Benefits of CNC Machining for Brass Components
By:Admin
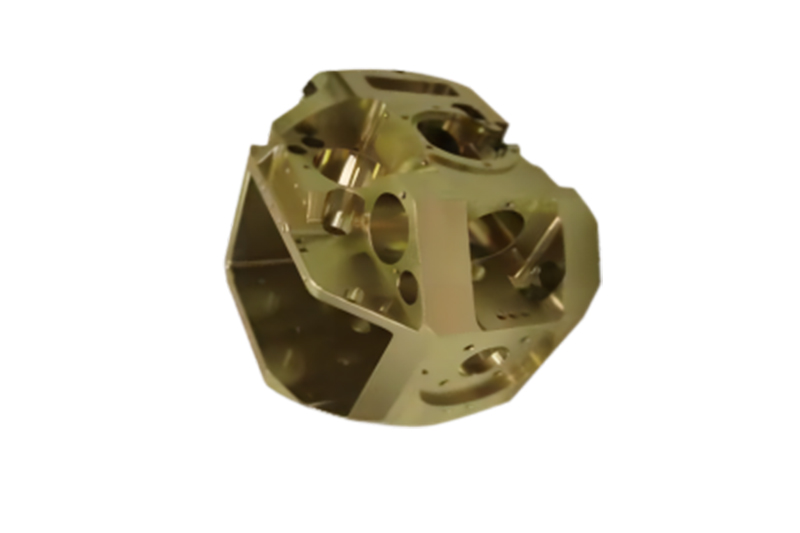
CNC machining brass is a critical process in the manufacturing industry, and it plays a significant role in the production of high-precision metal parts. Whether it is a small component for a medical device or a complex part for an aerospace application, CNC machining brass ensures that the final product meets the required specifications and standards. With the advancement of technology and the increasing demand for precision parts, the need for reliable and efficient CNC machining services has become more important than ever.
One company that has established itself as a leader in the CNC machining industry is {}. With years of experience and a commitment to quality and customer satisfaction, {} has become a trusted partner for businesses across various industries. The company's state-of-the-art facilities and skilled workforce enable them to handle complex projects with ease, delivering precision parts that meet the highest standards.
The process of CNC machining brass involves using computer-controlled machines to accurately cut, shape, and finish brass materials. The precision and accuracy of CNC machining allow for the production of intricate and custom-designed parts that would be impossible to achieve with traditional machining methods. This level of precision is crucial in industries where the performance and reliability of the final product are paramount.
Another advantage of CNC machining brass is the ability to produce parts with tight tolerances and fine surface finishes. This is essential in applications where the functionality of the part depends on its precise dimensions and surface quality. With CNC machining, the production of such parts is not only possible but also cost-effective, making it the preferred method for businesses looking to achieve the highest level of quality in their products.
Furthermore, CNC machining brass offers a high level of repeatability and consistency, ensuring that every part produced is identical to the next. This is particularly important in industries such as aerospace and automotive, where the interchangeability of components is critical. The ability to produce parts with consistent dimensions and features is a key factor in ensuring the overall quality and performance of the final product.
In addition to precision and consistency, CNC machining brass also offers flexibility in terms of design and customization. With the use of computer-aided design (CAD) software, businesses can create complex and intricate part designs that would be impractical or impossible to produce with traditional machining methods. This flexibility allows businesses to innovate and push the boundaries of what is possible in their respective industries.
As a leading provider of CNC machining services, {} understands the importance of staying at the forefront of technological advancements. The company continually invests in the latest CNC machining equipment and software to ensure that they can meet the evolving needs of their customers. This commitment to innovation has enabled {} to take on a wide range of projects, from small-scale production runs to large and complex parts for some of the most demanding applications.
With a focus on quality, precision, and customer satisfaction, {} has built a reputation as a reliable and trustworthy partner for businesses seeking CNC machining brass services. Their dedication to meeting and exceeding the expectations of their customers has solidified their position as a leader in the industry.
