Advanced 5 Axis Milling Machines for Precision Manufacturing
By:Admin
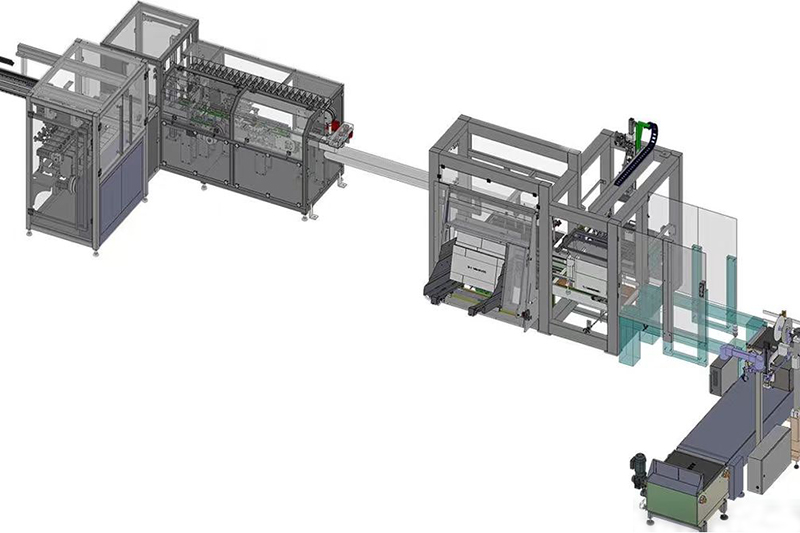
{} is a leading manufacturing company that specializes in producing a wide range of precision parts and components for various industries, including aerospace, automotive, and medical. With a strong commitment to innovation and continuous improvement, the company has invested heavily in state-of-the-art equipment, including 5 Axis Milling Machines, to meet the growing demands of its customers.
One of the key advantages of 5 Axis Milling Machines is their ability to perform complex machining operations with a high degree of accuracy. Unlike traditional 3-axis machines, which can only move in three directions (X, Y, and Z), 5 Axis Milling Machines have the capability to move in two additional rotary axes, allowing for greater flexibility in machining complex geometries. This means that {} is able to produce intricate parts and components with tight tolerances, without the need for multiple setups or repositioning of the workpiece.
In addition to improved precision, 5 Axis Milling Machines also offer significant time savings. By combining multiple machining operations into a single setup, the machines reduce the need for manual intervention and minimize the time it takes to produce a finished part. This results in shorter cycle times and increased productivity, allowing {} to meet tight production deadlines and deliver high-quality products to its customers.
Another benefit of 5 Axis Milling Machines is their ability to optimize tool paths and minimize material waste. With advanced software and simulation capabilities, {} is able to program the machines to follow the most efficient paths, reducing unnecessary tool movements and minimizing the amount of material that is removed during the machining process. This not only saves time and money, but also contributes to a more sustainable manufacturing process.
Furthermore, the use of 5 Axis Milling Machines has allowed {} to expand its capabilities and take on more complex projects. The machines have enabled the company to produce a wider range of parts and components, including those with intricate geometries and tight tolerances that would have been difficult or impossible to produce with traditional machining methods. This has opened up new opportunities for {} to serve a diverse range of industries and meet the evolving needs of its customers.
As a result of these advancements, {} has solidified its reputation as a trusted and reliable manufacturing partner. The company has built strong relationships with its customers by consistently delivering high-quality products on time and within budget. With the continued investment in 5 Axis Milling Machines and other advanced technologies, {} remains committed to pushing the boundaries of what is possible in the world of manufacturing.
In conclusion, the use of 5 Axis Milling Machines has had a significant impact on the capabilities and success of {}. By leveraging this advanced technology, the company has been able to achieve higher levels of precision, efficiency, and versatility in its manufacturing operations. As the demand for complex parts and components continues to grow, {} is well-positioned to meet the needs of its customers and drive innovation in the industry.
