Advanced CNC Machine Technology for Increased Precision and Efficiency
By:Admin
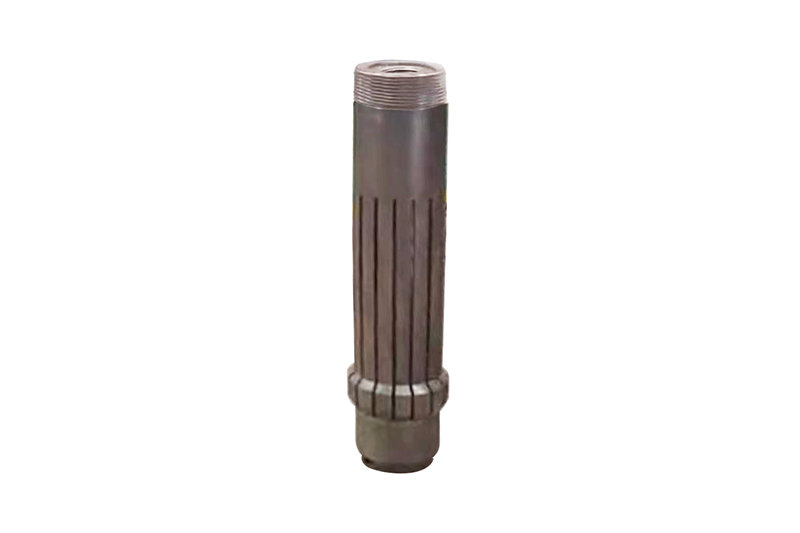
In today's modern manufacturing industry, efficiency and precision are essential in producing high-quality products. The advent of CNC (Computer Numerical Control) machine technology has revolutionized the way manufacturers approach production, leading to increased productivity, reduced costs, and higher quality products.
CNC machines have become an integral part of the manufacturing process, allowing for automated and precise machining of various materials, including metal, plastic, and wood. These machines are operated by computer programs that control the movement and operation of the cutting tools, resulting in highly accurate and consistent production.
One of the leading providers of CNC machine technology, {}, has been at the forefront of innovation in this field. With a comprehensive range of CNC machines and cutting-edge technology, they have been empowering manufacturers to achieve greater efficiency and precision in their production processes.
The company's CNC machines are equipped with advanced features such as multi-axis control, automatic tool changers, and high-speed machining capabilities, allowing for complex and intricate parts to be manufactured with ease. Furthermore, their CNC systems are designed to be user-friendly, with intuitive interfaces and programming software that streamline the production process.
The introduction of CNC machine technology has significantly reduced the reliance on manual labor in manufacturing, leading to increased productivity and higher output levels. Additionally, the precision and accuracy of CNC machines have resulted in a decrease in material waste and rework, leading to cost savings for manufacturers.
With the integration of CAD (Computer-Aided Design) and CAM (Computer-Aided Manufacturing) software, CNC machines can produce complex and intricate parts with ease. This synergy between design and production has allowed for rapid prototyping and shorter lead times, enabling manufacturers to bring their products to market faster.
The widespread adoption of CNC machine technology has also opened up new possibilities in terms of customization and variability in manufacturing. With the ability to easily reprogram CNC machines, manufacturers can quickly adjust production parameters to accommodate design changes or fulfill custom orders, providing greater flexibility in the production process.
Furthermore, the advancements in CNC machine technology have also led to improvements in the overall quality of manufactured products. The precision and consistency of CNC machining result in higher quality parts, reducing the likelihood of defects and errors in production.
The impact of CNC machine technology extends beyond just the manufacturing industry. With the ability to produce parts with high precision and accuracy, CNC machines have found applications in various industries, including aerospace, automotive, medical, and consumer goods.
As the demand for high-quality and complex parts continues to grow, the role of CNC machine technology in manufacturing will only become more prominent. With continued advancements in automation, connectivity, and artificial intelligence, the future of CNC machining is poised to further revolutionize the manufacturing industry.
In conclusion, CNC machine technology has reshaped the landscape of manufacturing, empowering manufacturers to achieve higher levels of efficiency, precision, and quality in their production processes. The advancements made by companies like {} have propelled the industry into a new era of manufacturing, where automation, customization, and innovation are driving forces. As we look to the future, the influence of CNC machine technology in manufacturing will continue to grow, shaping the way products are designed, produced, and brought to market.
