that users are able to overcome any challenges they may encounter during the molding process.As the home plastic injection molding industry continues to grow, {Company} is at the forefront of innovation and development in this space. Their commitment to providing high-quality, user-friendly machines and comprehensive support services has made them a trusted name in the industry. With a focus on accessibility and affordability, they are helping to democratize the plastic manufacturing process, making it accessible to a wide range of individuals and businesses.The future of home plastic injection molding looks bright, with more and more individuals and businesses recognizing the value of this innovative manufacturing method. As technology continues to advance, and the barriers to entry continue to lower, we can expect to see even greater adoption of home injection molding in the years to come. With companies like {Company} leading the way, the possibilities for custom plastic part production are endless.
Top 5 Tips for CNC Metalworking Success
CNC Metalworking Company Leads the Industry with Cutting-Edge TechnologyIn the ever-evolving world of metalworking, one company is at the forefront of innovation and technological advancement. With a strong commitment to precision, quality, and efficiency, CNC Metalworking has established itself as a leader in the industry. Founded in the early 2000s, CNC Metalworking has quickly risen to prominence due to its dedication to providing exceptional metalworking solutions to a diverse range of industries. The company's state-of-the-art facility is equipped with the latest in CNC technology, allowing for the production of complex and intricate metal components with unparalleled accuracy and speed.One of the key factors that sets CNC Metalworking apart from its competitors is its investment in cutting-edge technology. The company continuously invests in new equipment and software to ensure that it remains at the forefront of the industry. This commitment to innovation has enabled CNC Metalworking to take on a wide variety of projects, from small-scale prototypes to large-scale production runs, all with the same level of precision and attention to detail.In addition to its technological prowess, CNC Metalworking places a strong emphasis on quality control and customer satisfaction. Each project undergoes rigorous testing and inspection to ensure that it meets the highest standards of quality and accuracy. Furthermore, the company prides itself on its ability to work closely with clients to understand their specific needs and deliver customized solutions that exceed expectations.Furthermore, CNC Metalworking's team of highly skilled and experienced engineers and machinists are dedicated to pushing the boundaries of what is possible in the world of metalworking. Their collective expertise and passion for their craft enable CNC Metalworking to tackle even the most complex and challenging projects with confidence and precision.One of the standout features of CNC Metalworking's capabilities is its ability to work with a wide range of materials, including steel, aluminum, titanium, and various alloys. This versatility allows the company to cater to the diverse needs of its clients, whether they operate in aerospace, automotive, medical, or any other industry that requires high-quality metal components.In addition to its impressive capabilities, CNC Metalworking is also committed to sustainability and environmental responsibility. The company has implemented a range of initiatives to reduce waste, minimize energy consumption, and minimize its environmental footprint.Looking ahead, CNC Metalworking is poised to continue its trajectory of success and growth. With a steadfast commitment to innovation, quality, and customer satisfaction, the company is well-positioned to lead the industry and set new standards for metalworking excellence.In conclusion, CNC Metalworking's dedication to investing in cutting-edge technology, maintaining the highest standards of quality control, and fostering a team of passionate and skilled professionals has enabled it to emerge as a leader in the metalworking industry. As the company continues to push the boundaries of what is possible in the world of metalworking, it is poised to remain at the forefront of the industry for years to come.
What You Need to Know About Large CNC Machine Sizes
The demand for precision engineering and manufacturing continues to grow as industries seek to innovate and streamline production processes. In response to this demand, ** Company ** has announced the launch of their new CNC machine size, designed to meet the evolving needs of the industry.The new CNC machine size represents a significant step forward in the company's commitment to providing cutting-edge solutions for precision engineering and manufacturing. With a focus on versatility, efficiency, and accuracy, the CNC machine size offers a wide range of capabilities to meet the diverse needs of modern manufacturing operations.One of the key features of the new CNC machine size is its impressive accuracy and precision. Equipped with advanced technology and state-of-the-art controls, the machine is capable of producing intricate and complex parts with exceptional accuracy. This level of precision is essential for industries such as aerospace, automotive, and medical devices, where even the slightest deviation can have significant implications for performance and safety.In addition to its precision, the CNC machine size also offers a high level of versatility. Equipped with a range of tooling options and advanced programming capabilities, the machine is able to accommodate a wide variety of production needs. This flexibility is particularly valuable for manufacturers who need to adapt to changing demands and produce a diverse range of parts and components.Efficiency is another key focus of the new CNC machine size. With rapid tool change and high-speed machining capabilities, the machine is able to optimize production processes and minimize downtime. This not only improves productivity and throughput but also reduces operational costs, making it an attractive investment for manufacturers looking to enhance their competitive edge.The launch of the new CNC machine size reflects ** Company's ** commitment to innovation and continuous improvement. With a strong reputation for delivering high-quality precision engineering solutions, the company has a long history of meeting and exceeding the needs of its clients. The introduction of the new CNC machine size further strengthens ** Company's ** position as a leading provider of advanced manufacturing technology.In addition to its technical capabilities, ** Company ** is also known for its exceptional customer service and support. With a team of experienced engineers and technicians, the company is able to provide comprehensive training, installation, and ongoing maintenance to ensure that clients get the most out of their investment in the new CNC machine size. This level of support is crucial for manufacturers who rely on their equipment to deliver consistent and reliable performance.The launch of the new CNC machine size comes at a time when the demand for precision engineering and manufacturing solutions is higher than ever. With industries seeking to improve efficiency, reduce costs, and enhance quality, the new CNC machine size represents a valuable asset for manufacturers looking to stay ahead of the curve. As the industry continues to evolve, ** Company ** remains at the forefront of innovation, providing cutting-edge solutions to meet the changing needs of modern manufacturing.