Company News & Blog
Exploring the Benefits and Applications of Cnc Molding in Modern Manufacturing Processes
Title: Revolutionary Cnc Molding Technique Sets New Standards in ManufacturingIntroduction:In an era where innovation and efficiency drive the manufacturing industry, a breakthrough in the form of Cnc Molding technology is emerging as a game-changer. This revolutionary technique promises to reshape the way products are designed, developed, and produced. With its unparalleled precision, speed, and cost-effectiveness, Cnc Molding is poised to set new standards in the manufacturing field.Company Background and Expertise:{Company Name}, a prominent player in the manufacturing industry, has unveiled its cutting-edge Cnc Molding technology. With a rich history spanning several decades, {Company Name} has established itself as a pioneer in delivering excellence and embracing the latest technological advancements. Their expertise in the field, combined with their commitment to driving innovation, has paved the way for this groundbreaking development.Understanding Cnc Molding:Cnc Molding, also known as Computer Numerical Control Molding, is a state-of-the-art manufacturing process that utilizes computer-controlled machines to shape materials into desired forms. Unlike traditional molding techniques, Cnc Molding ensures unparalleled precision, efficiency, and repeatability. By following a digital design prototype, the technology enables manufacturers to produce highly intricate and complex components with utmost accuracy.Benefits of Cnc Molding:1. Enhanced Precision: The integration of computer control systems eliminates the possibility of human error, ensuring precise replication of designs and eliminating defects. This high level of precision ensures product consistency, reducing wastage and overall costs.2. Streamlined Production: Cnc Molding technology dramatically accelerates the production process. With its ability to perform multiple tasks simultaneously, the technology maximizes efficiency and reduces lead times. This streamlining of operations increases productivity, enabling manufacturers to meet market demands promptly.3. Cost-Effectiveness: By minimizing material wastage and requiring fewer human interventions, Cnc Molding significantly reduces production costs. The elimination of manual labor and the use of optimized resources result in improved cost-effectiveness, making it an attractive option for manufacturers across various industries.4. Design Freedom: Cnc Molding empowers designers to create innovative and intricate designs that were previously unachievable. With the ability to produce complex shapes and patterns with ease, this technology unlocks a new realm of possibilities, enabling manufacturers to create unique products that stand out in the market.Applications of Cnc Molding:The applications of Cnc Molding are vast and span across industries such as automotive, aerospace, electronics, medical, and consumer goods. Its usage is particularly prominent in the production of custom parts, prototypes, and intricate components that require high precision.Future Implications:As Cnc Molding continues to evolve, the implications for the manufacturing industry are immense. The integration of artificial intelligence, machine learning, and digital twins creates an even more robust system capable of even greater efficiency and accuracy. The technology's potential for customization and adaptability positions it as a frontrunner in the future of manufacturing.Conclusion:Cnc Molding technology, introduced by {Company Name}, is set to revolutionize the manufacturing industry. With its exceptional precision, streamlined production, cost-effectiveness, and design freedom, it promises to set new standards and transform the way products are made. As it continues to develop, this groundbreaking technology is poised to usher in a new era of manufacturing excellence.
Top Workholding Fixtures for CNC Machines: Everything You Need to Know
CNC Workholding Fixtures, Revolutionizing the Manufacturing IndustryIn today's fast-paced manufacturing industry, precision and efficiency are paramount. With the advancement in technology, companies are constantly seeking innovative solutions to improve their manufacturing processes. CNC workholding fixtures have emerged as a game-changer in the industry, offering a more efficient, accurate, and cost-effective way to hold and secure workpieces during machining operations.{Company name}, a leading provider of CNC workholding fixtures, has been at the forefront of this revolution, offering a wide range of solutions designed to meet the diverse needs of the manufacturing industry.The company's state-of-the-art CNC workholding fixtures are designed to ensure the highest levels of precision and repeatability, ultimately leading to improved productivity and reduced downtime. These fixtures are engineered to withstand the rigors of high-speed machining operations, offering unmatched stability and reliability.One of the key advantages of {company name}'s CNC workholding fixtures is their versatility. Whether it's a simple milling operation or a complex 5-axis machining process, these fixtures can be easily customized to accommodate different workpiece geometries and sizes. This flexibility allows manufacturers to streamline their production processes and adapt to changing demands with ease.Moreover, {company name}'s CNC workholding fixtures are designed with a focus on ergonomics and user-friendly features. This not only ensures a safer working environment for operators but also reduces the setup time, ultimately leading to increased operational efficiency.In addition to their standard range of CNC workholding fixtures, {company name} also offers custom design and manufacturing services to meet the unique requirements of their clients. Their team of skilled engineers and technicians work closely with customers to develop tailored solutions that optimize their manufacturing processes and enhance their competitive edge.The impact of {company name}'s CNC workholding fixtures can be seen across various industries, including aerospace, automotive, medical, and energy. By implementing these advanced fixtures, companies have been able to achieve higher levels of precision, reduce scrap rates, and