Company News & Blog
Ultimate Guide to Understanding CNC Mill Spindle Technology
, introducing the latest advancements in CNC mill spindle technology and its impact on the manufacturing industry.The advancements in CNC mill spindle technology have significantly contributed to the efficiency and precision of manufacturing processes across various industries. A CNC mill spindle serves as the powerhouse of a milling machine, providing the rotational power necessary to cut and shape materials with accuracy and speed. With the continual evolution of technology, companies are constantly striving to improve the performance and capabilities of CNC mill spindles to meet the growing demand for high-quality products.{Company} has been at the forefront of developing cutting-edge CNC mill spindles that are reliable, efficient, and capable of delivering exceptional performance. With a strong focus on research and development, the company has consistently pushed the boundaries of spindle technology to provide innovative solutions for the manufacturing industry. Their commitment to quality and precision has solidified their position as a leading supplier of CNC mill spindles to a wide range of industries, including automotive, aerospace, medical, and consumer electronics.The latest breakthrough in CNC mill spindle technology offered by {Company} is the introduction of their new {model} spindle series. This new series of spindles is designed to deliver unparalleled speed, accuracy, and durability, making it an ideal choice for high-speed machining applications. With advanced features such as high-torque capabilities, enhanced thermal stability, and improved dynamic performance, the {model} spindle series is poised to revolutionize the way manufacturers approach their milling operations.One of the key innovations of the {model} spindle series is its ability to achieve higher spindle speeds without compromising on stability and precision. This is made possible through the integration of advanced cooling technologies and precision-balanced components, ensuring that the spindle operates at optimal performance levels even during prolonged machining operations. As a result, manufacturers can expect a significant increase in productivity and a reduction in cycle times, ultimately leading to a more efficient and cost-effective production process.Additionally, the {model} spindle series incorporates smart sensor technology that monitors crucial performance parameters in real-time, allowing for predictive maintenance and diagnostics. This proactive approach to spindle maintenance helps to prevent unexpected downtime and prolong the lifespan of the spindle, ultimately reducing maintenance costs and increasing overall equipment effectiveness (OEE).Furthermore, {Company}'s {model} spindle series is designed to be compatible with a wide range of milling machines, offering manufacturers the flexibility to integrate this advanced spindle technology into their existing operations without the need for extensive modifications. This flexibility, combined with the spindle's high-performance capabilities, makes it a highly versatile solution for manufacturers seeking to enhance the capabilities of their machining processes.The introduction of the {model} spindle series represents a significant milestone in the evolution of CNC mill spindle technology. With its unparalleled speed, precision, and reliability, this new series of spindles has the potential to reshape the manufacturing landscape, empowering companies to produce complex and high-quality components with efficiency and confidence.In conclusion, {Company} continues to demonstrate its leadership in the development of CNC mill spindle technology with the introduction of their new {model} spindle series. This latest innovation is poised to set new standards for performance and reliability in the manufacturing industry, offering manufacturers a competitive edge in today's demanding market. As the industry continues to evolve, {Company} remains committed to pushing the boundaries of spindle technology and providing cutting-edge solutions that drive the success of their customers.