Different types of metal casting methods used in manufacturing industries
Metal Casting Methods: Innovations in ManufacturingMetal casting has been a fundamental process in the manufacturing industry for centuries. From fabricating small components to producing large industrial parts, metal casting methods play a crucial role in the production of a wide range of goods. With the advancements in technology and innovation, the metal casting industry has witnessed significant improvements in its processes and techniques, leading to higher efficiency, precision, and quality in the finished products.One of the key players in the metal casting industry is {}. With a strong reputation for excellence in metal casting, the company has been at the forefront of implementing innovative methods in its manufacturing processes. By combining traditional craftsmanship with modern technology, {} has been able to stay ahead of the competition and continue to meet the ever-evolving needs of its clients.One of the most significant developments in metal casting methods has been the introduction of advanced 3D printing technology. This cutting-edge technique allows for the creation of intricate metal parts with unparalleled precision and complexity. By using 3D printing in metal casting, companies like {} can produce components that were previously impossible to manufacture using traditional methods. The ability to create complex geometries and intricate designs has expanded the possibilities for manufacturers in various industries, from aerospace and automotive to medical and energy.In addition to 3D printing, {} has also been investing in automation and robotics to streamline its metal casting processes. By integrating robotics into its production line, the company has been able to improve efficiency, reduce labor costs, and enhance overall quality control. Automation has also proven to be invaluable in handling hazardous tasks, minimizing workplace accidents, and ensuring a safer working environment for its employees.Furthermore, {} has been actively exploring sustainable and eco-friendly metal casting methods. With a growing emphasis on environmental responsibility, the company has been investing in research and development to find ways to minimize waste, reduce energy consumption, and lower its carbon footprint. By implementing sustainable practices in its metal casting processes, {} is not only contributing to a greener planet but also appealing to a growing market of environmentally conscious consumers.Another notable advancement in metal casting methods is the use of advanced modeling and simulation software. By leveraging cutting-edge software tools, {} can optimize its casting designs, simulate various scenarios, and identify potential issues before they occur. This proactive approach to problem-solving has resulted in significant cost savings, reduced lead times, and improved overall product quality.The future of metal casting methods looks promising, and {} is well-positioned to lead the way in driving innovation and excellence in the industry. With a strong commitment to staying at the forefront of technological advancements, the company continues to invest in research and development to further enhance its capabilities and offerings.As the global demand for high-quality metal components continues to rise, the role of metal casting methods in meeting these demands becomes increasingly crucial. With {}'s dedication to innovation, sustainability, and excellence, the company is poised to play a significant role in shaping the future of metal casting. By embracing new technologies, refining its processes, and prioritizing customer satisfaction, {} is paving the way for a new era of metal casting methods that are more efficient, sustainable, and precise than ever before.In conclusion, metal casting methods have come a long way, thanks to the relentless pursuit of innovation and improvement by companies like {}. As the manufacturing industry continues to evolve, metal casting will undoubtedly remain a cornerstone of production, and the advancements in its methods will continue to drive progress and shape the future of manufacturing.