ultimately improve their bottom line.With the ever-increasing demand for high-quality precision components, manufacturers are constantly looking for innovative solutions to stay ahead of the competition. {Company name}'s CNC workholding fixtures are a testament to their commitment to pushing the boundaries of technology and delivering superior solutions that meet the evolving needs of the industry.Furthermore, with sustainability becoming a top priority for many companies, {company name} is also committed to developing eco-friendly solutions that minimize waste and energy consumption. Their CNC workholding fixtures are designed to optimize material usage and reduce the environmental impact of the manufacturing process.Overall, {company name}'s CNC workholding fixtures have revolutionized the manufacturing industry by providing a more efficient, accurate, and sustainable solution to workpiece holding and securing. With their commitment to innovation and excellence, {company name} continues to play a pivotal role in shaping the future of manufacturing.As the industry continues to evolve, companies can rely on {company name} to provide cutting-edge CNC workholding fixtures that meet the highest standards of quality and performance. With their expertise and dedication to customer satisfaction, {company name} is well-positioned to lead the way in the ever-changing world of manufacturing.
How to Achieve Successful Overmolding of Plastic onto Metal
Title: A Revolutionary Advancement in Manufacturing: Overmolding Plastic On MetalIntroduction:In a groundbreaking development in the manufacturing industry, a leading company has recently unveiled its latest innovation in overmolding technology, allowing the seamless integration of plastic onto metal components. This cutting-edge process promises to revolutionize various industries, offering unparalleled opportunities for enhanced product durability, design flexibility, and cost-effectiveness. By merging the benefits of metal strength with the versatility of plastic, this groundbreaking technique opens up endless possibilities for manufacturers across the globe. Background:Recognizing the growing demand for more durable and aesthetically appealing products, manufacturers have long been seeking innovative ways to combine the strengths of different materials. These endeavors have led to the evolution of overmolding, a process that involves molding one material, usually plastic, over an existing component made of another material, commonly metal. Overmolding has been widely utilized in various industries, including automotive, electronics, and consumer goods, to improve product performance, ergonomics, and aesthetics.Product Introduction:Leading the charge in this realm of technology-advanced manufacturing is an industry trailblazer known for its commitment to innovation and relentless pursuit of excellence. Through tireless research and development, this company has perfected the art of overmolding plastic on metal, achieving unparalleled precision and quality in their products. The company's breakthrough overmolding process involves the injection of molten plastic onto metal components, resulting in a durable, seamless bond that surpasses traditional plastic or metal components in terms of both strength and aesthetic appeal.Advantages of Overmolding Plastic On Metal:1. Enhanced Durability: Overmolding plastic on metal creates a robust bond that significantly improves the structural integrity of the product. By minimizing the risk of component failure due to impacts, temperature variations, or chemical exposure, manufacturers can ensure longer product lifespans and ultimately enhance customer satisfaction.2. Improved Design Flexibility: Overmolding offers unparalleled design freedom, enabling manufacturers to create complex shapes and innovative designs that were previously not achievable with traditional manufacturing techniques. The ability to combine various materials with different properties allows for the creation of aesthetically pleasing and ergonomically superior products.3. Cost-effectiveness: Overmolding eliminates the need for additional assembly processes, reducing overall production costs. By combining multiple components into a single overmolded part, manufacturers can streamline their manufacturing processes, minimize assembly time, and decrease labor expenses.4. Reduced Noise and Vibration: Overmolding plastic dampens noise and absorbs vibrations, making it an ideal choice for applications requiring noise reduction, such as automotive interiors and consumer goods. This not only enhances user comfort but also improves the overall quality and perceived value of the product.Applications in Various Industries:The introduction of overmolding plastic on metal opens up new possibilities across a wide range of industries:1. Automotive: Overmolded components find extensive use in automotive interiors, offering improved aesthetics, comfort, and functional integration. From steering wheels to gear knobs, the overmolding process allows manufacturers to create visually appealing, ergonomic, and durable components.2. Electronics: Overmolded connectors, switches, and protective casings in the electronics industry provide enhanced resistance to moisture, dust, and impact. This not only improves the product's performance and durability but also enhances user safety.3. Consumer Goods: Overmolding plastic on metal can significantly enhance the quality and functionality of consumer goods. From kitchen appliances to power tools, the incorporation of overmolded components improves ergonomics, reduces noise, and extends product lifespan.Conclusion:The advent of overmolding plastic on metal marks a significant leap forward in manufacturing technology, offering unprecedented opportunities for industries seeking to enhance the durability, design flexibility, and cost-effectiveness of their products. The seamless integration of plastic onto metal components enables manufacturers to create innovative, aesthetically pleasing, and high-performance products that surpass the limits of traditional manufacturing techniques. As this groundbreaking technology continues to evolve, it is poised to revolutionize numerous industries and drive the development of the manufacturing sector to new heights.