High-Quality Machined Aluminum Parts Making Waves in the Industry
Title: Precision Solutions Unveils High-Quality Machined Aluminum PartsIntroduction:Precision Solutions has made significant strides in the world of precision manufacturing, and it is now set to revolutionize the industry with its latest release – a wide range of high-quality machined aluminum parts. These parts, meticulously crafted by the company’s skilled engineers, are manufactured to meet the most stringent performance and quality standards. In this article, we will delve into the features and applications of these cutting-edge machined aluminum parts.1. Unparalleled Precision and Quality:Precision Solutions, renowned for its commitment to excellence, has spared no effort in producing machined aluminum parts that are second to none. Each part undergoes an extensive process, starting from the selection of premium-grade aluminum alloys. With a keen eye for detail and state-of-the-art machinery, the company ensures that every part is manufactured to precise specifications, meeting the highest quality standards.2. Diverse Range of Applications:The versatility of Precision Solutions' machined aluminum parts is key to their widespread use across various industries. From aerospace and automotive to electronics and medical equipment manufacturing, these parts find an array of applications. With their excellent corrosion resistance, lightweight design, and exceptional strength-to-weight ratio, they offer unparalleled performance, making them an ideal choice for numerous end-use applications.3. Unmatched Durability and Reliability:One of the foremost attributes of Precision Solutions' machined aluminum parts is their ability to withstand demanding operating conditions. The company utilizes advanced manufacturing techniques, including CNC machining, to ensure that these parts possess remarkable durability and reliability. With their superior mechanical properties and resistance to wear and tear, these parts promise a prolonged lifespan, reducing maintenance costs for end-users.4. Tailored Solutions for Specific Requirements:Understanding the diversity of industry needs, Precision Solutions offers customized machined aluminum parts, designed to meet specific requirements. Leveraging their extensive experience and technical expertise, the company's engineers collaborate closely with clients to develop bespoke solutions. Whether customers require prototypes or large-scale production, Precision Solutions can cater to various demands, providing tailor-made parts promptly and efficiently.5. Adherence to Environmental Standards:Precision Solutions is not only committed to delivering exceptional products but also to maintaining a sustainable manufacturing process. The production of their machined aluminum parts adheres to strict environmental standards, ensuring minimal waste generation and the utilization of eco-friendly materials. By upholding green manufacturing practices, the company underscores its commitment to protecting the environment.6. Continuous Research and Development:To remain at the forefront of the precision manufacturing industry, Precision Solutions invests heavily in research and development. By exploring the latest materials, technologies, and manufacturing processes, the company aims to continuously enhance the performance and quality of its machined aluminum parts. This commitment to innovation allows Precision Solutions to meet and surpass industry expectations, ensuring customer satisfaction.Conclusion:Precision Solutions' latest release of high-quality machined aluminum parts showcases the company's unwavering dedication to precision manufacturing. With their exceptional durability, reliability, and customized solutions, these parts are poised to revolutionize a wide range of industries. The company's commitment to sustainability and continuous improvement further cements its position as a leader in the industry. As Precision Solutions continues to push the boundaries of precision engineering, we can expect further innovations that will shape the future of the manufacturing sector.
Discover the Benefits of Rapid CNC Machining for Quality Results
Title: Leading CNC Machining Service Provider Offers Precision and Efficiency to Industrial Clients Introduction: In the dynamic world of industrial manufacturing, precision and efficiency are key factors that can make or break a company's success. Recognizing this, Rapid CNC Machining (brand name removed), a leading CNC machining service provider, has emerged as a reliable partner for industrial clients seeking high-quality and precise manufacturing solutions. With a commitment to cutting-edge technology, exceptional customer service, and seamless project management, Rapid CNC Machining continues to strengthen its position as a trusted name in the industry.Body:1. Company Overview and Expertise:Established in the heart of the manufacturing hub, Rapid CNC Machining has a proven track record of delivering precision-machined parts and components to a wide array of industries. The company's state-of-the-art facility houses an extensive range of CNC machines, allowing them to cater to diverse manufacturing needs. Their team of highly skilled technicians, engineers, and project managers ensure that each project is executed with utmost precision and efficiency.2. Technological Advancements:Rapid CNC Machining has stayed ahead of the competition by consistently investing in the latest CNC machining technology. The company's cutting-edge equipment enables them to provide comprehensive solutions, including design assistance, prototyping, custom part production, and mass production. By utilizing advanced software and tools, Rapid CNC Machining optimizes the manufacturing process, reducing lead times and maximizing product quality.3. Diverse Industry Applications:With an extensive portfolio of successful projects, Rapid CNC Machining serves various industries, including aerospace, automotive, medical, electronics, and more. Their expertise in machining a wide range of materials, including aluminum, stainless steel, titanium, plastics, and composites, enables them to meet the unique requirements of each industry. Whether it is complex aerospace components or intricate medical device parts, Rapid CNC Machining ensures the highest standards of accuracy, functionality, and durability.4. Commitment to Quality Assurance:Rapid CNC Machining places great emphasis on quality assurance throughout the manufacturing process. From initial design analysis to final inspection, the company employs rigorous