In conclusion, CNC machining brass is a critical process in the manufacturing of precision parts, and businesses across various industries rely on it to produce high-quality components. With the expertise and capabilities of companies like {}, businesses can be confident that their CNC machining needs will be met with the highest level of quality and professionalism. As technology continues to advance, CNC machining brass will undoubtedly play an even more significant role in the production of precision parts, driving innovation and excellence in the manufacturing industry.
Company News & Blog
Top Tips for Choosing the Best Material Casting for Your Project
Material Casting, a well-known leader in the industrial casting industry, has announced its latest advancements in technology and expansion of its facilities to meet the growing demands of its global clientele. With a focus on innovation and quality, Material Casting has remained a key player in the market for over [X] years, consistently delivering top-notch solutions for a wide range of industries including automotive, aerospace, and energy.The company's commitment to excellence is evident in its state-of-the-art facilities, equipped with the latest machinery and technology to ensure precision and efficiency in the casting process. Material Casting employs a team of highly skilled engineers and technicians who continuously push the boundaries of what is possible in the industry, utilizing advanced materials and techniques to deliver superior products.In addition to its commitment to technological advancement, Material Casting is also dedicated to sustainability and environmental responsibility. The company has implemented eco-friendly practices in its production processes, minimizing waste and maximizing energy efficiency. This focus on sustainability has not only reduced the company's environmental impact, but has also led to cost savings that are passed on to customers, making Material Casting a competitive and attractive choice for businesses worldwide.The expansion of Material Casting's facilities is a testament to the company's continued growth and success in the industry. The new facilities will allow for increased production capacity, enabling Material Casting to take on larger and more complex projects while maintaining its high standards of quality and precision. Additionally, the company plans to further invest in research and development, with the goal of introducing groundbreaking innovations that will revolutionize the casting industry and exceed customer expectations.When asked about the expansion and the future of Material Casting, [CEO Name] expressed his optimism and excitement for the company's prospects. "We are thrilled to be taking this next step in our journey," [CEO Name] said. "The expansion of our facilities represents not only our commitment to meeting the needs of our clients, but also our confidence in the future of the industry. We are continuously striving to push the boundaries of what is possible in casting technology, and we are eager to see what the future holds for Material Casting."Material Casting's dedication to excellence, innovation, and sustainability has solidified its position as a leading provider of casting solutions in the global market. The company's expansion and advancements in technology will undoubtedly further strengthen its standing, allowing it to continue meeting the evolving needs of its customers while remaining at the forefront of the industry.As Material Casting continues to make strides in the casting industry, its commitment to quality, innovation, and sustainability distinguishes it as a trusted and reliable partner for businesses seeking top-tier casting solutions. With a focus on continuous improvement and customer satisfaction, Material Casting is poised to remain a driving force in the industry for years to come.
Achieve Precision Results with 4 Axis CNC Milling Services
In the world of manufacturing and engineering, precision and efficiency are crucial components for success. This is particularly true in the field of CNC milling, where the ability to produce complex and intricate parts with speed and accuracy is essential. This is where the advanced technology of 4-axis CNC milling comes into play, and one company at the forefront of this innovation is {}.{} is a leading provider of advanced manufacturing solutions, specializing in CNC milling, turning, and grinding processes. With a strong focus on quality, efficiency, and customer satisfaction, the company has established itself as a trusted partner for businesses across a wide range of industries. With a commitment to staying ahead of the curve in terms of technological advancements, {} has recently invested in the acquisition of state-of-the-art 4-axis CNC milling equipment, further solidifying its position as a leader in the industry.The introduction of 4-axis CNC milling technology represents a significant leap forward in the capabilities of {}’s manufacturing processes. This advanced equipment allows for the simultaneous movement of the cutting tool along four different axes, enabling a higher level of precision and complexity in the parts that can be produced. By expanding the range of motion and cutting angles, 4-axis CNC milling opens up new possibilities for the creation of intricate and detailed components that would be difficult or impossible to achieve with traditional 3-axis milling machines.One of the key benefits of 4-axis CNC milling is the ability to reduce the number of setups required to machine a part. With the additional axis of movement, {} can perform more operations in a single setup, reducing the time and effort required to produce a finished component. This not only streamlines the manufacturing process but also improves overall accuracy