Understanding the Benefits of Computerized Numerical Control Technology
Computerized Numerical Control (CNC) technology has revolutionized manufacturing processes across industries, and one company that has been at the forefront of this innovation is {}.{} is a leading provider of CNC solutions for various industrial applications. The company's commitment to delivering high-quality, reliable, and efficient CNC systems has made it a trusted partner for manufacturers around the world.With a wide range of CNC products and services, {} has remained a key player in the global manufacturing landscape. Whether it's CNC machining centers, turning machines, or milling machines, {} has consistently been at the cutting edge of technological advancements, helping businesses enhance their productivity and profitability.One of the key features of {}'s CNC systems is their advanced control capabilities. These systems leverage the power of computerized numerical control to precisely control the movement of cutting tools and other machinery components. This level of precision allows manufacturers to produce complex and intricate parts with ease, resulting in higher quality end products.In addition to precision control, {}'s CNC systems are known for their versatility and flexibility. These systems can be easily programmed to accommodate a wide range of manufacturing tasks, making them suitable for various industries, including aerospace, automotive, medical, and electronics.The integration of computerized numerical control has also contributed to significant improvements in efficiency and productivity. By automating the manufacturing process, {}'s CNC systems reduce the need for manual intervention, leading to faster production cycles and reduced lead times. This has helped manufacturers streamline their operations and meet the ever-increasing demands of the market.Moreover, {} has always been committed to innovation, continually investing in research and development to further enhance its CNC solutions. The company's dedication to staying ahead of the curve has resulted in the introduction of state-of-the-art CNC technologies, such as advanced controller systems, multi-axis machining capabilities, and real-time monitoring and diagnostics.Furthermore, {}'s customer-centric approach sets it apart in the industry. The company works closely with its clients to understand their specific requirements and provide tailored CNC solutions that meet their unique needs. This personalized approach has earned {} a reputation for delivering exceptional customer satisfaction and building long-lasting partnerships with its clients.In line with its commitment to excellence, {} also offers comprehensive training and support services to ensure that its customers can maximize the potential of their CNC systems. From installation and setup to ongoing maintenance and troubleshooting, {}'s team of experts is dedicated to assisting clients every step of the way.As the manufacturing landscape continues to evolve, {} remains at the forefront, driving innovation and shaping the future of CNC technology. With a strong focus on precision, reliability, efficiency, and customer satisfaction, {} is poised to continue leading the way in the CNC industry for years to come.In conclusion, the integration of computerized numerical control has had a transformative impact on the manufacturing industry, and {} has been a driving force behind this revolution. With its cutting-edge CNC solutions, commitment to innovation, and customer-centric approach, {} has cemented its position as a global leader in the CNC technology space. As the industry evolves, {} is well-equipped to continue delivering high-quality, reliable, and efficient CNC solutions that empower manufacturers to thrive in a competitive market.