quality control measures to guarantee adherence to specifications and customer expectations. Their ISO 9001-certified facility ensures consistent quality and compliance with industry standards, earning them a reputation for excellence.5. Customer-Centric Approach:Understanding the importance of strong customer relationships, Rapid CNC Machining prioritizes open communication and collaboration with clients. Their skilled project management team ensures seamless coordination, from project initiation to product delivery. With a commitment to transparency, Rapid CNC Machining provides regular progress updates, addresses any concerns promptly, and maintains strict confidentiality protocols.6. Sustainable Manufacturing Practices:In an era of growing environmental consciousness, Rapid CNC Machining strives to implement sustainable manufacturing practices. By optimizing material utilization, reducing waste, and utilizing energy-efficient machinery, the company minimizes its environmental footprint. Moreover, investing in research and development, Rapid CNC Machining actively explores greener alternatives, ensuring its manufacturing processes are aligned with sustainability goals.7. Global Reach and Future Outlook:Rapid CNC Machining has established a global footprint by serving clients from various countries and regions. Their commitment to delivering exceptional value and their strong reputation for reliable service has positioned them as a preferred CNC machining partner worldwide. As the company continues to expand its capabilities, invest in technology, and nurture customer relationships, Rapid CNC Machining aims to remain at the forefront of the industry.Conclusion:Through consistent innovation, dedication to customer satisfaction, and a focus on precision and efficiency, Rapid CNC Machining has solidified its position as a leading provider of CNC machining services. Their state-of-the-art facility, diverse industry applications, and commitment to sustainable practices set them apart from competitors. As industrial manufacturing continues to evolve, the company's unwavering commitment to quality and customer-centricity ensures they will remain a trusted partner for businesses seeking superior CNC machining solutions.
CNC Machined Aluminum: Unveiling the Impactful Advantages
CNC MACHINED ALUMINIUM: Revolutionizing Precision Manufacturing[Company Introduction]In the fast-paced world of manufacturing, precision and efficiency are paramount. Companies are constantly on the lookout for innovative solutions that can enhance their production processes, reduce costs, and deliver unparalleled quality. One such breakthrough is CNC Machined Aluminium, a cutting-edge technique transforming the landscape of precision manufacturing.[Paragraph 1]CNC Machined Aluminium, or Computer Numerical Control Machining, is a method of using computer-controlled machines to shape and cut aluminium parts with high precision. This advanced manufacturing technique has gained popularity over the years due to its ability to create complex and intricate components with extraordinary accuracy. With CNC Machining, companies can achieve greater efficiency, reduced production times, and improved quality control.[Paragraph 2]The introduction of CNC Machined Aluminium has revolutionized various industries, including automotive, aerospace, electronics, and medical equipment manufacturing, among others. The ability to machine aluminium with unparalleled precision has opened new doors for companies looking to deliver cutting-edge products in these highly competitive sectors.[Paragraph 3]Compared to traditional manufacturing methods such as manual milling or turning, CNC Machined Aluminium offers several significant advantages. Firstly, the precision achieved through this technique is unmatched, ensuring that every part produced meets the strictest tolerance requirements. This accuracy eliminates human error and guarantees consistency in manufacturing, resulting in higher-quality products.[Paragraph 4]Furthermore, CNC Machining enables manufacturers to create complex geometric designs and shapes that were previously impractical or even impossible. The computer-controlled machines can effortlessly execute intricate designs, allowing companies to unleash their creativity and push the boundaries of what is achievable in aluminium manufacturing. This versatility allows for the production of lightweight yet robust components that contribute to fuel efficiency, improved performance, and increased product lifespan.[Paragraph 5]Another crucial advantage of CNC Machined Aluminium is its exceptional efficiency. The automated process significantly reduces the need for human labor, resulting in faster production times and increased productivity. Furthermore, the use of computer-aided design (CAD) software allows for seamless integration of the manufacturing process, reducing errors and minimizing material waste. This streamlined workflow ultimately translates into cost savings for companies, making CNC Machined Aluminium an economically viable choice.[Paragraph 6]It's worth mentioning that CNC Machined Aluminium is not limited to large-scale production. The versatility of this technique allows businesses of all sizes to benefit from its advantages. From prototyping to small and medium-sized batches, CNC Machining offers flexibility and affordability without compromising quality or precision. This accessibility has democratized precision manufacturing, leveling the playing field for businesses eager to bring their innovative ideas to life.[Paragraph 7]While CNC Machined Aluminium has undoubtedly reshaped the manufacturing industry, it is important to note the need for experienced and skilled professionals to harness its full potential. Operating CNC machines and programming the necessary codes require specialized knowledge and expertise. With proper training and an understanding of the intricacies involved, professionals can fully utilize CNC Machining to its maximum effectiveness.[Paragraph 8]In conclusion, CNC Machined Aluminium has emerged as a game-changer in precision manufacturing, providing companies with the tools they need to stay ahead of the competition. The unparalleled precision, versatility, and efficiency offered by this technique have transformed various industries, allowing for the production of complex and high-quality aluminium components. As technology continues to advance, we can expect CNC Machined Aluminium to continue pushing the boundaries of what is achievable in precision manufacturing, fostering innovation and driving industry growth.