and repeatability, leading to higher-quality finished products.Furthermore, the advanced capabilities of 4-axis CNC milling allow {} to take on a wider range of projects and meet more diverse customer needs. From complex geometries to intricate designs, the expanded capabilities of the new equipment enable {} to push the boundaries of what is possible in terms of precision and complexity. This positions the company to better serve industries such as aerospace, automotive, medical, and beyond, where intricate and high-precision parts are in high demand.In addition to the technological advantages, {} is also leveraging its extensive expertise and experience in CNC milling to maximize the potential of the new 4-axis equipment. The company’s team of skilled machinists and engineers are adept at programming and operating the advanced machinery, ensuring that they can fully harness its capabilities to deliver exceptional results for their clients. This combination of cutting-edge technology and skilled craftsmanship sets {} apart as a leader in the CNC machining industry.With the addition of 4-axis CNC milling capabilities, {} is poised to continue its trajectory of growth and success in the manufacturing and engineering sectors. By staying at the forefront of technological advancements and continuously improving its capabilities, the company has positioned itself as a go-to partner for businesses seeking high-quality, high-precision manufacturing solutions. As industries continue to demand ever more complex and intricate components, {}’s investment in 4-axis CNC milling technology ensures that it will remain a trusted and reliable resource for companies across a wide range of sectors.
Creating an Injection Mold: A Step-by-Step Guide
Title: Manufacturing Company Pioneers Effortless Injection Mold Creation ProcessIntroduction:{Company Name}, a leading manufacturing company, is revolutionizing the industry with their innovative approach to creating injection molds. With their cutting-edge technology and commitment to excellence, they are streamlining the production process for numerous industries. The company's recent advancements have paved the way for more efficient and cost-effective mold creation, ensuring faster turnaround times without compromising on quality or precision.Body:1. Introduction to Injection Molds:Injection molds are an essential component in the production of a wide range of plastic and metal parts. These molds are created to meet specific requirements, with intricate designs and precise dimensions. Traditionally, manufacturing injection molds was a time-consuming and costly process, often causing delays and skyrocketing production costs.2. Streamlined Process for Injection Mold Creation:{Company Name} has developed an innovative solution that simplifies the injection mold creation process. By leveraging the latest technologies and expertise, they have reduced the turnaround time while upholding the highest quality standards. Their streamlined process greatly benefits clients from various industries, including automotive, medical, and consumer goods.3. Customization and Design:One of the key features of {Company Name}'s injection mold creation process is its ability to provide customizable designs. They work closely with clients to understand their unique requirements, ensuring that every mold is tailored to their specific needs. The company's team of experts utilizes advanced software and tools to translate clients' ideas into flawless designs, guaranteeing optimal functionality and durability.4. Enhanced Precision and Quality Control:With their state-of-the-art technology and advanced manufacturing techniques, {Company Name} ensures precision to the finest detail in every injection mold they produce. The company's commitment to quality control is evident throughout the entire manufacturing process. Rigorous testing and inspection procedures are implemented to guarantee that each mold meets or exceeds industry standards before it is released to clients.5. Reduced Time and Cost Savings:{Company Name}'s accelerated injection mold creation process significantly reduces the lead time compared to traditional methods. By cutting down on waiting periods and optimizing production efficiency, clients can initiate their manufacturing processes sooner, thereby reducing downtime and costs. This advantage allows businesses to bring their products to market more rapidly, gaining a competitive edge.6. Sustainable Manufacturing Practices:In addition to their commitment to efficiency and quality, {Company Name} is dedicated to sustainable manufacturing practices. The company employs environmentally-friendly materials and processes wherever possible, prioritizing renewable resources and waste reduction. By adopting these practices, they contribute to a greener future while serving the needs of their clients.7. Dedicated Customer Support:{Company Name} prides itself on providing exceptional customer support throughout the mold creation process. Their team of experts collaborates closely with clients, offering guidance and support as needed. From the initial design phase to post-production assistance, the company ensures that clients have a smooth and hassle-free experience, fostering long-term partnerships built on trust and reliability.Conclusion:{Company Name}'s groundbreaking injection mold creation process sets a new standard for the manufacturing industry. Their commitment to precision, quality control, customization, and sustainability is revolutionizing the way molds are produced. With their shorter lead times, cost savings, and dedicated customer support, {Company Name} continues to transform the industry, enabling businesses to thrive in today's fast-paced market while maintaining the highest standards of quality and efficiency.