- Beginner's Guide to CNC Machining: Everything You Need to Know about Computer Numerical Control
Introducing CNC Machining: Revolutionizing Manufacturing ProcessesIn today's fast-paced world, manufacturing processes are constantly evolving, and companies are always on the lookout for ways to increase efficiency and improve the quality of their products. One such innovation that has revolutionized the manufacturing industry is CNC machining. This technology has drastically changed the way products are fabricated, providing precise and accurate results that were previously unattainable with traditional machining methods.CNC, which stands for Computer Numerical Control, is a manufacturing process that utilizes computerized controls and machine tools to produce complex and intricate parts and products. Unlike traditional machining, where human operators are required to manually guide the cutting tools, CNC machining employs automated processes that are programmed to perform specific tasks with a high degree of accuracy and repeatability.The introduction of CNC machining has significantly improved the efficiency and productivity of manufacturing operations, allowing companies to produce complex parts and components in a fraction of the time it would take with traditional methods. This has enabled businesses to meet the growing demand for high-quality products while reducing production costs and minimizing errors.Company, a leading manufacturer in the industry, has embraced the advancements in CNC machining and has integrated this technology into its production processes. By doing so, the company has been able to streamline its manufacturing operations and offer its customers a wider range of precision-engineered products. With the implementation of CNC machining, Company has been able to achieve unparalleled levels of accuracy and consistency in the production of its components, ultimately ensuring the satisfaction of its clients.The utilization of CNC machining has also allowed Company to take on more complex and challenging projects that were previously deemed unfeasible using traditional machining methods. The ability to produce intricate and precise parts has opened up new opportunities for the company, enabling it to expand its product offerings and cater to a broader market.Furthermore, the integration of CNC machining has enhanced the company's overall competitiveness in the industry, as it can now deliver high-quality products in shorter lead times, giving it an edge over its competitors. By leveraging the capabilities of CNC machining, Company has been able to solidify its position as an industry leader and meet the evolving needs of its customers.In addition to the various benefits that CNC machining has brought to Company, the technology has also contributed to significant advancements in the manufacturing industry as a whole. The increased efficiency and precision offered by CNC machining have led to improved product quality, reduced waste, and enhanced overall productivity in manufacturing processes across various sectors.As the demand for complex and highly precise parts continues to grow, the adoption of CNC machining is becoming increasingly essential for businesses looking to stay ahead in the competitive manufacturing landscape. Through its commitment to embracing cutting-edge technologies, Company has positioned itself as a pioneering force in the industry, and its utilization of CNC machining serves as a testament to its dedication to delivering top-tier products to its customers.In conclusion, the introduction of CNC machining has brought about a paradigm shift in the manufacturing industry, offering unprecedented levels of precision, efficiency, and versatility. Company's embrace of CNC machining has not only enhanced its own manufacturing capabilities but has also contributed to the advancement of the industry as a whole. As CNC machining continues to evolve and improve, its impact on manufacturing processes will undoubtedly be transformative, paving the way for a new era of innovation and excellence.
Top 5 Applications of Injection Molding in Manufacturing
Injection Molding Application Brings Revolutionary Changes to Manufacturing ProcessesIn today's fast-paced world, manufacturers are constantly seeking new and innovative ways to improve their production processes. One such method that has been gaining widespread attention is injection molding. This advanced manufacturing technique has the potential to bring about revolutionary changes in the way products are designed and produced.Injection molding is a manufacturing process for producing parts by injecting molten material into a mold. It is commonly used for manufacturing a variety of products, including plastic parts, components for medical devices, automotive parts, and consumer goods. This process has gained popularity due to its ability to produce complex and intricate parts with high precision and consistency.One company that has been at the forefront of utilizing injection molding technology is {} (). The company, established in 1990, has carved a niche for itself in the manufacturing industry by providing high-quality injection-molded parts for a wide range of applications. With a state-of-the-art facility equipped with the latest injection molding machines and a team of experienced engineers, {} is able to deliver custom solutions to meet the unique needs of its clients.{} is committed to staying ahead of the curve in the ever-evolving manufacturing landscape. With a focus on innovation and customer satisfaction, the company has continually invested in advanced technologies to enhance its production capabilities. This forward-thinking approach has not only enabled {} to maintain its competitive edge but has also positioned the company as a leader in the injection molding industry.One of the key advantages of injection molding is its ability to produce parts with exceptional precision and accuracy. The process allows for the creation of intricate designs and complex geometries that would be challenging to achieve using traditional manufacturing methods. With the use of computer-aided design (CAD) software and advanced mold-making techniques, {} is able to manufacture high-quality parts with tight tolerances, ensuring superior performance and functionality.Another advantage of injection molding is its cost-effectiveness. The ability to produce large volumes of parts with