High-quality CNC Machined Aluminum Parts for Precision Engineering
In the world of manufacturing and production, precision and quality are essential. This is why many industries rely on CNC machining to create high-quality metal parts with intricate specifications. One company that has excelled in this field is {}.With years of experience and expertise in CNC machining, {} has established itself as a trusted provider of aluminum parts for a wide range of industries. From automotive to aerospace, their precision machining capabilities have made them a go-to supplier for many businesses.Recently, {} has announced the expansion of their CNC machining services to include aluminum parts. This move comes in response to the growing demand for lightweight and durable metal components in various industries. Aluminum is known for its excellent strength-to-weight ratio, corrosion resistance, and machinability, making it an ideal material for a wide range of applications.{}'s CNC machining capabilities enable them to produce aluminum parts with tight tolerances and complex geometries. Their state-of-the-art machining centers are equipped with multi-axis capabilities, high-speed spindles, and advanced tooling systems, allowing them to efficiently produce parts with exceptional precision and surface finishes.One of the key advantages of {}'s CNC machining services is their ability to work with a wide range of aluminum alloys. Whether the application requires 6061, 7075, or another type of aluminum, {} has the expertise to select the right material and machining parameters to meet the specific requirements of their customers.In addition to their machining capabilities, {} also offers value-added services such as surface finishing, assembly, and quality inspection to ensure that the finished aluminum parts meet the highest standards. Their commitment to quality and customer satisfaction has earned them a solid reputation in the industry.Furthermore, {}'s dedication to continuous improvement and investment in the latest machining technology sets them apart from their competitors. They regularly invest in new equipment, software, and training to stay at the forefront of CNC machining capabilities, allowing them to tackle even the most challenging projects with confidence.With the expansion of their CNC machining services to include aluminum parts, {} is well-positioned to serve the evolving needs of their customers across various industries. Whether it's producing components for automotive engines, aircraft structures, or electronic enclosures, {}'s expertise in machining aluminum parts makes them an invaluable partner for businesses looking for high-quality and reliable metal components.In conclusion, {}'s expansion of CNC machining services to include aluminum parts is a testament to their commitment to meeting the ever-changing needs of the manufacturing industry. With their expertise, capabilities, and dedication to quality, {} is poised to continue serving as a leading provider of precision-machined aluminum parts for years to come.
Guide to Advanced Features of CNC Machines
The manufacturing industry has seen a tremendous advancement in technology over the years, with the introduction of Computer Numerical Control (CNC) machines revolutionizing the way products are designed and manufactured. With their ability to automate complex machinery processes, CNC machines have become an essential component in the production process for a wide range of industries.One of the leading companies in the CNC machine industry, {Company Name}, has been at the forefront of developing and producing state-of-the-art CNC machines that are known for their precision, efficiency, and reliability. With a focus on innovation and customer satisfaction, {Company Name} has established itself as a trusted provider of CNC machine solutions for businesses worldwide.The key features of {Company Name}'s CNC machines are what set them apart in the market. One of the most notable features is the machine's high-speed precision machining capability, which allows for the production of complex and intricate parts with exceptional accuracy. This level of precision is essential in industries such as aerospace, automotive, and medical, where the smallest deviation can have significant consequences.Furthermore, {Company Name}'s CNC machines are equipped with advanced software and control systems that optimize the machining process for efficiency and productivity. This ensures that the machines can handle a variety of tasks, including milling, turning, drilling, and more, all with minimal setup time and maximum output.The versatility of {Company Name}'s CNC machines is another standout feature, as they are designed to adapt to a wide range of materials and processes. Whether it's metal, plastic, wood, or composites, these machines can handle the job with ease, making them a valuable asset for businesses with diverse manufacturing needs.In addition to their technical capabilities, {Company Name}'s CNC machines are built to be user-friendly, with intuitive interfaces and ergonomic designs that make operation and maintenance straightforward. This allows businesses to maximize the potential of the machines with minimal training and resources, ultimately leading to a seamless integration into their existing production processes.The reliability and durability of {Company Name}'s CNC machines are also worth mentioning, as they are built to withstand the demands of high-volume production while maintaining consistent performance and accuracy over time. This level of dependability translates to lower maintenance costs and downtime for businesses, ultimately contributing to a more efficient and profitable operation.