The Benefits of Cnc Molding for Manufacturing Operations
CNC Molding Technology Enhances Manufacturing CapabilitiesWith the increasing demand for high-quality, precision parts in various industries, the need for advanced manufacturing technology has become more important than ever. One company that is making strides in this area is {}.{} is a leading manufacturer of precision machined components for a wide range of industries, including aerospace, automotive, medical, and more. The company has been at the forefront of manufacturing innovation, constantly investing in new technologies to improve its capabilities and meet the demands of its customers.One of the key technologies that {} has recently adopted is CNC molding. This advanced manufacturing process allows for the production of highly complex and intricate parts with exceptional precision and efficiency. With CNC molding, {} is able to produce parts with tight tolerances and intricate geometries that would be impossible to achieve with traditional machining methods.CNC molding works by using computer-aided design (CAD) software to create a digital model of the part to be manufactured. This digital model is then used to program a CNC machine, which uses cutting tools to shape the raw material into the desired form. The result is a highly accurate and consistent part, produced with minimal waste and at a fraction of the time it would take with traditional manufacturing methods.The adoption of CNC molding has allowed {} to expand its capabilities and offer a wider range of products to its customers. The company now has the ability to produce complex components such as gears, impellers, and turbine blades with unmatched precision and efficiency. This has not only expanded the company's customer base but also allowed it to take on more challenging projects in industries where precision is critical.In addition to its CNC molding capabilities, {} has also invested in state-of-the-art quality control systems to ensure that all parts meet the highest standards. This dedication to quality has earned the company a reputation for producing parts that meet or exceed the stringent requirements of its customers, especially in industries where safety and reliability are paramount.The adoption of CNC molding technology has also had a positive impact on {}'s operations. By streamlining the manufacturing process and reducing the need for manual labor, the company has been able to significantly increase its production capacity and reduce lead times. This has allowed {} to better meet the demands of its customers and take on larger orders with confidence.Looking ahead, {} is committed to staying at the forefront of manufacturing technology and continuing to invest in the latest advancements in CNC molding and other manufacturing processes. The company sees these investments as a way to better serve its customers and continue to grow its business in the highly competitive manufacturing industry.In conclusion, the adoption of CNC molding technology has greatly enhanced {}'s manufacturing capabilities, allowing the company to produce high-quality, precision parts with unmatched efficiency. With its commitment to innovation and quality, {} is well-positioned to continue meeting the demands of its customers and taking on new challenges in the ever-evolving manufacturing landscape.