minimal waste makes this manufacturing process highly efficient. {} has leveraged this advantage to offer competitive pricing to its customers, making it an attractive choice for businesses looking to streamline their production processes and reduce overall costs.Furthermore, injection molding is a versatile process that can accommodate a wide range of materials, including thermoplastics, thermosets, and elastomers. This flexibility allows {} to cater to diverse industry needs, from automotive and aerospace to medical and consumer products. By working closely with its customers, the company is able to recommend the most suitable materials for their specific applications, ensuring optimal performance and durability.In addition to its technical capabilities, {} is dedicated to sustainability and environmental responsibility. The company strives to minimize its environmental impact by implementing eco-friendly practices in its manufacturing processes. By using recyclable materials and optimizing energy consumption, {} is committed to promoting a greener and more sustainable future for the manufacturing industry.With its dedication to quality, innovation, and customer satisfaction, {} is poised to continue making significant contributions to the advancement of injection molding technology. As the manufacturing landscape continues to evolve, this company remains committed to staying ahead of the curve and delivering cutting-edge solutions to its clients.In conclusion, injection molding is a game-changer in the manufacturing industry, and {} is leading the charge in harnessing its potential. With its state-of-the-art facilities, technical expertise, and commitment to excellence, {} is well-positioned to continue driving revolutionary changes in the production of high-quality, precision-engineered parts. As the demand for complex and customized products continues to grow, injection molding is likely to play an even more prominent role in shaping the future of manufacturing.
Premium CNC Machining for Steel: Unlocking Precision and Efficiency
[News Title:]Steel CNC Machining Revolutionizes Precision Manufacturing with Cutting-Edge Processes[News Introduction:]In today's rapidly evolving world, precision manufacturing is becoming increasingly essential across various industries. One company that has caught the attention of experts and industry leaders worldwide has revolutionized the field with their exceptional steel CNC machining capabilities. Catering to diverse sectors such as automotive, aerospace, and electronics, this innovative company has managed to carve a niche for itself through its advanced processes, delivering unparalleled precision and efficiency. By harnessing the power of steel CNC machining, they have managed to streamline manufacturing processes and redefine the possibilities of precision engineering.[News Body:]The company (company name), a frontrunner in steel CNC machining, prides itself on its state-of-the-art facilities, cutting-edge technology, and a team of highly skilled engineers and machinists. Their commitment to quality and excellence has enabled them to secure a reputation as one of the leading providers of precision machining services worldwide.With steel CNC machining, this company expertly transforms raw materials into complex and intricate components used across a wide range of industries. By utilizing state-of-the-art computer numerical control (CNC) machines and a superior understanding of the properties of steel, they are capable of producing highly accurate and precise parts in a fraction of the time it would take traditional manufacturing methods.One of the key advantages of steel CNC machining lies in its ability to cater to a myriad of design specifications. This technique allows for the production of intricate, high-quality components with tight tolerances, ensuring a perfect fit for various applications. From gears and shafts to brackets and housings, their CNC machines are capable of creating parts that conform to the most demanding requirements.Moreover, the company's cutting-edge software and 3D modeling capabilities enable them to optimize designs and create custom components with unparalleled accuracy and efficiency. This ensures that the final product not only meets but exceeds the client's expectations, making steel CNC machining the ideal choice for industries that demand excellence.In addition to their superior manufacturing capabilities, the company takes pride in its commitment to quality control. With stringent quality checks at every stage of the machining process, they ensure that all components leaving their facilities meet the highest standards. Through the effective use of advanced inspection tools and techniques, they guarantee that each part is flawless, free from defects, and ready for immediate integration into the client's assembly line.The versatility of steel CNC machining also plays a significant role in its widespread adoption across multiple industries. From automotive manufacturing, where precision-engineered parts ensure optimal performance and safety, to aerospace applications, where stringent standards and requirements are paramount, (company name) has consistently delivered exceptional results. Their ability to work with a wide range of steel alloys further enhances their capabilities, allowing them to cater to the specific needs of each client.Going beyond traditional manufacturing, the company's research and development team remains at the forefront of technological advancements. By actively exploring new techniques and materials, they continually refine their processes to deliver even greater precision and efficiency. As industry demands evolve, this commitment to innovation ensures that the company remains a trusted partner for businesses seeking cutting-edge solutions.[News Conclusion:]As the field of precision manufacturing continues to advance, the importance of steel CNC machining cannot be understated. The processes and capabilities offered by (company name) have positioned them as a leader in the industry. With their commitment to quality, expertise, and constant innovation, they are poised to drive forward the next generation of precision components. From helping automotive manufacturers achieve superior performance to aiding aerospace engineers in pushing the boundaries of exploration, steel CNC machining continues to redefine what is possible in precision manufacturing.