{Company Name} prides itself on providing comprehensive support and services for their CNC machines, ensuring that customers have access to technical expertise, training, and spare parts when needed. This commitment to customer satisfaction has solidified {Company Name}'s reputation as a leading provider of CNC machine solutions, trusted by businesses of all sizes and industries.In conclusion, the features of {Company Name}'s CNC machines demonstrate the company's dedication to delivering high-quality, reliable, and versatile solutions that meet the evolving needs of the manufacturing industry. With a focus on innovation and customer satisfaction, {Company Name} continues to be a driving force in advancing the capabilities of CNC technology, and businesses can rely on their machines to optimize their production processes for years to come.
The Future of Injection Molding Industry: Trends and Growth Opportunities
The Injection Molding Industry is currently enjoying a surge in growth, thanks to the continuous technological advancements and increasing demand in different sectors such as automotive, packaging, healthcare, and consumer goods. As a prominent player in this industry, {Company Name} has continued to maintain its market leadership by delivering high-quality products and excellent customer service.{Company Name} has established itself as a reliable and innovative injection molding solution provider, offering a wide range of products and services to meet the diverse needs of its clients. With a strong focus on research and development, the company has been able to stay ahead of the competition by continuously introducing new and advanced molding techniques and processes. This has enabled {Company Name} to expand its product offerings and cater to a wider client base.In addition to its dedication to technological advancements, {Company Name} has also prioritized sustainability and environmental responsibility in its operations. The company has implemented eco-friendly manufacturing practices and has invested in state-of-the-art equipment to minimize energy consumption and reduce its carbon footprint. This commitment to sustainability has not only enhanced the company's reputation but has also positioned them as a preferred partner for clients who prioritize environmentally conscious suppliers.One of the key factors contributing to {Company Name}'s success is its commitment to understanding and meeting the specific needs of its clients. The company works closely with its customers to provide customized injection molding solutions that are tailored to their unique requirements. This personalized approach has earned {Company Name} a loyal customer base and has led to long-standing partnerships with reputable companies across various industries.Moreover, {Company Name} has also kept pace with the digital transformation in the manufacturing industry by incorporating cutting-edge technologies into its operations. The company has embraced automation and data-driven processes to streamline its production and enhance efficiency. This strategic adoption of Industry 4.0 practices has allowed {Company Name} to improve its production capabilities and deliver cost-effective solutions to its clients.Despite the challenges posed by the global pandemic, {Company Name} has demonstrated resilience and agility in maintaining a stable supply chain and meeting its clients' needs. The company has implemented robust safety measures to ensure the well-being of its employees and has adapted its operations to accommodate the changing market dynamics. As a result, {Company Name} has been able to navigate through the uncertainties and emerge as a reliable partner for its customers during these unprecedented times.Looking ahead, {Company Name} remains committed to furthering its position in the injection molding industry by continuously innovating and expanding its capabilities. With strategic investments in talent, technology, and infrastructure, the company aims to solidify its market presence and explore new growth opportunities. Additionally, {Company Name} is also exploring partnerships and collaborations to tap into emerging markets and offer its expertise to a broader global audience.In conclusion, {Company Name} stands as a frontrunner in the injection molding industry, driven by its steadfast commitment to innovation, sustainability, customer satisfaction, and operational excellence. With its strong industry presence, diverse product portfolio, and forward-thinking approach, {Company Name} is well-positioned to capitalize on the growing market demand and lead the way in shaping the future of injection molding.