How Insert Molding is Revolutionizing Manufacturing Processes
Title: Innovative Insert Molding Technology Revolutionizes Manufacturing ProcessesIntroduction:The manufacturing industry continually seeks advanced technologies to increase efficiency, minimize costs, and enhance product performance. One such revolutionary technique is Insert Molding, which combines the benefits of traditional molding techniques with precision insert placement, resulting in enhanced product performance and streamlined manufacturing processes. One company at the forefront of this innovation is {}. With their extensive experience and expertise in insert molding, they are pushing the boundaries of what is possible in the manufacturing industry.Paragraph 1:Insert Molding is a manufacturing process that involves injecting molten materials, such as plastic or metal, into a pre-formed cavity or mold containing one or more carefully positioned inserts. These inserts can be a wide range of components, including threaded inserts, electrical connectors, sensors, or metal reinforcements. The molten material effectively encapsulates the inserts, creating a strong bond between the two, resulting in a more robust and functional end product.Paragraph 2:Insert Molding offers several advantages over traditional manufacturing methods. Firstly, it eliminates the need for additional assembly processes, reducing labor costs and assembly time. By incorporating various inserts directly into the mold, the manufacturing process becomes more streamlined, efficient, and cost-effective. Furthermore, insert molding ensures precise and accurate positioning of the inserts, leading to higher product integrity and reliability.Paragraph 3:The innovation and expertise of {} in the field of insert molding have allowed them to cater to a diverse range of industries, including automotive, electronics, medical, and consumer goods. Their state-of-the-art facilities and skilled engineers enable them to create complex and high-quality molded products with exceptional precision. {} also offers comprehensive design assistance, ensuring that their customers' unique insert molding requirements are met, resulting in tailored solutions that exceed expectations.Paragraph 4:The automotive industry, in particular, has greatly benefited from the utilization of insert molding. By integrating metal inserts into plastic parts, manufacturers achieve significant weight reduction, increased part functionality, and improved overall vehicle performance. Electrical connectors, sensors, and wiring harnesses are seamlessly integrated, simplifying assembly and enhancing reliability. The implementation of insert molding enables automotive manufacturers to produce parts that meet the stringent safety and quality standards of the industry.Paragraph 5:In the ever-evolving electronics industry, where miniaturization and increased functionality are essential, insert molding plays a crucial role. With the ability to place delicate components, such as microchips, sensors, and connectors, with utmost precision, manufacturers can produce smaller and slimmer electronic devices without sacrificing performance. This technique also enhances the devices' durability by protecting fragile components and reducing the risk of damage caused by external factors.Paragraph 6:In the medical industry, insert molding offers numerous benefits in terms of product design, functionality, and sterilization. The ability to encapsulate electronics, sensors, and metal components within a single molded part ensures a seamless integration of various functionalities, such as drug delivery systems, diagnostic equipment, and surgical devices. The use of insert molding in the medical field has resulted in advancements in patient care and treatment efficiency.Conclusion:With its ability to combine diverse materials and precisely position inserts, Insert Molding has revolutionized the manufacturing industry by enhancing product performance, reducing costs, and streamlining production processes. The expertise and cutting-edge solutions provided by {} have solidified their place as industry leaders in insert molding technology. As new advancements continue to be made, the possibilities and applications of Insert Molding are boundless, driving innovation throughout various sectors and shaping the future of manufacturing.
Advanced Rail Machining Techniques and Services for Enhanced Performance
Rail Machining, a leading provider of railway maintenance and repair services, has recently announced a new partnership with a major railway company in an effort to expand its services and reach a wider customer base. The partnership will allow Rail Machining to leverage its expertise in railway maintenance and repair, while also benefiting from the extensive infrastructure and resources of the railway company.Rail Machining has been in the railway maintenance and repair industry for over 20 years, and has built a strong reputation for its high-quality services and cutting-edge technology. The company offers a wide range of services, including rail grinding, rail milling, and wheel reprofiling, all of which are essential for maintaining the safety and efficiency of railway tracks and rolling stock.The new partnership will allow Rail Machining to expand its services to new regions and customers, while also providing the railway company with access to Rail Machining's expertise and technology. This collaboration is expected to have a significant impact on the railway industry, as it will improve the efficiency and safety of railway operations, while also reducing maintenance costs for the railway company.In addition to the partnership, Rail Machining is also investing in new technology and equipment to further enhance its services. The company has recently acquired a state-of-the-art rail milling machine, which is capable of removing defects and imperfections from railway tracks with unprecedented precision. This advanced technology will allow Rail Machining to provide even more efficient and effective maintenance services, further solidifying its position as a leader in the railway maintenance and repair industry."We are thrilled to announce our new partnership with the railway company," said the CEO of Rail Machining. "This collaboration represents a major milestone for our company, and we are excited about the opportunities it presents. By combining our expertise and technology with the resources of the railway company, we will be able to provide even better services to our customers and contribute to the overall efficiency and safety of the railway industry."Rail Machining's commitment to innovation and excellence has made it a trusted partner for railway companies around the world. The company's dedication to providing high-quality services and cutting-edge technology has earned it a reputation as a leader in the railway maintenance and repair industry. With this new partnership and the acquisition of advanced technology, Rail Machining is well-positioned to continue its growth and make a significant impact on the railway industry.As the railway industry continues to evolve and expand, the demand for efficient and effective maintenance and repair services is greater than ever. Rail Machining's new partnership and investment in technology will allow the company to meet this demand and continue to be a reliable and trusted partner for railway companies worldwide. With its industry-leading expertise and state-of-the-art technology, Rail Machining is poised to further solidify its position as a leader in the railway maintenance and repair industry.