Exploring the Advantages of Computer Numerical Control Machining in Modern Manufacturing
Title: Computer Numerical Control Machining Revolutionizes Manufacturing ProcessesIntroduction:In today's fast-paced world, businesses are constantly seeking innovative solutions to enhance the precision, speed, and efficiency of their manufacturing processes. One such technological advancement that has transformed the industry is Computer Numerical Control (CNC) Machining. By leveraging cutting-edge software and automation, CNC Machining has revolutionized traditional manufacturing methods, allowing companies to fabricate components with utmost accuracy and reliability. In this article, we will explore the remarkable capabilities of CNC Machining and its impact on modern manufacturing systems.Paragraph 1:CNC Machining has emerged as a game-changing technology that has significantly enhanced the precision of component manufacturing. By utilizing computer-controlled systems, this manufacturing process converts digital designs into physical products with unparalleled accuracy. Unlike conventional manual machining, CNC Machining eliminates the scope for human error, resulting in higher product quality and reduced waste. This advancement has not only boosted productivity in various industries but also facilitated the creation of intricate designs and complex geometries that were previously unattainable.Paragraph 2:The key to the success of CNC Machining lies in its ability to perform multiple manufacturing operations using a single machine. From milling and drilling to lathing and grinding, CNC machines are equipped with a wide range of tools that can be seamlessly interchanged. Additionally, these machines can operate without human intervention, enabling manufacturers to optimize productivity by running the machines continuously even outside working hours. This level of automation not only reduces production time but also minimizes costs associated with manual labor, making CNC Machining a cost-effective solution for businesses across various sectors.Paragraph 3:Furthermore, CNC Machining has empowered companies to meet the growing demands for customized products while maintaining consistent quality. By leveraging CAD/CAM software, designers can create intricate 3D models of components, which are then translated into machine-readable code. This code is fed into the CNC machine, allowing it to precisely reproduce the model and produce multiple copies with utmost accuracy. Whether it is prototyping or mass production, CNC Machining ensures remarkable repeatability and uniformity of products, facilitating efficient scaling of operations.Paragraph 4:The impact of CNC Machining on various industries is undeniable. For instance, in the aerospace and automotive sectors, precision and reliability are of paramount importance. CNC Machining enables manufacturers to create intricate components such as turbine blades or engine parts with exceptional precision, meeting the stringent requirements of these industries. Moreover, the medical field has also witnessed immense benefits from CNC Machining, as it allows for the production of patient-specific implants and devices, improving treatment outcomes and reducing surgical costs.Paragraph 5:Despite these remarkable advantages, the adoption of CNC Machining may face certain challenges. The initial cost of acquiring state-of-the-art CNC machines and training personnel in their operation and maintenance can be significant for small to medium-sized enterprises. However, the long-term gains in terms of improved productivity, reduced waste, and enhanced product quality outweigh these concerns. As CNC Machining continues to advance, manufacturers must recognize its transformative potential and invest in this technology to remain competitive in an increasingly demanding market.Conclusion:Computer Numerical Control Machining has revolutionized traditional manufacturing processes by introducing automation, precision, and versatility. This technology has not only enabled companies to meet intricate design requirements but also improved productivity and reduced production time and costs. As industries continue to benefit from CNC Machining, it is crucial for manufacturers to stay abreast of evolving advancements and harness its potential to achieve sustainable growth and maintain a competitive edge in today's rapidly evolving marketplace.