Discover the Top Features of Cnc Machines for Precision Manufacturing
The use of CNC (Computer Numerical Control) machines has become increasingly popular in the manufacturing industry due to their high precision and efficiency. This technology has revolutionized the way products are made, and companies are constantly looking for the latest features and improvements to enhance their production capabilities. One company that has been at the forefront of CNC machine development is {} Company. With a rich history in the manufacturing industry, {} has established itself as a leader in producing cutting-edge CNC machines that are tailored to meet the evolving needs of the market.One of the standout features of {}'s CNC machines is their advanced control system. The machines are equipped with state-of-the-art software that allows for seamless integration with CAD/CAM systems, enabling users to create intricate designs and easily convert them into machining programs. This level of automation not only streamlines the production process but also reduces the margin for error, resulting in higher quality finished products.In addition, {}'s CNC machines boast superior cutting capabilities. The machines are equipped with high-speed spindles and multi-axis machining capabilities, allowing for complex and precise cuts on various materials. This level of versatility makes {}'s machines suitable for a wide range of industries, from automotive and aerospace to medical and electronics.Furthermore, {}'s CNC machines are built with robust and durable components, ensuring consistent and reliable performance. The machines undergo rigorous testing to ensure they can withstand the demands of heavy-duty machining operations, giving users peace of mind in their investment.Another key feature of {}'s CNC machines is their user-friendly interface. The machines are designed with intuitive controls and a user-friendly interface, making them accessible to operators of varying skill levels. This accessibility, combined with comprehensive training and support from {}'s team, ensures that users can maximize the potential of the machines and achieve optimal results.With a global presence, {} Company has a strong track record of delivering high-quality CNC machines to clients around the world. Their commitment to innovation and excellence has made them a trusted partner for companies looking to enhance their manufacturing capabilities.In conclusion, the latest features of {}'s CNC machines, combined with their extensive industry experience and commitment to excellence, make them a standout choice for companies seeking to elevate their production capabilities. With a focus on precision, efficiency, and reliability, {}'s CNC machines are well-positioned to meet the evolving needs of the manufacturing industry and drive the next wave of innovation in production technology.
The Power of Plastic Rapid Prototyping: Advantages and Applications
Plastic Rapid Prototyping: Revolutionizing Product DevelopmentIn today's fast-paced and highly competitive manufacturing industry, companies are constantly seeking ways to streamline their product development process in order to bring high-quality products to market in a timely manner. One company at the forefront of this movement is [Company Name], a leading provider of plastic rapid prototyping solutions.[Company Name] has built a solid reputation for delivering innovative and cutting-edge rapid prototyping and tooling solutions to a wide range of industries, including automotive, aerospace, medical, and consumer goods. Their state-of-the-art facilities and advanced technologies allow them to offer a comprehensive suite of prototyping services, including 3D printing, injection molding, CNC machining, and more.One of the key offerings that sets [Company Name] apart from its competitors is their plastic rapid prototyping capabilities. This process allows for the quick and cost-effective production of prototype parts and components using a variety of plastic materials. By leveraging advanced 3D printing technologies, [Company Name] is able to produce highly accurate and functional prototypes in a fraction of the time it would take using traditional methods.The benefits of plastic rapid prototyping are numerous. Not only does it significantly reduce the time and cost associated with traditional prototyping methods, but it also allows for greater design flexibility and iteration. This means that companies can quickly test and refine their product designs, leading to faster innovation and a more efficient product development cycle.Furthermore, plastic rapid prototyping enables companies to quickly respond to market demands and changes, giving them a competitive edge in today's fast-moving business landscape. With the ability to rapidly produce high-quality prototypes, companies can bring new products to market faster, allowing them to capitalize on emerging trends and customer needs.[Company Name] is committed to staying at the forefront of plastic rapid prototyping technology, continually investing in the latest equipment and software to ensure they can meet the evolving needs of their customers. Their team of highly skilled engineers and technicians are dedicated to providing top-quality prototyping solutions, working closely with clients to bring their concepts to life with precision and efficiency.Through their plastic rapid prototyping capabilities, [Company Name] has helped countless companies accelerate their product development process and bring innovative solutions to market. Whether it's creating prototypes for new product designs, testing out custom components, or producing low-volume production runs, [Company Name] is a trusted partner for companies looking to push the boundaries of what's possible in product development.As the manufacturing industry continues to evolve, the demand for rapid and cost-effective prototyping solutions is only expected to grow. [Company Name] is well-positioned to meet this demand, offering a wide range of plastic rapid prototyping services tailored to the specific needs of their clients.In conclusion, plastic rapid prototyping is revolutionizing the way companies approach product development, and [Company Name] is leading the charge with their advanced prototyping capabilities. By leveraging the latest technologies and a commitment to innovation, they are helping companies across industries bring their ideas to life faster and more efficiently than ever before.With a focus on quality, precision, and customer satisfaction, [Company Name] is poised to continue making a significant impact in the world of plastic rapid prototyping, driving forward the next generation of product development.