High-Quality Machined Aluminium: A Durable and Sturdy Material for Various Applications
Machined Aluminium, a leading manufacturer of high-quality aluminum products, has announced the launch of its new line of precision-machined aluminum components. With over 20 years of experience in the industry, Machined Aluminium has built a reputation for delivering top-notch products that meet the stringent requirements of various industries, including aerospace, automotive, and electronics.The new line of precision-machined aluminum components has been specifically designed to meet the growing demand for lightweight, yet durable components in various applications. With advancements in technology and manufacturing processes, Machined Aluminium has been able to produce components that offer superior strength-to-weight ratios and excellent resistance to corrosion, making them ideal for use in demanding environments."Our new line of precision-machined aluminum components represents a significant advancement in our capabilities and offerings," said [company spokesperson]. "We have invested heavily in state-of-the-art machinery and equipment to ensure that we can meet the exacting requirements of our customers. From complex geometries to tight tolerances, our components are designed to deliver outstanding performance in a wide range of applications."The precision-machined aluminum components from Machined Aluminium are available in various grades of aluminum, including 6061, 7075, and 2024, each offering unique properties that make them suitable for different applications. In addition, the components can be further enhanced through various surface treatments, such as anodizing and powder coating, to provide added protection and aesthetic appeal.Machined Aluminium's commitment to quality is evident in its stringent quality control processes, which ensure that each component meets the highest standards before it leaves the facility. Utilizing advanced inspection equipment and techniques, the company is able to verify the dimensional accuracy and surface finish of each component, providing customers with the confidence that they are receiving products of the highest caliber.In addition to its focus on quality, Machined Aluminium is also dedicated to sustainability and environmental stewardship. The company has implemented various initiatives to minimize its environmental impact, such as optimizing its manufacturing processes to reduce waste and energy consumption. Furthermore, the aluminum used in its products is fully recyclable, contributing to a circular economy and reducing the reliance on finite resources.Machined Aluminium's new line of precision-machined aluminum components has already garnered significant interest from customers in various industries. The company's reputation for excellence, combined with its ability to deliver custom solutions tailored to specific requirements, has positioned it as a preferred supplier for many leading organizations."We are excited about the potential that our new line of precision-machined aluminum components holds," said [company spokesperson]. "We have already received positive feedback from customers who have seen the benefits of using our components in their applications. We are confident that our products will continue to make a significant impact in the industries we serve."As Machined Aluminium continues to push the boundaries of what is possible with aluminum, the company remains committed to innovation, quality, and customer satisfaction. With its new line of precision-machined aluminum components, Machined Aluminium is poised to further solidify its position as a key player in the aluminum manufacturing industry, providing solutions that meet the evolving needs of modern engineering and design.