The Ultimate Guide to CNC: Everything You Need to Know
As a leader in the CNC industry, {} has consistently demonstrated its commitment to innovation and excellence. The company has been at the forefront of developing cutting-edge CNC technology, providing state-of-the-art solutions to its customers. Recently, {} has launched a new CNC guide that is set to revolutionize the way operators interact with CNC machines.The new CNC guide is an advanced software system that provides a user-friendly interface for operating CNC machines. It is designed to simplify the programming and operation of CNC equipment, making it more accessible to a wider range of users. With its intuitive design and advanced features, the CNC guide enables operators to perform complex tasks with ease, ultimately improving productivity and efficiency in manufacturing processes.One of the key features of the new CNC guide is its comprehensive library of pre-programmed templates and tool paths. This library allows operators to quickly and accurately program CNC machines without the need for extensive manual input. This not only saves time but also reduces the potential for errors, ensuring a higher level of precision in the machining process.In addition, the CNC guide incorporates advanced visualization tools that provide operators with real-time feedback on the machining process. This includes 3D simulations of tool paths and cutting operations, allowing operators to visually inspect and optimize their programs before running them on the machine. This level of visual feedback enhances the overall machining experience, giving operators greater control over the end result.Furthermore, the new CNC guide is equipped with smart sensors and monitoring capabilities that continuously track the performance of the CNC machine. This allows operators to detect any issues or anomalies in the machining process, enabling them to take corrective action in real time. As a result, machine downtime is minimized, and the overall reliability of the CNC system is significantly improved.The launch of the new CNC guide is a testament to {}'s ongoing dedication to creating innovative solutions that drive progress in the CNC industry. By leveraging the latest advancements in software and technology, {} is empowering its customers to achieve new levels of efficiency and precision in their manufacturing operations.In a statement, the CEO of {} expressed his enthusiasm for the new CNC guide, highlighting its potential to transform the way CNC machines are operated. He emphasized the company's commitment to continuous improvement and stated that the CNC guide is just one example of {}'s ongoing efforts to push the boundaries of what is possible in CNC technology.Customers who have had the opportunity to test the new CNC guide have already provided positive feedback, noting its user-friendly interface and powerful capabilities. Many have expressed their excitement about the potential impact of this technology on their own manufacturing processes, recognizing the significant benefits it offers in terms of productivity and quality.Looking ahead, {} plans to continue refining and expanding the capabilities of the CNC guide, with a focus on further enhancing its ease of use and performance. The company remains dedicated to maintaining its position as a trusted partner for CNC solutions, providing its customers with the tools they need to succeed in today's competitive manufacturing environment.In conclusion, the launch of the new CNC guide represents a major milestone for the CNC industry, and {} is proud to be at the forefront of this innovation. By combining its expertise in CNC technology with a commitment to excellence, {} has once again demonstrated its ability to deliver cutting-edge solutions that empower its customers to achieve greater success. The CNC guide is poised to make a significant impact on the way CNC machines are operated, setting a new standard for efficiency and precision in manufacturing.
Top Trends Shaping the Injection Molding Industry in 2021
In today's rapidly evolving manufacturing landscape, the injection molding industry continues to play a crucial role in the production of a wide range of goods. With advancements in technology and processes, the industry has witnessed significant growth and innovation, paving the way for the production of high-quality and complex plastic components. One company that has been at the forefront of this progress is {}.{} is a leading player in the injection molding industry, with a strong reputation for delivering exceptional quality products and solutions to its diverse customer base. The company's commitment to innovation, efficiency, and sustainability has positioned it as a key player in the global market.Established over two decades ago, {} has continually invested in state-of-the-art technology and machinery to meet the increasing demand for high-precision plastic components. The company's modern manufacturing facilities are equipped with advanced injection molding machines, automated production lines, and quality control systems to ensure the highest standards of production.A key differentiator for {} is its comprehensive range of services, which includes product design and development, mold design and fabrication, and custom injection molding. This end-to-end approach allows the company to offer tailored solutions to its clients, from initial concept to final production.The company serves a diverse array of industries, including automotive, electronics, consumer goods, medical devices, and more. With a proven track record of meeting and exceeding customer expectations, {} has built long-term partnerships with renowned brands and manufacturers globally.In addition to its commitment to quality and innovation, {} places a strong emphasis on sustainability and environmental responsibility. The company leverages cutting-edge technology and sustainable materials to minimize waste and energy consumption in its manufacturing processes. As a result, {} has earned recognition for its eco-friendly practices and dedication to corporate social responsibility.One of the cornerstones of {}'s success is its team of skilled and experienced professionals. The company's engineers, technicians, and support staff are highly trained and committed to delivering excellence in every aspect of their work. With a focus on continuous learning and improvement, {} fosters a culture of innovation and collaboration, ensuring that it remains at the forefront of the injection molding industry.Looking ahead, {} is poised to further expand its capabilities and reach new heights of success. The company continues to invest in research and development, exploring new materials and technologies to enhance its product offerings. Furthermore, {} is exploring opportunities for global expansion to better serve its international customer base and meet the growing demand for high-quality injection molded products.In conclusion, {} stands as a shining example of excellence in the injection molding industry. With its unwavering commitment to quality, innovation, and sustainability, the company has solidified its position as a trusted partner for manufacturers around the world. As {} continues to evolve and grow, it is set to shape the future of injection molding and set new standards for the industry as a whole.