- Precision Machining: A Guide to High-Quality Manufacturing
High Precision Machining, also known as (remove brand name), is a leading provider of high-quality precision machining services. With a strong focus on delivering superior products and customer satisfaction, (remove brand name) has carved a niche for itself in the manufacturing industry.The company's precision machining capabilities are driven by advanced technologies and a team of highly skilled engineers and technicians. (remove brand name) specializes in producing complex components with tight tolerances and high surface finishes for a wide range of industries, including aerospace, automotive, medical, and defense.One of the key factors that sets (remove brand name) apart from its competitors is its commitment to investing in the latest equipment and technology. The company's state-of-the-art manufacturing facilities are equipped with advanced CNC machinery, including multi-axis milling and turning centers, EDM machines, and inspection equipment. This enables (remove brand name) to consistently deliver precision parts that meet the most rigorous specifications and standards.In addition to its cutting-edge technology, (remove brand name) places a strong emphasis on quality control and process optimization. The company follows strict quality management systems and adheres to industry best practices to ensure that every component that leaves its facility is of the highest quality. (remove brand name) also offers value-added services such as design for manufacturability and engineering support to assist customers in achieving their manufacturing goals.Furthermore, (remove brand name) is known for its quick turnaround times and reliable delivery schedules. The company understands the importance of on-time delivery in the manufacturing industry and has implemented efficient production processes to meet the demands of its customers. (remove brand name) works closely with its clients to understand their specific needs and timeline requirements, and strives to exceed expectations with its fast and reliable service.With a proven track record of delivering precision components to some of the most demanding industries, (remove brand name) has earned a reputation for excellence and reliability. The company's commitment to quality, innovation, and customer satisfaction has positioned it as a preferred partner for OEMs and manufacturers seeking high-precision machining solutions.In addition to its technical capabilities, (remove brand name) takes pride in its commitment to sustainability and environmental stewardship. The company has implemented eco-friendly manufacturing practices and is dedicated to minimizing its environmental impact. (remove brand name) has also invested in energy-efficient equipment and processes to reduce its carbon footprint and contribute to a greener future.Looking ahead, (remove brand name) is poised for continued growth and success in the precision machining industry. The company plans to expand its capabilities and capacity to meet the increasing demand for high-quality precision components. (remove brand name) also aims to further enhance its technological capabilities and explore new opportunities for innovation and efficiency.In conclusion, (remove brand name) is a leading provider of high-precision machining services, known for its advanced technology, commitment to quality, and client-focused approach. With a strong track record of delivering superior products and exceeding customer expectations, (remove brand name) is well-positioned for a successful future in the manufacturing industry.
High-Quality CNC Machined Aluminum Parts for Your Project
CNC Aluminum, a leading manufacturer in the industry, has recently made significant strides in the production of precision components using advanced CNC machining technology. The company has been at the forefront of innovation and has built a reputation for delivering high-quality, custom-made aluminum parts for a wide range of industries.With a state-of-the-art manufacturing facility and a team of highly skilled engineers and technicians, CNC Aluminum has the capability to produce complex components with tight tolerances and intricate designs. The company's CNC machining capabilities allow for the production of parts that meet the highest standards of quality and precision.CNC Aluminum's commitment to excellence is evident in its dedication to investing in the latest CNC machining equipment and technology. The company continuously upgrades its machinery and software to ensure that it stays at the cutting edge of the industry. This investment in technology has enabled CNC Aluminum to expand its capabilities and take on more challenging projects.One of the key strengths of CNC Aluminum is its ability to work closely with its customers to understand their specific requirements and design custom solutions that meet their needs. The company has a team of experienced engineers who are skilled in using advanced CAD/CAM software to create designs and prototypes that can be turned into finished products with a high degree of accuracy.In addition to its technical expertise, CNC Aluminum also places a strong emphasis on quality control and inspection processes. The company has strict quality standards in place to ensure that every component that leaves its facility meets the highest levels of precision and performance. From the initial raw material inspection to the final product testing, CNC Aluminum follows a comprehensive quality assurance process to maintain consistency and reliability in its outputs.Furthermore, CNC Aluminum is committed to sustainability and environmental responsibility. The company utilizes efficient manufacturing processes that minimize waste and energy consumption. It also ensures that its raw materials are sourced from reputable suppliers who adhere to ethical and environmentally friendly practices.As CNC Aluminum continues to grow and expand its capabilities, it remains dedicated to providing its customers with the highest levels of quality, precision, and service. The company's focus on innovation, technology, and customer collaboration sets it apart in the industry and has cemented its position as a leading provider of CNC-machined aluminum components.In conclusion, CNC Aluminum's advancements in precision CNC machining technology, coupled with its dedication to quality, innovation, and customer satisfaction, have positioned the company as a trusted partner for businesses seeking high-quality aluminum components. As the company continues to push the boundaries of what is possible with CNC machining, it is poised to make even greater contributions to the industries it serves.