A guide to understanding CNC machine programming and operation
In a world of constantly evolving technology, the use of Computer Numerical Control (CNC) machines has become increasingly essential in the manufacturing industry. These machines are programmed to perform precision tasks such as cutting, milling, and drilling with incredible accuracy and efficiency. One company that has been at the forefront of the CNC machine industry is {}.{} is a leading manufacturer of CNC machines, known for their cutting-edge technology and high-quality products. With a commitment to innovation and customer satisfaction, the company has established itself as a trusted name in the industry. Their CNC machines are utilized in a wide range of applications, from small-scale production to large-scale manufacturing, and have earned a reputation for their reliability and precision.One of the key features of {}'s CNC machines is their versatility. Whether it's a simple drilling operation or a complex multi-axis milling task, their machines are equipped to handle a variety of tasks with ease. This flexibility allows manufacturers to streamline their production processes and enhance overall efficiency.In addition to their superior performance, {} also places a strong emphasis on user-friendly design. Their CNC machines are equipped with intuitive controls and user interfaces, making them accessible to operators of all skill levels. This focus on usability ensures that manufacturers can maximize the potential of their machines without extensive training or technical expertise.The CNC machines manufactured by {} are also known for their durability and longevity. Constructed with high-quality materials and components, these machines are built to withstand the rigors of continuous operation in demanding manufacturing environments. This reliability minimizes downtime and maintenance costs, allowing manufacturers to operate with confidence and peace of mind.Furthermore, {} is dedicated to staying at the forefront of technological advancements in the CNC machine industry. They consistently invest in research and development to integrate the latest advancements into their products, ensuring that their customers have access to the most cutting-edge technology available. This commitment to innovation sets {} apart as a leader in the industry, and positions them as a go-to resource for manufacturers seeking the best CNC solutions.One example of {}'s commitment to innovation is their integration of smart technology into their CNC machines. By incorporating features such as real-time monitoring, predictive maintenance, and remote diagnostics, their machines empower manufacturers to optimize their production processes and maximize efficiency. With these smart capabilities, manufacturers can proactively address potential issues and minimize downtime, ultimately improving their bottom line.In conclusion, the role of CNC machines in the manufacturing industry cannot be overstated, and {} has established itself as a top-tier provider of these essential tools. With a dedication to quality, innovation, and customer satisfaction, {}'s CNC machines have become synonymous with reliability, precision, and efficiency. As manufacturing technology continues to advance, {} remains at the forefront, constantly pushing the boundaries of what is possible with CNC technology. For manufacturers seeking a trusted partner in their quest for excellence, {} stands out as the company to turn to for all their CNC machine needs.
Unlocking the Power of 4-Axis CNC Milling: Exploring Advanced Machining Capabilities
Title: Enhancing Precision and Productivity with Advanced 4-Axis CNC Milling TechnologyIntroduction:In a rapidly evolving manufacturing landscape, companies across industries are constantly seeking innovative solutions to maximize precision and productivity. One such advancement that has garnered significant attention is the incorporation of 4-axis CNC milling technology. This cutting-edge technique allows for the creation of intricately designed parts and components with unparalleled precision, efficiency, and versatility. Today, we delve into the world of 4-axis CNC milling, exploring its remarkable capabilities and the ways in which it revolutionizes the manufacturing process, propelling industries into a new era of growth and competitiveness.Revolutionizing Manufacturing with 4-Axis CNC Milling:Traditionally, milling was a manual process that involved removing material from a workpiece with rotary cutters. However, with the advent of computer numerical control (CNC) machining, the process has been completely transformed. CNC milling utilizes pre-programmed computer software instructions that precisely control cutter movement and material removal, resulting in consistent and accurate machining operations. While 3-axis CNC milling has served the industry well, the incorporation of a fourth axis significantly expands the capabilities of this technology.The 4th axis, often referred to as the A-axis, enables the milling cutter to rotate around the X-axis, allowing for the creation of complex geometries and the machining of undercuts, bevels, and other intricate features. This added versatility opens up a myriad of possibilities for manufacturers, facilitating the production of more complex and aesthetically appealing components.Enhanced Precision and Efficiency:With 4-axis CNC milling, manufacturers can achieve unparalleled precision and accuracy. The rotational capabilities of the A-axis enable the machine to approach the workpiece from various angles, reducing the need for multiple setups. This not only saves time but also minimizes errors associated with manual repositioning. The result is faster production cycles, improved part quality, and reduced scrap rates, ultimately leading to increased cost-effectiveness and customer satisfaction.Furthermore, 4-axis CNC milling technology excels in machining complex curves, contours, and profiles, ensuring consistency across multiple parts. With the ability to perform intricate operations in a single setup, manufacturers can accelerate production while maintaining the highest level of precision, meeting the demands of even the most intricate designs.Versatility Across Industries:The applications of 4-axis CNC milling span a wide range of industries, benefiting from its inherent precision and flexibility. In the aerospace sector, this technology is instrumental in the production of engine components, turbine blades, and aircraft structural parts, which require intricate machining and strict adherence to tolerances. Similarly, in the automotive industry, companies utilize 4-axis CNC milling for machining engine blocks, cylinder heads, and transmission components.Medical practitioners also rely on 4-axis CNC milling to fabricate complex dental implants, prosthetics, and surgical instruments. The versatility of 4-axis CNC milling technology allows manufacturers to cater to the evolving needs of various industries, providing customized solutions that meet the highest standards of quality and precision.Conclusion:As industries continue to push the boundaries of innovation, the integration of 4-axis CNC milling technology has become an increasingly vital aspect of the manufacturing process. The enhanced precision, efficiency, and versatility offered by this cutting-edge technology propel industries to new heights, ensuring accelerated production cycles, improved part quality, and increased customer satisfaction. With its ability to machine intricate geometries and complex designs, 4-axis CNC milling paves the way for the future of precision manufacturing, revolutionizing industries and strengthening their competitive edge in the global market.