Unlocking the Power of 4-Axis CNC Milling: Exploring Advanced Machining Capabilities
Title: Enhancing Precision and Productivity with Advanced 4-Axis CNC Milling TechnologyIntroduction:In a rapidly evolving manufacturing landscape, companies across industries are constantly seeking innovative solutions to maximize precision and productivity. One such advancement that has garnered significant attention is the incorporation of 4-axis CNC milling technology. This cutting-edge technique allows for the creation of intricately designed parts and components with unparalleled precision, efficiency, and versatility. Today, we delve into the world of 4-axis CNC milling, exploring its remarkable capabilities and the ways in which it revolutionizes the manufacturing process, propelling industries into a new era of growth and competitiveness.Revolutionizing Manufacturing with 4-Axis CNC Milling:Traditionally, milling was a manual process that involved removing material from a workpiece with rotary cutters. However, with the advent of computer numerical control (CNC) machining, the process has been completely transformed. CNC milling utilizes pre-programmed computer software instructions that precisely control cutter movement and material removal, resulting in consistent and accurate machining operations. While 3-axis CNC milling has served the industry well, the incorporation of a fourth axis significantly expands the capabilities of this technology.The 4th axis, often referred to as the A-axis, enables the milling cutter to rotate around the X-axis, allowing for the creation of complex geometries and the machining of undercuts, bevels, and other intricate features. This added versatility opens up a myriad of possibilities for manufacturers, facilitating the production of more complex and aesthetically appealing components.Enhanced Precision and Efficiency:With 4-axis CNC milling, manufacturers can achieve unparalleled precision and accuracy. The rotational capabilities of the A-axis enable the machine to approach the workpiece from various angles, reducing the need for multiple setups. This not only saves time but also minimizes errors associated with manual repositioning. The result is faster production cycles, improved part quality, and reduced scrap rates, ultimately leading to increased cost-effectiveness and customer satisfaction.Furthermore, 4-axis CNC milling technology excels in machining complex curves, contours, and profiles, ensuring consistency across multiple parts. With the ability to perform intricate operations in a single setup, manufacturers can accelerate production while maintaining the highest level of precision, meeting the demands of even the most intricate designs.Versatility Across Industries:The applications of 4-axis CNC milling span a wide range of industries, benefiting from its inherent precision and flexibility. In the aerospace sector, this technology is instrumental in the production of engine components, turbine blades, and aircraft structural parts, which require intricate machining and strict adherence to tolerances. Similarly, in the automotive industry, companies utilize 4-axis CNC milling for machining engine blocks, cylinder heads, and transmission components.Medical practitioners also rely on 4-axis CNC milling to fabricate complex dental implants, prosthetics, and surgical instruments. The versatility of 4-axis CNC milling technology allows manufacturers to cater to the evolving needs of various industries, providing customized solutions that meet the highest standards of quality and precision.Conclusion:As industries continue to push the boundaries of innovation, the integration of 4-axis CNC milling technology has become an increasingly vital aspect of the manufacturing process. The enhanced precision, efficiency, and versatility offered by this cutting-edge technology propel industries to new heights, ensuring accelerated production cycles, improved part quality, and increased customer satisfaction. With its ability to machine intricate geometries and complex designs, 4-axis CNC milling paves the way for the future of precision manufacturing, revolutionizing industries and strengthening their competitive edge in the global market.