Top Applications of Injection Molding Technology Unveiled
Injection Molding Application: Advancing Manufacturing ProcessesIn the ever-evolving world of manufacturing, injection molding has emerged as an indispensable process for mass production of plastic components. Its wide range of applications and remarkable efficiency have made it a go-to solution for various industries. One company leading the way in this field is {}. With their cutting-edge technology and innovative approach, they have been revolutionizing the injection molding industry.Injection molding is a manufacturing process that involves injecting molten material, typically plastic, into a mold cavity. Once the material cools and solidifies, it takes the desired shape and can be ejected from the mold. This process is highly efficient, allowing for the rapid production of intricate and uniform parts. It is ideal for manufacturing items such as automotive components, consumer goods, medical devices, and packaging materials.{} is a pioneering company in the field of injection molding, constantly pushing the boundaries of what is possible. They have developed advanced equipment and techniques that have revolutionized the manufacturing processes of their clients. Through their dedication to innovation, they have not only improved product quality but also reduced production costs, making injection molding an accessible solution for businesses of all sizes.One of the key strengths of {} lies in their expertise in designing and manufacturing molds. The quality and precision of the molds are crucial in ensuring the final product meets the required specifications. {} employs state-of-the-art design software and utilizes the latest machining techniques to create molds with unmatched precision and durability. Their team of engineers works closely with clients to understand their specific needs and develop molds tailored to their unique requirements.Another notable feature of {} is their commitment to sustainability. In a world increasingly concerned about environmental impact, {} has taken substantial steps to minimize the ecological footprint of their manufacturing processes. They utilize eco-friendly materials and implement energy-efficient practices to ensure their operations are as sustainable as possible. By making environmentally conscious choices, {} sets an example for other companies in the industry, demonstrating that efficient manufacturing can be achieved without compromising the planet's well-being.{} also prides itself on its dedication to quality control. They have implemented rigorous procedures to guarantee the highest level of quality throughout the manufacturing process. Each product undergoes thorough inspections and tests to ensure it meets the required standards. By maintaining strict quality control measures, {} has gained the trust and satisfaction of their clients, positioning themselves as a reliable and dependable partner in the injection molding industry.Furthermore, {} recognizes the importance of staying at the forefront of technological advancements. They continuously invest in research and development to improve their equipment and processes. By embracing automation and utilizing cutting-edge technologies, such as robotics and artificial intelligence, {} optimizes production efficiency and reduces human error. This emphasis on innovation enables them to exceed customer expectations and remain a leader in the injection molding industry.Notably, the success of {} is not only built on their technological advancements, but also on their team of skilled professionals. They take pride in fostering a supportive and creative work environment that encourages employees to unleash their full potential. This culture of collaboration and continuous learning results in highly motivated and dedicated staff who strive for excellence in every project.In conclusion, injection molding has revolutionized the manufacturing industry, and {} has emerged as a key player in this field. Through their innovative technologies, commitment to sustainability, and dedication to quality control, they have set a new standard for injection molding companies. As they continue to push the boundaries of what is possible, {} remains at the forefront of advancing manufacturing processes, revolutionizing the way products are made.